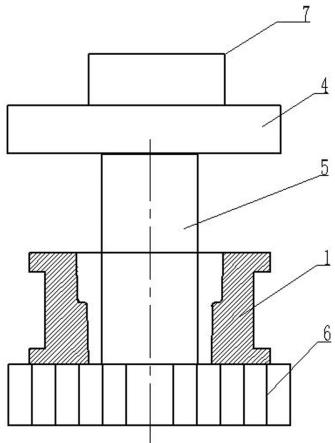
1.本发明属于锻造技术领域,涉及一种通过设计合理的模具和胎模锻造,可以使用连铸坯代替精炼钢锻造,只需要一次镦粗就能有效解决偏心、机加余量大问题的压机活塞锻造模具及成型方法,材料在充模过程中受到胎模壁及上下面360
°
压应力,达到中心压实效果,两端面凹心及内部质量能得到有效保证。
背景技术:2.dj-850型压机活塞属于金刚石六面顶压机的关重零部件,产品探伤质量要求高,超声波探伤不允许存在φ2.0以上单个缺陷,但该产品长度只有700mm,直径φ750-φ885,长径比太小,只有0.79;属于短粗型台阶轴类锻件,传统锻造工艺一般采用精炼钢,通过压钳把操纵机辅助加持,通过多次镦粗、拔长、刻痕、法兰局部镦粗工艺锻造成型,这种工艺复杂且成本高,并且存在以下四点不足:
①
需多次镦粗;
②
同轴度保证能力差,容易偏心;
③
锻造机加余量大(一般直径需要25~35mm机加余量);
④
拔长时砧宽比只有0.1~0.3,产品心部锻透性差,两端产生凹心,从而严重影响产品的内部质量及出材率,不利用企业生产的成本控制。
技术实现要素:3.本发明的目的在于克服现有技术中因该产品长径比小、直径大、油压机自由锻造所面临的镦粗次数多、同轴度保证能力差、机加余量大、两端凹心导致的材料利用率低、成本高的不足而提供一种压机活塞锻造模具及成型方法,可以使用连铸坯代替精炼钢锻造,不但可保证探伤合格,还能减少镦粗次数、保证同轴度、减少机加余量、避免两端凹心、提高材料利用率,大大降低生产成本。
4.本发明技术方案是这样实现的:一种压机活塞锻造模具,该模具包括成型胎模、脱模垫环、脱模冲子三部分;所述成型胎模,材料选用h13热做模具钢作为模具的材料,胎模加工前先通过镦粗-冲孔-扩孔-超细化处理,通过锻造成型工艺制作完成成型胎模锻坯,并非铸造成型,以满足冲模时的高强度需要,避免冲模时模具开裂,然后将其中心孔加工成阶梯孔,阶梯孔分为两部分,第一部分为成型活塞的法兰,第二部分为成型活塞的轴身,所述第一部分和第二部分中心线为同一条中心线,为顺利脱模,其中第一部分法兰脱模角度和第二部分轴身脱模角度均为1.2~1.5
°
,两台阶相交部位倒圆弧r20~30;所述成型胎模的外径两端加工成作为吊耳的台阶,用作操纵机加持翻料或吊装时使用,完成成型胎模制作;所述脱模垫环为上端面开设有一个定位槽,中心为内孔,所述定位槽、脱模垫环、成型胎模三者中心线重合,锻造脱模时,法兰端朝下,坐落在脱模垫环的定位槽中,在坯料的上端面放置脱模冲子,通过油压机锤头对脱模冲子进行施压,完成脱模。
5.所述成型胎模锻坯成型部分的外径φ1500mm,总高度700mm,成型胎模锻坯的第一部分为成型活塞的法兰,其孔径大小为φ885mm,孔深310mm,第二部分是成型活塞的轴身,
其孔径大小为φ755mm,深度为390mm。
6.所述成型胎模锻坯成型部分的外径两端加工成高度100mm,深度100mm的一个台阶,作为吊耳,用作操纵机加持翻料或吊装时使用,完成成型胎模制作。
7.所述脱模垫环的尺寸为外径φ1800mm,内孔φ1100mm,高度300mm,定位槽的深度尺寸为50mm,直径φ1550mm(图3)。
8.一种压机活塞锻造模具的成型方法,是按照如下步骤成型的:步骤1)、首先设计模具,该模具包括成型胎模、脱模垫环、脱模冲子三部分;所述成型胎模,材料选用h13热做模具钢作为模具的材料,胎模加工前先通过镦粗-冲孔-扩孔-超细化处理等锻造成型工艺制作完成成型胎模锻坯,并非铸造成型,以满足冲模时的高强度需要,避免冲模时模具开裂,成型胎模锻坯成型部分的外径φ1500mm,总高度700mm,内孔φ730mm,然后将中心加工成阶梯孔,阶梯孔分为两部分,第一部分是成型活塞的法兰,其孔径大小为φ885mm,孔深310mm;第二部分是成型活塞的轴身,其孔径大小为φ755mm,深度为390mm;所述第一部分和第二部分中心线为同一条中心线,为顺利脱模,其中第一部分法兰脱模角度和第二部分轴身脱模角度均为1.2~1.5
°
,两台阶相交部位倒圆弧r20~30,所述胎模成型部分,外径两端加工成高度100mm,深度100mm的一个台阶,作为吊耳,用作操纵机加持翻料或吊装时使用,完成成型胎模制作;所述脱模垫环,尺寸为外径φ1800mm,内孔φ1100mm,高度300mm,上端面有一个定位槽,定位槽的深度尺寸为50mm,直径φ1550mm;所述定位槽、脱模垫环、成型胎模三者中心线重合,锻造脱模时,法兰端朝下,坐落在脱模垫环的定位槽中,在坯料的上端面放置脱模冲子,通过油压机锤头对脱模冲子进行施压,完成脱模;步骤2)、选择φ600连铸坯,加热至锻造温度并保温4~6小时后,出炉锻造,锻造前将所述胎模放置在旋转镦粗台中心位置,然后将加热好的连铸坯立放在所述成型胎模中,再在连铸坯端面盖上平面镦粗板进行镦粗,镦粗至h=720~750时,旋转镦粗台每转动30
°
~60
°
时,上平砧施压一次,采用上砧旋压,对活塞法兰端面进行精整成型,因在充模过程中,锻件外观尺寸完全被按照成型胎模的型腔进行填充,而成型胎膜的两个阶梯孔型腔中心线相互重合,因此锻件的两个台阶不会出现偏心缺陷,从而可以减小机加余量至10~20mm;在金属填充过程中,因连铸坯两端面受到轴向压应力,四面受到成型胎模壁的反作用压应力,这样锻件端面无凹心,心部锻透性好,既能保证产品内部质量,又能提高材料利用率;步骤3)、脱模:油压机操纵机将充型好的锻件及成型胎模上下翻转180
°
,操纵机夹持成型胎模放置在脱模垫环的定位槽中,然后在成型胎模上放置脱模冲子,压机锤头对脱模冲子施压脱模,完成脱模。
9.本发明具有如下有益效果:采用本发明锻造的dj-850型压机活塞锻件,可以使用连铸坯代替精炼钢锻造,不但可保证探伤合格,还能减少镦粗次数、保证同轴度、减少机加余量、两端无凹心、提高材料利用率,大大降低生产成本。
附图说明
10.图1 为本发明所述的压机活塞锻坯图。
11.图2 为本发明所述的成型胎模剖面图。
12.图3 为本发明所述的脱模垫环剖面图。
13.图4为本发明所述的脱模冲子。
14.图5 为本发明所述的冲模示意图。
15.图6 为本发明所述的锤头旋压图。
16.图7 为本发明所述的脱模图。
17.图1~图7标注为:1、成型胎膜;2、脱模垫环;3、脱模冲子;4、平面镦粗板;5、φ600连铸坯;6、旋转镦粗台;7、锤头。
具体实施方式
18.实施例1:以锻造如图1所示的活塞杆锻坯为例进行说明,(图纸尺寸单位为mm),所需锻坯重量2900kg,提前将φ600连铸坯进行锯切下料,锯切长度1375mm,连铸坯重量3050kg,连铸坯利用率95%。具体锻造方法如下:考虑到锻造退火后锻件直径尺寸存在热收缩,锻坯直径热热缩系数按1.5%考虑设计所需模具尺寸,胎模尺寸与锻坯尺寸存在的差异主要是因为考虑到公差及热收缩引起,属于工艺正常现象。
19.步骤1)、设计合理的锻造模具;该模具包括成型胎模、脱模垫环、脱模冲子三部分;所述模具应具备以下特点:所述成型胎模,用h13作为胎模的选用材料,胎模加工前先通过镦粗-冲孔-扩孔-超细化处理等锻造成型工艺制作完成胎模锻坯,非铸造成型,以满足冲模时的高强度需要,避免冲模时模具开裂;锻造成型后的成型胎模坯外径φ1500mm,总高度700mm,内孔φ730mm,然后将坯的内孔加工成阶梯孔,阶梯孔分为两部分,第一部分用来成型活塞的法兰,其孔径大小为φ885mm,孔深310mm,第二部分用来成型活塞的轴身,其孔径大小为φ755mm深度为390mm(图2);所述第一部分和第二部分中心线为同一条中心线,为了方便脱模,其中第一部分法兰脱模角度和第二部分轴身脱模角度均设计为1.3
°
,两台阶相交部位倒圆弧r20~30。所述胎模成型部分,外径两端加工成高度100,深度100的一个台阶,作为吊耳,以用作吊装或者操纵机加持翻料(图2所示)。
20.所述脱模垫环,尺寸为外径φ1800mm,内孔φ1100mm,高度300mm,其中一个端面上有一定位槽,定位槽的深度尺寸为50mm,直径φ1550(如图3所示);所述定位槽、脱模垫环、成型胎模三者中心线重合,锻造脱模时,法兰端朝下,坐落在脱模垫环的定位槽中,在坯料的端面放置脱模冲子,通过油压机锤头对脱模冲子进行施压,完成脱模(图7)。
21.步骤2)、加热:锻造前先将所述成型胎模放置在旋转镦粗台中心,将φ600mm*1375mm连铸坯加热到1230
±
10℃保温5h,到温出炉锻造;步骤3)、冲模:再将加热好的连铸坯,快速出炉吊运,立料放置在成型胎模中,然后将平面镦粗板放置在连铸坯端面中心位置(如图4所示),油压机锤头通过镦粗进行胎模填充,先将连铸坯镦粗至h=720mm时预成型,再将平面镦粗板吊走,开始采用锤头进行旋压成型,以便使胎模局部充分填充,旋转镦粗台每旋转30~60
°
,锤头施压一次,通过多次反复修整施压填充,完成充模(图6),开始进行下一步的脱模。(解释:因在充模过程中,锻件外观尺寸完全被按照成型胎模的型腔进行填充,而成型胎膜的两个阶梯孔型腔中心线相互重合,因此活塞锻件的两个台阶不会出现偏心缺陷,从而可以减小机加余量;在金属填充过程中,
因连铸坯两端面受到轴向压应力,四面受到成型胎模壁的反作用压应力,这样活塞锻件端面无凹心,心部锻透性好,既能保证产品内部质量,又能提高材料利用率)。
22.步骤4)、脱模;操纵机加持胎模外径,将胎模及充模好的坯料上下翻转180
°
,法兰端朝下,放置在脱模垫环的定位槽中,然后在坯料的端面放置脱模冲子(如图6所示),通过油压机锤头对脱模冲子进行施压,完成脱模。
23.通过此方法锻造的dj-850压机活塞,外观尺寸、同轴度得到很好的保证,基本达到近径成型,机加余量小,端面无凹心,利用率与精炼钢相比,至少能提高15%,利用率得到大大提高,内部质量能达到jb4730-2005(i级)要求,即满足单个分散缺陷≤φ2.0的技术要求,达到了用户使用要求。