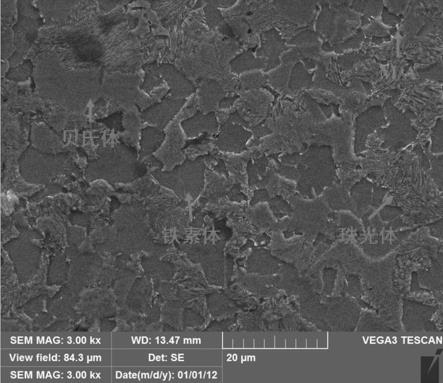
一种700mpa级高强韧热轧锚杆钢筋及其制备工艺
技术领域
1.本发明属于冶金材料制备技术领域,涉及锚杆钢筋,具体为一种700mpa级高强韧热轧锚杆钢筋及其制备工艺。
背景技术:2.我国煤炭的80%是由井工矿生产,且开采深度正以8-12m/a的速度增加,很多煤矿将进入到1000-1500m的开采深度。而随着矿井采掘深度的增加,矿压力变大,巷道支护的安全稳固问题越来越突出。
3.煤巷锚杆支护技术近年来发展极为迅速,高强度、高预应力、高刚度和高可靠性设计成为一种发展趋势。目前大量使用的mg335、mg400、mg500等级别的热轧锚杆钢已经难以适应高强度、高预应力支护技术发展的要求。
4.虽然采用传统的热轧生产工艺,通过增加钢中的碳或合金含量,可以提高锚杆钢的强度,但是无法达到兼顾超高强度与延伸率≥15%的要求。而采用离线调质热处理的方式虽然可以实现高强度与高塑韧性的结合,但其生产工序多,生产效率低、耗能高,造成了锚杆制造成本的大幅上升。
5.cn 108913990b公开了一种600mpa级高塑性锚杆钢筋及生产方法,终轧后采用穿水冷却,上冷床抛钢温度为850-900℃,堆冷≥12h后,加热至100-500℃保温5-20h进行热处理。所述锚杆钢的屈服强度rel 665-690mpa,抗拉强度rm 820-845mpa,断后伸长率a 25-26%。上述方法制备的锚杆钢筋虽然具有较好的塑性,满足了延伸率≥15%的要求,但是屈服强度较低,不高于690mpa;此外,热轧后钢材还需要进行堆冷12h并进行人工时效热处理,降低生产效率,增加能源消耗。
6.cn 102352462a公开了一种高强高冲击韧性的锚杆钢筋及其制备方法,成品组织为回火索氏体和少量铁素体。热轧钢筋通过淬火、回火热处理后,其屈服强度等级达到600-785mpa,断后伸长率a不小于15.0%。该制备方法的不足之处是相比热轧的同等级锚杆钢产品,增加了调质热处理工序,生产工艺复杂性大,增加能源消耗,生产成本大幅提高,生产效率低,不具备成本优势和大规模推广性。
技术实现要素:7.本发明旨在解决现有锚杆钢筋不能兼顾屈服强度、抗拉强度、延伸率等特性,不满足高预应力发展的需求且生产工艺效率低、耗能高、成本高的技术问题,提供了一种700mpa级高强韧热轧锚杆钢筋及其制备工艺。
8.本发明解决其技术问题采用的技术手段是:一种700mpa级高强韧热轧锚杆钢筋,所述锚杆钢筋的化学元素组成及其质量百分含量为:c:0.28~0.34%,si:0.70~1.20%,mn:1.60~1.90%,v:0.12~0.40%、n:0.013~0.040%,cr:0.15~0.55%,nb:0.01~0.03%,其中v+nb+cr+n≤0.80%,残余元素p≤0.035%、s≤0.025%,其余为fe和不可避免的杂质。
9.本发明要求保护的锚杆钢筋的屈服强度rel≥700mpa,抗拉强度rm≥900mpa,延伸
率a≥17%。
10.锚杆钢筋中的c是提高钢材强度最有效和最廉价的元素,c能对铁素体组织起固溶强化作用,也是珠光体、贝氏体的组成元素,但随着其含量的上升,会导致塑性和韧性下降。
11.锚杆钢筋中的si是一种廉价的强化元素,可以显著提高钢的屈服强度,si促进铁素体相变,适当的si含量还能促进形成薄膜状的残余奥氏体,改善钢材的塑韧性。
12.锚杆钢筋中的mn主要是固溶于铁素体中提高钢的强度,含有一定量的锰可以消除或减弱因硫引起的脆性,从而改善钢的加工性能,但锰含量过高时会有晶粒粗化的倾向。
13.锚杆钢筋中的n与v、nb、c结合形成v(cn)、nb(cn),有析出强化的作用,并且在奥氏体的晶界和晶内析出,抵制奥氏体晶粒长大,为铁素体形核提供质点,细化铁素体晶粒,起细晶强化作用。
14.锚杆钢筋中的v是微合金化钢最常用也是最有效的强化元素之一,v的主要作用是通过在铁素体中形成vn、v(cn)沉淀析出,强化铁素体相,从而提高钢材的强度。另外,应变诱导析出的v(cn),为铁素体形核提供质点,增大铁素体的形核率,细化铁素体晶粒。
15.锚杆钢筋中的nb在钢坯热轧前加热时可以阻止奥氏体晶粒的长大,提高粗化温度至1250℃。在热变形过程中,nb的固溶拖曳作用及应变诱导析出均具有强烈的阻碍奥氏体再结晶发生的作用,阻止再结晶后的晶粒长大,使奥氏体晶粒细化。扩大奥氏体未再结晶区,增加未再结晶区的变形量和变形道次,使相变后铁素体晶粒细化。nb能产生显著的晶粒细化和中等的沉淀强化作用。nb的碳化物、氮化物既可在奥氏体较高温度区域内溶解,也可在低温下重新析出,可起到析出强化的效果。nb的c、n化合物有着较高的析出温度,对晶界起到强烈的钉扎作用,能够细化晶粒,起到细晶强化的作用,而且能提高塑性,增加韧性。nb有利于钢中诱导相变的发生,nb提高了诱导相变临界温度,降低了诱导相变临界变形量,并且对诱导相变细晶铁素体的长大有抑制作用,在一定程度上拓宽了利用临界轧制工艺获得细晶组织的控轧控冷工艺窗口。
16.锚杆钢筋中的cr能显著提高钢的强度、硬度和耐腐蚀性,但通常会降低塑性和韧性,在轧后控制冷却条件下,钢中加入适量cr,可以细化珠光体的层片间距,提升钢的强韧性。
17.锚杆钢筋中的s/p为有害元素,损害钢材塑性,但如果彻底去除s/p或要求过低含量会导致大量增加成本,最终经实践,s/p质量分数≤0 .030%时,能够使成本和产品性能达到较可观的平衡状态。
18.本发明还提供了一种700mpa级高强韧热轧锚杆钢筋的制备工艺,包括以下步骤:第一步、按名义成分冶炼钢液,钢液的化学组成及其质量百分比为:c:0.28~0.34%,si:0.70~1.20%,mn:1.60~1.90%,v:0.12~0.40%、n:0.013~0.040%,cr:0.15~0.55%,nb:0.01~0.03%,其中v+nb+cr+n≤0.80%,残余元素p≤0.035%、s≤0.025%,其余为fe和不可避免的杂质;第二步、lf精炼;第三步、连铸钢坯;第四步、轧钢:第五步、在线组织及析出物调控:轧钢完成后先将钢筋穿水冷却至750~870℃,然后再进入保温装置冷却至450~600℃,最后钢筋出保温装置后上冷床自然冷却。
19.上述第五步中,钢筋精轧结束后,穿水快速冷却至750-870℃,是为了抵制晶粒长大, 让奥氏体保留变形过程中形成的位错和亚组织,为奥氏体
→
铁素体相变及v(cn)、nb(cn)析出提供形核场所,提高相变及析出的形核率,获得更为细小的铁素体晶粒和更多的碳氮化物析出。在500~870℃的温度范围内保温、缓慢冷却,nb、v能够从过饱和固溶体中形成尺寸小于15nm的极细且与铁素体部分相容碳氮化物。这些析出物阻碍位错的移动从而起到析出强化的作用,大大地提高了钢的屈服极限。在线热处理,可以促进铁素体形核、抑制晶粒长大,使珠光体的层片间距变细,调控奥氏体分解后所得复相组织的构成,在提高强度的同时不降低塑韧性。通过采用不同的钢材进出保温缓冷装置温度、逗留时间组合,可以调控铁素体、珠光体和贝氏体的相比例及v(cn)、nb(cn)析出物的数量和尺寸,从而获得期望的力学性能。
20.优选的,第五步中,穿水冷却的速度为150~230℃/s。
21.优选的,第五步中,保温装置的冷却速度为0.5~5℃/s。
22.优选的,第四步中轧钢的步骤为:加热钢坯后依次进行粗轧、中轧以及控温精轧;其中钢坯加热时间为1.5~2h,在1100~1200℃温度段保持60-90min;入粗轧的开轧温度为1000~1090℃,精轧前轧件穿水冷却,控制其精轧入口温度为700~950℃。
23.轧钢工序中,钢坯在加热炉加热时间1.5-2h,在1100-1200℃温度段时间60-90min;这是为了保证钢坯中的碳/氮化物有足够的温度和时间,使其得到充分溶解和均匀分布,改善微观偏析,为组织均匀提供有利条件。
24.轧钢工序中,控温精轧时轧件穿水冷却,精轧入口的温度控制在700-850℃,这是通过对变形速率、变形量及变形温度进行控制,让钢在奥氏体非再结晶区/两相区进行变形,形成应变诱发铁素体,增加塑性高的铁素体相占比,对细化晶粒有明显的作用。采用常规轧制工艺,钢在1000℃左右进行精轧,轧后自然冷却,铁素体晶粒最好的情况为7-8级,晶粒直径>20
µ
m。而采用本发明的控温轧制工艺,铁素体晶粒可以达到12级,其直径可为5
µ
m,通过晶粒细化,可以使钢材的强度和塑韧性能同时得到提升。
25.在700-950℃进行控温精轧,奥氏体过冷以及获得较大累积变形量,在形变诱导铁素体相变过程中获得细小铁素体,在相变过程中,由于变形,奥氏体晶粒内形成位错胞,其分布及尺寸同超细晶铁素体基本上一致。也就是说,在相变过程中,铁素体不仅仅在奥氏体晶界上形核,晶内位错胞壁也可以成为形核位置,这也使得新相的形核位置增加,晶粒得以超细化。超细铁素体由于相邻晶粒之间大多是以大角晶界隔开,所以能在轧后稳定存在。在高温下,晶粒之间会相互吞并,而超细晶铁素体之间大位向差的存在阻碍了这种吞并。在dift过程中,铁素体中的碳浓度过饱和,这是因为在相变中,碳来不及从铁素体向奥氏体扩散,此时,逆相变发生,使得组织得到超细化。综上所述,此种相变需要很大的剪切应变,铁素体同时在奥氏体晶界和晶内形核,生成的铁素体晶粒位向差较大。形核位置的增多和铁素体晶粒间碰撞阻碍长大共同造成了晶粒的超细化。同时,还发生v(cn)、nb(cn)的应变诱导析出,这些析出物促进了晶粒的细化。
26.在线组织及析出物调控,钢筋精轧结束后,穿水快速冷却至750-870℃,让奥氏体保留变形过程中形成的位错和亚组织,为奥氏体
→
铁素体相变及v(cn)、nb(cn)析出提供形核场所,提高相变及析出的形核率,获得更为细小的铁素体晶粒和更多的碳氮化物析出, 还能使珠光体的层片间距变细,调控奥氏体分解后所得复相组织的构成,在提高强度的同
时不降低塑韧性。在500~870℃的温度范围内保温、缓慢冷却,nb、v能够从过饱和固溶体中形成尺寸小于15nm的极细且与铁素体部分相容的纳米级碳氮化物。这些纳米级碳氮化物可作为晶内铁素的形核质点,使铁素体的晶粒更为细小这些析出物阻碍位错的移动从而起到析出强化的作用,大大地提高了钢的屈服极限。通过采用不同的钢材进出保温缓冷装置温度、逗留时间组合,可以调控铁素体、珠光体和贝氏体的相比例及v(cn)、nb(cn)析出物的数量和尺寸,从而获得期望的力学性能。
27.常规轧制中,加入的v、nb只是起到沉淀强化的作用,虽然使钢的强度上升,但不能提升塑韧性。在控温精轧+在线热处理工艺中,可以使形成的nb/v(cn)纳米级析出,不但析出物更多,而且更加细小弥散,不仅强化作用更大,同时还能作为铁素体的形核点,促进晶粒细化,使钢的强度升高,塑韧性能同时提高。
28.优选的,第四步中轧钢的精轧出口速度为11-15m/s。
29.优选的,第二步的lf精炼中,包底吹氮时间为10~20min,氮气流量200~400l/min,氮气压力0.8~2mpa。lf精炼工序中,包底吹氮,降低生产成本,氮含量控制稳定。
30.优选的,第四步中,钢胚加热使用的加热炉为步进梁式加热炉。
31.本发明的有益效果是:1、本发明在炼钢过程控制成分、控制坯料加热温度、控温精轧及在线热处理,形成铁素体+珠光体+贝氏体复相组织;2、本发明锚杆钢筋屈服强度rel≥700mpa,抗拉强度rm≥900mpa,断后伸长率a≥17%;4、本发明工艺简单,产品具有强度和塑性配合良好的特点;5、在同样的支护安全性下,采用本发明高强韧热轧锚杆钢筋可以减少巷道支护钢材使用量,相对于目前大量的mg335,支护用钢量可以节省50%,相对于mg500可以节省28%;6、采用本发明的锚杆钢筋,可以在节省矿用锚杆使用量的情况下提高安全性,减少劳动强度,助力矿井采煤的高效高产;7、与同等强度热处理锚杆相比,本发明高强韧热轧锚杆钢筋生产工序少、流程短,生产效率高,能源消耗少,对环境更为友好。
附图说明
32.为了更清楚地说明本发明具体实施方式或现有技术中的技术方案,下面将对具体实施方式或现有技术描述中所需要使用的附图作简单地介绍,显而易见地,下面描述中的附图是本发明的一些实施方式,对于本领域普通技术人员来讲,在不付出创造性劳动的前提下,还可以根据这些附图获得其他的附图。
33.图1为本发明实施例1制备高强韧热轧锚杆钢筋的金相组织图。
34.图2为本发明实施例1制备高强韧热轧锚杆钢筋的碳氮化物纳米级析出示意图。
具体实施方式
35.下面将结合附图对本发明的技术方案进行清楚、完整地描述,显然,所描述的实施例是本发明一部分实施例,而不是全部的实施例。基于本发明中的实施例,本领域普通技术人员在没有做出创造性劳动前提下所获得的所有其他实施例,都属于本发明保护的范围。
36.实施例1:一种700mpa级高强韧热轧锚杆钢筋的制备工艺,其包括以下步骤:第一步、按名义成分冶炼钢液,钢液的化学组成及其质量百分比为:c:0.28%,si:0.72%,mn:1.64%,v:0.0.387%、n:0.0389%,cr:0.15%,nb:0.027%,残余元素p:0.015%、s:0.008%,其余为fe和不可避免的杂质;
第二步、lf精炼:钢包底吹氮,包底吹氮时间为20min,氮气流量200l/min,氮气压力0.8mpa;第三步、连铸钢坯;第四步、轧钢:使用步进梁式加热炉对连铸钢坯进行加热,加热钢坯后依次进行粗轧、中轧以及控温精轧;其中钢坯加热时间为2h,在1200℃温度段保持60min;入粗轧的开轧温度为1090℃,精轧前轧件穿水冷却,控制其精轧入口温度为760℃,轧钢的精轧出口速度为15m/s;第五步、在线组织及析出物调控:轧钢完成后先将钢筋穿水冷却至870℃,穿水冷却的速度为230℃/s;然后再进入保温装置,保温装置的冷却速度为2.5℃/s,降温2.8min,上冷床前冷却至450℃,最后钢筋出保温装置上冷床自然冷却,制备得到φ18热轧锚杆钢筋。
37.实施例1制备得到的φ18热轧锚杆钢筋的力学性能检测结果见表1。
38.实施例2:一种700mpa级高强韧热轧锚杆钢筋的制备工艺,其包括以下步骤:第一步、按名义成分冶炼钢液,钢液的化学组成及其质量百分比为:c:0.3%,si:0.87%,mn:1.64%,v:0.0.167%、n:0.0239%,cr:0.28%,nb:0.033%,残余元素p:0.017%、s:0.01%,其余为fe和不可避免的杂质;第二步、lf精炼:钢包底吹氮,包底吹氮时间为12min,氮气流量330l/min,氮气压力0.9mpa;第三步、连铸钢坯;第四步、轧钢:使用步进梁式加热炉对连铸钢坯进行加热,加热钢坯后依次进行粗轧、中轧以及控温精轧;其中钢坯加热时间为1.8h,在1130℃温度段保持80min;入粗轧的开轧温度为1050℃,精轧前轧件穿水冷却,控制其精轧入口温度为790℃,轧钢的精轧出口速度为14m/s;第五步、在线组织及析出物调控:轧钢完成后先将钢筋穿水冷却至855℃,穿水冷却的速度为195℃/s;然后再进入保温装置,保温装置的冷却速度为1.1℃/s,降温4.5min,上冷床前冷却至558℃,最后钢筋出保温装置上冷床自然冷却,制备得到φ20热轧锚杆钢筋。
39.图1为实施例1钢筋的金相组织sem照片。图1显示金相组织为铁素体+珠光体+贝氏体。
40.图2为实施例1钢筋的tem照片。图2中的深色点状物是纳米级碳氧化物v(c,n)、nb(c,n)和cr(c,n)析出物。
41.实施例2制备得到的φ20热轧锚杆钢筋的力学性能检测结果见表1。
42.实施例3:一种700mpa级高强韧热轧锚杆钢筋的制备工艺,其包括以下步骤:第一步、按名义成分冶炼钢液,钢液的化学组成及其质量百分比为:c:0.34%,si:1.16%,mn:1.89%,v:0.127%、n:0.0186%,cr:0.51%,nb:0.0132%,残余元素p:0.035%、s:0.025%,其余为fe和不可避免的杂质;第二步、lf精炼:钢包底吹氮,包底吹氮时间为10min,氮气流量280l/min,氮气压力2mpa;第三步、连铸钢坯;
第四步、轧钢:使用步进梁式加热炉对连铸钢坯进行加热,加热钢坯后依次进行粗轧、中轧以及控温精轧;其中钢坯加热时间为1.5h,在1100℃温度段保持90min;入粗轧的开轧温度为1000℃,精轧前轧件穿水冷却,控制其精轧入口温度为850℃,轧钢的精轧出口速度为12m/s;第五步、在线组织及析出物调控:轧钢完成后先将钢筋穿水冷却至754℃,穿水冷却的速度为155℃/s;然后再进入保温装置,保温装置的冷却速度为0.5℃/s,降温5.2min,上冷床前冷却至598℃,最后钢筋出保温装置上冷床自然冷却,制备得到φ22热轧锚杆钢筋。
43.实施例3制备得到的φ22热轧锚杆钢筋的力学性能检测结果见表1。
44.实施例3:一种700mpa级高强韧热轧锚杆钢筋的制备工艺,其包括以下步骤:第一步、按名义成分冶炼钢液,钢液的化学组成及其质量百分比为:c:0.34%,si:1.16%,mn:1.89%,v:0.127%、n:0.0186%,cr:0.51%,nb:0.0132%,残余元素p:0.035%、s:0.025%,其余为fe和不可避免的杂质;第二步、lf精炼:钢包底吹氮,包底吹氮时间为10min,氮气流量280l/min,氮气压力2mpa;第三步、连铸钢坯;第四步、轧钢:使用步进梁式加热炉对连铸钢坯进行加热,加热钢坯后依次进行粗轧、中轧以及控温精轧;其中钢坯加热时间为1.5h,在1100℃温度段保持90min;入粗轧的开轧温度为1000℃,精轧前轧件穿水冷却,控制其精轧入口温度为850℃,轧钢的精轧出口速度为12m/s;第五步、在线组织及析出物调控:轧钢完成后先将钢筋穿水冷却至754℃,穿水冷却的速度为155℃/s;然后再进入保温装置,保温装置的冷却速度为0.5℃/s,降温5.2min,上冷床前冷却至598℃,最后钢筋出保温装置上冷床自然冷却,制备得到φ22热轧锚杆钢筋。
45.实施例3制备得到的φ22热轧锚杆钢筋的力学性能检测结果见表1。
46.对比例1:制备φ20热轧锚杆钢筋,包括以下步骤第一步、按名义成分冶炼钢液,钢液的化学组成及其质量百分比为:c:0.3%,si:0.87%,mn:1.64%,v:0.0.167%、n:0.0239%,cr:0.28%,nb:0.033%,残余元素p:0.017%、s:0.01%,其余为fe和不可避免的杂质;第二步、lf精炼:钢包底吹氮,包底吹氮时间为12min,氮气流量330l/min,氮气压力0.9mpa;第三步、连铸钢坯;第四步、采用常规轧制,不控温精轧,也不在线热处理:将连铸坯在步进梁式热炉中加热2h,加热炉均热段温度为1100℃;在轧制工序中,粗轧的开轧温度为1110℃,精轧出口温度1050℃,同时控制轧件的精轧出口速度为13m/s;第五步、精轧前后不进行在线热处理,钢筋上冷床前温度1045℃,在冷床自然冷却;制备得到φ20热轧锚杆钢筋。
47.对照例1制备得到的φ20热轧锚杆钢筋的力学性能检测结果见表1。
48.对照例2:采用mg600成份的钢坯制备φ20热轧锚杆钢筋,步骤如下
第一步、mg600成份的钢坯的化学组成及其质量百分比为:c:0.29%,si:0.80%,mn:1.60%,v:0.0.120%、n、cr、 nb的分量均低于本发明对应化学组份的范围下限,残余元素p:0.020%、s:0.018%,其余为fe和不可避免的杂质;第二步、lf精炼:钢包底吹氮,包底吹氮时间为12min,氮气流量330l/min,氮气压力0.9mpa;第三步、连铸钢坯;第四步、轧钢:使用步进梁式加热炉对连铸钢坯进行加热,加热钢坯后依次进行粗轧、中轧以及控温精轧;其中钢坯加热时间为2h,在1130℃温度段保持80min;入粗轧的开轧温度为1052℃,精轧前轧件穿水冷却,控制其精轧入口温度为793℃,轧钢的精轧出口速度为14m/s;第五步、在线组织及析出物调控:轧钢完成后先将钢筋穿水冷却至855℃,穿水冷却的速度为195℃/s;然后再进入保温装置,保温装置的冷却速度为1.1℃/s,降温4.5min,上冷床前冷却至558℃,最后钢筋出保温装置上冷床自然冷却,制备得到φ20热轧锚杆钢筋。
49.对比例2制备得到的φ20热轧锚杆钢筋的力学性能检测结果见表1。
50.本发明700mpa级高塑性锚杆钢筋产品标准参考yb/t4364;产品检测方法参考gb/t228 .1。
51.实施例2与对比例1比较,表明即使符合本发明所述的同一化学成份,同样的轧制规格,若不采用本发明所述的轧钢工艺和在线热处理,延伸率达不到本发明所述锚杆钢的17%以上的水平。
52.实施例2与对比例2比较,可以发现,采用本发明所述的相同轧钢及在线热处理工艺,若不采用本发明所述的化学成份,nb、cr和n含量低于本发明成份范围下限,其他元素符合本发明规定的成份要求,也达不到本发明所述锚杆钢的力学性能。同时也表明,增加nb、cr和n含量对实现本发明锚杆钢力学性能具有关键作用。
53.表1 实施例与对照例力学性能。
54.最后应说明的是:以上各实施例仅用以说明本发明的技术方案,而非对其限制;尽管参照前述各实施例对本发明进行了详细的说明,本领域的普通技术人员应当理解:其依然可以对前述各实施例所记载的技术方案进行修改,或者对其中部分或者全部技术特征进行等同替换;而这些修改或者替换,并不使相应技术方案的本质脱离本发明各实施例技术方案的范围。