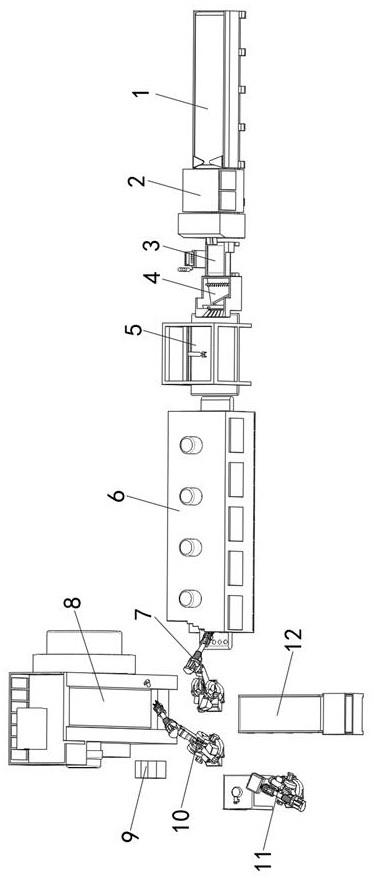
1.本发明涉及涡旋盘加工技术领域,特别涉及一种铝合金涡旋盘智能生产线及生产方法。
背景技术:2.锻造行业工作环境恶劣,生产线技术落后,锻件质量难保证,随着人口红利的消失,实现自动锻造生产是解决上述问题的必然趋势和有效手段。
3.汽车空调压缩机铝合金涡旋盘外形结构复杂,成形过程中变形程度大,同时铝合金流动性差,锻造温度范围狭窄,需要严格控制坯料温度与模具温度保证锻件质量。
4.在现有生产线中,通过对冷却后锻件的测量从而判断模具的磨损量,该方法时效性差,此外有众多学者采用修正archard公式预测模具寿命,但通常用于理想情况下的模具结构优化,时效性及适用性方面仍然存在不足。
技术实现要素:5.本发明的目的在于,提供一种铝合金涡旋盘智能生产线及生产方法。本发明可以使铝合金涡旋盘生产的自动化,提高生产效率、产品合格率及产品质量。
6.本发明的技术方案:一种铝合金涡旋盘智能生产线,包括铝棒输送设备、切断设备、称重设备、上料装置、模具冷却润滑设备、下料装置和锻件输送装置,所述切断设备设置在铝棒输送设备的前方,称重设备设置在切断设备的前方;所述称重设备的前方依次设有上料装置、排序设备和加热设备;所述加热设备的前方依次设置上料装置和下料装置;所述上料装置的一侧设有锻压设备,模具冷却润滑设备设置在锻压设备的一侧;所述锻件输送装置位于上料装置另一侧,并与锻压设备相对设置;所述锻件输送装置的侧方还设有检测设备;所述上料设备包括依次设置的第一导向装置、第一输送装置和第二导向装置;所述第一导向装置阻拦并倾倒竖向滚动的圆饼状坯料,使得圆饼状坯料在第一输送装置输送前保持水平滑动,所述第一输送装置使坯料规则地排布进入第二导向装置,所述第二导向装置用于扩大坯料之间的间距并使得坯料单个输送。
7.上述的铝合金涡旋盘智能生产线,所述上料设备包括上料箱体,上料箱体中设有第一导向装置、第一输送装置和第二导向装置;所述第一导向装置包括设置在上料箱体前侧面之间的导向杆以及倾斜向前的第一导向底板,第一导向底板上设有斜向设置的导向板;所述第一输送装置包括位于上料箱体中的升降气缸,升降气缸的伸缩端连接有升降台;所述升降台的台面呈倾斜状,升降台的台面高点位于导向板的低端方向;所述第二导向装置包括倾斜向前的第二导向底板,第二导向底板上设有多片导向叶片,所述导向叶片前设有挡料杆,所述挡料杆右侧设有挡料板。
8.前述的铝合金涡旋盘智能生产线,所述排序设备包括固定架,固定架的下方设有排序输送带,固定架的上方设有排序装置。
9.前述的铝合金涡旋盘智能生产线,所述固定架左右两侧分别设有对称的限位移动
槽;所述排序装置包括一根移动杆,移动杆的中部设有排序气缸,排序气缸的伸缩端设有夹爪;所述移动杆的两端分别设有设置在限位移动槽内的滚轮;所述固定架的前后两侧分别设有从动带轮和排序电机,排序电机的输出端连接有主动带轮,主动带轮与从动带轮之间设有传动带,传动带的中部与移动杆固定连接。
10.前述的铝合金涡旋盘智能生产线,所述加热设备包括加热炉,加热炉的下方设有链板输送带,链板输送带上设有多列坯料槽组;所述加热炉的前方设有炉口门和第一温度传感器,所述链板输送带位于排序设备的前方。
11.前述的铝合金涡旋盘智能生产线,所述坯料槽组中的坯料槽有5个,所述炉口门呈阶梯状排布;所述第一温度传感器设置于炉口门的上方。
12.前述的铝合金涡旋盘智能生产线,所述锻压设备包括锻压机主体,锻压机主体上设有第二温度传感器和压力传感器。
13.前述的铝合金涡旋盘智能生产线,所述检测设备包括锻件固定架,锻件固定架的一侧设有检测用机械手,检测用机械手上设有三维成像装置。
14.前述的铝合金涡旋盘智能生产线的生产方法,通过铝棒输送设备输送铝棒,所述切断机将铝合金棒料切断成圆饼状的胚料,所述称重设备检查坯料重量,所述上料设备与所述排序设备对坯料进行上料和排序,所述加热设备对坯料进行加热,加热完成后,所述上料装置抓取坯料进锻压设备,所述锻压设备进行锻造成形,成形完毕后,所述下料装置抓取坯料至检测装置检测锻件质量,再抓取坯料至锻件输送装置输送,所述模具冷却润滑系统对锻压设备中的模具进行冷却与润滑。
15.前述的铝合金涡旋盘智能生产线的生产方法,通过检测冷却前的锻件的工艺参数结果,采用公式并基于有限元分析软件deform-3d的二次开发计算单次模具磨损量,利用单次模具磨损量输入至matlab中拟合获取函数模型,利用函数模型将单次模具磨损量的累加结果与最大允许模具磨损量进行比较,从而实时预测模具剩余可用次数;所述的公式如下:;式中,表示模具冷却液喷涂的间隔次数,为整个数值模拟过程中的模拟步数,和分别为第次成形模拟,第个时间增量和成形位置在模具上的相对滑动距离和模具界面压力 是磨损系数关于温度的函数,是模具硬度关于温度的函数,是模具i位置处的磨损量。
16.与现有技术相比,本发明通过铝棒输送设备输送铝棒,由切断机将铝合金棒料切断成圆饼状的胚料,通过称重设备检查坯料重量,再由上料设备与所述排序设备对坯料进行上料和排序,然后加热后锻压成形,成形完毕后由下料装置抓取坯料至检测装置检测锻
件质量,再抓取坯料至锻件输送装置输送,所述模具冷却润滑系统对锻压设备中的模具进行冷却与润滑。本发明的上料装置通过导向杆使得胚料向第一导向底板的低端聚集,并结合导向板使得胚料聚集在右侧,利用升降气缸带动升降台的上下升降,使得胚料能够通过上下升降的方式依次的落入到升降台的台面上,再利用升降台倾斜的方式,胚料在升降台的台面上向第二导向装置的方向移动,当升降台上升到足够高度时,利用片导向叶片将第二导向底板进行分隔,使得胚料可以均匀排布并单独的进入一个导向通道中,同时配合挡料杆和挡料板的作用,可以挡住多余坯料,保证上料时坯料数量。本发明可以提高铝合金涡旋盘生产的自动化,提高生产效率。本发明的三维成像装置通过检测冷却前的锻件的工艺参数结果,结合模具冷却润滑设备使用频率,采用公式并基于有限元分析软件deform-3d的二次开发计算单次模具磨损量,利用单次模具磨损量输入至matlab中拟合获取函数模型,解决了deform-3d计算速度慢时效性差的问题,最后利用函数模型将单次模具磨损量的累加结果与最大允许模具磨损量进行比较,从而实时预测模具剩余可用次数,具有时效性好,适应性强的优点,提高了产品合格率及产品质量。
17.附图说明
18.图1是本发明的结构示意图;图2是本发明上料装置的结构示意图;图3本发明上料装置的另一视角的结构示意图图4是本发明排序设备的结构示意图;图5是本发明加热设备的结构示意图;图6是本发明锻压设备的结构示意图;图7是本发明检测设备的结构示意图。
19.附图标记1、铝棒输送设备;2、切断设备;3、称重设备;4、上料设备;5、排序设备;6、加热设备;7、上料装置;8、锻压设备;9、模具冷却润滑设备;10、下料装置;11、检测设备;12、锻件输送装置;41、第一导向装置;410、导向杆;411导向板;412、第一导向底板;42、第一输送装置;421、升降气缸;422、升降台;43、第二导向装置;430、导向叶片;431、挡料杆;432、挡料板;423、第二导向底板; 51、排序输送带;52、固定架;53、排序装置;54、限位移动槽;55、移动杆;56、排序气缸;57、夹爪;58、滚轮;510、排序电机;511、主动带轮;512、传动带;61、链板输送带;62、加热炉;63、坯料槽;64、炉口门;65、第一温度传感器;81、锻压机主体;82、第二温度传感器;83、压力传感器;111、锻件固定架;812、检测用机械手;813、三维成像装置。
20.。具体实施方式下面结合附图和实施例对本发明作进一步的说明,但并不作为对本发明限制的依据。此处所述的具体实例仅用于解释本发明,本文叙述中的“上”、“下”、“左”、“右”、“前”、“后”仅用于叙述本发明,不用于限定本发明。
21.实施例:一种铝合金涡旋盘智能生产线,包括铝棒输送设备1、切断设备2、称重设备3、上料装置7(可以是常规的上料机械手)、模具冷却润滑设备9、下料装置10和锻件输送装置12,所述切断设备2设置在铝棒输送设备1的前方,称重设备3设置在切断设备2的前方;
所述称重设备3的前方依次设有上料设备4、排序设备5和加热设备6;所述加热设备6的前方依次设置上料装置7和下料装置10;所述上料装置7的一侧设有锻压设备8,模具冷却润滑设备9设置在锻压设备8的一侧;所述锻件输送装置12位于上料装置7另一侧,并与锻压设备8相对设置;所述锻件输送装置12的侧方还设有检测设备11。该铝合金涡旋盘智能生产线的生产方法,通过铝棒输送设备1输送铝棒,所述切断机将铝合金棒料切断成圆饼状的胚料,所述称重设备3检查坯料重量,所述上料设备与所述排序设备5对坯料进行上料和排序,所述加热设备6对坯料进行加热,加热完成后,所述上料装置7抓取坯料进锻压设备8,所述锻压设备8进行锻造成形,成形完毕后,所述下料装置10抓取坯料至检测装置检测锻件质量,再抓取坯料至锻件输送装置12输送,所述模具冷却润滑系统对锻压设备8中的模具进行冷却与润滑。所述上料设备4包括第一导向装置41、第一输送装置42和第二导向装置43;所述第一导向装置41阻拦并倾倒竖向滚动的圆饼状坯料,使得圆饼状坯料在第一输送装置42输送前保持水平滑动,所述第一输送装置42使坯料规则地排布进入第二导向装置43,所述第二导向装置43用于扩大坯料之间的间距并使得坯料单个输送。
22.如图2和图3所示,所述上料设备4包括上料箱体,上料箱体中设有第一导向装置41、第一输送装置42和第二导向装置43;所述第一导向装置41包括设置在上料箱体前侧面之间的导向杆410以及倾斜向前的第一导向底板412,导向杆410呈螺旋状,可以由电机带动转动,所述第一导向底板412上设有斜向设置的导向板411;所述第一输送装置42包括位于上料箱体中的升降气缸421,升降气缸421的伸缩端连接有升降台422;所述升降台422的台面呈倾斜状,升降台的台面高点位于导向板411的低端方向;所述第二导向装置43包括倾斜向前的第二导向底板433,第二导向底板433上设有多片导向叶片430,导向叶片430将第二导向底板433分隔成多个通道,所述导向叶片前设有挡料杆431,挡料杆431横向水平设置,所述挡料杆431右侧设有挡料板432。本发明的上料装置通过导向杆使得胚料向第一导向底板的低端聚集,并结合导向板使得胚料聚集在右侧,利用升降气缸带动升降台的上下升降,使得胚料能够通过上下升降的方式依次的落入到升降台的台面上,再利用升降台倾斜的方式,胚料在升降台的台面上向第二导向装置的方向移动,当升降台上升到足够高度时,利用片导向叶片将第二导向底板进行分隔,使得胚料可以均匀排布并单独的进入一个导向通道中,同时配合挡料杆和挡料板的作用,可以挡住多余坯料,保证上料时坯料数量。
23.如图4所示,所述排序设备5包括固定架52,固定架52的下方设有排序输送带51,固定架52的上方设有排序装置53。所述固定架52左右两侧分别设有对称的限位移动槽54;所述排序装置53包括一根移动杆55,移动杆55的中部设有排序气缸56,排序气缸56的伸缩端设有夹爪57;所述移动杆55的两端分别设有设置在限位移动槽54内的滚轮58;所述固定架52的前后两侧分别设有从动带轮和排序电机510,排序电机510的输出端连接有主动带轮511,主动带轮511与从动带轮之间设有传动带512,传动带512的中部与移动杆55固定连接。所述排序装置53判断排序输送带51上的坯料是否处于合理位置,对处于不合理位置的坯料进行整理,即通过排序电机510转动带动传动带512转动,传动带512带动移动杆55在限位移动槽54内移动,从而调节位置,使得移动杆55下方的排序气缸56到达合适的地点,再利用夹爪57对不合理位置的坯料进行夹取调整。
24.如图5所示,所述加热设备6包括加热炉62,加热炉62的下方设有链板输送带61,链板输送带61上设有多列坯料槽63组;所述加热炉62的前方设有炉口门64和第一温度传感器
65,所述链板输送带61位于排序设备5的前方。所述坯料槽63组中的坯料槽63有5个,所述炉口门64呈阶梯状排布;所述第一温度传感器65设置于炉口门64的上方。所述链板输送带61可以调整速度控制加热时间,所述加热炉62可以调节加热功率控制加热温度,所述坯料槽63用于固定坯料,所述炉口门64呈阶梯状排列,解决铝合金在室温下冷却过快的问题,提高铝合金坯料加热温度的一致性,采用所述第一温度传感器65检测坯料温度,使加热炉62形成闭环控温提高控制系统的抗干扰能力,此外利用实时检测的坯料温度进行模具寿命预测可以提高预测结果实时性。
25.如图6所示,所述锻压设备8包括锻压机主体81,锻压机主体81上设有第二温度传感器82和压力传感器83。所述第二温度传感器82用于检测模具温度,实现模具温度闭环控制,压力传感器83用于检测成形载荷,此外利用实时检测的模具温度和成形载荷进行模具寿命预测可以提高其实时性。
26.如图7所示,所述检测设备11包括锻件固定架111,锻件固定架111的一侧设有检测用机械手812,检测用机械手812上设有三维成像装置813。其中,各传感器的实时检测保证了模具寿命预测的时效性。由于模具尺寸直接决定锻件尺寸,所述三维成像装置通过检测冷却前的锻件外部尺寸,从而判断当下模具的磨损状态,将检测结果转化为x_t格式后为有限元分析软件deform-3d的模具剩余寿命预测提供模具有限元模型,利用工艺参数结果,结合模具冷却润滑设备使用频率,采用公式并基于有限元分析软件deform-3d的二次开发计算单次模具磨损量,利用单次模具磨损量输入至matlab中拟合获取函数模型,利用函数模型将单次模具磨损量的累加结果与最大允许模具磨损量(如涡旋盘成形模具的最大允许磨损量为0.2mm)进行比较,,从而实时预测模具剩余可用次数;所述的公式如下:;式中,表示模具冷却液喷涂的间隔次数,为整个数值模拟过程中的模拟步数,和分别为第次成形模拟,第个时间增量和成形位置在模具上的相对滑动距离和模具界面压力是磨损系数关于温度的函数,是模具硬度关于温度的函数,是模具i位置处的磨损量。
27.综上所述,本发明可以提高铝合金涡旋盘生产的自动化,提高生产效率,并且可以实时预测模具剩余可用次数,具有时效性好,适应性强的优点,提高了产品合格率及产品质量。