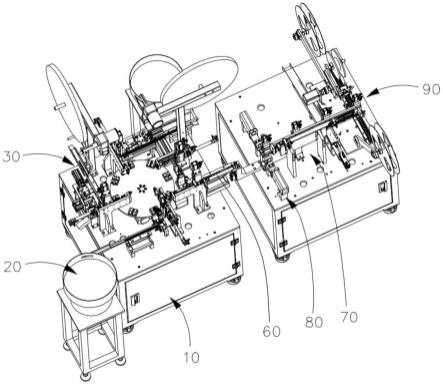
1.本发明涉及电池座生产技术领域,特别是涉及一种电池座生产线。
背景技术:2.纽扣电池也叫扣式电池,是指外形尺寸像一颗小纽扣的电池,纽扣电池安装于电池座的内部搭配使用。电池座生产制造时需要将正极弹片、负极弹片安装于电池座主体内,然后再盖上胶盖,才算完成整个电池座的组装工作。
3.目前的组装方式都是直线式组装设备,这种直线式组装设备的长度较大,占用空间也较大,需要配合很多工序将上述的零件逐按工序逐一进行组装,生产麻烦,生产成本居高不下,大大影响了电池座的生产组装效率。加上电池座组装后包装时要人工检测、放入载带、封膜等工艺,传统技术是利用肉眼对每一个产品进行组装质量检测后放入载带,然后再自动包装。然而包装大批数量时肉眼检测容易出错,效率较低,无法实现全自动化,已经不能满足电池座工业生产的需求。
技术实现要素:4.基于此,本发明提供一种电池座生产线,结构简单,设计合理,电池座自动组装机通过转盘式结构能够大大节省占用空间,有效提高电池座的组装效率,降低生产成本,再通过电池座检包机的第一ccd相机与第二ccd相机进行检测,有效提高检测效率,降低出错率,可满足电池座工业生产的需求。
5.为了实现本发明的目的,本发明采用如下技术方案:
6.一种电池座生产线,包括:电池座自动组装机、及连接于电池座自动组装机一侧的电池座检包机;
7.所述电池座自动组装机包括:
8.承载组件,包括工作台、安装于所述工作台顶面中部的凸轮分割器、连接所述凸轮分割器的转盘、及均匀间隔安装于所述转盘周缘上的多个治具;及
9.依次间隔围设于所述转盘周围的电池座主体组装组件、正极插片组件、负极插片组件、胶盖组装组件与成品输出组件;
10.所述电池座检包机包括:
11.用于连接所述成品输出组件的检包机主机台;
12.安装于所述检包机主机台上的移载取料组件;所述移载取料组件包括安装于所述检包机主机台上的支架、安装于所述支架顶部的横移直线模组、连接所述横移直线模组的横移板、及均匀间隔安装于所述横移板上的多个移载取料手;所述横移板的一端朝向所述成品输出组件;及
13.安装于所述移载取料组件一侧的检测组件;所述检测组件包括安装于所述横移板一侧的检测台、安装于所述检测台相对两端处的检测载具、安装于所述检测台一端相对两侧的第一ccd相机、及安装于所述检测台另一端底部的第二ccd相机;所述检测载具用于放
置成品电池座;所述第一ccd相机的检测方向与所述第二ccd相机的检测方向相互垂直。
14.上述电池座生产线,结构简单,设计合理,电池座自动组装机采用转盘式结构,将电池座主体组装组件、正极插片组件、负极插片组件及胶盖组装组件依次围设于转盘的周围,能够大大节省占用空间,减少工位之间的转运距离,有效提高电池座的组装效率,降低生产成本,再通过电池座检包机的第一ccd相机与第二ccd相机进行不同视角的检测,有效提高检测效率,降低出错率,可满足电池座工业生产的需求。
15.在其中一个实施例中,所述电池座主体组装组件包括电池座主体上料圆振、连接所述电池座主体上料圆振的电池座主体直振送料器、安装于所述电池座主体直振送料器末端处的定量送料器、及安装于所述定量送料器一端的电池座主体组装机械手;
16.所述正极插片组件包括正极料带放送轮、安装于所述正极料带放送轮一侧的正极间歇送料器、安装于所述安装于正极间歇送料器远离所述正极料带放送轮的一端处的正极切端器、及安装于所述正极切端器一侧的正极插片机械手;
17.所述负极插片组件包括负极料带放送轮、安装于所述负极料带放送轮一侧的负极间歇送料器、安装于所述负极间歇送料器远离所述负极料带放送轮的一端处的负极切端器、及安装于所述负极切端器一侧的负极插片机械手;
18.所述胶盖组装组件包括胶盖上料圆振、连接所述胶盖上料圆振的胶盖直振送料器、及安装于所述胶盖直振送料器末端的胶盖组装机械手。
19.在其中一个实施例中,所述定量送料器包括定位座、滑动连接于所述定位座内的推料块、及安装于所述定位座底面的取料气缸;所述取料气缸的活塞杆用于连接所述推料块,以驱动所述推料块在所述定位座内部滑动。
20.在其中一个实施例中,所述定位座的中部设有滑槽,所述滑槽用于匹配容纳所述推料块;所述定位座上对应于所述滑槽的一侧设有进料口,所述进料口的一端连通所述电池座主体直振送料器,所述进料口的另一端连通所述滑槽。
21.在其中一个实施例中,所述成品输出组件包括输出机械手、安装于所述输出机械手一侧的成品输出直振送料器、及安装于所述成品输出直振送料器末端处的定量阻挡器;所述检包机主机台连接所述成品输出直振送料器的末端。
22.在其中一个实施例中,所述所述定量阻挡器包括升降安装于所述成品输出直振送料器末端下方的阻挡块、及连接所述阻挡块的升降气缸;所述升降气缸的活塞杆用于连接所述阻挡块,以驱动所述阻挡块穿设所述成品输出直振送料器的末端。
23.在其中一个实施例中,所述检测台与所述成品输出直振送料器相邻设置;两个所述检测载具的间距等于相邻两个所述移载取料手的间距。
24.在其中一个实施例中,所述检测组件还包括间隔设置于所述检测台一端处的支撑台、可滑动安装于所述支撑台顶部一端的暂存板、固定安装于所述支撑台顶部另一端的推动气缸、及安装于所述支撑台一侧的排料坡道;所述推动气缸用于推动所述暂存板移动至所述移载取料手的下方;所述排料坡道的一端位于所述横移板的下方,所述排料坡道的另一端延伸至所述主机台的外部。
25.在其中一个实施例中,所述电池座检包机还包括安装于所述移载取料组件一端处的包装组件;所述包装组件包括位于所述横移板远离所述成品输出组件的一端处的包装传送模组、安装于所述包装传送模组一端的载带放送轮、安装于所述包装传送模组另一端的
封膜放送轮、位于所述封膜放送轮一侧的出货收集轮、及安装于所述包装传送模组中部的第一光纤传感器与所述第二光纤传感器。
26.在其中一个实施例中,所述第一光纤传感器的检测方向与所述第二光纤传感器的检测方向相互垂直。
附图说明
27.图1为本发明一实施方式的电池座生产线的立体示意图;
28.图2为图1所示的电池座生产线的另一视角的立体示意图;
29.图3为图1所示的电池座生产线中电池座自动组装机的立体示意图;
30.图4为图1所示的电池座生产线中电池座自动组装机的另一视角的立体示意图;
31.图5为图3所示的电池座生产线中电池座自动组装机的局部立体示意图,其中不包括胶盖组装组件与成品输出组件;
32.图6为图3所示的电池座生产线中电池座自动组装机的另一视角的局部立体示意图,其中不包括胶盖组装组件与成品输出组件;
33.图7为图3所示的电池座生产线中电池座主体组装组件的立体示意图;
34.图8为图7所示的电池座生产线中电池座主体组装组件的另一视角的局部立体示意图;
35.图9为图8所示的电池座生产线中电池座主体组装组件的局部结构分解示意图;
36.图10为图3所示的电池座生产线中电池座自动组装机的局部立体示意图,其中不包括电池座主体组装组件、正极插片组件、及负极插片组件;
37.图11为图10所示的圆圈a处的放大示意图;
38.图12为图10所示的电池座生产线中成品输出组件的局部结构半剖示意图;
39.图13为图12所示的圆圈b处的放大示意图;
40.图14为图1所示的电池座生产线中电池座检包机的立体示意图;
41.图15为图14所示的电池座生产线中电池座检包机的另一视角的立体示意图;
42.图16为图14所示的圆圈c处的放大示意图;
43.图17为图14所示的圆圈d处的放大示意图;
44.图18为图15所示的圆圈e处的放大示意图。
具体实施方式
45.为了便于理解本发明,下面将参照相关附图对本发明进行更全面的描述。附图中给出了本发明的较佳实施例。但是,本发明可以以许多不同的形式来实现,并不限于本文所描述的实施例。相反地,提供这些实施例的目的是使对本发明的公开内容的理解更加透彻全面。
46.需要说明的是,当元件被称为“固定于”另一个元件,它可以直接在另一个元件上或者也可以存在居中的元件。当一个元件被认为是“连接”另一个元件,它可以是直接连接到另一个元件或者可能同时存在居中元件。
47.除非另有定义,本文所使用的所有的技术和科学术语与属于本发明的技术领域的技术人员通常理解的含义相同。本文中在本发明的说明书中所使用的术语只是为了描述具
体的实施例的目的,不是旨在于限制本发明。
48.请参阅图1至图18,为本发明一实施方式的电池座生产线,包括电池座自动组装机、及连接于电池座自动组装机一侧的电池座检包机。其中,电池座自动组装机包括承载组件10、及依次间隔围设于承载组件10周围的电池座主体组装组件20、正极插片组件30、负极插片组件40、胶盖组装组件50与成品输出组件60。电池座检包机包括检包机主机台、安装于检包机主机台上的移载取料组件70、间隔安装于移载取料组件70一侧的检测组件80、及安装于移载取料组件70一端处的包装组件90;所述检包机主机台用于连接成品输出组件60,移载取料组件70远离包装组件90的一端靠近成品输出组件60。
49.所述承载组件10包括工作台11、安装于工作台11顶面中部的凸轮分割器12、连接凸轮分割器12的转盘13、及均匀间隔安装于转盘13周缘上的多个治具14。如图3所示,转盘13沿箭头方向旋转;电池座主体组装组件20、正极插片组件30、负极插片组件40、胶盖组装组件50与成品输出组件60依次围设于转盘13的周围。
50.所述电池座主体组装组件20包括电池座主体上料圆振21、连接电池座主体上料圆振21的电池座主体直振送料器22、安装于电池座主体直振送料器22末端处的定量送料器23、及安装于定量送料器23一端的电池座主体组装机械手24。电池座主体上料圆振21用于装载电池座主体25,电池座主体25从电池座主体上料圆振21送出,并沿着电池座主体直振送料器22送至定量送料器23处,以供电池座主体组装机械手24夹取。
51.在本实施例中,如图5至图9所示,定量送料器23包括定位座26、滑动连接于定位座26内的推料块27、及安装于定位座26底面的取料气缸28;取料气缸28的活塞杆用于连接推料块27,以驱动推料块27在定位座26内部滑动。
52.定位座26的中部设有滑槽261,滑槽261用于匹配容纳推料块27;滑槽261的长度方向与电池座主体直振送料器22的长度方向相互垂直。定位座26上对应于滑槽261的一侧设有进料口262,进料口262的一端连通电池座主体直振送料器22,进料口262的另一端连通滑槽261,使得电池座主体25可沿着进料口262转移至推料块27上。具体地,推料块27的末端设有凹陷270,凹陷270用于容纳单个电池座主体25,使得每次只推送一个电池座主体25,进而使得电池座主体组装机械手24每次只夹取一个电池座主体25,实现定量取料。电池座主体组装机械手24夹取电池座主体25后,将其转移至治具14内,接着转盘13旋转带动装载有电池座主体25的治具14依次移动至正极插片组件30、负极插片组件40的下方进行插片。
53.所述正极插片组件30包括正极料带放送轮31、安装于正极料带放送轮31一侧的正极间歇送料器32、安装于正极间歇送料器32远离正极料带放送轮31的一端处的正极切端器33、及安装于正极切端器33一侧的正极插片机械手34。正极料带放送轮31用于放送正极弹片料带,正极间歇送料器32用于运送正极弹片料带,正极切端器33用于裁切正极弹片料带以分离出单体的正极弹片,然后正极插片机械手34夹取正极弹片并插接于治具14内的电池座主体25上。由于正极插片组件30为本领域常见的切端插端结构,故不作过多的细节描述。
54.所述负极插片组件40包括负极料带放送轮41、安装于负极料带放送轮41一侧的负极间歇送料器42、安装于负极间歇送料器42远离负极料带放送轮41的一端处的负极切端器43、及安装于负极切端器43一侧的负极插片机械手44。负极料带放送轮41用于放送负极弹片料带,负极间歇送料器42用于运送负极弹片料带,负极切端器43用于裁切负极弹片料带以分离出单体的负极弹片,然后负极插片机械手44夹取负极弹片并插接于治具14内的电池
座主体25上。由于负极插片组件40为本领域常见的切端插端结构,故不作过多的细节描述。
55.所述胶盖组装组件50包括胶盖上料圆振51、连接胶盖上料圆振51的胶盖直振送料器52、及安装于胶盖直振送料器52末端的胶盖组装机械手53。胶盖上料圆振51用于装载胶盖54,胶盖54从胶盖上料圆振51送出,并沿着胶盖直振送料器52送至胶盖直振送料器52的末端处,胶盖组装机械手53夹取胶盖54后盖设于治具14内的电池座主体25上,以完成组装工作形成成品电池座55。此时,正极弹片与负极弹片夹设于电池座主体25与胶盖54之间。与传统的直线式组装设备,本发明的电池座自动组装机采用转盘式结构,将电池座主体组装组件20、正极插片组件30、负极插片组件40及胶盖组装组件50依次围设于转盘13的周围,能够大大节省占用空间,减少工位之间的转运距离,有效提高电池座的组装效率,降低生产成本。
56.所述成品输出组件60包括输出机械手61、安装于输出机械手61一侧的成品输出直振送料器62、及安装于成品输出直振送料器62末端处的定量阻挡器63;输出机械手61用于夹取治具14上的成品电池座55,然后再将成品电池座55转移放置于成品输出直振送料器62上,由成品输出直振送料器62送往下一工序。此处,定量阻挡器63用于分离出单独的成品电池座55,以便于下一工序取用。
57.在本实施例中,如图13所示,定量阻挡器63包括升降安装于成品输出直振送料器62末端下方的阻挡块631、及连接阻挡块631的升降气缸632;升降气缸632的活塞杆用于连接阻挡块631,以驱动阻挡块631穿设成品输出直振送料器62的末端后穿设于两个成品电池座55之间,以分离出单独的成品电池座55。进一步地,如图13所示,阻挡块631的顶端呈楔形设置,以便于阻挡块631穿设于两个相邻的成品电池座55之间。
58.与传统的电池座生产设备相比,本发明的电池座自动组装机,结构简单,设计合理,采用转盘式结构,将电池座主体组装组件20、正极插片组件30、负极插片组件40及胶盖组装组件50依次围设于转盘13的周围,能够大大节省占用空间,减少工位之间的转运距离,有效提高电池座的组装效率,降低生产成本。
59.所述检包机主机台连接成品输出直振送料器62的末端,以将成品电池座55送入移载取料组件70。所述移载取料组件70包括安装于检包机主机台上的支架71、安装于支架71顶部的横移直线模组72、连接横移直线模组72的横移板73、及均匀间隔安装于横移板73上的多个移载取料手74。其中,横移板73的一端朝向成品输出直振送料器62,横移板73的另一端朝向包装组件90。
60.在本实施例中,所述横移直线模组72为电动滑台等直线模组,为机械领域常见的直线运动模组,无需赘述。所述横移直线模组72可驱动横移板73沿其长度方向做往返运动,以将成品电池座55转移到不同工位上。
61.在本实施例中,如图16所示,移载取料手74包括安装于横移板73顶部的取料驱动气缸741、及连接于取料驱动气缸741的活塞杆的吸嘴742;吸嘴742用于吸取成品电池座55。
62.所述检测组件80包括安装于横移板73一侧的检测台81、安装于检测台81相对两端处的检测载具82、安装于检测台81一端相对两侧的第一ccd相机83、安装于检测台81另一端底部的第二ccd相机84、间隔设置于检测台81一端处的支撑台85、可滑动安装于支撑台85顶部一端的暂存板86、固定安装于支撑台85顶部另一端的推动气缸87、及安装于支撑台85一侧的排料坡道88;推动气缸87用于推动暂存板86移动至移载取料手74的下方;排料坡道88
的一端位于横移板73的下方,排料坡道88的另一端延伸至检包机主机台的外部。
63.其中,检测台81与成品输出直振送料器62相邻设置,两个检测载具82的间距等于相邻两个移载取料手74的间距。检测载具82用于放置成品电池座55;第一ccd相机83的检测方向与第二ccd相机84的检测方向相互垂直。
64.第一ccd相机83用于检测成品电池座55的平整度和胶盖的组装精度,并将检测结果传回控制系统。简单来说,第一ccd相机83用于检测成品电池座55的正负极端子底部到检测载具82的顶面之间的距离,若该距离位于预设范围内,则说明成品电池座55的平整度符合规格;另一方面,第一ccd相机83用于检测胶盖的顶端与检测载具82的顶面之间的距离,若该距离位于预设范围内,则说明胶盖的组装到位。
65.第二ccd相机84用于从下方检测成品电池座55内部的正负极端子是否组装到位,并将检测结果传回控制系统。具体地,检测台81上对应第二ccd相机84的一端设有过孔(图未示),第二ccd相机84穿过过孔后从下方检测成品电池座55的正负极端子外露部分的长度、位置是否符合规格,若不符合规格,则说明成品电池座55的正负极端子组装不到位。
66.具体地,在本实施例中,暂存板86的端部还安装有暂存载具860,暂存载具860用于承载良品。实际使用中,若经过第一ccd相机83与第二ccd相机84检测后的产品为良品,则推动气缸87驱动暂存板86移动至移载取料手74的下方,以便于移载取料手74释放良品临时放置于暂存载具860上。若经过第一ccd相机83与第二ccd相机84检测后的产品为不良品,则推动气缸87驱动暂存板86回缩,暂存载具860不在移载取料手74的下方,移载取料手74的吸嘴742释放不良品直接落入排料坡道88,以实现不良品的排放。在本实施例中,支撑台85与检测台81的间距等于相邻两个移载取料手74的间距。
67.所述包装组件90包括位于横移板73远离成品输出组件60的一端处的包装传送模组91、安装于包装传送模组91一端的载带放送轮92、安装于包装传送模组91另一端的封膜放送轮93、位于封膜放送轮93一侧的出货收集轮94、及安装于包装传送模组91中部的第一光纤传感器95与第二光纤传感器96。包装传送模组91用于传送载带97,良品对应放置于载带97上,然后盖上封膜(图未示)形成出货成品,该出货成品收卷于出货收集轮94上。
68.在本实施例中,第一光纤传感器95的检测方向与第二光纤传感器96的检测方向相互垂直,第一光纤传感器95与第二光纤传感器96均用于检测良品在载带97上的摆放位置是否端正。若第一光纤传感器95或第二光纤传感器96发现摆放位置不端正,则发出停机信号给控制系统,控制系统控制整个电池座检包机停止工作,待处理完异常后再重新启动工作。
69.如图15及图18所示,在本实施例中,包装传送模组91包括包装传送轨道911、安装于包装传送轨道911一端底面的包装传送齿轮912、及同轴连接包装传送齿轮912的传送驱动电机913。其中,包装传送轨道911用于供载带97穿设,具体地,载带97的中部均匀间隔设有多个容纳腔971,容纳腔971用于容纳良品;载带97的相对两侧分别均匀间隔设有多个通孔972,包装传送齿轮912的齿峰穿设进入包装传送轨道911的内部并对应卡设通孔972,使得包装传送齿轮912转动的同时可带动载带97沿着包装传送轨道911的长度方向进行移动,实现对载带97的传送。
70.与传统的电池座生产设备相比,本发明的电池座检包机,结构简单,使用方便,第一ccd相机83的检测方向与第二ccd相机84的检测方向相互垂直。通过第一ccd相机83与第二ccd相机84进行不同视角的检测,有效提高检测效率,降低出错率,可满足电池座工业生
产的需求。
71.综上所述,本发明的电池座生产线,结构简单,设计合理,电池座自动组装机采用转盘式结构,将电池座主体组装组件20、正极插片组件30、负极插片组件40及胶盖组装组件50依次围设于转盘13的周围,能够大大节省占用空间,减少工位之间的转运距离,有效提高电池座的组装效率,降低生产成本,再通过电池座检包机的第一ccd相机83与第二ccd相机84进行不同视角的检测,有效提高检测效率,降低出错率,可满足电池座工业生产的需求。
72.以上所述实施例的各技术特征可以进行任意的组合,为使描述简洁,未对上述实施例中的各个技术特征所有可能的组合都进行描述,然而,只要这些技术特征的组合不存在矛盾,都应当认为是本说明书记载的范围。
73.以上所述实施例仅表达了本发明的几种实施方式,其描述较为具体和详细,但并不能因此而理解为对发明专利范围的限制。应当指出的是,对于本领域的普通技术人员来说,在不脱离本发明构思的前提下,还可以做出若干变形和改进,这些都属于本发明的保护范围。因此,本发明专利的保护范围应以所附权利要求为准。