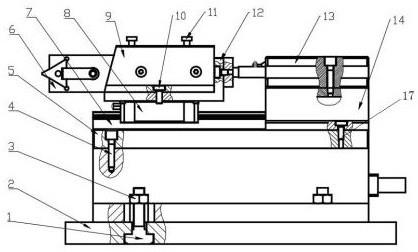
1.本发明涉及一种机械工程领域,具体涉及一种安装在车床上的摩擦磨损试验装置及其工作方法。
2.
背景技术:3.在切削加工过程中,为了研究刀具的力学性能以及抗磨损性能,需要对刀具进行摩擦磨损试验;在现有技术中,普遍都是在球-盘、销-盘摩擦磨损试验机中进行摩擦磨损试验,而由于设备结构原因,试验中存在着磨擦速度范围有限、加载力矩较小、摩擦震动大、对磨配件制备繁琐等问题,并且,在摩擦磨损试验机上进行的模拟试验并不能代替真正车床上刀具的磨损情况。
4.为解决上述的技术问题,现有学者也设计应用在车床上辅助进行摩擦磨损试验的装置,通过采用弹簧组件提供正压力,采用螺栓固定刀片进行试验,而这种结构存在着刚性不足、在大载荷情况下弹簧组件疲劳变形使得正压力减小的缺陷,当刀具发生较大磨损时,正压力会发生改变;另外也有学者将刀架改造并设置液压恒力设备,结构复杂,存在污染的风险。
5.
技术实现要素:6.本发明根据上述现有技术存在的问题进行了改进,即本发明解决的技术问题是提供了一种安装在车床上的摩擦磨损试验装置及其工作方法,该装置结构简单、设计合理、使用方便。
7.本发明安装在车床上的摩擦磨损试验装置,其特征在于:包括底板和设在底板上的测力仪,底板固定连接在数控车床的刀架上,所述测力仪的上方固定设有垫板和固定在垫板上的直线导轨,所述直线导轨上滑动设有导轨滑块,所述直线导轨的后侧部固定设有u型垫板,所述导轨滑块上设有l型助推板和固定在l型助推板上的u型紧固板,所述u型紧固板内可拆固定连接有刀杆组件,所述u型垫板上固定设有双轴气缸,所述双轴气缸的伸缩杆的输出端固定连接l型助推板的后部,所述刀杆组件上连接有刀片。
8.进一步的,上述测力仪的下部通过t型螺栓连接所述底板。
9.进一步的,上述测力仪的上部通过第一内六角螺栓与垫板固定连接;所述u型垫板通过第二内六角螺栓与垫板固定连接。
10.进一步的,上述u型紧固板通过第三内六角螺栓与导轨滑块固定连接。
11.进一步的,上述刀杆组件包括刀杆基体、刀片和压头,所述刀杆基体设在u型紧固板的槽内,刀片通过定位螺栓将其定位在刀杆基体上的刀槽,所述压头的前端压置在刀片的表面上,所述压头的后端通过双头内六角螺栓锁紧在刀杆基体上。
12.进一步的,上述u型紧固板的上部和侧部设有第四内六角螺栓,第四内六角螺栓的
内端抵压在刀杆基体的上表面和侧表面上。
13.本发明安装在车床上的摩擦磨损试验装置的工作方法,其特征在于:包括步骤如下:(1)当摩擦磨损试验开始时:根据试验所需的正压力fn,由p=fn/s求出需要在双轴气缸中加载的气压p,其中s为双轴气缸腔内活塞接触气压面的表面积;(2)在双轴气缸输入稳定的气压p,使得气缸活塞推动l型助推板和轨滑块以及刀杆组件往左边移动,刀杆组件中的刀片与工件接触进行摩擦磨损试验;(3)测力仪在摩擦磨损试验进行时完成对正压力fn的监测以及摩擦力ff的收集;(4)根据求出刀具与工件的摩擦系数μ=fn/ff;(5)当摩擦磨损试验结束时:双轴气缸中的气压减小,气缸活塞往右边移动,带动刀杆组件往右边移动,刀片与工件分离,摩擦磨损试验结束。
14.本发明装置与现有技术相比具有以下有益效果:结构简单、设计合理,本装置采用的动力装置为双轴气缸,相较于恒力弹簧组件具有更好的刚性以及稳定性,减小了由振动带来的数据误差,当刀片发生较大磨损时,刀片正压力也不会发生改变;相较于液压恒力装置,气动装置更加环保,造价更低更安全;刀杆组件设计更加匹配市面上刀片形状的多样化,适用面更广,且刀片的装夹、定位更加简便、效率化,大大提高了试验效率;测力组件的安装对于数据的监测与收集起到了重要作用,提高了实验数据的准确性和精度。
15.附图说明
16.图1是本发明的主视构造示意图;图2是图1的左视图;图3是图1的俯视图;图4、5是刀杆组件的a、b面的主视构造示意图;图6是图4的c-c剖视图;图中:1-t型螺栓,2-底板,3-m6六角螺母,4-第一内六角螺栓(psba-3-16),5-垫板,6-刀杆组件,7-直线导轨,8-导轨滑块,9-u型紧固板,10-第三内六角螺栓(psba-3-10),11-第四内六角螺栓(psba-3-8),12-l型助推板,13-双轴气缸,14-u型垫板,15-内六角螺栓(psba-3-12),16-测力仪,17-第二内六角螺栓psba-3-12,61-刀杆基体,62-三角刀片,63-定位螺栓,64-刀片压头,65-双头内六角螺栓。
17.具体实施方式
18.下面结合附图和具体实施方式对本发明做进一步详细说明;如图1-6所示,在本实施例中,安装在车床上的摩擦磨损实验装置,包括进给组件、刀杆组件和测力组件,用以进行摩擦磨损试验;具体包括底板2和设在底板上的测力仪16,底板2固定连接在数控车床的刀架上,测力仪的上方固定设有垫板5和固定在垫板上的直线导轨7,所述直线导轨7上滑动设有导轨滑块8,所述直线导轨7的后侧部固定设有u型垫板14,所述导轨滑块8上设有l型助推板12和固定在l型助推板上的u型紧固板9,所述u型紧固板9内可拆固定连接有刀杆组件6,所述u型垫板上固定设有双轴气缸13,所述双轴气缸13的伸缩杆的输出端固定连接l型助推板12
的后部,所述刀杆组件上连接有刀片62。
19.其中进给组件包括双轴气缸13、l型助推板12和u型垫板14等,其中测力组件包括底板2和测力仪16;工作时,根据所需的磨擦速度将数控车床的刀架移动到一定的位置,让车床主轴旋转,使其模拟车削过程,当试验开始时,进给组件中的双轴气缸13内部输入稳定气压,使进给组件带动刀杆组件向左运动完成摩擦磨损试验,测力组件完成水平方向正压力的监测与竖直方向摩擦力的收集工作。
20.其中测力仪16的下部通过t型螺栓1连接所述底板2;测力仪16的上部通过第一内六角螺栓4与垫板5固定连接;所述u型垫板14通过第二内六角螺栓17与垫板5固定连接;u型紧固板14通过第三内六角螺栓10与导轨滑块8固定连接;u型紧固板的上部和侧部设有第四内六角螺栓11,第四内六角螺栓的内端抵压在刀杆基体的上表面和侧表面上。
21.其中刀杆组件6包括刀杆基体61、刀片62和压头64,刀杆基体设在u型紧固板的槽内,刀片通过定位螺栓63将其定位在刀杆基体上的刀槽,所述压头64的前端压置在刀片62的表面上,所述压头的后端通过双头内六角螺栓65锁紧在刀杆基体上;刀具基体61的对称面a面和b面设有三角形和正方形凹槽,用来安装三角形和正方形刀片,两边的定位方式和夹紧方式相同。
22.具体的刀片62定位安装方式为,在刀杆基体61的a面和b面的头端设有三角形和正方形凹槽,在三角形凹槽与正方形凹槽之间开设有螺纹孔道,在螺纹孔道内螺纹连接有定位螺栓63,定位螺栓63包括上部的圆柱轴、中部的凸缘和下部的螺杆段,该圆柱轴与刀片62上的定位孔相互小间隙配合安装,中部的凸缘沉入螺孔孔道的沉孔内,下部的螺纹段与螺纹孔道螺纹连接。
23.本发明安装在车床上的摩擦磨损试验装置的工作方法,包括步骤如下:(1)当摩擦磨损试验开始时:根据试验所需的正压力fn,由p=fn/s求出需要在双轴气缸中加载的气压p,其中s为双轴气缸腔内活塞接触气压面的表面积;(2)在双轴气缸输入稳定的气压p,使得气缸活塞推动l型助推板和轨滑块以及刀杆组件往左边移动,刀杆组件中的刀片与工件接触进行摩擦磨损试验;(3)测力仪在摩擦磨损试验进行时完成对正压力fn的监测以及摩擦力ff的收集;(4)根据求出刀具与工件的摩擦系数μ=fn/ff;(5)当摩擦磨损试验结束时:双轴气缸中的气压减小,气缸活塞往右边移动,带动刀杆组件往右边移动,刀片与工件分离,摩擦磨损试验结束。