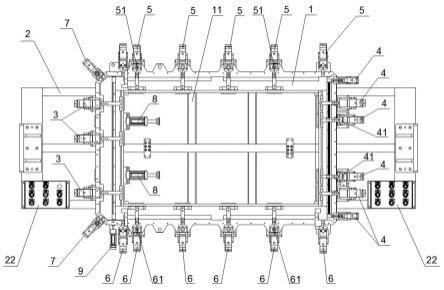
1.本发明涉及新能源电池托盘加工技术领域,具体为一种动力电池托盘快速拼框焊接方法。
背景技术:2.近年来,新能源电动车辆逐渐取代燃油汽车,成为日益增长的汽车类型。电动汽车中的动力电池是其电能的储存部件,在整个车辆中属于核心部件。动力电池模组被电池托盘承载,电池托盘再与车辆底架相连,构成坚固的承载车身。由于新能源电动车重与其续航里程紧密关联,基于车身轻量化考虑,铝制车架结构由于其轻量化、耐腐蚀和回收残值等综合指标均达到优秀,成为越来越多新能源汽车的选择,电池托盘作为其结构重要部件,也免不了使用铝合金材料进行加工制作。
3.现有的大部分铝合金电池托盘采用铝合金型材连接组合而成,空心的铝合金型材具有质量小,承载能力强的优点。利用其多变的空心结构,首尾相互搭接或者榫卯,构成电池托盘纵横框架承载结构。在进行电池托盘拼焊时,需要工装夹具将各个边框杆件位置牢固固定,然后再使用弧焊将接头处焊接。在焊接机器人广泛使用的今天,如何将工装夹具适应焊接机器人摆臂的要求,以及提高焊接的效率和质量,保证托盘的整体尺寸达到要求,尽量减少尺寸误差,是当今铝合金电池托盘生产需要着重考虑的问题。
4.检索到关于电池托盘焊接工装的现有文献如下:1、自锁滑动式电池托盘边框焊接固定工装;cn201920556549.7;一种自锁滑动式电池托盘边框焊接固定工装,采用固定基准梁和活动基准梁同时对电池托盘边梁进行定位,固定基准梁布置在其中一组长边梁和短边梁的内侧进行定位,活动基准梁布置在另一组长边梁和短边梁的内侧,活动基准梁上配设有辅推气动元件、限位基准块和楔形自锁机构,活动基准梁通过辅推气动元件和限位基准块进行滑动定位,活动基准梁上还通过楔形自锁机构实现压紧自锁。通过上述方式,本实用新型自锁滑动式电池托盘边框焊接固定工装能够保证电池托盘边框内部是采用整体梁接触,活动的梁也能起到定位基准的作用,防止产品局部的不可控变形,整体均可实施电控,极大的方便了生产操作,有效的的提高了生产效率。
5.2、具有翻转功能的电池托盘固定工装;cn201721762431.7;一种具有翻转功能的电池托盘固定工装,所述电池托盘包括底板、设于所述底板边缘位置的侧挡及焊接于所述侧挡上的若干支耳,所述电池托盘固定工装包括底架、固设于所述底架上且用于对所述电池托盘进行固定和限位的电池托盘固定结构;所述电池托盘固定结构包括设于所述底架上的固定架,所述电池托盘置于所述固定架上,所述电池托盘固定结构还包括设于所述固定架上且从所述电池托盘的纵向和横向方向对所述电池托盘进行限位的第一限位结构以及设于所述固定架上且从所述电池托盘的竖直方向上对所述电池托盘进行限位的第二限位结构;还包括分别与所述底架的两端可拆卸连接的用于180度翻转所述电池托盘的第一翻转机以及第二翻转机。
6.3、铝合金电池托盘边框底板摩擦搅拌焊接固定工装;cn201920556218.3;一种铝合金电池托盘边框底板摩擦搅拌焊接固定工装,包括水平方向定位机构和垂直方向定位机构,水平方向定位机构包括一组直角边固定定位基准梁以及一组直角边双开活动夹紧机构,边框底板顶至直角边固定定位基准梁进行限位固定,并通过直角边双开活动夹紧机构对边框底板水平方向压紧定位,然后通过垂直方向定位机构对边框底板的垂直方向压紧定位。通过上述方式,本实用新型铝合金电池托盘边框底板摩擦搅拌焊接固定工装能够确保产品摩擦搅拌焊接前定位的一致性,对产品水平和垂直方向同时夹持固定,保证装夹强度和焊接质量的稳定性,解决产品在摩擦搅拌后变形取出问题,极大提高了生产效率,实施批量化生产作业要求。
7.虽然现有文献中公开了一些电池托盘的焊接工装,但是对于具有前边框、前斜边框、左右边框和后边框的动力电池托盘拼焊,并没有相关的记载,对于具有多边框的动力电池托盘如何实现精确高效的拼焊,一直是本领域技术人员需要考虑解决的问题。
技术实现要素:8.本发明的目的是提供一种动力电池托盘快速拼框焊接方法,所使用的工装可匹配电池托盘边框cmt拼焊机器人的作业需求,通过可旋转的工装机架上布置与各个方向边框相对应的伸缩定位销和夹紧装置,实现电池托盘的多个边框一次夹紧焊接即可完成焊接,电池托盘整体尺寸得到保证,焊接质量大大提高,作业效率提升的优点。
9.为达到上述目的,本发明的技术方案如下:一种动力电池托盘快速拼框焊接方法,焊接定位方法包括:电池托盘边框包括前边框、后边框、左边框、右边框和前斜边框组成,其中后边框、左边框和右边框上分别预加工两个工艺孔,在焊接工装上分别设置匹配的伸缩定位销和夹紧装置,利用工艺孔与定位销的限位关系,以及夹紧装置夹持固定电池托盘边框边缘,从而固定焊接位置。
10.所述焊接定位方法还包括如下步骤:(a)后定位销升起,放入后边框并将两个工艺孔对准后定位销插入,后夹紧装置夹紧后边框,后边框定位完成;(b)左定位销升起,放入左边框并将两个工艺孔对准左定位销插入,左夹紧装置夹紧左边框,左边框定位完成;(c)右定位销升起,放入右边框并将两个工艺孔对准右定位销插入,右夹紧装置夹紧右边框,右边框定位完成;(d)侧定位装置气缸伸出,放入前边框,并用前边框端部抵靠侧定位装置,前定位装置回缩并抵靠在前边框的内侧面,然后前夹紧装置夹紧前边框边缘,前边框定位完成;侧定位装置气缸缩回,前定位装置伸出;(e)分别放入前边框两侧的前斜边框,前斜边框两端与前边框、左右边框端部贴靠,前斜夹紧装置夹紧前斜边框,前斜边框定位完成;(f)启动cmt焊接机器人焊接,焊接工装随着焊接位置自动旋转,完成焊接后,松开所有夹紧定位装置。
11.所述焊接工装的机架两端为端架,端架上中轴线处设置转轴座,转轴座通过转轴与旋转台连接;机架的四周设置若干定位夹紧装置。
12.所述夹紧装置包括前夹紧装置、前斜夹紧装置、后夹紧装置、右夹紧装置和左夹紧装置。
13.所述前夹紧装置、前斜夹紧装置、后夹紧装置、右夹紧装置和左夹紧装置均由支撑台、夹紧气缸、快速夹和夹紧臂组成,支撑台安装夹紧气缸,夹紧气缸的活塞杆固定连接快速夹的连杆施力端,快速夹的连杆动作端固定连接夹紧臂。
14.所述支撑台下方安装插销气缸,插销气缸的活塞杆穿过支撑台通孔,活塞杆端部连接定位插销;后夹紧装置对应设置后定位销,右夹紧装置对应设置右定位销,左夹紧装置对应设置左定位销。
15.所述焊接工装的机架前部内侧设置前定位装置,前定位装置的气缸活塞杆端部设置定位块,定位块的内端面与前边框的内侧面贴靠。前定位装置的作用在于:将前边框的前后位置进行定位。
16.所述焊接工装的机架侧部设置侧定位装置,侧定位装置的气缸活塞杆端部设置定位块,定位块的端面与前边框的端部贴靠。侧定位装置的作用在于:将前边框的左右位置进行定位。
17.所述焊接工装的机架两端为端架,两个端架上分别设置控制箱,两个控制箱上布置控制按钮分别与各个夹紧装置、定位销和定位装置电性相连。
18.所述机架中部设置水平纵横的中梁。纵横中梁结构可保证机架外形结构刚度更好,在旋转焊接过程中保证电池托盘框架的稳定。
19.本发明的优点:1、本发明应用于全铝电池托盘边框的拼焊,可匹配电池托盘边框cmt拼焊机器人的作业需求,通过可旋转的工装机架上布置与各个方向边框相对应的伸缩定位销和夹紧装置,其定位的逻辑为:先通过形成具有工艺孔的后边框、左边框和右边框形成的半封闭框架,然后在半封闭框架已经在定位插销固定的基础上,再完成前边框的定位,由此电池托盘边框的外形尺寸得以精确确定,最后把前斜边框嵌入到空缺的位置并贴合后夹紧定位,由于贴靠面为斜面楔形贴合,因此通过平移必然可以实现紧密贴靠,最后整体焊接。经现场测试,从型材边框夹紧至焊接完成,仅需要8分钟即可完成所有操作,较之前的工作效率提高了150%。
20.2、本发明可实现电池托盘各个边框一次夹紧焊接即可完成焊接,定位准确、快速而稳固,焊接效率大大提高,焊接作业效率提升,电池托盘整体尺寸得到保证的优点。
21.3、后边框和左右边框所对应的定位夹紧装置,采用了气动伸缩定位销+气动快速夹夹紧一体化的夹紧定位装置进行定位,整个插销夹紧定位装置结构紧凑,布置合理。
22.4、本发明工装设备自动化程度高,操作便捷,操作箱设置于端架两端,操作人员可一面观察组装情况,一边对设备进行操作。
23.附图说明:图1为本发明俯视结构示意图;图2为工装上伸缩定位销和夹紧装置布置图;图3为带伸缩定位销的夹紧装置外观结构图;图4为带伸缩定位销的夹紧装置另一角度外观结构图;图5为不带伸缩定位销的夹紧装置外观结构图;
图6为不带伸缩定位销的夹紧装置另一角度外观结构图;图7为电池托盘边框俯视结构示意图;图中的序号和部件名称为:1-机架;11-中梁;2-端架;21-转轴座;22-控制箱;3-前夹紧装置;4-后夹紧装置;41-后定位销;5-右夹紧装置;51-右定位销;6-左夹紧装置;61-左定位销;7-前斜夹紧装置;8-前定位装置;9-侧定位装置。
具体实施方式
24.实施例1一种动力电池托盘快速拼框焊接方法,焊接定位方法中包括:电池托盘边框包括前边框、后边框、左边框、右边框和前斜边框组成,其中后边框、左边框和右边框上分别预加工两个工艺孔,在焊接工装上分别设置匹配的伸缩定位销和夹紧装置,利用工艺孔与定位销的限位关系,以及夹紧装置夹持固定电池托盘边框边缘,从而固定焊接位置。
25.动力电池托盘快速拼框焊接方法,焊接定位方法还包括如下步骤:(a)后定位销升起,放入后边框并将两个工艺孔对准后定位销插入,后夹紧装置夹紧后边框边缘,后边框定位完成;(b)左定位销升起,放入左边框并将两个工艺孔对准左定位销插入,左夹紧装置夹紧左边框边缘,左边框定位完成;(c)右定位销升起,放入右边框并将两个工艺孔对准右定位销插入,右夹紧装置夹紧右边框边缘,右边框定位完成;(d)侧定位装置气缸伸出,放入前边框并抵靠侧定位装置,前定位装置伸出抵靠在前边框侧面,然后前夹紧装置夹紧前边框边缘,前边框定位完成;侧定位装置气缸缩回;(e)分别放入前边框两端的前斜边框,前斜夹紧装置夹紧前斜边框边缘,前斜边框定位完成;(f)启动cmt焊接机器人焊接,焊接工装随着焊接位置自动旋转,完成拼焊后,松开所有夹紧定位装置。
26.所述焊接工装的机架1两端为端架2,端架2上中轴线处设置转轴座21,转轴座21通过转轴与旋转台连接;机架1的四周设置若干定位夹紧装置31。
27.所述夹紧装置包括支撑台、夹紧气缸、快速夹和夹紧臂,支撑台安装夹紧气缸,夹紧气缸的活塞杆固定连接快速夹的连杆施力端,快速夹的连杆动作端固定连接夹紧臂。
28.所述夹紧装置的支撑台下方安装插销气缸,插销气缸的活塞杆穿过支撑台端部连接定位插销。
29.所述焊接工装的机架1两端为端架2,两个端架2上分别设置控制箱22,两个控制箱22上布置控制按钮分别与各个方向的伸缩定位销和夹紧装置电性相连。
30.所述机架1中部设置水平纵横的中梁11。
31.应用实施例:根据实施例1所述电池边框,原拼焊工艺采用无伸缩定位销的固定工装,分别将前后左右边框用气动工装进行夹紧后焊接,在焊接前对各边框的焊接处进行检查,人工确认拼接缝合格后开始焊接,焊接后取出进行焊缝检查,因焊缝不合格造成的不良率为1.5%左右,其不良的原因主要在于:焊接过程中,边框产生移位,导致焊缝间隙过大,边框焊接边缘
没有严密贴靠;其次,边框在拼合的过程中存在原始间隙,人工检查无法全部将其检出。
32.采用实施例1的电池托盘快速拼焊方法和工装后,因焊缝不合格造成的不良率下降为0.3%,由此可见,本发明焊接方法和工装取得了显著的技术效果。