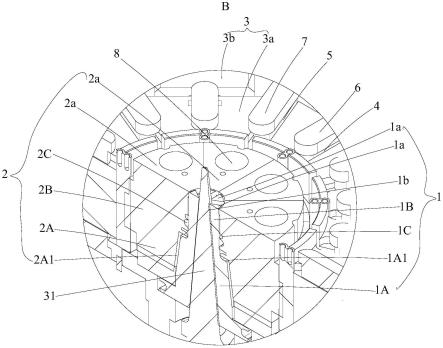
1.本实用新型涉及管端成型设备领域,具体涉及一种管件管端成型用的夹持机构。
背景技术:2.卡压式管件是以带有特种密封圈的承口管件连接管道,用专用工具压紧管口而起密封和固定作用的一种连接件。在卡压式管件加工完成后,还需对其管端进行进一步成型加工。
3.目前,卡压式管件的管端成型设备,其通常包括外模和内模,外模设于管件管端外周,并通过夹紧板向内夹紧,内模沿着管端的长度方向伸入管端并绕自对应管端的轴心线同步转动,管件的管端随之形变成型。然而,在实际加工过程中,上述的管端成型设备存在以下问题:(1)加工时内模在管端内不停转动,外模需要与管件管端外周具有一定距离以供管端外扩,两者均无法对管件进行有效固定,需要人工或机械手全程夹持管件,极大的增加了人力物力成本,同时若人工或机械手夹持不牢靠还会影响管件管端的成型质量;(2)外模通过夹紧板向内夹紧,由于夹紧板的尺寸固定,导致外模只能适配固定尺寸的管件,在加工不同管径的管件时需要配备不同尺寸的模具,这进一步的增加了成本。
技术实现要素:4.本实用新型的目的是克服现有技术的不足,提供一种管件管端成型用的夹持机构。
5.为达到上述目的,本实用新型采用的技术方案是:
6.一种管件管端成型用的夹持机构,安装于管端成型机的机架上,其包括用于插入所述管件管端的内模、设于所述管件管端外周的外模,所述内模包括多个绕着圆周方向排布且能够沿着靠近或远离环绕中心的方向运动的内模单体,所述外模包括多个绕着所述内模的周向排布且能够沿着靠近或远离所述内模的方向运动的外模单体,所述夹持机构还包括多个分别用于一一对应的驱动所述的多个外模单体运动的驱动组件。
7.优选地,所述管端成型机具有锥状的芯轴,所述的多个内模单体之间围合成供所述芯轴伸入并同步转动的芯槽。
8.进一步优选地,所述内模包括内模座、形成于所述内模座端部的用于插入所述管件管端的内模头,所述内模座、所述内模头的排布方向与所述管件管端的长度方向一致,所述芯槽在所述内模座远离所述内模头的一端面上形成有供所述芯轴穿入的第一槽口、在所述内模头远离所述内模座的一端面上形成有供所述芯轴穿出的第二槽口,所述芯槽沿着所述第一槽口至所述第二槽口的方向径向减小。
9.更进一步优选地,所述内模座成圆台状且沿着所述第一槽口至所述第二槽口的方向径向内缩;所述内模头成圆柱形且与所述管件管端的内腔相匹配。
10.更进一步优选地,所述内模座靠近所述内模头的一端形成用于抵住所述管件管端的限位面,所述限位面的直径大于所述管件管端的直径。
11.更进一步优选地,所述外模包括外模座、形成于所述外模座端部的外模环,所述外模座中开设有用于容置所述内模座的模腔,所述外模环位于所述管件管端外周。
12.更进一步优选地,所述内模还包括环绕于所述内模头的外周侧部的凸起,所述外模还包括开设于所述外模环的内环面上且与所述凸起相匹配的凹槽。
13.优选地,所述驱动组件包括与对应所述外模单体相连接且沿着靠近或远离所述内模的方向可滑动的设置的滑块、用于驱动所述滑块滑动的动力模块。
14.进一步优选地,所述滑块上沿其自身滑动方向开设有第一导向槽,相邻的两个所述滑块之间形成有第二导向槽,所述夹持机构还包括设于所述机架上的第一导向块和第二导向块,所述第一导向块卡嵌于所述第一导向槽中,所述第二导向块卡嵌于所述第二导向槽中。
15.优选地,所述外模还包括多个分别对应的开设于所述的多个外模单体上的通孔,所述通孔沿着垂直所述外模单体的运动方向贯穿所述外模单体。
16.由于上述技术方案的运用,本实用新型与现有技术相比具有下列优点:
17.(1)本实用新型的内模仅被赋予扩口成型功能,其插入管件管端后不会转动,能够起到固定管件的作用,无需人工夹持管件或另外配备机械手,不仅节约了成本,而且避免了夹持不牢靠而影响管件管端的成型质量;
18.(2)将外模分隔为多个外模单体,同时通过多个驱动组件分别驱动多个外模单体运动,使得本实用新型的外模能够适配多种不同尺寸的管件,节约了成本。
附图说明
19.附图1为本实用新型的具体实施例中的夹持机构的俯视示意图;
20.附图2为附图1中去除固定板后的a-a截面示意图;
21.附图3为图2的b处放大示意图。
22.图中:1、内模;1a、内模单体;1b、芯槽;1a、内模座;1a1、限位面;1b、内模头;1c、凸起;2、外模;2a、外模单体;2a、外模座;2a1、模腔;2b、外模环;2c、凹槽;3、驱动组件;3a、滑块;3b、动力模块;
23.4、第一导向槽;5、第二导向槽;6、第一导向块;7、第二导向块;8、通孔;9、固定板;10、液压控制箱;
24.30、机架;31、芯轴。
具体实施方式
25.下面结合附图来对本实用新型的技术方案作进一步的阐述。
26.本实用新型涉及对管件的管端成型设备的改进,提出了一种管件管端成型用的夹持机构,该夹持机构的内模1能够起到固定管件的作用,无需人工夹持管件或另外配备机械手,不仅节约了成本,而且避免了夹持不牢靠而影响管件管端的成型质量;同时将外模2分隔为多个外模单体2a,同时通过多个驱动组件3分别驱动多个外模单体2a运动,使得外模2能够适配多种不同尺寸的管件,节约了成本。
27.参见图1-3所示,其中示出了一种管件管端成型用的夹持机构,安装于管端成型机的机架30上,其包括用于插入管件管端的内模1、设于管件管端外周的外模2,内模1包括多
个绕着圆周方向排布且能够沿着靠近或远离环绕中心的方向运动的内模单体1a,外模2包括多个绕着内模1的周向排布且能够沿着靠近或远离内模1的方向运动的外模单体2a,夹持机构还包括多个分别用于一一对应的驱动多个外模单体2a运动的驱动组件3。
28.如此一来,加工时,只需将内模11插入管件管端即能够实现管件的固定,无需再另外设置机械手;同时,根据管件管端的外扩尺寸需要设计外模2与管件管端之间的距离,并通过驱动组件3驱动外模单体2a运动到位,使得外模2能够适配多种不同尺寸的管件。
29.在本实施例中,管端成型机具有锥状的芯轴31,且锥状的芯轴31的直径沿着远离内模1的方向逐渐增大,多个内模单体1a之间围合成供芯轴31伸入并同步转动的芯槽1b。
30.进一步地,内模1包括内模座1a、形成于内模座1a端部的用于插入管件管端的内模头1b,内模座1a、内模头1b的排布方向与管件管端的长度方向一致,芯槽1b在内模座1a远离内模头1b的一端面上形成有供芯轴31穿入的第一槽口、在内模头1b远离内模座1a的一端面上形成有供芯轴31穿出的第二槽口,芯槽1b沿着第一槽口至第二槽口的方向径向减小。如此,在内模1插入管件管端后,通过芯轴31插入芯槽1b并同步转动实现多个内模单体1a的运动与管件管端的外扩成型,内模1和芯轴31各司其职,不仅实现了管件的夹持固定,而且不会影响管件的成型质量。
31.在本实施例中,内模座1a成圆台状且沿着第一槽口至第二槽口的方向径向内缩,内模头1b成圆柱形且与管件管端的内腔相匹配。内模座1a靠近内模头1b的一端形成用于抵住管件管端的限位面1a1,限位面1a1的直径大于管件管端的直径。
32.外模2包括外模座2a、形成于外模座2a端部的外模环2b,外模座2a中开设有用于容置内模座1a的模腔2a1,外模环2b位于管件管端外周。其中模腔2a1的设置为内模座1a的向外运动提供了空间余量。
33.进一步地,内模1还包括环绕于内模头1b的外周侧部的凸起1c,外模2还包括开设于外模环2b的内环面上且与凸起1c相匹配的凹槽2c。通过凸起1c和凹槽2c的设置,在多个内模单体1a向外运动的过程中能够在卡压管件管端上形成一凸环。这里,凸起1c和凹槽2c是为了形成凸环而设计的配合件,当然,本领域技术人员也可根据卡压管件管端的连接需要设计其他的配合件,以加工其他形状的结构。
34.在本实施例中,驱动组件3包括与对应外模单体2a相连接且沿着靠近或远离内模1的方向可滑动的设置的滑块3a、用于驱动滑块3a滑动的动力模块3b。这里的动力模块3b为油缸。本例中的夹持机构还包括用于控制油缸的液压控制箱10。
35.作为优选地方案,滑块3a上沿其自身滑动方向开设有第一导向槽4,相邻的两个滑块3a之间形成有第二导向槽5,夹持机构还包括设于机架30上的第一导向块6和第二导向块7,第一导向块6卡嵌于第一导向槽4中,第二导向块7卡嵌于第二导向槽5中。本例中,机架30上固设有一圆形的固定板9,第一导向块6和第二导向块7均卡嵌于固定板9中且两者绕着固定板9的周向间隔错位排布。这样一来,在多个滑块3a的滑动过程中,通过第一导向槽4与第一导向块6、及第二导向槽5与第二导向块7的配合,能够保证滑块3a的滑动方向,避免滑块3a跑偏,保证了夹持效果。
36.在本实施例中,外模2还包括多个分别对应的开设于多个外模单体2a上的通孔8,通孔8沿着垂直外模单体2a的运动方向贯穿外模单体2a。通孔8的设置能够减轻外模单体2a的重量,一方面节约了成本,另一方面也减轻了驱动组件的驱动负担。
37.上述实施例只为说明本实用新型的技术构思及特点,其目的在于让熟悉此项技术的人士能够了解本实用新型的内容并据以实施,并不能以此限制本实用新型的保护范围。凡根据本实用新型精神实质所作的等效变化或修饰,都应涵盖在本实用新型的保护范围之内。