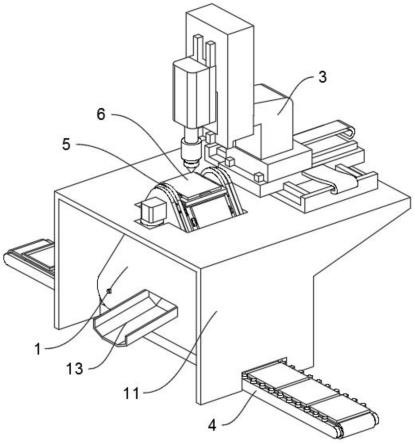
1.本发明涉及钕铁硼切割领域,尤其涉及全自动钕铁硼激光切割机。
背景技术:2.钕铁硼磁铁被广泛应用于硬盘、手机、耳机等电子产品内,根据使用的产品不同需要对钕铁硼磁铁加工成不同形状,对钕铁硼切割的方法有多种,其中激光切割是较为高效、精确的一种。
3.激光切割目前限于对6mm以下的钕铁硼使用,将钕铁硼基础板材置于激光切割设备上,在基础板材表面切割形成若干特定形状的钕铁硼材料;
4.现有钕铁硼激光切割设备需要配置独立的夹持工位、上料工位、排料工位,一次切割完成后需要夹持工位向排料工位排放切割料,再移动夹持工位向上料工位取料、归位,进行二次加工,难以实现连续性切割工作。
技术实现要素:5.本发明的目的是解决现有技术存在的以下问题:现有钕铁硼激光切割设备需要配置独立的夹持工位、上料工位、排料工位,一次切割完成后需要夹持工位向排料工位排放切割料,再移动夹持工位向上料工位取料、归位,进行二次加工,难以实现连续性切割工作。
6.为解决现有技术存在的问题,本发明提供全自动钕铁硼激光切割机,包括激光切割机体和传料组件,围绕所述传料组件设置若干载架,传料组件驱动载架围绕其轮廓循环传导,激光切割机体对位所述传料组件顶部的载架,传料组件底部设有导料传送带,传料组件的底部平行于导料传送带;
7.载架包括架框,架框的两侧对称设有两组夹块,两组夹块在架框的表面相对弹性开合滑动,夹块固定有触条,传料组件的底部具有两组对称分布的挡条,两组挡条用于挤压两组触条扩张。
8.优选的,两组所述触条靠近前进方向的一端向外侧弯曲扩张,两组所述挡条接近触条的一端向内弯曲收拢。
9.优选的,所述传料组件包括两组面板,两组所述面板之间设置两组同轴连接的传动链条,所述载架置于传动链条之间、且围绕传动链条分布,传动链条的底部平行导料传送带,传动链条通过轴杆转动连接所述架框的边缘。
10.优选的,所述架框的两侧对称分布四个滑块,滑块与架框边缘弹性滑动,所述轴杆与滑块转动连接。
11.优选的,所述架框远离前进方向的一端具有挡块,所述挡条初始挤压触条扩张时,挡块未到达传料组件的底部。
12.优选的,所述导料传送带的两侧设置有限位轮,所述夹块与限位轮之间具有间隙。
13.优选的,所述传动链条呈三角形状传导分布,所述面板之间固定有排料板,排料板倾斜穿出一侧面板。
14.优选的,所述传动链条的两个倾斜部位外侧转动设有压料辊,所述压料辊对位载架,压料辊的表面具有若干橡胶凸起。
15.与相关技术相比较,本发明提供的全自动钕铁硼激光切割机具有如下有益效果:
16.1、本发明通过传动链条对若干载架循环传导,在挡条挤压接触触条扩张以及触条弹性收缩,使载架自动夹持导料传送带表面的基料板以及释放加工后的余料框架在导料传送带的表面,实现对钕铁硼的连续性自动激光切割加工,料物传导衔接紧密、加工效率高;
17.2、本发明通过设置压料辊剥离切割后粘连的成品件,使成品件由排料板排出,而余料框架由导料传送带导出,实现双路分料,便于对后续余料回收以及成品料整理。
附图说明
18.图1为本发明的整体结构示意图之一;
19.图2为本发明的整体结构示意图之二;
20.图3为本发明的钕铁硼围绕传料组件的传导状态结构示意图;
21.图4为本发明的排料板结构示意图;
22.图5为本发明的传料组件结构示意图;
23.图6为本发明的载架结构示意图之一;
24.图7为本发明的载架结构示意图之二;
25.图8为本发明的触条与挡条对位结构示意图;
26.图9为本发明的载架在导料传送带表面拾料状态结构示意图。
27.图中标号:1、面板;11、加工台;12、压料辊;13、排料板;2、载架;21、架框;22、滑块;23、轴杆;24、触条;25、夹块;26、挡块;3、激光切割机体;4、导料传送带;41、限位轮;5、传动链条;6、基料板;7、粘连料板;8、余料框架;9、挡条。
具体实施方式
28.为了使本发明的目的、技术方案及优点更加清楚明白,以下结合附图及实施例,对本发明进行进一步详细说明。应当理解,此处所描述的具体实施例仅仅用以解释本发明,并不用于限定本发明。
29.以下结合具体实施例对本发明的具体实现进行详细描述。
30.实施例一
31.如图1、图2和图3所示,全自动钕铁硼激光切割机,具有加工台11,将激光切割机体3安装在加工台11表面,传料组件由加工台11下部穿出其表面,导料传送带4置于传料组件的下部;
32.如图3、图4和图5所示,传料组件包括两组面板1,两组面板1对称设置,在面板1之间设置两组同轴连接的传动链条5,传动链条5的传导轮廓可为三角形状、矩形状、半圆形状、梯形状、平行四边形状等,要确保传动链条5的底部具有平行于导料传送带4的阶段,传动链条5的其中一个链轮连接安装电机;
33.如图3、图4、图6和图7所示,若干载架2置于传动链条5之间,并且围绕传动链条5分布,载架2包括四方形的架框21,架框21中部贯通,用于落料,架框21的两侧对称分布四个滑块22,滑块22通过弹簧弹性滑动在架框21的边缘,滑块22的滑动方向与载架2移动方向齐
平,在滑块22表面转动连接轴杆23,轴杆23连接两侧的传动链条5;
34.通过电机驱动两组传动链条5同步单向运动,通过轴杆23的带动使架框21围绕传动链条5传动,通过滑块22与架框21的弹性滑动,使架框21适应在传动链条5弯折部位的传导,避免锁死传导动作;
35.在架框21的两侧对称设有两组夹块25,夹块25位于架框21的外侧面,夹块25通过弹簧与架框21弹性滑动连接,使两组夹块25在架框21的表面可相对弹性开合滑动,夹块25贯穿架框21固定有触条24,触条24位于架框21的内侧面,在面板1的内侧底部对称固定两组挡条9,两组触条24靠近前进方向的一端向外侧弯曲扩张,两组所述挡条9接近触条24的一端向内弯曲收拢,架框21远离前进方向的一端具有挡块26;
36.如图3、图4、图8和图9所示,加工动作如下步骤:
37.a、设定传动链条5的传导方向为逆时针,电机驱动传动链条5间歇传导,每次传导长度以相邻载架2换位为基准,开启导料传送带4向左侧传导料物;
38.b、基料板6由导料传送带4右侧排列传导,此时传动链条5下部的触条24受挡条9支撑后带动夹块25发生扩张,扩张幅度大于基料板6宽度,最前部的基料板6进入到夹块25之间,并受挡块26推动向右侧移动;
39.c、直至触条24脱离与挡条9的接触,两组夹块25闭合夹持基料板6,使该工位的载架2上料完成,并跟随传动链条5向上传导,下移工位的载架2继续进行夹持基料板6;
40.d、载架2夹持基料板6上升至传动链条5的顶部,并到达水平状态,该位置为切割工位,通过激光切割机体3对基料板6进行激光切割;
41.e、基料板6被切割后有的成品件直接脱落有的成品件粘附在余料表面,此时形成粘连料板7,粘连料板7跟随传动链条5后续移动过程中进行脱料,使载架2表面只剩下余料框架8;
42.f、当载架2移动接近传动链条5的底部时,挡条9的弯曲端与触条24的弯曲端逐渐接触,使触条24带动夹块25逐渐扩张,释放余料框架8落在导料传送带4表面,这一过程要确保夹块25释放余料框架8时,挡块26未到达底部位置,避免挡块26阻挡余料框架8向左排放;
43.g、释放余料框架8的载架2在传动链条5底部持续向右移动,进行下一轮的夹持上料工作。
44.在导料传送带4右端的两侧设置若干限位轮41,限位轮41用于限制基料板6直线传导,使基料板6能精确进入夹块25之间,并且在最前部基料板6受挡块26推动时,后方的基料板6被方向推动,在限位轮41的限制下,有效避免基料板6因被反向挤压发生散乱;
45.限位轮41对基料板6夹持位置的高度位于基料板6厚度一半以下的位置,而夹块25初始对位基料板6位置的高度位于厚度一半以上的位置,使夹块25与限位轮41之间具有间隙,避免发生碰撞;
46.实施例二
47.如图2、图3和图4所示,传动链条5的传导轮廓可为三角形、梯形、半圆形等形状,确保传动链条5的底部具有平行于导料传送带4的阶段,传动链条5两侧为向下扩张的倾斜轮廓,面板1轮廓与传动链条5适配,在面板1之间的下部固定排料板13,排料板13倾斜穿出一侧面板1;
48.在加工台11两侧转动安装两组压料辊12,压料辊12对位传动链条5两侧倾斜部位,
并在压料辊12的表面设置若干橡胶凸起;
49.由于夹块25初始夹持基料板6时未完全契合,当夹块25夹持基料板6倾斜上升时,基料板6与压料辊12挤压接触,压料辊12在旋转过程中将基料板6压入夹块25更深位置,使基料板6贴附架框21的表面,使切割时基料板6的固定形态更加精确;
50.当载架2带动粘连料板7倾斜下降时,压料辊12表面的橡胶凸起挤压粘连料板7,使成品件脱落到排料板13表面,避免成品件跟随余料框架8排出;
51.成品件落在排料板13表面排出,余料框架8送到导料传送带4表面排出,实现分离出料。