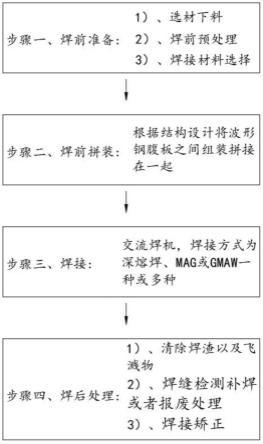
1.本发明涉及波形钢腹板焊接技术领域,尤其涉及一种波形钢腹板现场自动焊的工艺。
背景技术:2.波形钢腹板组合体内外预应力混凝土箱梁是一种以波形钢代替传统混凝土作为箱梁的腹板受力的桥梁结构形式,具有自重轻、跨度大、预应力效率高、造型美观等诸多优点。同时,其独特的结构形式使结构各组成部分受力明确,避免了传统预应力混凝土梁桥容易发生腹板开裂的缺点。
3.波形钢腹板的焊接质量直接影响着波形钢腹板组合体箱梁的质量,此前波形钢腹板与顶底板全熔透焊缝主要采用焊缝坡口侧打底、填充、盖面的焊接方法,背侧采用碳弧气刨刨削清根的方式,以确保熔透。但在实际生产作业过程中,存在焊缝根部熔合效果不理想、清根作业噪声大、清根飞溅多、焊缝熔數金属填充量大、焊接变形严重、焊接质量不稳定等情况,对整个钢梁的精确、高质加工影响较大。
4.因此,有必要提供一种新的波形钢腹板现场自动焊的工艺解决上述技术问题。
技术实现要素:5.为解决上述技术问题,本发明提供一种焊接变形小、焊接质量稳定的波形钢腹板现场自动焊的工艺。
6.本发明提供的波形钢腹板现场自动焊的工艺包括如下步骤:
7.步骤一、焊前准备:
8.1)、选材下料,选用牌号为q345d厚度为10~20mm统一材质规格的波形钢腹板,按照设计进行下料;
9.2)、焊前预处理,对波形钢腹板焊接区域表面进行打磨除锈,清洗油污,焊接坡口处理;
10.3)、焊接材料选择,根据波形钢腹板的牌号q345d,焊丝选用牌号为er50-6实心焊丝,焊丝直径为1.6mm,焊接方式采用气体保护自动焊接;
11.步骤二、焊接拼装:
12.根据结构设计,将波形钢腹板之间组装拼接在一起,利用支护支撑锚杆钢索铆接固定,并在波形钢腹板之间安装加强肋板和筋条,同时水平相邻的波纹钢腹板的焊缝形式采用贴角焊或者对接接头,相互垂直的波纹钢腹板或者与波纹钢腹板垂直对接的加强肋板和筋条采用t型接头;
13.其中,贴角焊、对接接头和t型接头组装间隙为0~3mm,t型接头的坡口为单侧45
°
、钝边为1~3mm;
14.步骤三、焊接:
15.若焊缝形式为贴角焊或对接接头,采用交流焊机,焊接方式为mag或gmaw;
16.若焊缝形式为t型接头,采用交流焊机,焊接方式为深熔焊和mag或gmaw混合焊接;
17.步骤四、焊后处理:
18.1)、清除焊渣以及飞溅物;
19.2)、焊缝检测补焊或者报废处理;
20.3)、焊接矫正。
21.优选的,所述步骤一中焊丝表面镀铜处理。
22.优选的,所述步骤一中的保护气体采用富氩混合气体,即为百分之八十的氩气和百分之二十的二氧化碳气体混合。
23.优选的,所述步骤三中的焊接电流、焊接电压、气体流量和焊接速度均有与焊机配套的电脑控制。
24.优选的,所述步骤三中的mag或gmaw焊接参数:焊接电流为187~305a,焊接电压为25~35v,气体流量为15~25l/min,焊接速度为350~400mm/min;
25.步骤三中的深熔焊的焊接参数:焊接电流为320~343a,焊接电压为23~33v,气体流量为15~25l/min,焊接速度为400~550mm/min。
26.优选的,所述步骤四中的清除焊渣以及飞溅物具体为:
27.当焊接后利用打磨装置对焊接的毛刺进行打磨处理,并清除焊缝周围焊渣。
28.优选的,所述步骤四中的焊缝检测补焊或者报废处理具体为:
29.利用焊缝探伤设备如超声检测仪、磁粉检测仪或者x射线检测仪对焊缝进行检测,当探伤检测不合格时,优先采用补焊二次修补,补焊后依旧不合格则作报废处理。
30.优选的,所述步骤四中的焊接矫正具体为:
31.当焊缝探伤检测合格时,对焊接变形区域利用机械矫正机,对波形钢腹板不同焊接部位变形进行矫正。
32.与相关技术相比较,本发明提供的波形钢腹板现场自动焊的工艺具有如下有益效果:
33.本发明提供一种波形钢腹板现场自动焊的工艺,通过采用上述工艺,根据不同的焊缝方式采用不同的焊接工艺参数,并通过焊后检测和矫正,确保了波形钢腹板现场自动焊的焊接质量,使得波形钢腹板现场焊接焊接变形小、焊接质量稳定,对波形钢腹板现场焊接工作的效率和质量有显著提升。
附图说明
34.图1为本发明提供的波形钢腹板现场自动焊的工艺的框序图;
35.图2为本发明提供的波形钢腹板现场自动焊的贴角焊焊缝形式以及焊道顺序示意图;
36.图3本发明提供的波形钢腹板现场自动焊的对接接头焊缝形式以及焊道顺序示意图;
37.图4为本发明提供的波形钢腹板现场自动焊的t型接头焊缝形式以及焊道顺序示意图。
具体实施方式
38.为了使本发明的目的、技术方案及优点更加清楚明白,以下结合附图及实施例,对本发明进行进一步详细说明。应当理解,此处所描述的具体实施例仅仅用以解释本发明,并不用于限定本发明。
39.以下结合具体实施例对本发明的具体实现进行详细描述。
40.请参阅图1至图4,本发明实施例提供的一种波形钢腹板现场自动焊的工艺,所述波形钢腹板现场自动焊的工艺包括:步骤一、焊前准备、步骤二、焊接拼装、步骤三、焊接和步骤四、焊后处理。
41.步骤一焊前准备:选用牌号为q345d厚度为10~20mm统一材质规格的波形钢腹板,按照设计进行下料,下料后根据焊接焊缝的形式,进行坡口处理,焊前控制在波形钢腹板与顶板组装过程中,为减小焊接变形,选用适合波形钢腹板焊缝施焊坡口,控制熔敷金属填充量,较厚的波形钢腹板尽量采用k形对称施焊坡口,焊接区域打磨除锈,其中,这里对贴角焊焊缝的焊接区域只需要打磨焊接处即可,不需要额外开设坡口,对接接头的焊缝形式,坡口开设成v型,并对v型坡口进行打磨清理,对t型接头的焊缝形式,坡口开设成45
°
角,然后根据q345d的低碳素钢和低合金钢焊接标准选用直径为1.6mm牌号为er50-6的实心焊丝,进行焊接,焊接选用百分之八十的氩气和百分之二十的二氧化碳气体混合富氩混合气体保护自动焊接,它既具有ar弧电弧稳定、飞溅小、容易获得轴向喷射过渡的优点,又具有氧化性。克服了氩气焊接时表面张力大、液体金属粘稠、阴极斑点易飘移等问题,同时对焊缝蘑菇形熔深有所改善。
42.其中,焊丝表面镀铜处理,这样焊丝进行镀铜处理后,焊接后的焊缝抗氧化能力更强。
43.完成步骤一后,进行步骤二焊接拼装:根据结构设计,将波形钢腹板之间组装拼接在一起,利用支护支撑锚杆钢索铆接固定,组装过程施加一定的反变形量,并在波形钢腹板之间安装加强肋板和筋条,需要栓接形式连接杆,制作可拆卸的机械锁紧工装,尽量减少焊接变形,水平相邻的波纹钢腹板的焊缝形式采用贴角焊或者对接接头,相互垂直的波纹钢腹板或者与波纹钢腹板垂直对接的加强肋板和筋条采用t型接头,贴角焊、对接接头和t型接头组装间隙为0~3mm,t型接头的坡口为单侧45
°
、钝边为1~3mm。
44.完成步骤二后,进行步骤三焊接:若焊缝形式为贴角焊或对接接头,采用交流焊机,焊接方式为mag或gmaw;
45.若焊缝形式为t型接头,采用交流焊机,焊接方式为深熔焊和mag或gmaw混合焊接;将焊接处利用交流焊机进行自动焊接。
46.其中,所述步骤三中的mag或gmaw焊接参数:焊接电流为187~305a,焊接电压为25~35v,气体流量为15~25l/min,焊接速度为350~400mm/min,焊接电流为320~343a,焊接电压为23~33v,气体流量为15~25l/min,焊接速度为400~550mm/min,具体的焊接工艺参数参见贴角焊焊接工艺表1-1、对接接头焊接工艺表1-2和t型接头焊接工艺表1-3:
47.贴角焊焊接工艺表1-1
[0048][0049]
对接接头焊接工艺表1-2
[0050][0051]
t型接头焊接工艺表1-3
[0052][0053][0054]
需要说明的是:利用贴角焊焊接工艺表1-1、对接接头焊接工艺表1-2和t型接头焊接工艺表1-3配合图2、图3和图4所示的焊道图对不同波形钢腹板拼接焊缝形式,进行自动焊接,确保焊缝质量,直至整体箱梁的波形钢腹板整体焊接完成。
[0055]
完成步骤三后,进行步骤四焊后处理:清除焊渣以及飞溅物,具体为利用打磨装置若角磨机或者磨轮机对焊接的毛刺进行打磨处理,并清除焊缝周围焊渣;焊缝检测补焊或者报废处理,具体为利用焊缝探伤设备如超声检测仪、磁粉检测仪或者x射线检测仪对焊缝
进行检测,当探伤检测不合格时,优先采用补焊二次修补,补焊后依旧不合格则作报废处理,焊接矫正,具体为当焊缝探伤检测合格时,对焊接变形区域利用机械矫正机,对波形钢腹板不同焊接部位变形进行矫正。
[0056]
其中,这里机械矫正机,根据不同的焊接部位和拼接方式,选用不同的顶板提升矫正机、底板顶压提升机,对向下变形的进行提升,对向上翘起的变形进行下压,从而对具体的变形进行针对性矫正。
[0057]
从而完成整体的波形钢腹板现场自动焊,整个焊接过程,根据不同的焊缝方式采用不同的焊接工艺参数,并通过焊后检测和矫正,确保了波形钢腹板现场自动焊的焊接质量,使得波形钢腹板现场焊接焊接变形小、焊接质量稳定,对波形钢腹板现场焊接工作的效率和质量有显著提升。
[0058]
以上所述仅为本发明的实施例,并非因此限制本发明的专利范围,凡是利用本发明说明书及附图内容所作的等效结构或等效流程变换,或直接或间接运用在其它相关的技术领域,均同理包括在本发明的专利保护范围内。