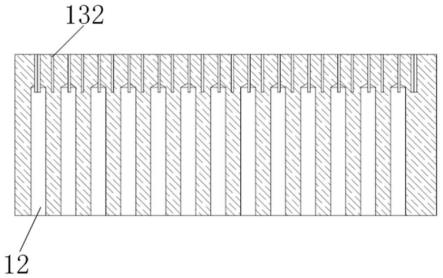
1.本发明涉及一种大小孔蜂窝结构体挤出模具的加工方法,属于蜂窝状陶瓷加工技术领域。
背景技术:2.目前市场使用的蜂窝陶瓷dpf是对称型产品,即储烟孔和过滤出烟孔的容积比是1:1的。其缺点是储烟量小;载碳量少;使用背压高;体积大。针对以上问题推出了非对称蜂窝陶瓷dof,即大小孔蜂窝陶瓷dpf,小孔和大孔的比例是1:1.7左右,大孔储烟,小孔过滤出烟,大大的提高了储烟量和碳载量,降低了使用背压,从而缩小了体积,提高环保的效果。
3.但是现在使用的大小孔蜂窝结构体挤出模具大部分是用金属3d加工完成的,缺点是进料孔和成型槽内壁粗糙度过大,成型槽宽度的精密度较差,更重要的是耐磨性差,使用寿命太短。
4.其中也有一小部分是采用普通电火花机床加工的,所用的是紫铜加工的网格式电极。其缺点是电极加工成本高,电极报废率高,并且电极容易变形,并且普通电火花机床放电功率微调受限,加工出来的模具成型槽,尺寸偏大,均匀性比较差,往往通过镀膜才能使用,这样大大增加了模具制作成本。
技术实现要素:5.本发明所要解决的技术问题是提供一种大小孔蜂窝结构体挤出模具的加工方法,能够提高大小孔蜂窝结构体的制造精度和耐磨性,延长使用寿命,降低成本。
6.本发明解决上述技术问题的技术方案如下:一种大小孔蜂窝结构体挤出模具的加工方法,包括以下步骤:步骤1)选择高碳钢材为原材料进行毛坯加工,加工成适配挤压机的结构体;步骤2),对所述结构体进行热处理加工及进料孔加工;步骤3),对所述结构体进行挤出成型槽加工,采用安装校准在精雕机上的石墨电极进行单行曲线加工工艺成型所述挤出成型槽。
7.本发明的有益效果是:高碳钢材耐磨性强;对结构体进行热处理使其外硬内软,提高抗冲击力性,延长使用寿命,在结构体两面分别加工挤出成型槽和进料孔,形成能够制备大小孔蜂窝结构体的模具;石墨具有宁折不弯的特性,代替容易变形的紫铜电极;使用石墨电极代替紫铜加工电极,提高韧性,防止变形,降低成本。
8.在上述技术方案的基础上,本发明还可以做如下改进。
9.进一步,所述结构体正面加工所述挤出成型槽,反面加工所述进料孔,所述挤出成型槽槽底与所述进料孔连通。
10.进一步,步骤2)中所述热处理加工至所述结构体表皮至表皮以下5mm硬度在hrc55
°
~62
°
,并控制所述结构体硬度波动范围在
±2°
。
11.采用上述进一步方案的有益效果是:提高结构体的硬度和稳定性,延长使用寿命。
12.进一步,所述热处理加工的参数为初始温度为90~100℃,热处理升温速度为150~160℃/h,升高到840~880℃,保温1~2h,再采用油淬工艺淬火。
13.采用上述进一步方案的有益效果是:升温速度为150~160℃/h,经过5~6小时将温度升高到840~880℃,保温1~2h,再采用油淬工艺淬火,结构体内的分子更加稳定,使得结构体稳定性强,不易变形。
14.进一步,所述油淬工艺为淬火温度为840~880℃,保温40~90分钟,油淬到50℃后,保持150~220℃回火4~6h。
15.采用上述进一步方案的有益效果是:硬度能够达到hrc55
±5°
。
16.进一步,所述进料孔加工具体为:使用精密cnc机床,首先采用合金定点钻精准找位,打引孔来保证所述进料孔的位置精准度以及孔道垂直度;然后采用高速钢麻花钻头,以每次0.75mm的进刀量进行加工,孔径误差控制在
±
0.05mm。
17.进一步,所述单行曲线加工具体为:先沿第一方向在所述结构体的正面加工出第一成型槽,使得所述第一成型槽槽底与所述进料孔接通,将石墨电极旋转90
°
,沿垂直第一方向的第二方向加工出第二成型槽,使得第二成型槽槽底与所述进料孔接通,所述第一成型槽与所述第二成型槽形成所述挤出成型槽。
18.采用上述进一步方案的有益效果是:使用石墨代替紫铜加工电极,提高韧性,防止变形。
19.进一步,所述单行曲线加工结束,然后更换一个全新的石墨电极对所述第一成型槽槽底和所述第二成型槽槽底进行清底,直至所述挤出成型槽槽底与所述进料孔交接0.8~1mm,误差为
±
0.05mm,完成模具加工。
20.采用上述进一步方案的有益效果是:使用单行曲线加工代替网格加工,降低电极加工成本,降低电极报废率。
21.进一步,所述高碳钢材的的型号是cr12mov。
22.进一步,所述进料孔为圆孔。
23.采用上述进一步方案的有益效果是:圆孔加工方便,且内表面积大。
附图说明
24.图1为本发明一种大小孔蜂窝结构体挤出模具的加工方法中沿第一方向加工出第一成型槽的结构示意图;图2为本发明一种大小孔蜂窝结构体挤出模具的加工方法中模具正面的结构示意图;图3为本发明一种大小孔蜂窝结构体挤出模具的加工方法中模具反面的结构示意图;图4为图2中沿a-a剖开的的剖视图。
25.附图中,各标号所代表的部件列表如下:1-结构体、12-进料孔、13-挤出成型槽、131-第一成型槽、132-第二成型槽。
具体实施方式
26.以下结合附图对本发明的原理和特征进行描述,所举实例只用于解释本发明,并
非用于限定本发明的范围。
27.本发明的目的是提供一种大小孔蜂窝结构体挤出模具的加工方法,以解决现有技术存在的问题,能够提高大小孔蜂窝结构体的制造精度和耐磨性,延长使用寿命,降低成本。
28.为使本发明的上述目的、特征和优点能够更加明显易懂,下面结合附图和具体实施方式对本发明作进一步详细的说明。
29.本发明提供一种大小孔蜂窝结构体挤出模具的加工方法,本发明一具体实施例中,如图1~4所示,包括以下步骤:步骤1)选择高碳钢材为原材料进行毛坯加工,加工成适配挤压机的结构体1;步骤2),对结构体1进行热处理加工及进料孔12加工;步骤3),对结构体1进行挤出成型槽13加工,采用安装校准在精雕机上的石墨电极进行单行曲线加工工艺成型挤出成型槽13。
30.本发明提供一种大小孔蜂窝结构体挤出模具的加工方法,高碳钢材耐磨性强;对结构体1进行热处理使其外硬内软,提高抗冲击力性,延长使用寿命,在结构体1正面和反面加工进料孔12和挤出成型槽13,形成能够制备大小孔蜂窝结构体1的模具;石墨具有宁折不弯的特性,代替容易变形的紫铜电极;使用石墨电极代替紫铜加工电极,提高韧性,防止变形,降低成本。
31.本发明一具体实施例中,结构体1正面加工挤出成型槽13,反面加工进料孔12,挤出成型槽13槽底与进料孔12连通。
32.本发明一具体实施例中,步骤2)中热处理加工至结构体1表皮至表皮以下5mm硬度在hrc55
°
~62
°
,并控制结构体1硬度波动范围在
±2°
。
33.提高结构体1的硬度和稳定性,延长使用寿命。
34.本发明一具体实施例中,热处理加工的参数为初始温度为90~100℃,热处理升温速度为150~160℃/h,升高到840~880℃,保温1~2h,再采用油淬工艺淬火。
35.热处理加工的参数为初始温度为90~100℃,升温速度为150~160℃/h,经过5~6小时将温度升高到840~880℃,保温1~2h,再采用油淬工艺淬火,结构体1内的分子更加稳定,使得结构体1稳定性强,不易变形。
36.本发明一具体实施例中,油淬工艺为淬火温度为840~880℃,保温40~90分钟,油淬到50℃后,保持150~220℃回火4~6h。
37.硬度能够达到hrc55
±5°
。
38.本发明一具体实施例中,进料孔12加工具体为:使用精密cnc机床,首先采用合金定点钻精准找位,打引孔来保证进料孔12的位置精准度以及孔道垂直度;然后采用高速钢麻花钻头,以每次0.75mm的进刀量进行加工,孔径误差控制在
±
0.05mm。
39.本发明一具体实施例中,单行曲线加工具体为:先沿第一方向在结构体1的正面加工出第一成型槽131,使得第一成型槽131槽底与进料孔12接通,将石墨电极旋转90
°
,沿垂直第一方向的第二方向加工出第二成型槽132,使得第二成型槽132槽底与进料孔12接通,第一成型槽131与第二成型槽132形成挤出成型槽13。
40.因为精雕机加工俯视都有r角,无法采用精雕机上的石墨电极进行网格加工,第一成型槽131和第二成型槽132分开加工可以规避以上问题。
41.本发明一具体实施例中,单行曲线加工结束,然后更换一个全新的石墨电极对第一成型槽131槽底和第二成型槽132槽底进行清底,直至挤出成型槽槽底与进料孔12交接0.8~1mm,误差为
±
0.05mm,完成模具加工。
42.采用上述进一步方案的有益效果是:使用单行曲线加工代替网格加工,降低电极加工成本,降低电极报废率。
43.优选的,选用高精度镜面火花机加工成型槽,精密控制放电功率,加工出成型槽内壁光滑,槽宽一致;高精度镜面火花机可选用三菱sg8或沙迪克aq55l或牧野ednc43。
44.本发明一具体实施例中,高碳钢材的的型号是cr12mov。
45.本发明一具体实施例中,进料孔12为圆孔。
46.圆孔加工方便,且内表面积大。
47.优选的,圆孔的直径为1.5~1.6mm。
48.本发明实施例,过程如下:1、选用型号为cr12mov高碳钢材作为毛坯,采用高碳钢用车床、平面磨床加工出适合自己公司的挤压机适用的结构体1;2、采用热处理工艺,初始温度为100℃,热处理升温速度为150℃/h,升温5小时,达到850℃,保温1.5h,再采用油淬工艺淬火,油淬工艺的淬火温度为850℃,保温75分钟,油淬到50℃后,保持190℃回火5h,加工至结构体1表皮至表皮以下5mm硬度在hrc55
°
~62
°
,并控制结构体1硬度波动范围在
±2°
,以保证结构体1的耐磨性、耐冲击性和稳定性;3、使用精密cnc机床,首先采用合金定点钻精准找位,打引孔来保证进料孔12的位置精准度以及孔道垂直度;然后采用高速钢麻花钻头,以每次0.75mm的进刀量进行加工,孔径误差控制在
±
0.05mm,保证孔道内壁光滑,孔位精准,孔道垂直;4、挤出成型槽13加工,这道工序分两个部分:4.1电极加工,采用石墨作为电极,采用cnc精雕机单向曲线加工电极成型公位,以及安装位和校准位。
49.4.2电火花加工,采用三菱sg8高精密镜面电火花加工机床加工,用其放电功率可微调的特性以及电极损耗小的特性,先沿第一方向在结构体1的正面加工出第一成型槽131,使得第一成型槽131槽底与进料孔12接通,将石墨电极旋转90
°
,沿垂直第一方向的第二方向加工出第二成型槽132,使得第二成型槽132槽底与进料孔12接通,第一成型槽131与第二成型槽132形成挤出成型槽13;然后更换一个全新的石墨电极对第一成型槽131槽底和第二成型槽132槽底进行清底,直至挤出成型槽与进料孔12交接0.8~1mm,误差为
±
0.05mm,完成模具加工。
50.以上所述仅为本发明的较佳实施例,并不用以限制本发明,凡在本发明的精神和原则之内,所作的任何修改、等同替换、改进等,均应包含在本发明的保护范围之内。