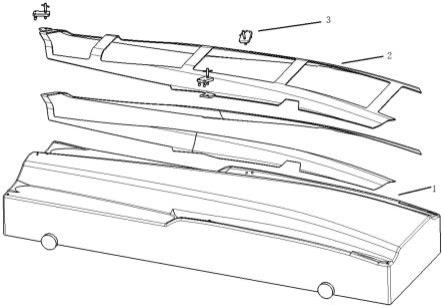
1.本发明涉及金属材料钣金加工技术领域,尤其涉及一种大型叉形蒙皮轮廓制备方法。
背景技术:2.钛合金材料因具备比强度高、耐高温、抗疲劳、耐腐蚀等优点,被广泛应用于航空制造业,尤其是后机身蒙皮及内部结构件。随着对飞机性能要求的提高,零件整体化、大型化、高精度化,已成为新一代飞机设计的趋势。钛合金蒙皮零件,一般采用净尺寸检验模加工零件外缘,而对于大型且兼具内外形的零件(如“回”型零件、叉形零件),内轮廓加工较为困难。一般需按照图纸或零件三维数模粗略加工零件内轮廓,然后由钣金钳工按照检验模将零件内轮廓打磨、修整至理论位置,加工周期较长,且精度不高。而且在加工时需将检验模架起,操作者在下方加工,存在较大的安全隐患,为生产所禁止。如何解决大尺寸叉形蒙皮零件轮廓的加工效率问题,成为了该类零件外形加工的一大难点,所以需要探索一种高效、便捷、安全的大型叉形蒙皮轮廓制备方法。
技术实现要素:3.为了解决上述难题,降低大型钛合金叉形蒙皮轮廓制备难度,提升加工效率,本发明提供了一种大型叉形蒙皮轮廓制备方法,针对原净尺寸检验模确定零件内轮廓困难的问题,通过调整检验模结构,并增加部分附件的方式,大大简化了零件轮廓加工过程,解决了前述问题。
4.本发明的技术方案:一种大型叉形蒙皮轮廓制备方法,包括步骤如下;
5.步骤1、模具需求分析;
6.零件为细长叉形蒙皮,零件外形为一整张板料直接液压成形,成形后存在加工余量;检验模边缘与零件型面夹角不大于90
°
;
7.步骤2、轮廓加工方案设计
8.检验模包括盖板1和胎体2;零件一侧型面上随形一叉形的盖板1,其沿厚度方向尺寸减小,按零件一侧型面法向增厚10mm,盖板1的两叉中间增加若干连接筋条增加强度;零件另一侧型面上设置胎体2,用于支撑零件和盖板1;盖板1和胎体2采用三孔定位;
9.步骤3、检验模结构设计
10.胎体1型面按照零件内表面随形,内外侧余量按照零件型面曲率延伸进行补偿,胎体1型面上划出零件轮廓线,整体采用数控加工,加工精度为-0.1mm-0.1mm;盖板2按照零件外表面设计,内其外轮廓与零件边缘平齐加工精度为-0.1mm-0.1mm;钻模板3用于钻制定位孔,孔位精度为-0.1mm-0.1mm;钻模板3与胎体1之间采用插销或定位销定位;胎体1、盖板2与零件定位孔对应处开有定位孔,用于三者定位。
11.所述胎体1和钻模板3均为数控加工。所述胎体1材料为树脂或金属材质。所述胎体1上设置吊环或吊棒,用于模具搬运。所述盖板2为玻璃钢材质。
12.本发明的有益效果:本发明将检验模外形和轮廓加工及检验功能分解,设计了专用盖板来加工和检验零件轮廓,与传统的净尺寸检验模相比,无需通过型面的二次定位来分别加工内外轮廓,轮廓一次加工精度和加工效率,都有了较大程度的提升。此外,轮廓盖板的使用,无需将检验模架高来加工内轮廓,加工安全性也得到了提升。
附图说明
13.图1为典型叉形蒙皮零件结构示意图;
14.图2为叉形蒙皮零件与检验模的安装示意图。
15.图中:1-胎体;2-盖板;3-钻模板。
具体实施方式
16.根据本发明的大型叉形蒙皮轮廓制备方法进行具体一叉形零件的轮廓制备。
17.1、模具需求分析;
18.某典型零件外形结构如图1所示,零件为细长叉形蒙皮,外廓尺寸约为2000
×
500mm,自身刚性较差,且受飞机气动外形影响,零件型面较为复杂。零件外形为一整张板料直接液压成形而成,成形后存在较大加工余量需要去除。
19.因切割夹具限制,零件余量加工时需在凸表面划出零件内外侧边缘线,因零件尺寸较大,出于方便操作和安全角度考虑,应避免在检验模背面进行操作。同时为了保证划线精度,检验模边缘与零件型面夹角应不大于90
°
。
20.2、轮廓加工方案设计
21.零件轮廓一般按照净尺寸检验模加工,按前述检验模要求,为保证边缘与零件型面夹角小于90度,检验模边缘会出现较大倾角,影响结构稳定性,并极大增加加工难度。且由于零件内侧加工余量尺寸较大,会遮挡检验模内轮廓,无法在检验模正面进行加工。
22.为满足前述要求,可将净尺寸检验模厚度方向尺寸大幅减小,按零件型面法向增厚10mm制作一个随形盖板1,并在盖板1的两叉中间增加若干连接筋条增加强度,如此便可将盖板1平铺在零件上划内外轮廓线,十分便捷。但是因零件及盖板尺寸较大且厚度较薄,自身刚度难以维持零件外形,需在另一侧型面增加一个较大的胎体2,用于支撑零件和盖板1,盖板1和胎体采用三孔定位。
23.3、检验模结构设计
24.按照前述加工思路,零件检验模可分为两个主要部分:胎体2和盖板1,然后根据实际需要增加必要的附件,即可完成零件检验模设计,现以典型零件检验模,如图2所示为例进行说明,其结构主要包括:
25.1)胎体1
26.胎体1型面按照零件内表面设计,内外侧余量按照零件型面曲率延伸进行补偿,并在型面上划出零件轮廓线,整体采用数控加工,加工精度为-0.1mm-0.1mm。胎体1材料可选择树脂或金属材质,其强度和刚度满足使用需求即可。若胎体1尺寸较大,可在适当位置设置吊环或吊棒方便模具搬运。胎体1应在定位孔等相应位置开孔,用于钻孔躲避及定位销定位。胎体1用于支撑零件和盖板2,零件型面定位及贴胎检查,并辅助检查零件轮廓。
27.2)盖板2
28.盖板2按照零件外表面设计,内外轮廓应与零件边缘平齐,厚度满足强度最低需求即可,盖板2可在适当位置增加连筋以增加整体强度,加工精度为-0.1mm-0.1mm。盖板2按照零件设计的定位孔位置设置定位耳片及定位孔,用于与盖板2和零件、盖板2和胎体1间定位。盖板2主要用于划零件内外轮廓线,并检查零件轮廓。
29.3)钻模板3
30.因零件和盖板2定位需求,需在检验模上增加钻模板3用于钻制定位孔。钻模板3采用钢板数控加工而成,孔位精度为-0.1mm-0.1mm,孔镶钻套以避免孔位磨损。钻模板3应设计为方便拆卸的结构,其与胎体1之间可采用插销或定位销定位,因零件成形后周边有较大的加工余量,定位销不可设计在胎体1上或应留出一定的余量空间,以避免与零件发生干涉。
31.现以某典型零件为例,详细说明制备方法。一种大型叉形蒙皮轮廓制备方法,该方法可实现类似大型零件的高效、便捷、安全的外形轮廓加工。胎体1为树脂材质,采用吊棒进行起吊搬运;盖板2为玻璃钢材质。
32.步骤1)、零件毛料准备
33.零件按下料尺寸下料,并经表面处理,去除表面污物及字迹;
34.步骤2)、热成形准备
35.将热成形模放入热成形机中装夹,并加热至成形温度,该典型零件成形温度为700℃左右;
36.步骤3)、喷涂润滑剂
37.在毛料上下表面喷涂耐高温成形润滑剂;
38.步骤4)、热成形
39.将毛料放入热成形模,保温10分钟后,开始热压成形,成形压力约70吨,热成形模上下模合模后,保温保压20分钟,然后将零件取出。
40.步骤5)、检验模准备
41.吊装检验模的吊棒,将该检验模安放到一个开敞的位置,并检查相关配件是否齐全、完好;
42.步骤6)、粗切外形
43.按照检验模粗切零件外形,去除零件内外大部分加工余量,避免零件坯料与检验模补加型面、钻模板3等机构干涉。
44.步骤7)、钻定位孔
45.将零件坯料按型面在检验模胎体1上定位,然后按钻模板3钻制3个直径为5.2mm的定位孔。
46.步骤8)、划零件轮廓线
47.将零件坯料放在胎体1上,然后将盖板2覆盖在零件表面,三者按定位孔插定位销定位。然后按盖板2轮廓,在零件坯料上画出零件轮廓线。
48.步骤9)、制外形
49.将零件坯料取下,按定位孔在切割夹具上定位并夹紧,按划线加工出零件外形,加工完成后取下零件,并按划线切除三个定位耳片。
50.步骤10)、检查零件
51.10.1)将加工完的零件放在胎体1上,按型面及零件轮廓线定位,检查零件与胎体1型面贴合间隙。
52.10.2)将盖板2覆在零件上,并按定位孔与胎体1定位,然后按盖板2边缘检查零件轮廓。
53.步骤11)、表面处理
54.零件检验合格后,即可送表面处理车间,进行后续酸洗、喷漆等表面处理工序。