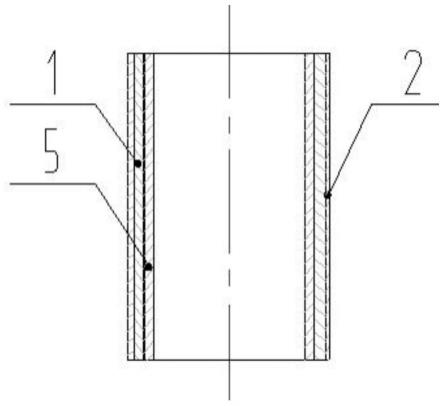
一种不锈钢-铜复合薄壁管制造方法
1.技术领域
2.本发明属于金属复合材料制造领域,具体涉及到一种不锈钢-铜复合薄壁管的制造方法。
背景技术:3.铜与不锈钢两种生活中常见材料,在性能和用途上有各自的优缺点,铜有良好的导热、导电性能,但退火后强度低,易变形;不锈钢具有一定的强度、耐腐蚀的优点,所以在某些服役环境下常常需要使用兼具两者优点的不锈钢-铜复合结构。
4.本发明介绍了一种用于制作真空器件売体、热交换器等的不锈钢-铜复合薄壁管制造方法,以不锈钢材料为外层,铜材料为内层,不锈钢管和铜管之间通过采用一系列变形和连接技术达到紧密结合。成型后的不锈钢-铜复合薄壁管紧密结合,机械强度好,且该复合材料既具有铜优异的散热、导电能力,又具备一定强度。
技术实现要素:5.发明目的:本发明是为了解决现有技术的不足,提供一种机械强度好、散热、导电能力的不锈钢-铜复合薄壁管制造方法。
6.技术方案:为了实现以上目的,本发明采取的技术方案为:一种不锈钢-铜复合薄壁管制造方法,其包括如下步骤:(1)根据设计需要,对不锈钢管外径和内径进行车加工,以获得设计需要的尺寸; (2)将加工好的不锈钢管和铜棒进行清洗、备用;(3)对不锈钢管内、外表面进行镀膜;(4)对表面镀膜后的不锈钢管进行加热,使不锈钢管与铜棒间形成400℃~500℃的温差,不锈钢管和铜棒处于过盈配合状态下,进而将铜棒插进不锈钢管内;(5)在准备好的紧箍模具内刷一层氧化铝粉末,将步骤(4)装配好的不锈钢-铜组合放入紧箍模具内,使两者紧密配合,然后将紧箍模具放入在烧氢炉中,选择合适的焊接温度和时间进行瞬时液相扩散焊接;(6)焊接完成后,对不锈钢-铜组合进行加工,即以不锈钢外径为基准,将铜棒加工成需要的壁厚尺寸,获得所需的不锈钢-铜复合薄壁管。
7.作为优选方案,以上所述的一种不锈钢-铜复合薄壁管制造方法,步骤(1)不锈钢管内径d1与铜棒外径d2两者的过盈量,d2-d1控制在0.02mm-0.05mm范围内。
8.作为优选方案,以上所述的一种不锈钢-铜复合薄壁管制造方法,步骤(2)中,加工好的不锈钢管清洗方法为:(2.11)超声去油,将加工好的不锈钢管放入50℃-70℃的碱溶液中超声20~30min;(2.12)水洗,用自来水将超声过的不锈钢管表面碱溶液冲洗干净;
(2.13)脱水,将水洗后的不锈钢管浸入乙醇溶液15s-30s,去除表面水分;(2.14)烘干,将水洗干净的不锈钢管用热风烘干备用。
9.作为优选方案,以上所述的一种不锈钢-铜复合薄壁管制造方法,步骤(2)中,加工好的铜棒清洗方法为:(2.21)超声去油,将加工好的铜棒放入50℃-70℃的碱溶液中超声20-30min;(2.22)水洗,用自来水将超声过的铜棒表面的碱溶液冲洗干净;(2.23)酸洗,将铜棒放在铬酸抛光铜溶液中浸泡5s-10s;(2.24)水洗,用自来水冲洗酸洗过的铜棒;(2.25)酸洗,将铜棒在50%体积浓度的盐酸溶液中浸泡5s-10s;(2.26)水洗,用自来水冲洗酸洗过的铜棒;(2.27)酸洗,将铜棒在铬酸溶液中浸泡4s-6s;(2.28)水洗,用自来水冲洗铬酸洗过的铜棒;(2.29)脱水,将水洗后的铜棒浸入乙醇溶液,去除表面水分;(2.30)烘干,将水洗干净的铜棒用热风烘干表面,备用。
10.作为优选方案,以上所述的一种不锈钢-铜复合薄壁管制造方法,步骤(3)不锈钢管内、外表面镀膜的方法为:(3.1)电镀液配制:将质量比3:3:1:3的去离子水、氰化银、游离氰化和碳酸钾混匀配成电镀液;(3.2)预镀银将洗净好的不锈钢管用镍丝捆扎好放入具有氰化镀银溶液的电镀槽中;在电流密度1-2 a/dm
2 下预电镀2-3min;(3.3)镀银将电流密度设为0.5~1 a/dm
2 继续进行电镀,直至不锈钢表面镀层厚度达到0.01mm~0.02mm,最终测量不锈钢管含镀层的内径尺寸为d1;(3.4)水洗,取出电镀槽中的不锈钢管,用自来水冲洗干净;(3.5)脱水,将水洗后的不锈钢浸入乙醇溶液,去除表面水分;(3.6)烘干,将水洗干净的不锈钢用热风烘干表面,并去除表面镍丝,备用。
11.作为优选方案,以上所述的一种不锈钢-铜复合薄壁管制造方法,步骤(5)在准备好的紧箍模具内刷一层氧化铝粉末,将步骤(4)装配好的不锈钢-铜组合放入钨材质的紧箍模具内,使两者紧密配合,然后将紧箍模具放入在烧氢炉中,选择钎焊温度750~780℃,保温5-7min进行瞬时液相扩散焊接;即不锈钢内表面和铜棒之间的镀膜层加热到一定温度后,镀膜层融化,在不锈钢和铜棒之间形成瞬间液相膜,最终使得不锈钢管与铜牢固连接,提高不锈钢管与铜的可靠性。
[0012] 作为优选方案,以上所述的一种不锈钢-铜复合薄壁管制造方法,所述的碱溶液由质量比为8:6:1:1的去离子水、洗洁剂、焦磷酸钠和edta 二钠配制成。
[0013]
有益效果:相比现有技术本发明具有以下优点:本发明采用过盈配合装配方法,即利用材料热胀冷缩的原理,对不锈钢管加热,增大与铜棒间的温差,进而实现两者的紧密结合;采用瞬时液相扩散焊接的方式,在不锈钢和铜之间添加镀膜层作为中间夹层,加热到一定温度后,中间层镀膜融化,在不锈钢和铜表面
形成瞬间液相膜,起到焊料作用,最终使得不锈钢管与铜牢固连接,提高不锈钢管与铜的可靠性,抗拉强度可达300mpa;采用不锈钢-中间镀层-铜结构形式,在不锈钢内表面进行镀膜,增加连接可靠性,又保护不锈钢管外表面不被氧化,成型后的不锈钢-铜复合薄壁管紧密结合,机械强度好,且该复合材料既具有铜优异的散热、导电能力,又具备一定强度。
附图说明
[0014]
图1为覆膜后的不锈钢管的结构示意图。
[0015]
图2为铜棒的结构示意图。
[0016]
图3为不锈钢-铜组合后的结构示意图。
[0017]
图4为放入紧箍模具内的不锈钢-铜组合的结构示意图。
[0018]
图5为不锈钢-铜复合薄壁管的结构示意图。
具体实施方式
[0019]
下面结合具体实施对本发明的技术方案进行进一步详细地说明,本发明所述的技术特征或连接关系没有进行详细描述的部分均为采用的现有技术。
[0020]
实施例1一种不锈钢-铜复合薄壁管制造方法,其包括如下步骤:(1)根据设计需要,对不锈钢管外径和内径进行车加工,以获得设计需要的尺寸;(2)将加工好的不锈钢管1和铜棒3进行清洗、备用;加工好的不锈钢管1清洗方法为:(2.11)超声去油,将加工好的不锈钢管1放入50℃-70℃的碱溶液(由质量比为8:6:1:1的去离子水、洗洁剂、焦磷酸钠和edta 二钠配制成)中超声30min;(2.12)水洗,用自来水将超声过的不锈钢管1表面碱溶液冲洗干净;(2.13)脱水,将水洗后的不锈钢管1浸入乙醇溶液15s-30s,去除表面水分;(2.14)烘干,将水洗干净的不锈钢管用热风烘干备用。
[0021]
加工好的铜棒清洗方法为:(2.21)超声去油,将加工好的铜棒3放入50℃-70℃的碱溶液(由质量比为8:6:1:1的去离子水、洗洁剂、焦磷酸钠和edta 二钠配制成)中超声20-30min;(2.22)水洗,用自来水将超声过的铜棒3表面的碱溶液冲洗干净;(2.23)酸洗,将铜棒放在铬酸抛光铜溶液中浸泡5s-10s;(2.24)水洗,用自来水冲洗酸洗过的铜棒3;(2.25)酸洗,将铜棒在50%体积浓度的盐酸溶液中浸泡5s-10s;(2.26)水洗,用自来水冲洗酸洗过的铜棒3;(2.27)酸洗,将铜棒3在铬酸溶液中浸泡4s-6s;(2.28)水洗,用自来水冲洗铬酸洗过的铜棒;(2.29)脱水,将水洗后的铜棒3浸入乙醇溶液,去除表面水分;(2.30)烘干,将水洗干净的铜棒3用热风烘干表面,备用。
[0022]
(3)对不锈钢管内、外表面进行镀膜:具体方法为:将清洗好的不锈钢管1用镍丝捆扎好放入电镀槽中,选用银作为镀层材料,进行电镀具体方法为:
(3.1)电镀液配制:将质量比3:3:1:3的去离子水、氰化银、游离氰化和碳酸钾混匀配成电镀液;(3.2)预镀银将洗净好的不锈钢管用镍丝捆扎好放入具有氰化镀银溶液的电镀槽中;在电流密度1.5a/dm
2 下预电镀2min;(3.3)镀银将电流密度设为0.5~1 a/dm
2 继续进行电镀,直至不锈钢表面镀层厚度达到0.01mm~0.02mm,最终测量不锈钢管含镀层的内径尺寸为d1;(3.4)水洗,取出电镀槽中的不锈钢管,用自来水冲洗干净;(3.5)脱水,将水洗后的不锈钢浸入乙醇溶液,去除表面水分; (3.6)烘干,将水洗干净的不锈钢用热风烘干表面,并去除表面镍丝,备用。
[0023]
镀膜后的不锈钢管内径d1与加工后的铜棒外径d2两者的过盈量,d2-d1控制在0.02mm-0.05mm范围内。
[0024]
(4)对表面镀膜后的不锈钢管进行加热,使不锈钢管与铜棒间形成400℃~500℃的温差,不锈钢管和铜棒处于过盈配合状态下,进而将铜棒插进不锈钢管内;(5)如图4,在准备好的紧箍模4内刷一层氧化铝粉末,将步骤(4)装配好的不锈钢-铜组合放入钨材质的紧箍模具内,使两者紧密配合,然后将紧箍模具放入在烧氢炉中,选择钎焊温度760℃,保温6min进行瞬时液相扩散焊;即不锈钢内表面和铜棒之间的镀膜层加热到一定温度后,镀膜层融化,在不锈钢和铜棒之间形成瞬间液相膜,最终使得不锈钢管与铜牢固连接,提高不锈钢管与铜的可靠性。
[0025]
(6)焊接完成后,对不锈钢-铜组合进行加工,即以不锈钢外径为基准,将铜棒加工成需要的壁厚尺寸的铜管5,获得所需的不锈钢-铜复合薄壁管。如图5所示。
[0026]
本发明提供的一种不锈钢-铜复合薄壁管制造方法,该方法操作简单,可靠性高,机械强度好,抗拉强度可达300mpa。
[0027]
可以理解地是,以上关于本发明的具体描述,仅用于说明本发明而并非受限于本发明实施例所描述的技术方案,这里无法对所有的实施方式予以穷举,本领域的普通技术人员应当理解,仍然可以对本发明进行修改或等同替换,以达到相同的技术效果;只要满足使用需要,都在本发明的保护范围之内。