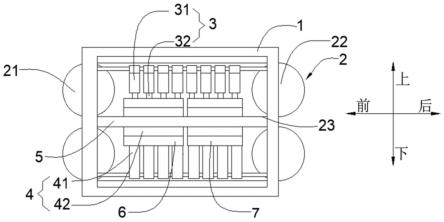
1.本发明涉及复合材料板材加工设备技术领域,特别是涉及一种双钢带压机。
背景技术:2.连续纤维增强热塑性复合材料板材是以连续纤维作为增强材料,以热塑性树脂为基体,通过将热塑性树脂熔融浸渍的工艺制造的高强度、高刚性、高韧性的复合材料,在其加工的过程中一般需要用到双带压机来做层叠复合,当复合加工温度超过250℃,压力超过2bar时,就需要用到双钢带压机。
3.目前的双钢带压机主要包括三种,分别是辊压式双钢带压机、链毯式双钢带压机和等压式双钢带压机,其中辊压式双钢带压机和链毯式双钢带压机提供的压力并不是面压,当对压力有严格要求的复合材料板材时,只能通过等压式双钢带压机进行加工,而等压式双钢带压机虽然可以提供面压,但由于其压力传递是通过与钢带直接接触的高压油或高压气体,因而需要复杂的密封系统,导致造价昂贵,并且还会存在泄漏风险。
技术实现要素:4.本发明的目的是:提供一种双钢带压机,其不仅能够持续提供面压,而且结构简单,造价低廉。
5.为了实现上述目的,本发明提供了一种双钢带压机,包括框架、两个传动装置、施压装置、两组与各所述传动装置一一对应的压合组件;
6.所述传动装置包括主动轮、从动轮以及传动绕于所述主动轮及所述传动轮外周的钢带,两个所述传动装置从上至下间隔对应设置,且两个所述钢带之间限定形成有传输通道,所述主动轮及所述从动轮均转动安装于所述框架上;
7.所述压合组件包括固定架和自润滑板,所述固定架安装在所述框架上,所述自润滑板设于至所述钢带所围合的空间内,且所述自润滑板的一侧安装在所述固定架上,另一侧与所述钢带的内侧抵接;
8.所述施压装置安装于其中一组所述压合组件上,所述施压装置包括驱动部和设于所述驱动部上的动力输出端,所述驱动部安装在所述固定架上,所述动力输出端与所述自润滑板连接,所述施压装置用于将所述自润滑板抵压至所述钢带的内侧,使得所述钢带朝向所述传输通道移动至所述传输通道变窄;
9.所述自润滑板包括板体与固体润滑剂,所述板体与所述钢带接触的一侧开设有容置槽,所述固定润滑剂设于所述容置槽内。
10.优选的,还包括两个安装在所述框架上且与各所述传动装置一一对应的热加工装置,所述热加工装置包括加热装置和冷却装置,所述加热装置和所述冷却装置从前至后间隔设置在所述钢带所围合的空间内,通过设置所述加热装置和所述冷却装置以满足不同的加工要求。
11.优选的,所述压合组件包括两块从前至后间隔设置的所述自润滑板,其中位于前
方的所述自润滑板的所述板体与所述加热装置连接,位于后方的所述自润滑板的所述板体与所述冷却装置连接,所述板体为导热板,通过将加热装置和冷却装置直接与所述自润滑板连接,减少能量损耗,保证加热效果与冷却效果。
12.优选的,所述加热装置包括用于加热的加热板,所述冷却装置包括用于冷却的冷却板,所述加热板和所述冷却板从前至后分别设于两块所述自润滑板上,通过设置所述加热板和所述冷却板,增大于所述板体的接触面积,进而增强加热效果与冷却效果。
13.优选的,所所述施压装置包括多个所述动力输出端,且各所述动力输出端均匀间隔的连接于所述自润滑板,通过设置多个所述动力输出端,使得所述自润滑板受到的压力更加均匀。
14.优选的,所述驱动部为气压缸或液压缸,气压缸与液压缸能够施加稳定的压力,并且能够根据需求进行调节。
15.优选的,所述板体的材质为高力黄铜,高力黄铜有较强的耐磨性能,且强度高、硬度大、耐化学腐蚀性强,适合作为所述自润滑板的基体。
16.优选的,所述固体润滑剂的材质为石墨、石墨烯、二硫化钼和六方氮化硼中的一种或多种,上述材质均具有较好的耐磨性、良好的热稳定性以及吸附性,能够更好的实现润滑作用。
17.优选的,所述自润滑板包括多个间隔设置的所述容置槽,通过增加所述容置槽的数量,使得所述固体润滑剂与所述板体的接触面积更大以便于在所述板体的表面形成固体润滑膜,进而增强润滑效果。
18.优选的,所述容置槽的形状为圆形、长条形和连续轨道形中的一种,通过改变所述容置槽的形状,使得所述固体润滑剂与所述板体的接触面积更大以便于在所述板体的表面形成固体润滑膜,进而增强润滑效果。
19.本发明实施例一种双钢带压机与现有技术相比,其有益效果在于:通过将施压装置安装在其中一组压合组件上,使得施压装置的动力输出端能够将压力作用至这一组压合组件中的自润滑板,然后自润滑板再将其施加的面压通过钢带传递至在传输通道内的材料,使材料获得的面压,并且因自润滑板的板体上设有固体润滑剂,所以在进行材料加工过程中,固体润滑剂会在板体上与所述钢带接触的一侧形成润滑膜,使得自润滑板与钢带进行相对运动时不会造成磨损,进而自润滑板能够持续提供面压,除此之外,本装置提供面压只需要通过施压装置与自润滑板,因此相对于现有技术,结构简单,造价低廉。
附图说明
20.图1是本发明实施例的双钢带压机的主体结构示意图;
21.图2是本发明实施例的双钢带压机的当容置槽的形状为圆形时自润滑板的结构示意图;
22.图3是本发明实施例的双钢带压机的当容置槽的形状为长条形时自润滑板的结构示意图;
23.图4是本发明实施例的双钢带压机的当容置槽的形状为连续轨道形时自润滑板的结构示意图。
24.图中,1、框架;2、传动装置;21、主动轮;22、从动轮;23、钢带;3、施压装置;31、驱动
部;32、动力输出端;4、压合组件;41、固定架;42、自润滑板;421、板体;4211、容置槽;422、固体润滑剂;5、传输通道;6、加热板;7、冷却板。
具体实施方式
25.下面结合附图和实施例,对本发明的具体实施方式作进一步详细描述。以下实施例用于说明本发明,但不用来限制本发明的范围。
26.在本发明的描述中,应当理解的是,本发明中采用的术语“上”“下”、“前”、“后”、“内”、“外”等指示的方位或位置关系为基于附图所示的方位或位置关系,仅是为了便于描述本发明和简化描述,而不是指示或暗示所指的装置或元件必须具有特定的方位、以特定的方位构造和操作,因此不能理解为对本发明的限制。
27.如图1和图2所示,包括框架1、两个传动装置2、施压装置3、两组与各所述传动装置2一一对应的压合组件4;
28.所述传动装置2包括主动轮21、从动轮22以及传动绕于所述主动轮21及所述传动轮外周的钢带23,两个所述传动装置2从上至下间隔对应设置,且两个所述钢带23之间限定形成有传输通道5,所述主动轮21及所述从动轮22均转动安装于所述框架1上;
29.所述压合组件4包括固定架41和自润滑板42,所述固定架41安装在所述框架1上,所述自润滑板42设于至所述钢带23所围合的空间内,且所述自润滑板42的一侧安装在所述固定架41上,另一侧与所述钢带23的内侧抵接;
30.所述施压装置3安装于其中一组所述压合组件4上,所述施压装置3包括驱动部31和设于所述驱动部31上的动力输出端32,所述驱动部31安装在所述固定架41上,所述动力输出端32与所述自润滑板42连接,所述施压装置3用于将所述自润滑板42抵压至所述钢带23的内侧,使得所述钢带23朝向所述传输通道5移动至所述传输通道5变窄;
31.所述自润滑板42包括板体421与固体润滑剂422,所述板体421与所述钢带23接触的一侧开设有容置槽4211,所述固定润滑剂设于所述容置槽4211内。
32.基于上述方案,通过将施压装置3安装在其中一组压合组件4上,使得施压装置3的动力输出端32能够将压力作用至这一组压合组件4中的自润滑板42,然后自润滑板42再将其施加的面压通过钢带23传递至在传输通道5内的材料,使材料获得的面压,并且因自润滑板42的板体421上设有固体润滑剂422,所以在进行材料加工过程中,固体润滑剂422会在板体421上与所述钢带23接触的一侧形成润滑膜,使得自润滑板42与钢带23进行相对运动时不会造成磨损,进而自润滑板42能够持续提供面压,除此之外,本装置提供面压只需要通过施压装置3与自润滑板42,因此相对于现有技术,结构简单,造价低廉。
33.如图1所示,为了能够更好地进行加工,并且满足不同的加工需求,还包括两个安装在框架1上且与各所述传动装置2一一对应的热加工装置(附图中未标出),所述热加工装置包括加热装置(附图中未标出)和冷却装置(附图中未标出),所述加热装置和所述冷却装置从前至后间隔设置在所述钢带23所围合的空间内,通过设置所述加热装置和所述冷却装置以满足不同的加工要求。
34.如图1所示,为了减少能源损耗,所述压合组件4包括两块从前至后间隔设置的所述自润滑板42,其中位于前方的所述自润滑板42的所述板体421与所述加热装置连接,位于后方的所述自润滑板42的所述板体421与所述冷却装置连接,所述板体421为导热板,通过
将加热装置和冷却装置直接与所述自润滑板42连接,减少能量损耗,保证加热效果与冷却效果。
35.如图1所示,为了增强加热效果与冷却效果所述加热装置包括用于加热的加热板6,所述冷却装置包括用于冷却的冷却板7,所述加热板6和所述冷却板7从前至后分别设于两块所述自润滑板42上,通过设置所述加热板6和所述冷却板7,增大与所述板体421的接触面积,进而增强加热效果与冷却效果。
36.如图1所示,为了使所述自润滑板42的受力更加均匀,所述施压装置3包括多个所述动力输出端32,且各所述动力输出端32均匀间隔的连接于所述自润滑板42,通过设置多个所述动力输出端32,使得所述自润滑板42受到的压力更加均匀。
37.优选的,为了便于操作,所述驱动部31为气压缸或液压缸,气压缸与液压缸不仅能够施加稳定的压力,并且能够根据需求进行调节。
38.优选的,为了增加使用寿命,所述板体421的材质为高力黄铜,高力黄铜有较强的耐磨性能,且强度高、硬度大、耐化学腐蚀性强,适合作为所述自润滑板42的基体。
39.优选的,为了保证润滑效果,所述固体润滑剂422的材质为石墨、石墨烯、二硫化钼和六方氮化硼中的一种或多种,上述材质均具有较好的耐磨性、良好的热稳定性以及吸附性,能够更好的实现润滑作用。
40.如图2和图3所示,所述自润滑板包括多个间隔设置的所述容置槽4211,通过增加所述容置槽4211的数量,使得所述固体润滑剂422与所述板体421的接触面积更大以便于在所述板体421的表面形成固体润滑膜,进而增强润滑效果。
41.如图2-图4所示,为了增强润滑效果,所述容置槽4211的形状为为圆形、长条形和连续轨道形中的一种,通过改变槽孔的形状使得所述固体润滑剂422与所述板体421的接触面积更大以便于在所述板体421的表面形成固体润滑膜,进而增强润滑效果。
42.本发明的工作过程为:将材料放入传输通道5中,通过两个钢带23的转动带动材料进行移动,在移动过程中先通过加热装置进行加热、再通过冷却装置进行冷却,并且施压装置3持续提供压力至其中一组压合组件4中的自润滑板42,然后再由自润滑板42将其施加的面压通过钢带23持续提供至材料,最终材料成型并从传输通道5中移出。
43.综上,本发明实施例提供一种双钢带压机,其通过将施压装置3安装在其中一组压合组件4上,使得施压装置3的动力输出端32能够将压力作用至这一组压合组件4中的自润滑板42,然后自润滑板42再将其施加的面压通过钢带23传递至在传输通道5内的材料,使材料获得的面压,并且因自润滑板42的板体421上设有固体润滑剂422,所以在进行材料加工过程中,固体润滑剂422会在板体421上与所述钢带23接触的一侧形成润滑膜,使得自润滑板42与钢带23进行相对运动时不会造成磨损,进而自润滑板42能够持续提供面压,除此之外,本装置提供面压只需要通过施压装置3与自润滑板42,因此相对于现有技术,结构简单,造价低廉。
44.以上所述仅是本发明的优选实施方式,应当指出,对于本技术领域的普通技术人员来说,在不脱离本发明技术原理的前提下,还可以做出若干改进和替换,这些改进和替换也应视为本发明的保护范围。