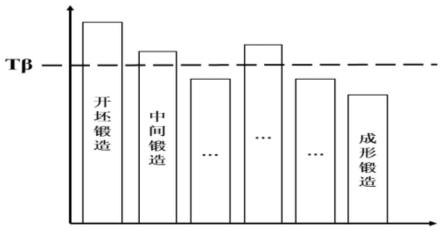
一种短流程tc25g钛合金高均匀棒材的制备方法
技术领域
1.本发明属于有色金属加工技术领域,涉及航空航天及其他行业用tc25g钛合金高均匀棒材,具体涉及一种短流程tc25g钛合金高均匀棒材的制备方法。
背景技术:2.近年来,随着我国航空航天产业的快速发展,航空发动机及飞机结构件用高温钛合金的需求越来越大,特别是对高性能高温钛合金以及长寿命高温钛合金的需求最为迫切。tc25g钛合金因其具有优越的高温、高强度和长寿命的特点,已开始在多种型号发动机和飞机结构件上使用,并逐步成为航空航天用主型高温钛合金材料之一。业内悉知,tc25g钛合金是一种综合性能良好的马氏体型α+β两相钛合金,该合金是在tc25合金基础上为提高高温钛合金的性能和工作寿命而研制的改良型合金,名义成分为ti-6al-4mo-4zr-2sn-1w-0.2si。该合金的最高工作温度为500℃~550℃,被推荐为450℃~550℃使用的高压压气机盘和转子叶片材料,具有广泛的应用前景。
3.目前,tc25g钛合金棒材主要用于制造航空发动机压气机盘件,由于压气机盘件一般在高温高压环境下服役,为保证盘件的安全性,对盘件组织和探伤均匀性要求极高。上述需求为制备出高均匀的tc25g钛合金棒材,并以该合金棒材为原材料,为后续经制坯和模锻制备出合格的盘件奠定了基础。而由于tc25g钛合金因所含合金元素种类多、含量高,随着棒材规格的增大,锻造过程中如何实现原始晶粒充分细化和坯料整体均匀变形至关重要,在此基础上才能保证合金棒材组织均匀,进而为合金盘件组织和探伤的均匀性提供保证。
4.有鉴于此,特提出本发明,通过采用更为科学的变形路线,并配合精确控制的变形过程及参数,实现变形量和变形均匀性的良好匹配,最终获得组织均匀细小的合金棒材。
5.为解决以上难点,需要在常规锻造工艺的基础上重新设计并优化合金大规格棒材生产过程。通过制定准确的锻造工艺路线及变形参数,采取相适应的锻造方式,获得高均匀的tc25g钛合金大规格棒材成为该合金锻件制备的关键技术之一。
技术实现要素:6.本发明的目的在于克服上述现有技术的缺点,提供一种短流程tc25g钛合金高均匀棒材的制备方法,能够生产出合格的tc25g钛合金ф200mm~ф350mm棒材,棒材制备流程短、能耗少,制备的棒材组织均匀细小,棒材整体均匀性良好,可满足航空发动机及其他行业对该合金棒材的严格要求,适用于工业化生产。
7.为实现上述目的,本发明提供了如下技术方案:
8.这种短流程tc25g钛合金高均匀棒材的制备方法,所述制备方法具体包括,
9.步骤1、开坯锻造:将钛合金铸锭加热至相变点温度以上100℃~250℃保温指定时间t1,出炉后对所述钛合金铸锭进行多火次镦拔锻造,得到第一坯料,锻后空冷;其中,火次之间可采用回炉补温方式,单道次变形量为20%~40%,累加变形量大于80%;
10.步骤2、中间锻造:
11.步骤2.1、第一阶段:将步骤1中得到的第一坯料在相变点温度以上20℃~120℃至相变点温度以下20℃~60℃进行2~4火次镦拔锻造,得到第二坯料,锻后空冷;其中,火次之间采用回炉补温方式,单道次变形量为30%~50%,累加变形量大于90%,最后一火次在相变点以上30℃~60℃内进行保温及锻造,变形量大于30%;
12.步骤2.2、第二阶段:将步骤2.1中得到的第二坯料在相变点温度以下30℃~80℃内进行多火次保温及锻造,得到第三坯料,锻后空冷;其中,火次之间采用回炉补温方式,单道次变形量为20%~40%,每火次累加变形量大于40%;
13.步骤2.3、第三阶段:对步骤2.2中得到的第三坯料的表面裂纹进行清除,进行重复加热和锻造,循环2~5火次直至坯料组织充分破碎,得到第四坯料;其中,火次之间采用回炉补温方式;
14.步骤3、成形锻造:将步骤2.3得到的第四坯料加热至相变点以下30℃~80℃保温指定时间t2,出炉后将第四坯料锻造整形成圆棒,期间可采用回炉补温方式,单道次变形量为10%~40%,锻后空冷。
15.进一步,所述s1中指定时间t1的计算方式如下:
16.t1=d0×
(0.45~0.8) (1)
17.式(1)中,d0为钛合金铸锭最小直径,单位为mm,t1的单位为min。
18.进一步,所述步骤2.1中第二坯料的横截面为正方或者八方,以保证第二坯料各部分均匀变形。
19.进一步,所述步骤2.2中保温时间为t3,且t3的计算方式如下:
20.t3=d
20
×
(0.6~0.8) (2)
21.式(2)中,d
20
为第二坯料的最小直径,单位为mm,t3的单位为min。
22.进一步,所述步骤2.2中第三坯料的横截面形状为正方或者八方,以保证第三坯料各部分均匀变形。
23.进一步,所述步骤3中指定时间t2的计算方式如下:
24.t2=d
40
×
(0.6~0.8) (3)
25.式(3)中,d
40
为第四坯料的最小直径,单位为mm,t2的单位为min。
26.进一步,所述步骤3中圆棒的规格为ф200mm~ф350mm。
27.与现有技术相比,本发明提供的技术方案包括以下有益效果:采用开坯锻造和中间锻造的组合锻造工艺,可适当采用回炉补温,大大缩短了tc25g钛合金的制备周期;根据合金反复再结晶细化晶粒原理,优化设计工艺路线(三个阶段的中间锻造),通过加热温度、变形量和变形方式的优化设置以及加热和锻造参数的精确控制,获得组织均匀一致的tc25g钛合金棒材;在锻造过程中采用回炉补温,在保证tc25g钛合金坯料充分均匀变形的同时大大缩短加热保温时间,实现了合金组织破碎并避免了保温时间过长引起的晶粒长大,充分实现了合金晶粒均匀细化;此外,在中间锻造过程中,根据合金组织演变规律确定了最佳的组织细化变形过程,通过最短的变形过程获得了满足要求的合金组织,极大地缩短了tc25g钛合金棒材的制备过程,生产效率得到了显著提升。
附图说明
28.此处的附图被并入说明书中并构成本说明书的一部分,与说明书一起用于解释本
发明的原理。
29.为了更清楚地说明本发明实施例或现有技术中的技术方案,下面将对实施例或现有技术描述中所需要使用的附图作简单地介绍,显而易见地,对于本领域普通技术人员而言,在不付出创造性劳动性的前提下,还可以根据这些附图获得其他的附图。
30.图1为本发明提供的短流程tc25g钛合金高均匀棒材的制备流程图;
31.图2为本发明提供的短流程tc25g钛合金高均匀棒材的工艺路线图;
32.图3为本发明提供的tc25g钛合金棒材的金相取样位置图;
33.图4(a)为本发明实施例1提供的tc25g钛合金头部棒材低倍组织图;
34.图4(b)为本发明实施例1提供的tc25g钛合金头部棒材1/2r处低倍组织图;
35.图4(c)为本发明实施例1提供的tc25g钛合金尾部棒材低倍组织图;
36.图4(d)为本发明实施例1提供的tc25g钛合金尾部棒材1/2r处低倍组织图;
37.图5(a)为本发明实施例1提供的tc25g钛合金头部棒材边部热处理态显微组织图;
38.图5(b)为本发明实施例1提供的tc25g钛合金头部棒材1/2r处热处理态显微组织图;
39.图5(c)为本发明实施例1提供的tc25g钛合金尾部棒材心部热处理态显微组织图;
40.图6(a)为本发明实施例2提供的tc25g钛合金头部棒材低倍组织图;
41.图6(b)为本发明实施例2提供的tc25g钛合金头部棒材1/2r处低倍组织图;
42.图6(c)为本发明实施例2提供的tc25g钛合金尾部棒材低倍组织图;
43.图6(d)为本发明实施例2提供的tc25g钛合金尾部棒材1/2r处低倍组织图;
44.图7(a)为本发明实施例2提供的tc25g钛合金头部棒材边部热处理态显微组织图;
45.图7(b)为本发明实施例2提供的tc25g钛合金头部棒材1/2r处热处理态显微组织图;
46.图7(c)为本发明实施例2提供的tc25g钛合金尾部棒材心部热处理态显微组织图。
具体实施方式
47.这里将详细地对示例性实施例进行说明,其示例表示在附图中。下面的描述涉及附图时,除非另有表示,不同附图中的相同数字表示相同或相似的要素。以下示例性实施例中所描述的实施方式并不代表与本发明相一致的所有实施方式。相反,它们仅是与所附权利要求书中所详述的、本发明的一些方面相一致的方法的例子。
48.结合图1-2所示,本发明提供了一种短流程tc25g钛合金高均匀棒材的制备方法,具体包括,
49.步骤1、开坯锻造:将钛合金铸锭加热至相变点温度以上100℃~250℃保温指定时间t1,出炉后对所述钛合金铸锭进行多火次镦拔锻造,锻后空冷,得到第一坯料;其中,火次之间采用回炉补温方式,单道次变形量为20%~40%,累加变形量大于80%;
50.步骤2、中间锻造:
51.步骤2.1、第一阶段:将步骤1中得到的第一坯料在相变点温度以上20℃~120℃至相变点温度以下20℃~60℃进行2~4火次镦拔锻造,锻后空冷,得到第二坯料;其中,火次之间采用回炉补温方式,单道次变形量为30%~50%,累加变形量大于90%,最后一火次在相变点以上30℃~60℃内进行保温及锻造,变形量大于30%;
52.步骤2.2、第二阶段:将步骤2.1中得到的第二坯料在相变点温度以下30℃~80℃内进行多火次保温及锻造,锻后空冷,得到第三坯料;其中,火次之间采用回炉补温方式,单道次变形量为20%~40%,每火次累加变形量大于40%;
53.步骤2.3、第三阶段:对步骤2.2中得到的第三坯料的表面裂纹进行清除,进行重复加热和锻造,循环2~5火次直至坯料组织充分破碎,得到第四坯料;其中,火次之间采用回炉补温方式;
54.步骤3、成形锻造:将步骤2.3得到的第四坯料加热至相变点以下30℃~80℃保温指定时间t2,出炉后将第四坯料锻造整形成圆棒,期间可采用回炉补温方式,单道次变形量为10%~40%,锻后空冷。
55.进一步,所述s1中指定时间t1的计算方式如下:
56.t1=d0×
(0.45~0.8) (1)
57.式(1)中,d0为钛合金铸锭最小直径,单位为mm,t1的单位为min。
58.进一步,所述步骤2.1中第二坯料的横截面为正方或者八方,以保证第二坯料各部分均匀变形。
59.进一步,所述步骤2.2中保温时间为t3,且t3的计算方式如下:
60.t3=d
20
×
(0.6~0.8) (2)
61.式(2)中,d
20
为第二坯料的最小直径,单位为mm,t3的单位为min。
62.进一步,所述步骤2.2中第三坯料的横截面形状为正方或者八方,以保证第三坯料各部分均匀变形。
63.进一步,所述步骤3中指定时间t2的计算方式如下:
64.t2=d
40
×
(0.6~0.8) (3)
65.式(3)中,d
40
为第四坯料的最小直径,单位为mm,t2的单位为min。
66.进一步,所述步骤3中圆棒的规格为ф200mm~ф350mm。
67.为了使本领域的技术人员更好地理解本发明的技术方案,下面结合附图及实施例对本发明作进一步详细描述。
68.实施例1
69.本实施例以具体的tc25g钛合金棒材为例,对本发明提供的制备方法进行详细阐述,这种短流程tc25g钛合金高均匀棒材的制备方法,具体包括:
70.步骤1、开坯锻造:
71.对tc25g钛合金铸锭进行锯切后坯料单重约1800kg,合金相变点为980℃。铸锭采用台阶式升温至1170℃(合金相变点以上190℃)保温300min,出炉后进行镦拔锻造,累加变形约为50%,随后继续在1080℃(合金相变点以上100℃)进行保温及镦拔锻造,单道次变形量约为35%,累加变形量约70%,完成锻造后得到第一坯料,锻后空冷。
72.步骤2、中间锻造:
73.步骤2.1、第一阶段:第一坯料在1080℃(合金相变点以上100℃)至920℃(合金相变点以下60℃)内进行3火次镦拔锻造,单道次变形量约为35%,前2火次累加变形量约70%,第3火次保温温度为1020℃(合金相变点以上40℃),变形量约为35%,第3火次锻造完成后得到的第二坯料横截面为八方,锻后空冷;
74.步骤2.2、第二阶段:将完成以上3火次锻造的第二坯料打磨清除表面裂纹后,在
935℃(合金相变点以下45℃)保温420min,出炉后进行拔长,单道次变形量约为25%,累加变形量为50%,其中适当采用回炉保温方式,锻造完成后得到第三坯料,锻后空冷;
75.步骤2.3、第三阶段:第三坯料打磨清除表面裂纹后,在935℃(合金相变点以下45℃)保温300min,出炉后进行直拔,单道次变形量约为30%,累加变形量为60%,其中适当采用回炉保温方式,拔长完成后得到的第四坯料横截面为八方,锻造完成后空冷。
76.步骤3、成形锻造:
77.将第四坯料在930℃(合金相变点以下50℃)保温240min,出炉后进行拔长,变形量约为20%,锻后坯料横截面为圆形,回炉补温至930℃保温60min,出炉后采用型砧整形成ф270mm棒坯,成形结束后空冷。
78.经以上锻造成形的棒坯,后续通过机加工成ф260mm的成品棒材(一),结合图3所示位置,对成品棒材(一)进行金相取样,其中,a处代表棒材边部,b代表棒材1/2r处,c处代表棒材心部。图4(a)~图4(d)为观察到的成品棒材(一)不同取样位置的低倍组织图,由图4(a)~图4(d)可知,棒材头尾低倍组织均匀细小,不同位置低倍组织均匀一致。图5(a)~图5(c)为观察的成品棒材(一)不同取样位置热处理态的显微组织图,由图5(a)~5(c)可知,棒材显微组织呈等轴状或短棒状组织,不同位置显微组织均匀一致。
79.实施例2
80.本实施例以具体的tc25g钛合金棒材为例,对本发明提供的制备方法进行详细阐述,这种短流程tc25g钛合金高均匀棒材的制备方法,具体包括:
81.步骤1、开坯锻造:
82.对tc25g钛合金铸锭进行锯切后坯料单重约860kg,合金相变点为980℃。铸锭采用台阶式升温至1170℃(合金相变点以上190℃)保温300min,出炉后进行镦拔锻造,单道次变形量约为30%,累加变形约为60%,完成锻造后空冷。坯料经打磨清除表面裂纹后,加热至1080℃(合金相变点以上100℃)保温210min,出炉后进行镦拔锻造,单道次变形量约为35%,累加变形量约70%,完成锻造后得到第一坯料,锻后空冷。
83.步骤2、中间锻造:
84.步骤2.1、第一阶段:第一坯料在1080℃(合金相变点以上100℃)至920℃(合金相变点以下60℃)内进行4火次镦拔锻造,单道次变形量约为35%,前3火次累加变形量约120%,第4火次保温温度为1030℃(合金相变点以上50℃),变形量约为35%,第4火次完成后得到的第二坯料横截面为八方,锻后空冷;
85.步骤2.2、第二阶段:将完成以上4火次锻造的第二坯料打磨清除表面裂纹后,在930℃(合金相变点以下50℃)保温360min,出炉后进行镦拔锻造,单道次变形量约为30%,累加变形量为90%,其中适当采用回炉保温方式,锻造完成后得到第三坯料,空冷;
86.步骤2.3、第三阶段:第三坯料打磨清除表面裂纹后,在920℃(合金相变点以下60℃)保温330min,出炉后进行镦拔锻造,单道次变形量约为30%,累加变形量为90%,其中适当采用回炉保温方式,最后一次拔长后得到的第四坯料横截面为八方,锻造完成后空冷;第四坯料打磨清除表面裂纹后,在915℃(合金相变点以下65℃)保温360min,出炉后进行直拔,单道次变形量约为30%,累加变形量为60%,其中适当采用回炉保温方式,最后一次拔长后得到的第五坯料横截面为八方,锻造完成后空冷。
87.步骤3、成形锻造:
88.第五坯料打磨清除表面裂纹后,将第五坯料在910℃(合金相变点以下70℃)保温240min,出炉后进行拔长,变形量约为35%,锻后坯料横截面为圆形,回炉补温至910℃保温60min,出炉后采用型砧整形成ф270mm棒坯,成形结束后空冷。
89.经以上锻造成形的棒坯,后续通过机加工成ф260mm的成品棒材(二),结合图3所示位置,对成品棒材(二)进行金相取样,其中,a处代表棒材边部,b代表棒材1/2r处,c处代表棒材心部。图6(a)~图6(d)为观察到的成品棒材(二)不同取样位置的低倍组织图,由图6(a)~图6(d)可知,棒材头尾低倍组织均匀细小,不同位置低倍组织均匀一致。图7(a)~图7(c)为观察到的成品棒材(二)不同取样位置热处理态的显微组织图,由图7(a)~图7(c)可知,棒材显微组织呈等轴状或短棒状组织,不同位置显微组织均匀一致。
90.综上,本发明提供的制备方法,根据钛合金反复再结晶均匀细化晶粒原理,形成了开坯锻造和中间锻造的组合锻造工艺路线,通过合理设置变形温度、变形量和变形方式并通过加热和锻造参数的精确控制,可制备出组织均匀一致的tc25g钛合金棒材。在开坯锻造中适当采用回炉补温方式,保证合金铸态晶粒充分破碎的同时大幅缩短坯料保温时间,提高生产效率。在中间锻造过程中,利用合金反复再结晶细化晶粒原理优化设计工艺路线,同时适当采用回炉补温,减少合金保温时间,避免保温过程中的晶粒长大。通过以上改进,可实现合金晶粒充分均匀细化,以获得高均匀的合金坯料。在后续的变形过程中,以直拔变形为主,确保合金组织均匀性,同时适当采用回炉补温,在保证组织破碎的同时减少反复加热时间,缩短合金制备周期。综上,利用本发明提供的制备方法,可制备出高均匀性的tc25g合金棒材,且制备周期大大缩短,生产效率极大提升。
91.以上所述仅是本发明的具体实施方式,使本领域技术人员能够理解或实现本发明。对这些实施例的多种修改对本领域的技术人员来说将是显而易见的,本文中所定义的一般原理可以在不脱离本发明的精神或范围的情况下,在其它实施例中实现。
92.应当理解的是,本发明并不局限于上述已经描述的内容,并且可以在不脱离其范围进行各种修改和改变。本发明的范围仅由所附的权利要求来限制。