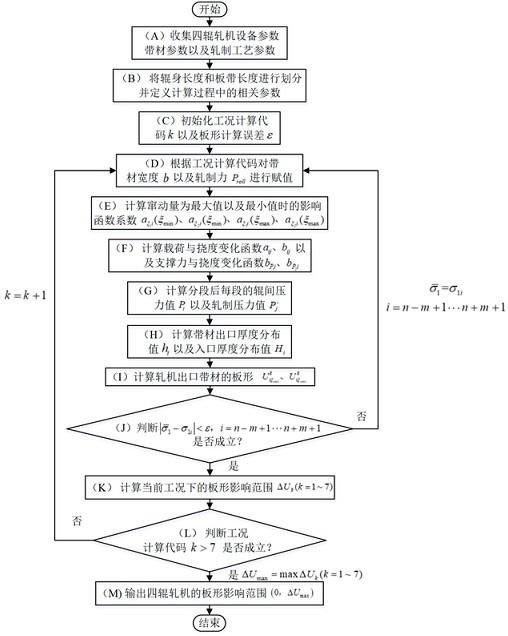
1.本发明涉及一种四辊轧机工作辊窜动对板形影响范围的预报方法,属于热连轧方法技术领域。
背景技术:2.随着我国家电、汽车等领域的快速发展,客户对高质量板带的需求量不断增加,对带钢的性能以及板形质量提出了更高的要求。板形精度的提高对于提升带钢产品的市场竞争力具有决定性的作用。四辊轧机轧制的带钢板形主要受轧辊弯辊力、窜动量、压下量、轧制力、张力等诸多因素的影响,其中通过窜动量的调整可达到提高四辊轧机板形控制能力以及改善带钢板形的目的,在四辊轧机轧制过程中轧辊窜动量的变化会影响轧辊表面接触应力分布的不均匀性,亦会引起轧辊磨损深度的变化,而轧辊磨损与轧辊表面接触应力的不均会直接导致轧机出口带钢出现板形缺陷,而合理的调整轧辊窜动量可使得轧辊表面的磨损均匀性以提高带钢表面板形。另外,窜动量的变化也会导致轧辊热凸度的不均匀性增加从而使得带钢出口板形质量变差,对轧机轧制的稳定性造成影响。轧辊窜动量变化会直接导致轧辊挠度发生变化,而挠度大小会影响板凸度的大小从而间接对带钢出口板形产生影响。不同宽度与轧制力下的带材板形影响范围受到轧辊窜动量调整范围的限制。轧辊窜动量过大或者过小都不利于优良板带的生产,因此如何在轧辊窜动量调节范围确定的情况下得出板形影响的范围成为重要的研究内容,根据板形影响范围以及检测到的板形就可以对板形进行在线检测达到提高带材板形的目的。目前,根据文献检索的内容可知,国内外的研究内容主要是对轧辊窜动控制方法的研究,通过优化与改善工作辊的窜动方法以减少轧辊磨损程度、提高板形控制能力;或者综合考虑窜动量、张力以及轧制力等参数对四辊轧机板形预报模型进行改进与优化从而提高板带的成材率,减少带钢浪形缺陷。并没有根据四辊轧机窜动量调节范围以及板形控制模型对四辊轧机的板形影响范围进行预估。
技术实现要素:3.本发明目的是提供一种四辊轧机工作辊窜动对板形影响范围的预报方法,综合考虑带材宽度在最窄且轧制力最小及最大时的板形影响范围、带材宽度在最宽且轧制力最小及最大时的板形影响范围、带材为平均宽度且轧制力最小、最大及平均值时的板形影响范围并求出七种工况下的综合板形影响范围,进而实现对四辊轧机工作辊窜动对板形影响范围的预报以提高四辊轧机特定机架的带钢板形控制能力,有效地解决了背景技术中存在的上述问题。
4.本发明的技术方案是:一种四辊轧机工作辊窜动对板形影响范围的预报方法,包含以下步骤:
5.(a)收集设备参数、带材参数及轧制参数;
6.(b)将辊身长度和板带长度进行分段并定义相关参数;
7.(c)初始化工况计算代码k及板形计算误差ε;
8.(d)根据工况计算代码k的数值以及模型对带材宽度以及轧制力进行赋值;
9.(e)基于窜动量影响函数模型计算窜动量为最大值以及最小值时的影响函数计算模型如下:
10.式中:xi、xj是支撑辊的第i个和第j个位置的辊身长度,δx为轧辊辊身以及带材每个段的长度,k1为工作辊影响函数的系数,取值为k1=4.25
×
10-8
。
11.(f)基于影响函数模型计算第j段载荷引起的第i段工作辊和支撑辊挠度变化的影响函数a
ij
、b
ij
以及左右支撑力对第i段工作辊和支撑辊挠度变化的影响函数计算模型如下所示:
[0012][0013]
式中:k2为支撑辊影响函数的系数,取值为k2=3.44
×
10-9
。
[0014]
(g)根据金属塑性变形模型和辊系弹性变形模型计算每段的辊间压力值pi以及轧制压力值计算模型如下所示:
[0015][0016]
式中:k为工作辊与支承辊相互压扁的柔度系数,β为工作辊相对支撑辊的刚性转角,经求解可得β=0,f1、f2为过程函数。
[0017]
(h)根据模型计算带材的入口厚度分布以及出口厚度分布;
[0018]
式中:x1为来料板形所划分的各段板形的位置,x1=iδx+δx/2,为工作辊与轧件间的压扁系数,θ为工作辊与支撑辊的交叉角,δhi为第i段带钢的出入口厚度差。
[0019]
(i)根据模型计算窜动量分别为最大值和最小值时的出口带材板形;
[0020]
式中:kr为前后张应力对轧制力的影响系数,取值为kr=0.015。
[0021]
(j)判断i=n-m+1
…
n+m+1是否成立,若不成立令i=n-m+1
…
n+m+1进入步骤(d),若成立则进入步骤 (k);
[0022]
(k)根据模型计算最小窜动量ξ
min
和最大窜动量ξ
max
的板形影响范围以及在此工况下的板形影响范围;
[0023]
(l)判断工况计算代码值k>7是否成立,若不成立则令k=k+1 进入步骤(d),否则令δu
max
=maxδuk(k=1~7)进入步骤(m);
[0024]
(m)输出四辊轧机的板形影响预报范围(0,δu
max
)。
[0025]
所述步骤(a)中,收集轧制过程中的相关参数包含特定机架支撑辊辊身长度lb,特定机架的工作辊直径dw,支撑辊直径db,带材弹性模量及泊松比e、ν,特定机架下的带钢最小、最大及平均宽度为b
min
、b
max
、b
av
,特定机架下的最小、最大以及平均轧制压力带材轧制时的弯辊力s,后张力、前张力平均值特定机架带钢入口厚度平均值h,出口厚度平均值h,带钢的变形抗力σ,板形计算误差ε,轧辊窜动量最大值ξ
max
,轧辊窜动量最小值ξ
min
,左支撑力的力臂右支撑的力臂左弯辊力的力臂右弯辊力的力臂和上下工作辊的辊径差之和δdi。
[0026]
所述步骤(b)中,定义轧制过程中的相关参数包含支撑辊辊身长度以及广义轧制压力横向分段为2n+1段,轧制压力非零部分分段为2m+1段,为方便计算使n2=2n+1、n1=2m+1,其中n2为支撑辊辊身长度以及广义轧制压力横向分段总段数,n1为轧制压力非零部分总分段数,设定分段数中的某两段为i,j∈{1,2,...,2n+1},窜动量对挠度的影响函数第j段载荷引起的第i段工作辊和支撑辊挠度变化的影响函数a
ij
、b
ij
,左右支撑力对第i段工作辊和支撑辊挠度变化的影响函数第j段辊间压力值pj,第j段轧制压力值p'j,出口带材分段后每段的厚度hi,入口带材分段后每段的厚度hi,特定机架的总轧制力p
roll
,带材宽度b,轧辊窜动量为ξ,工况计算代码为k(k=1~7),出口带材第i个位置的前张力σ
1i
,出口带材第i个位置的后张力σ
0i
,特定机架下的最大板形影响范围δu
max
,特定机架在特定工况下的板形影响范围δuk,特定机架在特定工况以及最小窜动量时的板形影响范围特定机架在特定工况以及最大窜动量时的板形影响范围特定机架在特定工况以及最小窜动量时带钢分段后每段的板形特定机架在特定工况以及最大窜动量时带钢分段后每段的板形
[0027]
本发明的有益效果是:综合考虑带材宽度在最窄且轧制力最小及最大时的板形影响范围、带材宽度在最宽且轧制力最小及最大时的板形影响范围、带材为平均宽度且轧制力最小、最大及平均值时的板形影响范围并求出七种工况下的综合板形影响范围,进而实现对四辊轧机工作辊窜动对板形影响范围的预报以提高四辊轧机特定机架的带钢板形控制能力。
附图说明
[0028]
图1为本发明的总体流程图;
[0029]
图2为本发明实施例1七种工况下的最大板形影响范围以及最小板形影响范围曲线图;
[0030]
图3为本发明实施例2七种工况下的最大板形影响范围以及最小板形影响范围曲线图。
具体实施方式
[0031]
为了使发明实施案例的目的、技术方案和优点更加清楚,下面将结合实施案例中的附图,对本发明实施案例中的技术方案进行清晰的、完整的描述,显然,所表述的实施案例是本发明一小部分实施案例,而不是全部的实施案例,基于本发明中的实施案例,本领域普通技术人员在没有做出创造性劳动前提下所获得的所有其他实施案例,都属于本发明保护范围。
[0032]
一种四辊轧机工作辊窜动对板形影响范围的预报方法,包含以下步骤:
[0033]
(a)收集设备参数、带材参数及轧制参数;
[0034]
(b)将辊身长度和板带长度进行分段并定义相关参数;
[0035]
(c)初始化工况计算代码k及板形计算误差ε;
[0036]
(d)根据工况计算代码k的数值以及模型对带材宽度以及轧制力进行赋值;
[0037]
(e)基于窜动量影响函数模型计算窜动量为最大值以及最小值时的影响函数计算模型如下:
[0038]
式中:xi、xj是支撑辊的第i个和第j个位置的辊身长度,δx为轧辊辊身以及带材每个段的长度,k1为工作辊影响函数的系数,取值为k1=4.25
×
10-8
。
[0039]
(f)基于影响函数模型计算第j段载荷引起的第i段工作辊和支撑辊挠度变化的影响函数a
ij
、b
ij
以及左右支撑力对第i段工作辊和支撑辊挠度变化的影响函数计算模型如下所示:
[0040][0041]
式中:k2为支撑辊影响函数的系数,取值为k2=3.44
×
10-9
。
[0042]
(g)根据金属塑性变形模型和辊系弹性变形模型计算每段的辊间压力值pi以及轧制压力值计算模型如下所示:
[0043][0044]
式中:k为工作辊与支承辊相互压扁的柔度系数,β为工作辊相对支撑辊的刚性转角,经求解可得β=0,f1、f2为过程函数。
[0045]
(h)根据模型计算带材的入口厚度分布以及出口厚度分布;
[0046]
式中:x1为来料板形所划分的各段板形的位置,x1=iδx+δx/2, ki、为工作辊与轧件间的压扁系数,θ为工作辊与支撑辊的交叉角,δhi为第i段带钢的出入口厚度差。
[0047]
(i)根据模型计算窜动量分别为最大值和最小值时的出口带材板形;
[0048]
式中:kr为前后张应力对轧制力的影响系数,取值为kr=0.015。
[0049]
(j)判断i=n-m+1
…
n+m+1是否成立,若不成立令i=n-m+1
…
n+m+1进入步骤(d),若成立则进入步骤 (k);
[0050]
(k)根据模型计算最小窜动量ξ
min
和最大窜动量ξ
max
的板形影响范围以及在此工况下的板形影响范围;
[0051]
(l)判断工况计算代码值k>7是否成立,若不成立则令k=k+1 进入步骤(d),否则令δu
max
=maxδuk(k=1~7)进入步骤(m);
[0052]
(m)输出四辊轧机的板形影响预报范围(0,δu
max
)。
[0053]
所述步骤(a)中,收集轧制过程中的相关参数包含特定机架支撑辊辊身长度lb,特定机架的工作辊直径dw,支撑辊直径db,带材弹性模量及泊松比e、ν,特定机架下的带钢最小、最大及平均宽度为b
min
、b
max
、b
av
,特定机架下的最小、最大以及平均轧制压力带材轧制时的弯辊力s,后张力、前张力平均值特定机架带钢入口厚度平均值h,出口厚度平均值h,带钢的变形抗力σ,板形计算误差ε,轧辊窜动量最大值ξ
max
,轧辊窜动量最小值ξ
min
,左支撑力的力臂右支撑的力臂左弯辊力的力臂右弯辊力的力臂和上下工作辊的辊径差之和δdi。
[0054]
所述步骤(b)中,定义轧制过程中的相关参数包含支撑辊辊身长度以及广义轧制压力横向分段为2n+1段,轧制压力非零部分分段为 2m+1段,为方便计算使n2=2n+1、n1=2m+1,其中n2为支撑辊辊身长度以及广义轧制压力横向分段总段数,n1为轧制压力非零部分总分段数,设定分段数中的某两段为i,j∈{1,2,...,2n+1},窜动量对挠度的影响函数第j段载荷引起的第i段工作辊和支撑辊挠度变化的影响函数a
ij
、b
ij
,左右支撑力对第i段工作辊和支撑辊挠度变化的影响函数第j段辊间压力值pj,第j段轧制压力值p'j,出口带材分段后每段的厚度hi,入口带材分段后每段的厚度hi,特定机架的总轧制力p
roll
,带材宽度b,轧辊窜动量为ξ,工况计算代码为k(k=1~7),出口带材第i个位置的前张力σ
1i
,出口带材第i个位置的后张力σ
0i
,特定机架下的最大板形影响范围δu
max
,特定机架在特定工况下的板形影响范围δuk,特定机架在特定工况以及最小窜动量时的板形影响范围特定机架在特定工况以及最大窜动量时的板形影响范围特定机架在特定工况以及最小窜动量时带钢分段后每段的板形特定机架在特定工况以及最大窜动量时带钢分段后每段的板形
[0055]
实施例1:
[0056]
以钢种为700l,规格为1500mm
×
9.52mm(宽度
×
厚度)的产品为例,对本发明进行详细说明。
[0057]
首先在步骤(a)中收集轧制过程中的相关参数主要为特定机架支撑辊辊身长度lb=2050mm,特定机架的工作辊直径dw=800mm,支撑辊直径db=1500mm,带材弹性模量及泊松比 e=210000mpa、ν=0.3,特定机架下的带钢最小、最大及平均宽度为b
min
=1500mm、b
max
=1700mm、b
av
=1600mm,特定机架下的最小、最大以及平均轧制压力带材轧制时的弯辊力s=70t,后张力、前张力平均值带钢入口厚度平均值h=12.3mm,出口厚度平均值h=9.52mm,带钢的变形抗力σ=154mpa,板形计算误差ε=0.001,轧辊窜动量最大值ξ
max
=50mm,轧辊窜动量最小值ξ
min
=-50mm,左支撑力的力臂右支撑的力臂左弯辊力的力臂右弯辊力的力臂上下工作辊
的辊径差之和δdi=[-0.00053,-0.02813,-0.05243,-0.07360,-0.09175,-0.10704,-0.1196,
ꢀ‑
0.12960,-0.13715,-0.14240,-0.14550,-0.14658,-0.14580,-0.14328,
ꢀ‑
0.13918,-0.13364,-0.12679,-0.11878,-0.1097,-0.09984,-0.0892,-0.07796,-0.06627,-0.05427,-0.04211,-0.02992,-0.01784,-0.00603, 0.00538,0.01626,0.02645,0.0358,0.04421,0.05150,0.05754, 0.06218,0.06529,0.06672,0.06633,0.06398,0.05953];
[0058]
随后在步骤(b)中定义轧制过程中的相关参数主要为支撑辊辊身长度以及广义轧制压力横向分段为2n+1段,取值n=20,轧制压力非零部分分段为2m+1段,取值m=15,为方便计算使n2=2n+1、 n1=2m+1,其中n2为支撑辊辊身长度以及广义轧制压力横向分段总段数,取值n2=41,n1为轧制压力非零部分总分段数,取值n1=31,设定分段数中的某两段为i,j∈{1,2,...,2n+1},窜动量对挠度的影响函数第j段载荷引起的第i段工作辊和支撑辊挠度变化的影响函数a
ij
、b
ij
,左右支撑力对第i段工作辊和支撑辊挠度变化的影响函数第j段辊间压力值pj,第j段轧制压力值p'j,出口带材分段后每段的厚度hi,入口带材分段后每段的厚度hi,特定机架的总轧制力p
roll
,带材实际宽度b,轧辊窜动量为ξ,工况计算代码为 k(k=1~7),出口带材第i个位置的前张力σ
1i
,出口带材第i个位置的后张力σ
0i
,特定机架下的板形影响范围δu
max
,特定机架在特定工况下的板形影响范围δuk,特定机架在特定工况以及最小窜动量时的板形影响范围特定机架在特定工况以及最大窜动量时的板形影响范围特定机架在特定工况以及最小窜动量时带钢分段后每段的板形特定机架在特定工况以及最大窜动量时带钢分段后每段的板形
[0059]
随后在步骤(c)中初始化工况计算代码k=1,板形计算误差ε=0.001;
[0060]
随后在步骤(d)中根据工况计算代码k的数值以及模型对带材宽度以及轧制力进行赋值即 b=1500mm,p
roll
=1000t;
[0061]
随后在步骤(e)中基于窜动量影响函数模型以窜动量最小值为例,计算影响函数随后在步骤(e)中基于窜动量影响函数模型以窜动量最小值为例,计算影响函数随后在步骤(e)中基于窜动量影响函数模型以窜动量最小值为例,计算影响函数计算模型如下:
[0062][0063]
随后在步骤(f)中基于影响函数模型计算第j段载荷引起的第i 段工作辊和支撑辊挠度变化的影响函数a
ij
、b
ij
及左右支撑力对第i段工作辊和支撑辊挠度变化的影响函数计算模型如下所示,计算为数据矩阵过大,不再展示。
[0064][0065]
随后在步骤(g)中根据金属塑性变形模型和辊系弹性变形模型计算每段的辊间压力值pi=[34.65,33.27,32.06,31.02,30.13, 29.41,28.76,28.17,27.63,27.16,26.73,26.35,26.01,25.72, 25.48,25.27,25.10,24.97,24.88,24.82,24.80,24.82,24.88, 24.97,25.10,25.27,25.48,25.72,26.01,26.35,26.73,27.16, 27.63,28.17,28.76,29.41,30.13,31.02,32.06,33.27,34.65]t 以及轧制压力值
计算模型如下所示:
[0066][0067]
随后在步骤(h)中根据模型计算带材的入口厚度分布hi=[12.24, 12.25,12.26,12.27,12.28,12.29,12.30,12.31,12.31,12.32, 12.32,12.33,12.33,12.33,12.33,12.33,12.33,12.33,12.33, 12.33,12.32,12.32,12.31,12.31,12.30,12.29,12.28,12.27, 12.26,12.25,12.24]mm以及出口厚度分布即hi=[9.47,9.48,9.49, 9.50,9.51,9.51,9.52,9.53,9.53,9.53,9.54,9.54,9.54,9.54, 9.55,9.55,9.55,9.54,9.54,9.54,9.54,9.53,9.53,9.53,9.52, 9.51,9.51,9.50,9.49,9.48,9.47]mm计算模型为:
[0068]
[0069]
随后在步骤(i)中根据模型当轧辊窜动量为最小值时计算板形最小值时计算板形最小值时计算板形以及当窜动量为最大值时计算板形以及当窜动量为最大值时计算板形
[0070]
随后在步骤(j)中经过判断i=n-m+1
…
n+m+1成立则进入步骤(k);
[0071]
随后在步骤(k)中根据模型计算最小窜动量ξ
min
时的板形影响范围时的板形影响范围和最大窜动量时的板形影响范围窜动量时的板形影响范围以及在此工况下的板形影响范围δuk=[2.25,2.25,2.24,2.25,2.25,2.25,2.24]i;
[0072]
随后在步骤(l)中经过多次计算直至工况代码值k>7成立,令δu
max
=maxδuk(k=1~7)=2.25i进入步骤(m);
[0073]
最后在步骤(m)中输出四辊轧机的板形影响预报范围(0,2.25i)。
[0074]
本实施例通过对四辊轧机特定机架的窜动量进行控制,综合考虑带材宽度在最小且轧制力最小及最大时的板形影响范围、带材宽度在最大且轧制力最小及最大时的板形影
响范围、带材为平均宽度且轧制力为最小、最大及平均值时的板形影响范围,最终得到在七种工况下的最大板形影响范围以及最小板形影响范围曲线如图2,进而实现对四辊轧机工作辊窜动对板形影响范围的预报,提高了四辊轧机的板形控制能力。
[0075]
实施例2:
[0076]
以钢种为sphc-s,规格为1400mm
×
11.2mm(宽度
×
厚度)的产品为例,对本发明所述一种适合于四辊轧机工作辊窜动对板形影响范围的预报方法进行详细说明。
[0077]
首先在步骤(a)中收集轧制过程中的相关参数主要为特定机架支撑辊辊身长度lb=2050mm,特定机架的工作辊直径dw=800mm,支撑辊直径db=1500mm,带材弹性模量及泊松比 e=210000mpa、ν=0.3,特定机架下的带钢最小、最大及平均宽度为b
min
=1200mm、b
max
=1600mm、b
av
=1400mm,特定机架下的最小、最大以及平均轧制压力带材轧制时的弯辊力s=30t,后张力、前张力平均值特定机架带钢入口厚度平均值h=13.3mm,出口厚度平均值h=11.2mm,带钢的变形抗力σ=258mpa,板形计算误差ε=0.001,轧辊窜动量最大值ξ
max
=30mm,轧辊窜动量最小值ξ
min
=-30mm,左支撑力的力臂右支撑的力臂左弯辊力的力臂右弯辊力的力臂上下工作辊的辊径差之和δdi=[-0.00053,-0.02813,-0.05243,-0.07360,-0.09175,-0.10704,
ꢀ‑
0.1196,-0.12960,-0.13715,-0.14240,-0.14550,-0.14658,-0.14580,
ꢀ‑
0.14328,-0.13918,-0.13364,-0.12679,-0.11878,-0.1097,-0.09984,
ꢀ‑
0.0892,-0.07796,-0.06627,-0.05427,-0.04211,-0.02992,-0.01784,
ꢀ‑
0.00603,0.00538,0.01626,0.02645,0.0358,0.04421,0.05150, 0.05754,0.06218,0.06529,0.06672,0.06633,0.06398,0.05953];
[0078]
随后在步骤(b)中定义轧制过程中的相关参数主要为支撑辊辊身长度以及广义轧制压力横向分段为2n+1段,取值n=19,轧制压力非零部分分段为2m+1段,取值m=16,为方便计算使n2=2n+1、n1=2m+1,其中n2为支撑辊辊身长度以及广义轧制压力横向分段总段数,取值n2=39,n1为轧制压力非零部分总分段数,取值n1=33,设定分段数中的某两段为i,j∈{1,2,...,2n+1},窜动量对挠度的影响函数第j段载荷引起的第i段工作辊和支撑辊挠度变化的影响函数a
ij
、b
ij
,左右支撑力对第i段工作辊和支撑辊挠度变化的影响函数第j段辊间压力值pj,第j段轧制压力值p'j,出口带材分段后每段的厚度hi,入口带材分段后每段的厚度hi,特定机架的总轧制力p
roll
,带材宽度b,轧辊窜动量为ξ,工况计算代码为k(k=1~7),出口带材第i个位置的前张力σ
1i
,出口带材第i个位置的后张力σ
0i
,特定机架下的最大板形影响范围δu
max
,特定机架在特定工况下的板形影响范围δuk,特定机架在特定工况以及最小窜动量时的板形影响范围特定机架在特定工况以及最大窜动量时的板形影响范围特定机架在特定工况以及最小窜动量时带钢分段后每段的板形特定机架在特定工况以及最大窜动量时带钢分段后每段的板形
[0079]
随后在步骤(c)中初始化工况计算代码k=1,板形计算误差ε=0.001;
[0080]
随后在步骤(d)中根据工况计算代码k的数值以及模型对带材宽度以及轧制力进行赋值即 b=1200mm,p
roll
=1060t;
[0081]
随后在步骤(e)中基于窜动量影响函数模型以窜动量最小值为例,计算影响函数随后在步骤(e)中基于窜动量影响函数模型以窜动量最小值为例,计算影响函数随后在步骤(e)中基于窜动量影响函数模型以窜动量最小值为例,计算影响函数计算模型如下所示:
[0082]
随后在步骤(f)中基于影响函数模型计算第j段载荷引起的第i 段工作辊和支撑辊挠度变化的影响函数a
ij
、b
ij
及左右支撑力对第i段工作辊和支撑辊挠度变化的影响函数计算模型如下所示,计算为数据矩阵过大,不再展示。
[0083][0084]
随后在步骤(g)中根据金属塑性变形模型和辊系弹性变形模型计算每段的辊间压力值pi=[41.91,39.69,37.71,35.96,34.43,33.13, 31.95,30.89,29.95,29.10,28.34,27.68,27.10,26.60,26.17, 25.82,25.53,25.31,25.15,25.06,25.03,25.06,25.15,25.31, 25.53,25.82,26.17,26.60,27.10,27.68,28.34,29.10,29.95, 30.89,31.95,33.13,34.43,35.96,37.71,39.69,41.91]t以及轧制压力值33.13,34.43,35.96,37.71,39.69,41.91]t以及轧制压力值33.13,34.43,35.96,37.71,39.69,41.91]t以及轧制压力值计算模型如下所示。
[0085][0086]
随后在步骤(h)中根据模型计算带材的入口厚度分布值hi=[13.24,13.25,13.26,13.27,13.28,13.29,13.30,13.31,13.31, 13.32,13.32,13.33,13.33,13.33,13.33,13.33,13.33,13.33, 13.33,13.33,13.32,13.32,13.31,13.31,13.30,13.29,13.28, 13.27,13.26,13.25,13.24]mm以及出口厚度值即hi=[11.15,11.16, 11.17,11.18,11.19,11.19,11.20,11.21,11.21,11.22,11.22,11.22, 11.23,11.23,11.23,11.23,11.23,11.23,11.23,11.22,11.22,11.22, 11.21,11.21,11.20,11.19,11.19,11.18,11.17,11.16,11.15]mm 计算模型如下所示:
[0087]
随后在步骤(i)中根据模型当窜动量为最小值时计算板形为为最小值时计算板形为为最小值时计算板形为以及当窜动量为最大值时计算板形为以及当窜动量为最大值时计算板形为
[0088]
随后在步骤(j)中经过判断i=n-m+1
…
n+m+1成立则进入步骤(k);
[0089]
随后在步骤(k)中根据模型计算最小窜动量ξ
min
时的板形影响范围时的板形影响范围和最大窜动量时的板形影响范围窜动量时的板形影响范围以及在此情况下的板形影响范围δuk=[1.49,2.03,2.03,2.25,2.03,2.02,2.03]i;
[0090]
随后在步骤(l)中经过多次计算直至工况代码值k>7成立,令δu
max
=maxδuk(k=1~7)=2.25i进入步骤(m);
[0091]
最后在步骤(m)中输出四辊轧机的板形影响预报范围(0,2.25i)。本实施例通过对四辊轧机特定机架的窜动量进行控制,综合考虑带材宽度在最小且轧制力最小及最大时的板形影响范围、带材宽度在最大且轧制力最小及最大时的板形影响范围、带材为平均宽度
且轧制力为最小、最大及平均值时的板形影响范围,最终得到在七种工况下的最大板形影响范围以及最小板形影响范围曲线如图3,进而实现对四辊轧机工作辊窜动对板形影响范围的预报,提高了四辊轧机的板形控制能力。