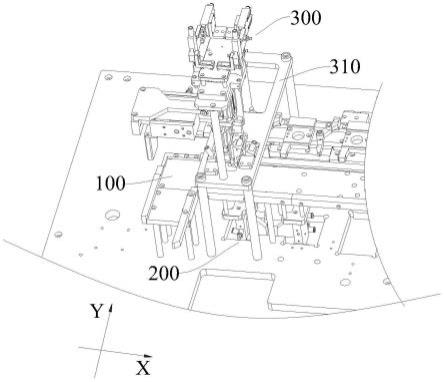
1.本技术涉及电器配件生产技术领域,特别涉及一种自动开关与固定件的装配装置。
背景技术:2.自动开关已广泛应用在家庭或工业用电当中。自动开关一般包括外壳及内部器件,需要通过固定件将内部器件固定在外壳中。目前,在生产过程中,通过自动开关自动装配固定件的设备,将固定件装入自动开关的孔位中,然而在此过程中,由于自动开关外形多为不规则形状,因此难以对自动开关定位,进而导致固定件难以对准自动开关的孔位装配。
3.需要说明的是,在上述背景技术部分公开的信息仅用于加强对本公开的背景的理解,因此可以包括不构成本领域普通技术人员已知的现有技术的信息。
技术实现要素:4.鉴于以上技术问题中的至少一项,本技术提供一种自动开关与固定件的装配装置,解决了由于自动开关外形多为不规则形状,因此难以对自动开关定位,进而导致固定件难以对准自动开关的孔位装配的问题。
5.根据本技术的实施例,提供一种自动开关与固定件的装配装置,包括:
6.承载平台,沿着第一预设方向设置,具有多个第一穿孔;
7.悬空组件,包括多个悬空柱,悬空柱活动穿设于第一穿孔中,使该悬空柱可沿第三方向伸出承载平台;
8.固定件装配组件,包括第一支撑平台、第二支撑平台、固定件压入气缸、第一连接板、第二连接板、固定件压入柱及固定件夹持单元,第一支撑平台沿着第二方向设于承载平台一侧,第二支撑平台设于第一支撑平台上,固定件夹持单元包括多个且对应第一穿孔设于第一支撑平台上,固定件压入气缸沿着第三方向固定于第二支撑平台上,第一连接板固定于固定件压入气缸的气缸轴上,第二连接板固定于第一连接板上,固定件压入柱的一端连接于第二连接板上,该固定件压入柱的另一端活动穿设于固定件夹持单元中;
9.当多个悬空柱悬空自动开关的情况下,固定件压入气缸移动第一连接板、第二连接板,使固定件压入柱在固定件夹持单元中抵接固定件并将固定件压入到自动开关中。
10.在一种实现方式中,悬空组件还包括悬空驱动气缸及第三连接板,悬空驱动气缸沿着第三方向设于承载平台一侧,第三连接板固定于悬空驱动气缸的气缸轴上,第三连接板包括中央连接部、第一延伸部、第二延伸部及第三延伸部,中央连接部与悬空驱动气缸连接,第一延伸部、第二延伸部位于该中央连接部的同一端,第三延伸部位于该中央连接部的另一端,中央连接部、第一延伸部、第二延伸部及第三延伸部上均开设有第一安装孔,悬空柱设置于第一安装孔中。
11.在一种实现方式中,固定件夹持单元包括第四连接板、固定件出料件、入料接管、左夹持块及右夹持块,第四连接板固定于第一支撑平台上,固定件出料件连接于第四连接
板上,入料接管设置于固定件出料件上用以固定件进料至固定件出料件中,左夹持块、右夹持块对称铰接于固定件出料件上,该左夹持块、右夹持块的一端通过弹簧与固定件出料件连接,固定件压入柱活动穿设于固定件出料件中。
12.在一种实现方式中,固定件出料件具有第二穿孔及第三穿孔,第二穿孔贯穿固定件出料件设置用以让固定件压入柱活动穿设,第三穿孔与第二穿孔连接,入料接管与第三穿孔对接,左夹持块上对应第二穿孔设置有第一容纳槽,右夹持块上对应第二穿孔设置有第二容纳槽,第一容纳槽、第二容纳槽共同形成固定件容置空间,固定件容置空间呈上宽下窄结构设置。
13.在一种实现方式中,第二穿孔的中轴线与第三穿孔的中轴线之间形成第一夹角。
14.在一种实现方式中,固定件装配组件还包括分料组件及隔料组件;
15.分料组件包括分料固定板、分料气缸及入料块,分料固定板固定于第二支撑平台上,该分料固定板的相对两端延伸出分选部,每一分选部上具有两个分选接口,每一分选接口与一固定件夹持单元对应,分料气缸沿着第二方向设于分料固定板上,入料块连接于分料气缸的气缸轴上,该入料块的相对两端分别具有与分选接口连通的过料孔;
16.隔料组件对应过料孔设置。
17.在一种实现方式中,隔料组件包括隔料气缸、隔料片、储料器及下料接口,储料器固定于入料块一侧,该储料器中纵向贯穿设置有进料孔,下料接口设置于储料器靠近入料块的一端且与进料孔连通,该下料接口分别与过料孔对应设置,隔料气缸设于储料器一侧,隔料气缸的一输出端与隔料片连接用以伸入储料器中隔断进料孔。
18.在一种实现方式中,储料器的侧壁上开设有与隔料片配合的阻隔空间,该阻隔空间与进料孔连通。
19.在一种实现方式中,装配装置还包括自动开关移料组件;
20.自动开关移料组件包括第一移动模组、第一移动板、第二移动模组、第二移动板及自动开关搬运单元,第一移动模组沿着第一方向设于承载平台一侧,第一移动板连接于第一移动模组的移动端上,第二移动模组沿着第二方向设于第一移动板上,第二移动板连接于第二移动模组的移动端上,自动开关搬运单元设于第二移动板上。
21.在一种实现方式中,自动开关搬运单元包括驱动气缸、驱动杆、固定夹块、铰接拨动件及拨动块,固定夹块具有多个且间隔设置于第二移动板上,铰接拨动件数量与固定夹块相同,该铰接拨动件设于固定夹块一侧,驱动气缸沿着第二方向设于第二移动板上,驱动杆连接于驱动气缸的气缸轴上,且该驱动杆穿过固定夹块,拨动块间隔设置于驱动杆上,该拨动块与铰接拨动件的一端活动配合用以控制铰接拨动件的另一端靠近或远离固定夹块。
22.本技术具有如下技术效果:本装配装置通过悬空组件及固定件装配组件相互配合,使自动开关悬空后再开始固定件定位装配,进而有效保持自动开关在装配时候的平整度,确保固定件能精确地装入自动开关中。
23.下面结合附图与实施例,对本发明进一步说明。
附图说明
24.为了更清楚地说明本发明实施例或现有技术中的技术方案,下面将对实施例或现有技术中所需要使用的附图作简单地介绍,显而易见地,下面描述中的附图仅仅是本发明
的一些实施例,对于本领域普通技术人员来讲,在不付出创造性劳动的前提下,还可以根据这些附图获得其他的附图。
25.图1是本技术实施例中装配装置的结构示意图;
26.图2是本技术实施例中固定件装配组件的第一结构示意图;
27.图3是本技术实施例中悬空组件的结构示意图;
28.图4是本技术实施例中固定件夹持单元的结构示意图;
29.图5是图4中a-a方向的剖视图;
30.图6是本技术实施例中分料组件及隔料组件的结构示意图;
31.图7是本技术实施例中自动开关移料组件的结构示意图;
32.图8是图7中a处的放大结构示意图。
具体实施方式
33.为使本技术的上述目的、特征和优点能够更加明显易懂,下面结合附图对本技术的具体实施方式做详细的说明。在下面的描述中阐述了很多具体细节以便于充分理解本技术。但是本技术能够以很多不同于在此描述的其它方式来实施,本领域技术人员可以在不违背本技术内涵的情况下做类似改进,因此本技术不受下面公开的具体实施例的限制。
34.在本技术的描述中,需要理解的是,术语“上”、“下”、“前”、“后”、“左”、“右”、“竖直”、“水平”、“顶”、“底”“内”、“外”等指示的方位或位置关系为基于附图所示的方位或位置关系,仅是为了便于描述本技术和简化描述,而不是指示或暗示所指的装置或元件必须具有特定的方位、以特定的方位构造和操作,因此不能理解为对本技术的限制。
35.在本技术的描述中,需要理解的是,术语“第一”、“第二”仅用于描述目的,而不能理解为指示或暗示相对重要性或者隐含指明所指示的技术特征的数量。由此,限定有“第一”、“第二”的特征可以明示或者隐含地包括至少一个该特征。在本技术的描述中,“多个”的含义是至少两个,例如两个,三个等,除非另有明确具体的限定。
36.在本技术实施例中,除非另有明确的规定和限定,术语“安装”、“相连”、“连接”、“固定”等术语应做广义理解,例如,可以是固定连接,也可以是可拆卸连接,或成一体;可以是机械连接,也可以是电连接;可以是直接相连,也可以通过中间媒介间接相连,可以是两个元件内部的连通或两个元件的相互作用关系。对于本领域的普通技术人员而言,可以根据具体情况理解上述术语在本技术实施例中的具体含义。
37.如图1至图8所示,根据本技术的实施例,提供一种自动开关与固定件的装配装置,包括:
38.承载平台100,沿着第一预设方向设置,具有多个第一穿孔;
39.悬空组件200,包括多个悬空柱210,悬空柱210活动穿设于第一穿孔中,使该悬空柱210可沿第三方向伸出承载平台100;
40.固定件装配组件300,包括第一支撑平台310、第二支撑平台320、固定件压入气缸330、第一连接板340、第二连接板350、固定件压入柱360及固定件夹持单元370,第一支撑平台310沿着第二方向设于承载平台100一侧,第二支撑平台320设于第一支撑平台310上,固定件夹持单元370包括多个且对应第一穿孔设于第一支撑平台310上,固定件压入气缸330沿着第三方向固定于第二支撑平台320上,第一连接板340固定于固定件压入气缸330的气
缸轴上,第二连接板350固定于第一连接板340上,固定件压入柱360的一端连接于第二连接板350上,该固定件压入柱360的另一端活动穿设于固定件夹持单元370中;
41.当多个悬空柱210悬空自动开关的情况下,固定件压入气缸330移动第一连接板340、第二连接板350,使固定件压入柱360在固定件夹持单元370中抵接固定件并将固定件压入到自动开关中。
42.示例性的,悬空柱210的数量为四个,且悬空柱210的长度均相同。用以活动穿设在第一穿孔当中,并悬空自动开关。进一步的,自动开关上具有不同的凹陷部,悬空柱210穿过第一穿孔并置于这些凹陷部中,然后让自动开关悬空,进而保持自动开关的平整度。
43.在固定件装配组件300使用时,悬空柱210将自动开关升高。固定件置于固定件夹持单元370中,固定件压入气缸330移动第一连接板340及第二连接板350,进而朝向悬空组件200方向移动固定件压入柱360,使固定件压入柱360与固定件夹持单元370中的固定件抵接,并将固定件推入至自动开关中。
44.本装配装置通过悬空组件200及固定件装配组件300相互配合,使自动开关悬空后再开始固定件定位装配,进而有效保持自动开关在装配时候的平整度,确保固定件能精确地装入自动开关中。
45.如图1至图8所示,悬空组件200还包括悬空驱动气缸220及第三连接板230,悬空驱动气缸220沿着第三方向设于承载平台100一侧,第三连接板230固定于悬空驱动气缸220的气缸轴上,第三连接板230包括中央连接部231、第一延伸部232、第二延伸部233及第三延伸部234,中央连接部231与悬空驱动气缸220连接,第一延伸部232、第二延伸部233位于该中央连接部231的同一端,第三延伸部234位于该中央连接部231的另一端,中央连接部231、第一延伸部232、第二延伸部233及第三延伸部234上均开设有第一安装孔,悬空柱210设置于第一安装孔中。
46.悬空组件200在使用时,悬空驱动气缸220移动第三连接板230,进而移动悬空柱210,使悬空柱210沿着第三方向移动。如此实现自动开关相对于承载平台100悬空,方便固定架装配。
47.第三连接板230的结构有利于悬空时自动开关的平衡,具体的,中央连接板的一端具有第一延伸部232、第二延伸部233,在第一延伸部232、第二延伸部233上的悬空柱210用于承载自动开关较为重的一端。中央连接板的另一端具有第三延伸部234,第三延伸部234上的悬空柱210用于承载自动开关较为轻的一端。
48.悬空柱210的形状与第一穿孔的形状匹配,悬空柱210的形状呈圆柱状。在悬空柱210的端部设置有尖端部,用以减少悬空柱210与自动开关之间的接触面积。
49.如图1至图8所示,固定件夹持单元370包括第四连接板371、固定件出料件372、入料接管373、左夹持块374及右夹持块375,第四连接板371固定于第一支撑平台310上,固定件出料件372连接于第四连接板371上,入料接管373设置于固定件出料件372上用以固定件进料至固定件出料件372中,左夹持块374、右夹持块375对称铰接于固定件出料件372上,该左夹持块374、右夹持块375的一端通过弹簧与固定件出料件372连接,固定件压入柱360活动穿设于固定件出料件372中。
50.固定件出料件372具有第二穿孔3721及第三穿孔3722,第二穿孔3721贯穿固定件出料件372设置用以让固定件压入柱360活动穿设,第三穿孔3722与第二穿孔3721连接,入
料接管373与第三穿孔3722对接,左夹持块374上对应第二穿孔3721设置有第一容纳槽,右夹持块375上对应第二穿孔3721设置有第二容纳槽,第一容纳槽、第二容纳槽共同形成固定件容置空间3723,固定件容置空间3723呈上宽下窄结构设置。
51.第二穿孔3721的中轴线与第三穿孔3722的中轴线之间形成第一夹角。
52.示例性的,当固定件从入料接管373依次进入到第三穿孔3722、第二穿孔3721,并最终停在固定件容置空间3723上时。固定件压入柱360将沿着第二穿孔3721下移并与固定件抵接,随着固定件压入柱360继续下移,固定件的宽部撑开左夹持块374、右夹持块375,使左夹持块374、右夹持块375打开,并装配至自动开关中。
53.当左夹持块374、右夹持块375被固定件撑开时,左夹持块374、右夹持块375的上端压缩弹簧。当固定件完全装配入自动开关内时,左夹持块374、右夹持块375的上端受到弹簧的弹力作用,进而复位至初始状态。如此,能保证自动开关的一个空位只装配一个固定件,不会出现漏装或多装的情况,降低发生不良品的概率。
54.另外,第一夹角为锐角,如此能有利于固定件快速经过第三穿孔3722进入到第二穿孔3721中,提升固定件的落料效率。
55.如图1至图8所示,固定件装配组件300还包括分料组件380及隔料组件390;
56.分料组件380包括分料固定板381、分料气缸382及入料块383,分料固定板381固定于第二支撑平台320上,该分料固定板381的相对两端延伸出分选部3811,每一分选部3811上具有两个分选接口3812,每一分选接口3812与一固定件夹持单元370对应,分料气缸382沿着第二方向设于分料固定板381上,入料块383连接于分料气缸382的气缸轴上,该入料块383的相对两端分别具有与分选接口3812连通的过料孔3831;
57.隔料组件390对应过料孔3831设置。
58.示例性的,隔料组件390用于控制固定件有序进入到分料组件380当中,使进料不混乱。分料组件380用以将固定件分配到四个固定件夹持单元370上。
59.分料组件380在使用时,分料气缸382移动入料块383,使位于入料块383前端的过料孔3831对准隔料组件390,此时,隔料组件390将固定件输送至位于入料块383前端的过料孔3831中。分料气缸382移动入料块383,使位于入料块383前端的过料孔3831对准位于分料固定板381前端的分选接口3812,固定件顺着该分选接口3812落入到对应的固定件夹持单元370中。在同一时间,另一个固定件输送至位于入料块383后端的过料孔3831中。分料气缸382移动入料块383,使位于入料块383后端的过料孔3831对准位于分料固定板381后端的分选接口3812,该固定件顺着该分选接口3812落入到对应的固定架夹持单元中。如此,通过分选组件的结构,能同时进行上料及落料固定件的操作,且上料及落料操作是分开单独进行,互不干扰,进而能保证固定件能有序进入到固定件夹持单元370当中。
60.如图1至图8所示,隔料组件390包括隔料气缸391、隔料片392、储料器393及下料接口394,储料器393固定于入料块383一侧,该储料器393中纵向贯穿设置有进料孔,下料接口394设置于储料器393靠近入料块383的一端且与进料孔连通,该下料接口394分别与过料孔3831对应设置,隔料气缸391设于储料器393一侧,隔料气缸391的一输出端与隔料片392连接用以伸入储料器393中隔断进料孔。
61.储料器393的侧壁上开设有与隔料片392配合的阻隔空间,该阻隔空间与进料孔连通。
62.示例性的,固定件由上料机构通过管道进入到进料孔中,通过隔料气缸391控制隔料片392移动,从而使进料孔贯通或闭合,进一步控制固定件在进料孔落料。
63.如图1至图8所示,装配装置还包括自动开关移料组件400;
64.自动开关移料组件400包括第一移动模组410、第一移动板420、第二移动模组、第二移动板430及自动开关搬运单元440,第一移动模组410沿着第一方向设于承载平台100一侧,第一移动板420连接于第一移动模组410的移动端上,第二移动模组沿着第二方向设于第一移动板420上,第二移动板430连接于第二移动模组的移动端上,自动开关搬运单元440设于第二移动板430上。
65.自动开关搬运单元440包括驱动气缸441、驱动杆442、固定夹块443、铰接拨动件444及拨动块445,固定夹块443具有多个且间隔设置于第二移动板430上,铰接拨动件444数量与固定夹块443相同,该铰接拨动件444设于固定夹块443一侧,驱动气缸441沿着第二方向设于第二移动板430上,驱动杆442连接于驱动气缸441的气缸轴上,且该驱动杆442穿过固定夹块443,拨动块445间隔设置于驱动杆442上,该拨动块445与铰接拨动件444的一端活动配合用以控制铰接拨动件444的另一端靠近或远离固定夹块443。
66.示例性的,第一移动模组410为实现直线移动的机构,可以为直线电机,可以为丝杆传动机构,亦或是气缸驱动滑块机构,在此不作具体限定。其中,第一移动模组410实现自动开关搬运单元440沿着第一方向移动。
67.第二移动模组为实现直线移动的机构,可以为直线电机,可以为丝杆传动机构,亦或是气缸驱动滑块机构,在此不作具体限定。其中,第二移动模组实现自动开关搬运单元440沿着第二方向移动。
68.另外,固定夹块443的一端朝向承载平台100延伸出第一夹持部4431,铰接拨动件444的一端朝向承载平台100延伸出第二夹持部4441,第一夹持部4431与第二夹持部4441共同配合下降自动开关夹持。
69.其次,在铰接拨动件444的另一端上设置有与拨动块445配合的转动轮446。拨动块445具有第一接触面4442及第二接触面4443,第一接触面4442与第二接触面4443连接,且第一接触面4442与第二接触面4443之间形成第二夹角。
70.当驱动气缸441推动驱动杆442时,拨动块445的第二接触面4443与铰接拨动件444的转动轮446接触,从而使铰接拨动件444的另一端朝向固定夹块443靠近,进而夹紧自动开关。
71.当驱动气缸441拉动驱动杆442时,拨动块445的第一接触面4442与铰接拨动件444的转动轮446接触,使铰接拨动件444的另一端远离固定夹块443。当拨动块445的第一接触面4442拨动铰接拨动件444的转动轮446到一定程度后,拨动块445的第二接触面4443朝向铰接拨动件444的转动轮446。
72.以上,仅是本技术的较佳实施例而已,并非对本技术作任何形式上的限制。任何熟悉本领域的技术人员,在不脱离本技术技术方案范围情况下,都可利用上述揭示的方法和技术内容对本技术技术方案做出许多可能的变动和修饰,或修改为等同变化的等效实施例。故凡是未脱离本技术技术方案的内容,依据本技术之形状、构造及原理所作的等效变化,均应涵盖于本技术的保护范围内。