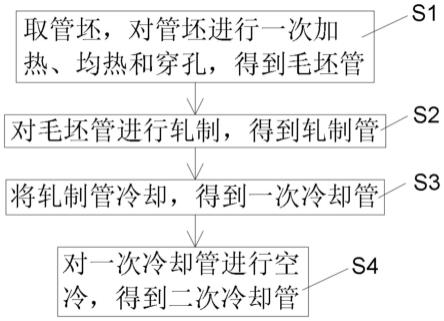
p91/p92无缝钢管的制备方法
技术领域
1.本发明涉及钢管制造技术领域,具体而言,涉及一种p91/p92无缝钢管的制备方法。
背景技术:2.p91/p92钢是在9cr-1mo(p9)钢的基础上,通过添加少量的nb、v或w微合金化元素并控制n元素的含量开发的新型马氏体型耐热钢,该钢热强性好,达到了奥氏体型耐热钢持久强度的水平,综合力学性能优异,热导性高,线膨胀系数低,具有良好的淬透性和可焊性。目前,9cr(p91/p92)钢已广泛用于超临界/超超临界电站锅炉承压耐热钢关键部件。
3.根据钢的轧制理论,钢加热到高温奥氏体区后进行热变形,钢的组织随形变量、变形温度、应变速率等的不同,加工硬化和动态软化(动态回复和再结晶)同时进行。奥氏体再结晶就是在轧制过程和轧制后γ组织结构发生变化,γ晶粒尺寸取决于轧制温度和形变量,并且,在一定温度下,不论发生动态还是静态再结晶,都有一个临界变形量要求,温度越低所需的临界变形量越大。含不同成分钢的各温度点(如再结晶终止温度tr及ar3等)并不相同,通常含nb钢的γ再结晶区温度tr在1050℃以上。钢在高温奥氏体区变形时有三个不同的轧制变形温度段,即再结晶温度区,为tr以上、未再结晶温度区tr~ar3以及两相温度区、ar3以下。钢在再结晶区和未再结晶温度区轧制,再结晶的γ晶粒尺寸随着轧制变形量的增大而减小,并会达到一个极限,如果变形量不能达到再结晶的临界变形量,得到的是部分再结晶和未再结晶的混合组织,晶粒尺寸差别较大,这种组织在后续相变成马氏体组织后仍不均匀,晶粒尺寸相差较大,混晶严重;如果在多道次低温轧制时不能全部进行再结晶,轧制后在很多处会出现比原始晶粒大几倍的巨大晶粒,这是由于轻微的变形在局部地方诱发晶界移动而发生的现象;这种现象就是混晶,混晶组织对材料性能有较多的不利影响。
4.因此,消除混晶组织时钢管制作的必备工序。在发明人所知的现有技术中,常见的消除混晶组织方法是通过在热处理前增加一道等温退火作为预备热处理工序;由于等温退火工序十分耗时,因此通过现有技术中的方式达到消除混晶组织的目的,会导致p91/p92钢管的制备效率大大降低,并增加较多的额外热处理成本,无法实现短期大规模的生产。
技术实现要素:5.本发明的主要目的在于提供一种p91/p92无缝钢管的制备方法,能够解决采用现有钢管的制备方法中通过增加等温退火工序消除混晶组织而导致钢管制作效率低和成本高的问题。
6.为了实现上述目的,根据本发明的一方面,提供了一种p91/p92无缝钢管的制备方法,制备方法包括以下步骤:
7.s1,取管坯,对管坯进行一次加热、均热和穿孔,得到毛坯管;
8.s2,对毛坯管进行轧制,得到轧制管;
9.s3,将轧制管冷却至400℃~650℃,使形变奥氏体发生相变,得到一次冷却管,其中,冷却的速率为0.8℃/s~2.5℃/s;
10.s4,对一次冷却管进行空冷,得到二次冷却管。
11.进一步地,步骤s3中的冷却的速率为0.8℃/s~2.0℃/s。
12.进一步地,步骤s3中冷却的方式为喷水冷却或水雾冷却,冷却速率通过冷却介质的流量和压力控制,冷却的终止温度通过冷却的时间确定。
13.进一步地,轧制前的毛坯管的温度为950℃~1100℃,冷却前的轧制管温度为800℃~1000℃。
14.进一步地,步骤s4后还包括热处理步骤:对二次冷却管进行热处理,得到钢管,钢管壁厚s≥25mm,热处理包括正火、正火冷却和回火三个步骤,正火温度为1040℃~1080℃,温度误差为
±
10℃,正火的保温时间为smm
×
(2min/mm~3min/mm),最低保温时间为40min,回火温度为720℃~780℃,温度误差为
±
10℃,回火的保温时间为smm
×
(3min/mm~4min/mm),最低保温时间为60min。
15.进一步地,回火冷却的方式为回火空冷,和/或,s≤30mm时,正火冷却的方式为正火空冷,30mm<s≤60mm时,正火冷却的方式为正火喷雾冷却,s>60mm时,正火冷却的方式为正火喷淋冷却或直接淬火。
16.进一步地,正火的保温时间大于或等于40min,回火的保温时间大于或等于60min。
17.进一步地,轧制用管坯加热时的均热的温度为1200℃~1250℃,温度偏差为
±
15℃,均热的时间为1~3h。
18.进一步地,轧制具体为:将毛坯管插入带有润滑剂的芯棒,并在预定时间内移至周期式轧管机中,轧管的温度为950℃~1100℃。
19.进一步地,步骤s4中空冷的时间为2~4h。
20.进一步地,步骤s3中的冷却步骤后还包括二次加热步骤和定径步骤,二次加热的温度为950℃~1150℃。
21.应用本发明的技术方案,通过在轧制工序后增加冷却工序的方式消除p91/p92钢管中的混晶组织,并通过控制步骤s3中的冷却的速率将轧制管快速冷却至400℃~650℃,能够抑制奥氏体晶粒长大而促使其马氏体转变,从而细化马氏体晶粒,使钢管产品不产生混晶组织。相比于现有钢管的制备方法中通过增加等温退火工序消除混晶组织,本发明的技术方案耗时短,进而不会因增加冷却工序导致p91/p92钢管的制备效率大大降低,不影响p91/p92钢管短期大规模生产的需求,并且降低了生产成本。
附图说明
22.构成本发明的一部分的说明书附图用来提供对本发明的进一步理解,本发明的示意性实施例及其说明用于解释本发明,并不构成对本发明的不当限定。在附图中:
23.图1示出了本发明的实施例的p91/p92无缝钢管制备方法的流程图;
24.图2示出了p91钢管的cct曲线图;
25.图3示出了p92钢管的cct曲线图;
26.图4示出了本发明的实施例一中p91无缝钢管的金相组织图;
27.图5示出了本发明的实施例二中毛坯管的金相组织图;
28.图6示出了本发明的实施例二中一次冷却管的金相组织图;
29.图7示出了本发明的实施例二中p91无缝钢管的金相组织图;
30.图8示出了本发明的对比例一的一次冷却管的金相组织图;
31.图9示出了本发明的对比例二的钢管的金相组织图;
32.图10示出了本发明的对比例四的钢管的金相组织图。
具体实施方式
33.需要说明的是,在不冲突的情况下,本发明中的实施例及实施例中的特征可以相互组合。下面将参考附图并结合实施例来详细说明本发明。
34.需要说明的是,本发明的制备方法用于制备直径为325mm~720mm、壁厚为25mm~120mm的p91/p92无缝钢管,p91/p92钢的化学成分满足asmesa-335m高温铁素体合金负公称管中的p91/p92和en10216-2中的x10crmovnb9-1、x10crwmovnb9-2以及gb/t5310中的10cr9mo1vnbn和10crwmow2vnbn钢的要求。
35.需要说明的是,根据p91/p92钢管的化学成分和相关试验,通过热膨胀法可以测定p91/p92钢管的转变温度ac1和ac3点,如表1所示。根据化学成分和加热速率的变化,可得到其相应的cct曲线图,如图1和图2所示,可见两种钢的基本参数相差不大,可以当成同一类进行处理。
36.表1p91/p92钢的特征温度转变点
37.钢种ac1/℃ac3/℃ms/℃mf/℃p91800-830890-940400100p92800-835900-920400100
38.需要说明的是,p91/p92钢混晶的形成原因:根据钢的轧制理论,钢加热到高温奥氏体区后进行热变形,钢的组织随形变量、变形温度、应变速率等的不同,加工硬化和动态软化(动态回复和再结晶)同时进行。奥氏体再结晶就是在轧制过程和轧制后γ组织结构发生变化,γ晶粒尺寸取决于轧制温度和形变量,并且,在一定温度下,不论发生动态还是静态再结晶,都有一个临界变形量要求,温度越低所需的临界变形量越大。含不同成分钢的各温度点(如再结晶终止温度tr及ar3等)并不相同,通常含nb钢的γ再结晶区温度tr在1050℃以上。钢在高温奥氏体区变形时有三个不同的轧制变形温度段,即再结晶温度区,为tr以上、未再结晶温度区tr~ar3以及两相温度区,ar3以下。钢在再结晶区和未再结晶温度区轧制,再结晶的γ晶粒尺寸随着轧制变形量的增大而减小,并达到一个极限,如果变形量不能达到再结晶的临界变形量时,得到的是部分再结晶和未再结晶的混合组织,晶粒尺寸差别较大,这种组织在后续相变成马氏体组织后仍不均匀,晶粒尺寸相差较大,混晶严重;如果在多道次低温轧制时不能全部进行再结晶,则会在很多处出现比原始晶粒大几倍的巨大晶粒,这是由于轻微的变形在局部地方诱发晶界移动而发生的现象;这种现象就是混晶,混晶组织对材料性能有较多的不利影响。
39.为了得到p91钢的动态再结晶的高温流变应力数据,在gleeble-1500d热模拟试验机进行了相关试验并取得的p91钢高温流变应力数据,得到p91的动态所需再结晶激活能为543.52kj/mol。并且试验也证实p91钢在1050℃~ar3温度,且应变速率为2s-1
以下变形,处于未再结晶区。
40.由于9cr(p91/p92)钢加热到1230℃以上时易形成δ铁素体,所以在大口径厚壁钢管的轧制过程,一般钢坯的加热温度控制较低,在1230℃以下。经过管坯加热、均热、穿孔多个工序后进入皮尔格轧制时温度为在950℃~1100℃,而轧制完成温度一般也处于930℃~1080℃的范围时,应变速率约为1.5~2s-1
,并且由于皮尔格轧制的每道次变形量较小,变形量不能达到再结晶的临界变形量,所以轧后钢(轧制管)的奥氏体晶粒只能发生γ部分再结晶,部分的晶粒将保持不变,并且,轻微的变形也在局部地方诱发晶界移动在很多处出现比原始晶粒大几倍的巨大晶粒,形成了大小不一的混合奥氏体组织,在随后的空冷后转变成马氏体,马氏体组织保留了原始的大晶粒和小晶粒的混晶组织。
41.p91/p92钢的热加工制度,包括加热温度、形变量、形变速率、热加工温度和轧后冷却速率、终冷温度等,对加工后的组织有较大影响。并且,由于钢中含有较多的合金元素造成这种组织具有极强的组织遗传性,后续常规热处理很难消除组织遗传,最终造成产品晶粒粗大或混晶,不能满足gb/t5310-2017《高压锅炉用无缝钢管》标准中6.9条款晶粒度的要求:晶粒度级别≥4级,两个试样上晶粒度最大级别和最不级别差≤3级。
42.基于上述的分析,为了有效消除p91/p92无缝钢管中的混晶组织,本发明提供了一种p91/p92无缝钢管的制备方法,制备方法包括以下步骤:
43.s1,取管坯,对管坯进行一次加热、均热和穿孔,得到毛坯管;
44.s2,对毛坯管进行轧制,得到轧制管;
45.s3,将轧制管冷却至400℃~650℃,使形变奥氏体发生相变,得到一次冷却管,其中,冷却的速率为0.8℃/s~2.5℃/s;
46.s4,对一次冷却管进行空冷,得到二次冷却管。
47.在上述技术方案中,当步骤s3中的冷却速率为1℃/s时,观测p91钢的tem微观组织亚结构和析出物。可见,p91/p92钢在冷却后的板条马氏体片平直完整,马氏体相变首先以孪晶来协调应变,同时由于穿孔大变形使原始奥氏体组织大大细化,轧制使用的轧管变形累积使形变奥氏体进一步强化,故在孪晶生长的同时,基体中产生大量位错,因此,在相变过程中马氏体板条可通过位错滑移来提供塑性协调而继续生成,这样就形成了孪晶与高密度位错共存的特殊亚结构,细密分布的位错网络位于马氏体板条边缘,孪晶结构在马氏体板条中部可见。加快冷却(步骤s3中的冷却)后,可得到含有高密度位错、微细孪晶及纳米级碳化物的超细板条马氏体组织,这种组织类型将大大提高轧制p91/p92钢管的力学性能。因此,本方案选择将冷却速率限定在0.8℃/s~2.5℃/s的范围内。
48.步骤s3中的冷却终止温度为400℃~650℃。
49.在一个实施例中,步骤s3包括:将轧制管冷却至400℃~650℃,使形变奥氏体发生相变,得到一次冷却管,将一次冷却管直接进炉后,再进行二次加热、定径,得到定径管;步骤s4包括:对定径管进行空冷,得到二次冷却管。
50.在另一个实施例中,步骤s3包括:将轧制管冷却至400℃~650℃,使形变奥氏体发生相变,得到一次冷却管,将一次冷却管继续空冷或风冷后,再进行二次加热、定径,得到定径管;步骤s4包括:对定径管进行空冷,得到二次冷却管。
51.在上述两个实施例中,二次加热的温度为950℃~1150℃。二次加热步骤和定径步骤是在轧制管的几何尺寸无法满足成品要求时增加的,如果轧制管的几何尺寸满足成品要求,则不需要进行二次加热步骤和定径步骤。二次加热步骤具体为:将一次冷却管通过小冷
床运送至步进炉进行二次加热。定径步骤具体为:根据定径方管的几何尺寸要求,选用合适的机架个数和孔型进行热定径;由于钢管的壁厚较厚,并且p91/p92钢变形抗力大,定径变形量少,因此不会发生大的组织变形。
52.钢在热轧制变形时有三个不同的轧制变形温度段,其中含不同成分钢的各温度点(如再结晶终止温度tr及ar3等)并不相同。通常含nb钢的γ再结晶区温度tr在1050℃以上。
53.较快的冷却速率可以抑制奥氏体晶粒长大而促使其发生马氏体转变,从而使马氏体晶粒来不及长大。根据图2和图3可知,具体的冷却速率为0.6℃/s以上。
54.通过上述设置,可以利用特定的冷却速率通过冷却工序将轧制管快速冷却至400℃~650℃,能够利用较快的冷却速率抑制奥氏体晶粒长大而促使奥氏体晶粒马氏体转变,从而细化马氏体晶粒,使钢管产品不产生混晶组织。相比于现有钢管的制备方法中通过增加等温退火工序消除混晶组织,本发明的技术方案耗时短,进而不会因增加冷却工序导致p91/p92钢管的制备效率大大降低,不影响p91/p92钢管短期大规模生产的需求,同时降低生产成本。
55.本发明的一个实施例中,步骤s3中的冷却速率为0.8℃/s~2.0℃/s,优选为0.8℃/s~1.5℃/s。
56.在上述技术方案中,如果将冷却速率增加到2.5℃/s以上时,钢组织中会出现部分片状马氏体,使得淬火应力增大,以及塑性和韧性的下降,这会导致钢组织在淬火过程中的变形,甚至开裂。因此,优选将冷却速率控制在2.0℃/s以下。
57.本发明的一个实施例中,步骤s3中冷却的方式为喷水冷却或水雾冷却,冷却速率通过冷却介质的流量和压力控制,冷却的终止温度通过冷却的时间确定。
58.在上述技术方案中,冷却前的轧制工艺时间较长,为3min~6min,冷却的终止温度通过在线红外测温仪测量,通过调整用于冷却工艺的冷却装置的冷却区域长度和冷却时间能够确定冷却的终止温度。
59.本发明的一个实施例中,轧制前的毛坯管的温度为950℃~1100℃,冷却前的轧制管温度为800℃~1000℃。
60.在上述技术方案中,根据图1和图2中p91/p92钢cct曲线可知,当奥氏体在tr~ar3温度区以较快的冷却速率进行冷却时可以抑制奥氏体晶粒长大而促使其马氏体转变,从而细化马氏体晶粒并且不产生混晶组织,较快的冷却速率是指0.6℃/s以上,也就是说,在tr~ar3温度区,即800℃~1050℃的范围内开始冷却的效果最好。
61.本发明的一个实施例中,步骤s4后还包括热处理步骤:对二次冷却管进行热处理,得到钢管,钢管壁厚s≥25mm,热处理包括正火、正火冷却和回火三个步骤,正火温度为1040℃~1080℃,温度误差为
±
10℃,正火的保温时间为smm
×
(2min/mm~3min/mm),最低保温时间为40min,回火温度为720℃~780℃,温度误差为
±
10℃,回火的保温时间为smm
×
(3min/mm~4min/mm),最低保温时间为60min。
62.在上述技术方案中,正火温度优选为1060℃
±
10℃,回火温度优选为780℃
±
10℃。
63.本发明的一个实施例中,回火冷却的方式为回火空冷,和/或,s≤30mm时,正火冷却的方式为正火空冷,30mm<s≤60mm时,正火冷却的方式为正火喷雾冷却,s>60mm时,正火冷却的方式为正火喷淋冷却或直接淬火。
64.在上述技术方案中,根据钢管的不同壁厚使用不同的正火冷却方式来保证一定的冷却速率。
65.本发明的一个实施例中,正火的保温时间大于或等于40min,回火的保温时间大于或等于60min。
66.通过上述设置,保证钢管制作过程中的性能稳定性。
67.本发明的一个实施例中,均热的温度为1200℃~1250℃,温度偏差为
±
15℃,均热的时间为1.5~3h。
68.通过上述设置,一方面,满足钢的轧制变形要求;另一方面,使得终得到的钢管不产生δ铁素体。
69.本发明的一个实施例中,穿孔的温度为1150℃~1220℃,通过合理的穿孔工艺参数得到设定尺寸的毛坯管。
70.本发明的一个实施例中,轧制具体为:将毛坯管插入带有润滑剂的芯棒,并在预定时间内移至周期式轧管机中,轧管的温度为950℃~1100℃。
71.在上述技术方案中,周期式轧管机即为皮尔格轧管机,轧管即为皮尔格轧管,轧制的工艺参数主要包括轧管机孔型、芯棒直径、喂入量、回转角度和回转形成,根据实际需求设定对应的工艺参数,轧制出需求规格的轧制管。
72.本发明的一个实施例中,步骤s4中空冷的时间为2~4h。
73.在上述技术方案中,空冷在轧制后冷床的保温罩中进行,空冷起到去应力的作用。本发明的一个实施例中,在热处理步骤后还包括钢管矫直步骤、理化性能取样步骤、表面加工步骤、检验步骤和喷标涂漆步骤,表面加工步骤通过内外磨削工艺或内镗外扒工艺实现,具体根据不同需求选用不同的工艺;检验步骤具体为人工检验。
74.从以上的描述中,可以看出,本发明的上述的实施例实现了如下技术效果:本发明在轧制后采取了控制冷却工艺,即步骤s3中的冷却,解决了形变奥氏体组织异常长大问题,从而使轧制管的组织细小均匀,经正火和回火形成均匀的回火马氏体组织,消除了粗晶和混晶,满足gb/t5310《高压锅炉用无缝钢管》对这两个钢种的金相组织的要求。本发明相比于现有的钢管制备方法而言,节省了等温退火工序,得到了无粗晶和混晶的厚壁p91/p92大口径钢管,加快了生产周期、节约了生产成本。
75.实施例一:
76.以直径711mm,壁厚63mm的p91无缝钢管为例:
77.(1)管坯坯料的化学成分
78.表2本发明p91管坯坯料的化学成分,wt%
79.元素csimnpscunicrmop910.090.370.410.0120.0020.030.068.680.90元素valsnaspbsbbinbnp910.220.0180.0060.0130.0010.0050.0060.070.059
80.(2)p91无缝钢管的力学性能
81.表3拉伸性能
82.r
p0.2
(mpa)rm(mpa)a(%)59071421
58771722
83.表4硬度(从钢管内表面到外表面)
84.硬度(hbw)225,227,225,223,225,227
85.表5冲击性能
86.温度a
kv
(j)室温222,216,2260200,185,222-20160,162,146
87.(3)采用本方法生产的p91无缝钢管的显微组织如图3所示,该组织为单一的回火马氏体组织,晶粒度为7.5级。
88.实施例二:
89.以直径559mm,壁厚95mm的p91无缝钢管为例:
90.(1)穿孔:取直径为700mm的管坯,经过一次加热、均热后,在1230℃穿孔为直径610mm、壁厚140mm的毛坯管,对毛坯管取样进行金相测验,得到如图4所示的金相图,金相图显示为马氏体组织,晶粒度为3级,由此可知,毛坯管没有出现混晶组织;
91.(2)轧制:使用本发明s2的轧制步骤,得到轧制管;
92.(3)冷却:将轧制管通过水冷环,冷却的同时转动轧制管,使冷却均匀,将冷却速率控制在1.0℃/s,冷却至430℃结束,得到一次冷却管;冷却方式采用喷水冷却,并通过调整水的流量和压力将冷却速率控制在1.0℃/s;对一次冷却管取样进行金相检验,得到如图5所示的金相图,金相图显示晶粒度7.5级,无混晶;
93.(4)空冷:使用本发明s4的步骤;
94.(5)热处理:使用本发明的热处理步骤;
95.(6)使用本发明的二次加热步骤和定径步骤;
96.(7)使用本发明的钢管矫直步骤、理化性能取样步骤、表面加工步骤、检验步骤和喷标涂漆步骤,得到p91无缝钢管;对p91无缝钢管取样并进行金相检验,得到如图6所示的金相图,金相图显示晶粒度6级,均匀无极差。
97.对比例一:
98.使用本发明的步骤s1至步骤s3制备得到一次冷却管,其中,冷却的速率不在本发明的范围内,冷却具体为:对轧制管进行空冷,冷却速率为0.1℃/s~0.4℃/s,对一次冷却管取样并进行金相检验,得到如图7所示的金相图,金相图显示部分晶粒出现异常长大的情况,晶粒度最粗为00级、细的6级,混晶严重;
99.对比例二:
100.使用本发明的步骤s1、步骤s2和步骤s4制备得到钢管,即不进行冷却工序得到钢管,对钢管取样并进行金相检验,得到如图8所示的金相图,金相图显示晶粒度最粗为0级、细的6级,混晶严重。
101.对比例三:
102.使用本发明的步骤s1、步骤s2和步骤s4,且在步骤s2和步骤s4之间增加冷却步骤制备得到钢管,其中,冷却步骤具体为:将轧制管冷却至400℃~650℃,使形变奥氏体发生
相变,得到一次冷却管,其中冷却速率为0.3℃/s~0.5℃/s,得到一次冷却管;
103.对比例四:
104.使用现有技术中的制备方法得到钢管,即在热处理前增加一道等温退火作为预备热处理工序,具体为:将钢管加热到970℃保温,得到奥氏体化组织,然后缓慢降温至750℃等温(等温时间5~6min/mm)。得到如图10所示的金相图,金相图显示晶粒度为6~6.5级
105.本发明与对比例三和对比例四对应修改各项参数后的晶粒度对比情况如下表所示:
106.表6本发明与对比例三和对比例四对应修改各项参数后的晶粒度对比表
[0107][0108][0109]
显然,上述所描述的实施例仅仅是本发明一部分的实施例,而不是全部的实施例。基于本发明中的实施例,本领域普通技术人员在没有做出创造性劳动前提下所获得的所有其他实施例,都应当属于本发明保护的范围。
[0110]
需要注意的是,这里所使用的术语仅是为了描述具体实施方式,而非意图限制根据本技术的示例性实施方式。如在这里所使用的,除非上下文另外明确指出,否则单数形式也意图包括复数形式,此外,还应当理解的是,当在本说明书中使用术语“包含”和/或“包括”时,其指明存在特征、步骤、工作、器件、组件和/或它们的组合。
[0111]
以上所述仅为本发明的优选实施例而已,并不用于限制本发明,对于本领域的技术人员来说,本发明可以有各种更改和变化。凡在本发明的精神和原则之内,所作的任何修改、等同替换、改进等,均应包含在本发明的保护范围之内。