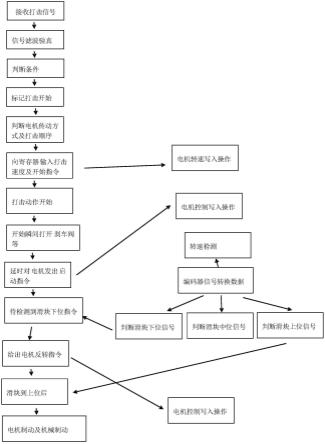
1.本发明涉及压力机领域,尤其是涉及改进的电动螺旋压力机、控制系统及控制方法。
背景技术:2.电动螺旋压力机通过电机来实现的滑块的向下打击与向上回程。驱动电机工作进行正、反向旋转,对电网冲击很大, 电负荷经常出现尖峰值,冲击电流大,功率因数较低,驱动电机发热现象严重。
3.针对之前的电动螺旋压力机(例如cn201210588700.8一种电动螺旋压力机控制系统及控制方法),申请人进行控制系统改进,提供了一套改进设备。
4.作为持续改进,发明人针对电路进行改进,提供更为先进的控制方法。
技术实现要素:5.为了提高电动压力机的控制能力,简化控制流程,从而提高设备的自动化,本发明提供一种改进的电动螺旋压力机、控制系统及控制方法。
6.本发明包括电机驱动器,用于控制电机给螺杆提供旋转动力;plc,作为控制中枢,与电机驱动器通讯连接;控制电源模块,通过电线281与280a给plc输入直流电源;各个电机电路,三相电通过两组串联的继电器常开开关接入对应电机。
7.本发明包括配套于压力机的可移动的辅助机械臂,在辅助机械臂上水平伸缩有伸缩杆部,在伸缩杆部摆动的机头,在机头上设置有磁力座,在磁力座端部设置有测量探头,在辅助机械臂尾部设置有上顶部,在载台一侧或机架上安装伸缩支撑座;在伸缩支撑座顶部安装多普勒测量仪;测量探头用于测量工件高度及多普勒测量仪探头位置。
8.该方法接收发出的打击信号;信号滤波验真,进行条件判断,当滤波信号符合设定要求,标记打击开始,否则不开始;判断电机传动方式及打击顺序;向寄存器输入打击速度及开始指令;打击动作开始;开始瞬间打开飞轮的刹车阀;延时对对应电机发出启动指令。
9.该方法包括信号滤波验真;其中,进行信号滤波验真步骤中,执行转速测量滤波算法;首先,进行预测;x(k+1)=x(k-1)+q;其中,x(k+1)为k+1 时刻的转速估态值;k为时间;x(k-1)为k-1时刻的转速值;q为系统过程噪声系数;其次,进行滤波争议计算;kf=x(k+1)/(x(k+1)+r);其中,r为过程噪声系数;kf为滤波增益系数;再次,转速估计计算;y(k)=y(k-1)+kf*[d(k)-y(k-1)];其中,y(k)为优化后当前转速;d(k)为k时的实际测量值;之后,进行估计误差计算;x(k)= x(k+1)*(1-kf);循环迭代完成预估滤波算法。
[0010]
在滑块下行进行打击前,首先,通过多普勒测量仪监测滑块部下部的压头下表面;然后,当多普勒测量仪监测压头下表面的下行到达设定时和/或速度发生变化时,说明压头已与工件接触,滑块由重力下拉螺杆变为螺杆下行一个螺纹间隙s而下顶压滑块,螺纹间隙s=(v1-v2)
ꢀ×
t-(h1-h2)或s=v3
×
t;v1为压头与工件接触时的下行速度,v2为压头与工件接触后的初始压速度,t为v1变为v2时间间隔,h1为压头与工件接触时的高度,h2为压头与工件接触时的压头与工件接触后的初始压高度;v3是螺杆转速。
[0011]
本发明包括机架,在机架上设置有载台及在载台上升降设置的滑块部;在机架上设置有控制系统和/或应用有控制方法。
[0012]
综上所述,本发明包括以下至少一种有益技术效果:本发明通过改进了现有电路设计,通过plc、继电器实现互锁、联动控制,从而保证了控制系统的安全。本发明改进了控制方法,设计了中位控制、滤波功能,从而实现了精准控制,去噪,安全可靠。本发明采用了改进的滤波去噪方案。本发明通过多普勒进行距离与速度测试,螺杆转速可知,根据探头实现对工件高点进行测量并记录多普勒雷达坐标,通过多普勒测距与上顶进行间隙测量与下行位置控制。本发明通过实现滤波去噪与间隙补偿实现精准控制。
附图说明
[0013]
图1是压力机优选结构示意图。
[0014]
图2是主回路主电机控制图。
[0015]
图3是主回路从电机控制图。
[0016]
图4是控制电源的控制图。
[0017]
图5是主回路电机的部分控制图i。
[0018]
图6是主回路电机的部分控制图ii。
[0019]
图7是风机润滑控制图。
[0020]
图8是plc控制图。
[0021]
图9是plc输入部分控制图i。
[0022]
图10是plc输入部分控制图ii。
[0023]
图11是plc输入部分控制图iii。
[0024]
图12是plc输出部分控制图i。
[0025]
图13是plc的i/o输入机械手控制图i。
[0026]
图14是plc的i/o输入机械手控制图ii。
[0027]
图15-图24是工作流程图。
[0028]
图25是压力机有限结构图。
[0029]
附图标记说明:1、载台;2、滑块部;3、辅助机械臂;4、上顶部;5、测量探头;6、磁力座;7、伸缩杆部;8、伸缩支撑座;9、多普勒测量仪。
具体实施方式
[0030]
以下结合附图1-25对本发明作进一步详细说明,以下各个实施例的技术方案与技术特征可以单独或组合使用。
[0031]
如图1,压力机执行以下步骤:接收发出的打击信号;信号滤波验真,进行条件判断,当滤波信号符合设定要求,标记打击开始,否则不开始;判断电机传动方式及打击顺序;向寄存器输入打击速度及开始指令;打击动作开始;开始瞬间打开飞轮的刹车阀;延时对对应电机发出启动指令;在向寄存器输入打击速度及开始指令后,进行电机转速写入操作;在延时对对应电机发出启动指令后,进行电机控制写入操作;在编码器中,进行信号转换数据,进行转速检测、判断滑块上位信号、判断滑块中位信号及判断滑块下位信号状态;当延时对对应电机发出启动指令后,判断滑块处于下位信号状态,进行待检测到滑块下位指令;给出电机反转指令,滑块到上位后并判断滑块处于上位信号状态,进行电机制动及机械制动;当给出电机反转指令,电机控制写入操作。
[0032]
通过上述流程,实现了对压力机的控制,其通过开关实现了全流程自动化控制, 增加中位控制,实现了位置验证,避免识别错误,从而提高控制的精准度。
[0033]
如图2-15,电力控制部分包括电机驱动器,用于控制电机给螺杆提供旋转动力;plc,作为控制中枢,与电机驱动器通讯连接;控制电源模块,通过电线281与280a给plc输入直流电源,从而保证plc的电压稳定;各个电机电路,三相电通过两组串联的继电器常开开关接入对应电机;从而实现双保险与远程低压控制。
[0034]
电机控制模块包括并联且电路结构相同的主电机控制模块与从电机控制模块;如图1主电机控制模块,包括主机开关km11,其通过线路233级线路281的继电器开关控制,从而实现低电压控制高电压,安全可靠,主机开关km11输入端通过主继电器qf11接入市电且输出端给主机控制器供电,主机控制器电连接plc以控制主电机srm旋转,从而实现智能控制;如图8,plc通过交换机及调试模块电连接有触摸屏;如图3控制电源模块, 通过电源变压器tc1接入交流电,并在初级线圈并联电压表,次级线圈电连接有通电常亮电源指示灯hl1,以对电路状态进行指示,保证供电安全;次级线圈通过电源常开开关sa1后,一路电连接有ac转dc模块,通过线路280、281输出,从而实现直流电输出;一路通过线路237输出交流电,从而实现交流电输出,一路电连接有继电器控制电路,继电器控制电路包括与电源常开开关sa1电连接的继电器常闭开关sb2,继电器常闭开关sb2输出端并联有继电器常开开关sb1支路及继电器km1的常开开关、km2的常开开关的串联支路,之后,电连接有并联的继电器km1的控制线圈、km2的控制线圈;从而实现闭锁联动控制,当继电器km1、km2的控制线圈中的一个出现问题,继电器km1的常开开关、km2的常开开关均断开,实现保护,sb2是应急开关,sb1是用于先导控制。
[0035]
如图5,电机电路的电机包括用于驱动载台1升降的顶料泵,用于润滑的润滑泵、散热风机。
[0036]
如图15,流程1,当接收到外部打击信号m0.6时,进行滤波,时间200ms;当确认滤波后的信号满足预设条件,进行打击,启动光电保护信号m4.7,验证光电保护信号m4.7是否有物体进入工作区域,开始执行程序打击开始指令m13.0;
其中,外部打击信号滤波定时器t130,用于对异常干扰过滤; 允许打击信号m13.4;单控设备或联机控制设备判断v1700.0;如图16,流程2;当开始执行程序打击开始指令m13.0时,对当前设备的传动形式进行判断,并将电机正反转转速赋值于通讯协议相关寄存器当中,并开始数据写入流程,之后,进入自动工作程序中;其中,允许打击信号m13.4;程序打击指令m13.0;打击顺序数据vw918;电机传动形式数据vw226;电机正转转速vw208;电机反转转速vw210;寄存器打击转速vw974;寄存器回程转速vw972;电机速度写入指令m17.1;打击动作开始指令m20.0;如图17,流程3,当进入流程2的自动工作程序中,电机正转,滑块开始下行,当检测到滑块位置到达指定点后,向电机发送反向允许控制指令,并在程序中标记滑块下行完成;vw226 电机控制指令;vw904寄存器控制指令;m8.0外部制动器阀;m8.1电机驱动使能信号;m13.6滑块下位信号;t116延时发送电机控制信号定时器;m17.0电机控制信号;m20.1滑块下行完成信号。
[0037]
如图18,流程4,当滑块下行完成后,电机开始反向转动,当检测到滑块位置到达指定点后,向电机发送电机制动指令,并在程序中,标记滑块完成工作;vw228电机反转起动数据;vw230电机制动停车数据;vw904寄存器控制指令;m13.5滑块上位信号位;m20.2滑块上行完成信号位;m20.3液压顶出开始信号位;m14.4液压顶出开始输出。
[0038]
如图19-20,还执行有位置检测流程5。plc接收到行程开关、传感器、电流变化或电平变化产生的脉冲信号,并转为位置数据;根据位置数据判断滑块的位置反馈给plc控制系统;其中,sm0.0始终导通;vd500脉冲数据;vd536脉冲转换位置系数;vd512位置数据;mul_r乘法运算;如图21,还执行有流程6,写入电机控制及转速;m17.1电机速度写入指令;m17.0 电机控制写入指令;vb237电机从站地址;&vb972寄存器地址起始符号;m26.0及m26.1完成通讯的脉冲;vb909及vb911通讯失败代码;如图22-23,流程7,根据位置信息判断滑块的位置反馈给控制系统滑块下及中间位置信号;如图24为滑块下滑标记流程。
[0039]
vd512 位置数据;vd580 滑块停止位数据;进行浮点数据比较;m13.5 滑块上位信号位;vd1100 允许打击上位数据;m15.3 滑块允许自动打击信号位; vd20 滑块下位数据;m13.6 滑块下位信号位;在流程1中,当利用脉冲增量式编码器对滑块的转速进行测量的时候,会因为plc的中断时间偏移或外部机械震动等原因速度检测波形会产生噪声数据。因此利用预估滤波算法的方式对检测结果进行滤波让数据更加接近真实数据。
[0040]
其中,进行信号滤波验真步骤中,执行转速测量滤波算法。
[0041]
首先,进行预测;x(k+1)=x(k-1)+q;其中,x(k+1)为k+1 时刻的转速估态值;k为时间;x(k-1)为k-1时刻的转速值;q为
系统过程噪声系数;其次,进行滤波争议计算;kf=x(k+1)/(x(k+1)+r);其中,r为过程噪声系数;kf为滤波增益系数;再次,转速估计计算;y(k)=y(k-1)+kf*[d(k)-y(k-1)];其中,y(k)为优化后当前转速;d(k)为k时的实际测量值;之后,进行估计误差计算;x(k)= x(k+1)*(1-kf);循环迭代上述4步完成预估滤波算法。
[0042]
如图25,压力机包括载台1,滑块部2。由于螺旋压力机运行时,其存在正反转实现升降。作为升降部,螺栓与螺母直接存在配合间隙,升降部与下端连接的滑块部2可能存在间隙,例如当螺栓与滑块部2连接时,当滑块部2下降的时候,在重力的作用下,螺栓的螺纹下表面与螺母的下方的螺纹的上表面接触,而与螺母的上方的下表面产生螺纹间隙。当滑块部2与位于载台1上的工件接触时,螺栓的螺纹下表面与螺母的下方的螺纹的上表面分离,此时,螺母继续旋转,而与螺母的上方的下表面压力接触并进行下压动作,而该间隙造成行程匹配误差,影响下压力,采用压力传感器控制,需要每次都进行程序调整,在高速与高压压力的作用下,容易损坏闭环的闭环反馈传感器。
[0043]
为了实现对间隙空程的监控,提高控制精度,配套有可移动的辅助机械臂3,在辅助机械臂3上水平伸缩有伸缩杆部7,在伸缩杆部7摆动的机头,在机头上设置有磁力座6,在磁力座6端部设置有测量探头5,在辅助机械臂3尾部设置有上顶部4,在载台1一侧或机架上安装伸缩支撑座8,其可以采用磁吸式或螺栓紧固,可以根据不同的工件,调整其安装位置,并通过伸缩部调整高度;在伸缩支撑座8顶部安装多普勒测量仪9,用于测量安装在滑块部2下部的压头下表面的下行实时的高度到达设定时和/或速度发生变化时,说明压头已与工件接触,滑块由重力下拉螺杆变为螺杆下行一个螺纹间隙s而下顶压滑块,压头到达设定高度后,上顶部4上顶压头,从而压头上行,该上行距离主要为螺纹间隙s,其可以包括相关的配合间隙或组装误差。多普勒通过测量该上行距离,补偿电机旋转,实现开环控制,可以精确对滑块下行距离进行参数补偿。本发明通过实现滤波去噪与间隙补偿实现精准控制。图25中测量为简化示意图,其结构不限制保护范围。
[0044]
本发明实施例一种改进的电动螺旋压力机、控制系统及控制方法的实施原理为:用户使用时,将可移动的辅助机械臂3安装在压机架底部,根据不同压机及工件的规格,配合不同的磁力座6,通过伸缩杆部7调整伸长量。通过测量探头5测量固定在载台1上的工件的高点位置,确定多普勒测量仪9的位置高度、压头下表面初始位置等参数,然后进行压测量,作为优选,可以先使得压头先低速空跑进行测量,从而使得v2位为零。
[0045]
以上均为本发明的较佳实施例,并非依此限制本发明的保护范围,故:凡依本发明的结构、形状、原理所做的等效变化,均应涵盖于本发明的保护范围之内。