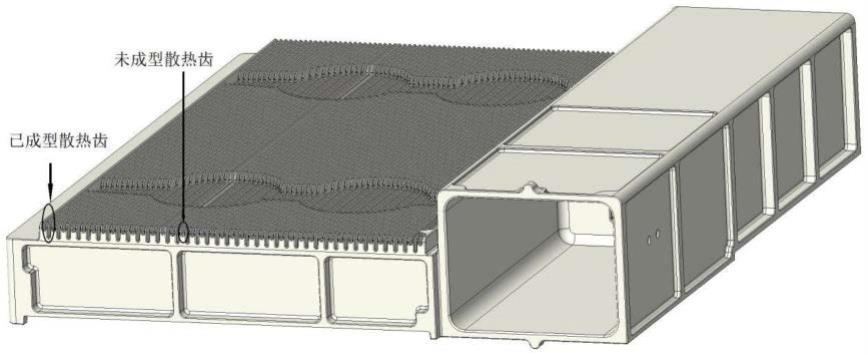
1.本发明属于散热器加工工艺技术领域,具体涉及一种电子设备用高密度散热齿的加工方法。
背景技术:2.在设计单兵背负的电子设备时,为了士兵背负后徒步的目的,对设备总重量进行了限制。电子设备发热量较大,所以在保证电子设备散热器的散热齿总数量的同时,采用了机加工艺制造散热齿的方式,以减小单片齿片的厚度来减轻散热器的重量,进而减轻整个电子设备的总重量。
3.在小批量生产制造散热齿时,机加工艺能勉强满足生产效率和成本的要求。但在大批量生产制造散热齿时,无法满足生产要求。例如,现有技术中将原有的平板叶齿挤型散热片的加工工艺由裁切-木工-碱洗-冲压简化为裁剖-碱洗-连续模冲压,简化加工工艺、提升加工过程中的稳定性、减少人力成本的同时,依然无法适应大批量生产制造,仍然存在效率低下的问题;而在公开的采用半固态压铸成型的散热器的制备方法中,通过将基板和筒体部分开采用半固态压铸成型,再将筒体部采用热压熔接的方式与基板的上表面结合,取代了传统之采用压铸一体成型的方式,有效简化成型工艺,降低成本,但其仍然存在单片散热柱(齿片)的厚度较厚而加大了散热器的总重量。
4.基于上述分析,有必要对目前高密度散热齿的加工方法进行改进,提出一种适用于电子设备用高密度散热齿的加工方法。
技术实现要素:5.本发明提供一种电子设备用高密度散热齿的加工方法,至少可以解决现有技术中存在的部分问题。
6.为解决上述技术问题,根据本发明的一个方面,本发明提供了如下技术方案:
7.一种高密度散热齿的加工方法,包括如下步骤:
8.s1:采用压铸成型的方式成型出散热齿;
9.s2:对压铸成型后的散热齿进行机加工,得到满足电子设备散热条件的散热齿。
10.作为本发明所述的一种高密度散热齿的加工方法的优选方案,其中:所述步骤s1中,具体包括如下步骤:
11.s1.1、预浇注阶段:将压铸机结构压室内用于制造散热齿的液态金属无涡流地引至浇口,压射活塞以恒定速度或加速度运动;
12.s1.2、充模过程:在短时的加速之后,以稳定的速度快速进行,以使浇口内液态金属达到稳定的流动速度;
13.s1.3、增压凝固:通过对容室内液态金属快速建压对模具型腔内的压铸件增密,保持模具型腔内的增压至铸件凝固,成型出散热齿。
14.作为本发明所述的一种高密度散热齿的加工方法的优选方案,其中:所述步骤
s1.3中,快速建压是通过增压器或直接控制压射来完成。
15.作为本发明所述的一种高密度散热齿的加工方法的优选方案,其中:所述步骤s1.3中,增压范围为90~100mpa。
16.作为本发明所述的一种高密度散热齿的加工方法的优选方案,其中:所述步骤s1.3中,铸件凝固后,通过顶出器杆及机械手配合从模具型腔中脱模取出铸件。
17.作为本发明所述的一种高密度散热齿的加工方法的优选方案,其中:所述步骤s2中,机加工后进行清洗干燥步骤。
18.作为本发明所述的一种高密度散热齿的加工方法的优选方案,其中:所述步骤s2中,将压铸好的毛坯用铣床或cnc设备进行机加工,将未成形的齿片进行加工,得到所需工艺参数与精度的散热齿,完成高密度散热齿的加工。
19.作为本发明所述的一种高密度散热齿的加工方法的优选方案,其中:所述方法还包括步骤s3:对机加工后的散热齿进行二次机加工。
20.作为本发明所述的一种高密度散热齿的加工方法的优选方案,其中:所述步骤s3中,二次机加工后进行质检包装步骤。
21.有益效果
22.本发明与现有技术相比具有明显的优点和有益效果,具体而言,由上述技术方案可知:
23.(1)通过先压铸后机加这种压铸、机加相结合的方式使高密度散热齿的制造效率相比于纯机加方式提高了70%以上,相比于纯压铸工艺,减轻了散热齿重量,也提高了散热效率。
24.(2)本技术中的压铸工艺,压铸件的尺寸精度较高,只需经过少量机械加工即可装配使用,有的压铸件可以直接装配使用。其材料利用率约60%~80%,毛坯利用率高达90%。由于高速充型,充型时间短,金属液体凝固迅速,压铸作业循环速度快。在常用制造工艺中,压铸工艺的生产效率最高,适合高密度散热齿的大批量生产。
附图说明
25.为了更清楚地说明本发明实施例或现有技术中的技术方案,下面将对实施例或现有技术描述中所需要使用的附图作简单地介绍,显而易见地,下面描述中的附图仅仅是本发明的一些实施例,对于本领域普通技术人员来讲,在不付出创造性劳动的前提下,还可以根据这些附图示出的结构获得其他的附图。
26.图1为本技术一种高密度散热齿的加工方法流程示意图;
27.图2为本技术一种高密度散热齿的加工方法压铸成型示意图;
28.图3为本技术一种高密度散热齿的加工方法压铸成型平面示意图;
29.图4为本技术一种高密度散热齿的加工方法机加工艺示意图;
30.图5为本技术一种高密度散热齿的加工方法实施示意图一;
31.图6为本技术一种高密度散热齿的加工方法实施示意图二。
32.附图标号说明:
33.s1-压铸成型,s2-机加工艺
34.本发明目的的实现、功能特点及优点将结合实施例,参照附图做进一步说明。
具体实施方式
35.下面通过参考附图描述的实施例是示例性的,旨在用于解释本发明,而不能理解为对本发明的限制。
36.在本发明的描述中,需要理解的是,术语“中心”、“纵向”、“横向”、“长度”、“宽度”、“厚度”、“上”、“下”、“前”、“后”、“左”、“右”、“竖直”、“水平”、“顶”、“底”、“内”、“外”、“顺时针”、“逆时针”等指示的方位或位置关系为基于附图所示的方位或位置关系,仅是为了便于描述本发明和简化描述,而不是指示或暗示所指的装置或元件必须具有特定的方位、以特定的方位构造和操作,因此不能理解为对本发明的限制。
37.实施例1
38.本发明实施例1公开了一种高密度散热齿的加工方法,如图1所示,包括以下步骤:
39.s1:采用压铸成型的方式成型出散热齿;
40.压铸一般分为三个阶段:在第一浇注阶段或预浇注阶段是要将压室内液态金属尽可能无涡流地引至浇口,压射活塞以恒定速度或加速度慢慢地运动;第二浇注阶段,这是实际的充模过程,在短的加速之后,以稳定的速度十分快地进行。以使浇口内液态金属达到稳定的流动速度;第三浇注阶段(增压)通过对容室内液态金属快速建压对模具型腔内的压铸件增密,压力的建立是通过增压器或直接控制压射来完成的,保持模具型腔内的增压至铸件凝固。
41.需要说明的是,整个压铸系统(压室、浇注系统、型腔等)都与大气相通,金属液体使以高压、高速充填,如果不能实现有序、平稳的流动状态,金属液会产生涡流,会把气体卷一同卷入,会使铸件产生气孔、气泡等压铸缺陷可能会使铸件报废,因此要确保液态金属无涡流地引至浇口。
42.根据模具的复杂程度以及产品壁厚等多种因素,同时还要结合比压、温度、速度综合考虑,通过试模(简单磨具通常一次,复杂磨具2~3次)来确定各个压铸参数,并记录作为之后生产的依据。通常模具比压较高时采用低温高压来保证金属液体流动性,比压较低时应提高温度降低金属粘度来保证流动性。
43.压铸工艺决定着散热齿的质量,有必要确保在第一浇注阶段室内液态金属无涡流的运动;在第二浇筑阶段,通过提高浇筑活塞速度缩短冲模时间以减少铸件内外浇筑缺陷,以期达到铸件的壁厚要求。
44.容室为压铸室存放液态金属的地方,增密即使压铸件密度增高防止气泡或腔室未被完全填充的现象发生,通常用高压+保压来避免上述缺陷产生,保压时间也要根据模具的复杂程度等多种因素通过试模来确定,记录参数作为日后生产依据。
45.此外,在铸件增密时从第二至第三浇筑阶段过度时间要最短,直至浇筑活塞停止运动。而对于压射机构本技术并未限定,本领域技术人员可以理解,凡是能够实现的各种不同压射机构,均可应用于压铸工艺中。本着应当减少压铸工艺中的孔隙度、毛刺以及其他压铸缺陷的目的,尽可能的优化浇筑过程以及冲模过程。从工艺上保证散热齿的压铸精度,制造出性能优良的散热器,提高产品的性能。
46.s2:对压铸成型的散热齿进行机加工;
47.将压铸好的毛坯用铣床或cnc等设备进行机加工,将未成形的齿片进行加工,得到所需工艺参数与精度的散热齿,完成高密度散热齿的加工。
48.本次机加工后,可对散热齿进行清洗干燥,如达到质量检验要求,可直接入库备用;如精度达到不到装配要求,对机加工后的散热齿酌情进行二次机加工,二次机加工后重复进行质检包装入库步骤。
49.当然,亦可根据加工精度要求,选择能够完成散热齿机加要求的装夹夹具,装夹夹具以在一个工位上加工产品多个面为宜,减少装夹次数,提高生产效率的同时,降低加工生产的成本。
50.实施例2
51.本发明实施例2公开了一种高密度散热齿的加工方法,如图2-6所示:
52.图2为压铸成型后的毛坯,对未成型部分散热齿进行加工后得到最终产品如图4所示。在图3所示的平面图中,相对于制造出与机加相同厚度的齿片,压铸成型后的散热齿毛坯需要纯机加工艺的余量少了很多,压铸成型后的齿片明显减少了机加时间,单件时间的减少,累积到批量产品的加工,显著提高了生产效率,降低了制造成本。
53.在图5-6中,给出了不同齿厚和齿间距的散热齿加工示意图:
54.图5中:齿厚1.4,齿间距3
55.用压铸工艺制造散热齿。受压铸工艺的限制,散热齿单片齿厚一般为1.2-1.5mm,齿间距一般为2.5-3mm,在大批量生产的情况下压铸工艺能够有效的降低制造成本,提高生产效率。
56.图6中:齿厚0.84,齿间距2
57.在设备发热量大、设备总质量有限制的情况下,通常用机加制造的办法减少单片散热齿的齿厚(可小于1mm),在保证设备散热能力的情况下能有效减少设备的质量。
58.为了降低制造成本,提高生产效率的同时,突破压铸工艺本身的限制能够制造更薄的齿片,设计了一种间隔式厚度的散热齿加工工艺,在压铸制造完成后,对产品用机加工艺二次加工,能够制造出于机加相同厚度的齿片。相对于纯机加工艺,显著的提高了生产效率。
59.尽管上面已经示出和描述了本发明的实施例,可以理解的是,上述实施例是示例性的,不能理解为对本发明的限制,本领域的普通技术人员在不脱离本发明的原理和宗旨的情况下在本发明的范围内可以对上述实施例进行变化、修改、替换和变型。