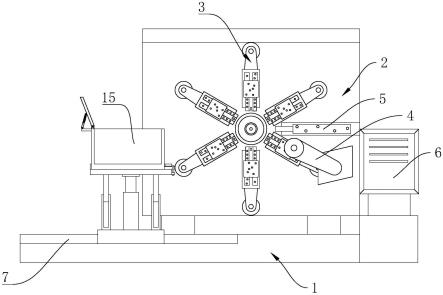
1.本实用新型属于弹簧加工技术领域,涉及一种大弹力弹簧强压形变机构。
背景技术:2.弹簧是一种利用弹性来工作的机械零件。用弹性材料制成的零件在外力作用下发生形变,除去外力后又恢复原状。亦作“弹簧”。一般用弹簧钢制成。弹簧的种类复杂多样,按形状分,主要有螺旋弹簧、涡卷弹簧、板弹簧、异型弹簧等。
3.按受力性质,弹簧可分为拉伸弹簧、压缩弹簧、扭转弹簧和弯曲弹簧,按形状可分为碟形弹簧、环形弹簧、板弹簧、螺旋弹簧、截锥涡卷弹簧以及扭杆弹簧等,按制作过程可以分为冷卷弹簧和热卷弹簧。普通圆柱弹簧由于制造简单,且可根据受载情况制成各种型式,结构简单,故应用最广。弹簧的制造材料一般来说应具有高的弹性极限、疲劳极限、冲击韧性及良好的热处理性能等,常用的有碳素弹簧钢、合金弹簧钢、不锈弹簧钢以及铜合金、镍合金和橡胶等。弹簧的制造方法有冷卷法和热卷法。弹簧丝直径小于8毫米的一般用冷卷法,大于8毫米的用热卷法。有些弹簧在制成后还要进行强压或喷丸处理,可提高弹簧的承载能力。
4.现有的大弹力弹簧在进行强压形变加工后,会在切割冲头的作用下直接推动至收集箱处被收集储存,但是当加工的弹簧质量过大或过轻时,由于放置收集箱的地方固定,进而使得弹簧再次被切割冲头切割推动时,就很难精准的落入到收集箱内部被收集处理,从而给用户的弹簧收集带来了一定的麻烦。
技术实现要素:5.本实用新型的目的是针对上述问题,提供一种大弹力弹簧强压形变机构。
6.为达到上述目的,本实用新型采用了下列技术方案:
7.一种大弹力弹簧强压形变机构,包括支撑底座,所述支撑底座上设置有固定侧板,所述固定侧板上设置有弹簧强压机构,所述固定侧板上还设置有弹簧弯折装置和切割冲击装置,所述支撑底座的侧边设置有用于智能控制的智能控制箱,所述支撑底座的顶端面开设有底端滑槽,所述底端滑槽上滑动设置有驱动滑块,所述驱动滑块的上方设置有顶端托板,所述顶端托板的底端通过设置在所述驱动滑块顶端的升降伸缩杆支撑,所述升降伸缩杆的侧边对称设置有两个侧边支撑杆。
8.在上述的大弹力弹簧强压形变机构中,所述侧边支撑杆的底端与所述驱动滑块相连,所述侧边支撑杆的顶端开设有中部滑槽。
9.在上述的大弹力弹簧强压形变机构中,所述中部滑槽的内部滑动插设有稳定连接杆,所述稳定连接杆穿出所述中部滑槽与所述顶端托板的底端相连。
10.在上述的大弹力弹簧强压形变机构中,所述顶端托板的顶端开设有顶端安装槽,所述顶端安装槽的内部滑动设置有弹簧收集仓。
11.在上述的大弹力弹簧强压形变机构中,所述顶端安装槽的内壁上开设有内壁通
孔,所述内壁通孔的内部穿插有第一固定插杆。
12.在上述的大弹力弹簧强压形变机构中,所述第一固定插杆与所述弹簧收集仓的底端相连,所述顶端托板的侧边设置有固定连接块。
13.在上述的大弹力弹簧强压形变机构中,所述第一固定插杆与所述顶端托板之间通过插设在所述第一固定插杆端部的第二固定插杆固定相连,所述第二固定插杆的底端穿过所述固定连接块。
14.在上述的大弹力弹簧强压形变机构中,所述顶端托板顶端的侧边铰接设置有弹簧阻挡板,所述顶端托板顶端的侧边设置有支撑连接板。
15.在上述的大弹力弹簧强压形变机构中,所述支撑连接板上铰接设置有支撑铰接杆,所述支撑铰接杆的杆身上套设有缓冲弹簧。
16.在上述的大弹力弹簧强压形变机构中,所述缓冲弹簧的一端与所述弹簧阻挡板相连,所述缓冲弹簧的另一端与所述支撑铰接杆杆身相连。
17.与现有的技术相比,本实用新型的优点在于:
18.1、本实用新型通过在弹簧强压机构的侧边设置有弹簧收集仓,通过设置在弹簧收集仓底端的升降伸缩杆能够将弹簧收集仓进行抬高,驱动滑块能够将弹簧收集仓的左右位置进行调节,从而使得弹簧收集仓能够被精准的设置在加工弹簧掉落的位置,进而对弹簧进行更加的收集,避免因为不同质量的弹簧飞出的距离不同而难以收集的问题,使得弹簧的收集更加的方便快捷。
19.2、本实用新型通过在弹簧收集仓顶端的侧边设置的弹簧阻挡板,弹簧阻挡板在缓冲弹簧的弹性支撑下,能够将弹簧阻挡板对飞来的弹簧进行撞击力的缓冲,使其更好的落入到弹簧收集仓内部被储存。
20.本实用新型的其它优点、目标和特征将部分通过下面的说明体现,部分还将通过对本实用新型的研究和实践而为本领域的技术人员所理解。
附图说明
21.图1是本实用新型的主视示意图。
22.图2是本实用新型中图1中弹簧收集仓的剖面示意图。
23.图3是本实用新型中图2中顶端安装槽的放大示意图。
24.图4是本实用新型中图2中支撑铰接杆的放大示意图。
25.图中:支撑底座1、固定侧板2、弹簧强压机构3、弹簧弯折装置4、切割冲击装置5、智能控制箱6、底端滑槽7、驱动滑块 8、顶端托板9、升降伸缩杆10、侧边支撑杆11、中部滑槽12、稳定连接杆13、顶端安装槽14、弹簧收集仓15、内壁通孔16、第一固定插杆17、固定连接块18、第二固定插杆19、弹簧阻挡板20、支撑连接板21、支撑铰接杆22、缓冲弹簧23。
具体实施方式
26.下面结合附图对本实用新型进行进一步说明。
27.如图1-4所示,一种大弹力弹簧强压形变机构,包括支撑底座1,支撑底座1上设置有固定侧板2,固定侧板2上设置有弹簧强压机构3,固定侧板2上还设置有弹簧弯折装置4和切割冲击装置5,支撑底座1的侧边设置有用于智能控制的智能控制箱6。
28.在本实施例中,由于现有的大弹力弹簧在进行强压形变加工后,会在切割冲头的作用下直接推动至收集箱处被收集储存,但是当加工的弹簧质量过大或过轻时,由于放置收集箱的地方固定,进而使得弹簧再次被切割冲头切割推动时,就很难精准的落入到收集箱内部被收集处理,从而给用户的弹簧收集带来了一定的麻烦。
29.在对弹簧进行加工时,通过智能控制箱6对弹簧强压机构3 和弹簧弯折装置4进行输入指令操控,使得从弹簧强压机构3中部伸出的弹簧铁条在弹簧强压机构3和弹簧弯折装置4的共同扭转下得以加工成弹簧形状,在通过切割冲击装置5对弹簧进行切割冲击,从而使得在弹簧强压机构3表面被加工的弹簧移走。
30.结合图1、图4所示,支撑底座1的顶端面开设有底端滑槽7,底端滑槽7上滑动设置有驱动滑块8,驱动滑块8的上方设置有顶端托板9,顶端托板9的底端通过设置在驱动滑块8顶端的升降伸缩杆10支撑,升降伸缩杆10的侧边对称设置有两个侧边支撑杆11,侧边支撑杆11的底端与驱动滑块8相连,侧边支撑杆 11的顶端开设有中部滑槽12,中部滑槽12的内部滑动插设有稳定连接杆13,稳定连接杆13穿出中部滑槽12与顶端托板9的底端相连。
31.在本实施方式中,当用户需要根据加工的不同的质量的弹簧来对收集箱进行调整时,用户可通过滑动驱动滑块8,使得驱动滑块8在底端滑槽7的内部左右滑动,从而来调控位于顶端托板 9上的收集箱与弹簧掉落位置的距离。
32.再通过升降伸缩杆10对顶端托板9的高度进行一定的调节,使得升降伸缩杆10对顶端托板9的底端进行顶起,使得顶端托板 9上的收集箱能够升高到合适的收集弹簧高度,进而使得弹簧在掉落时,恰好落在收集箱内部,不需要用户来回对收集箱进行挪动,更加方便用户的操作。
33.结合图1、图4所示,在本实施方式中,顶端托板9的顶端开设有顶端安装槽14,顶端安装槽14的内部滑动设置有弹簧收集仓15,顶端安装槽14的内壁上开设有内壁通孔16,内壁通孔16的内部穿插有第一固定插杆17,第一固定插杆17与弹簧收集仓15的底端相连,顶端托板9的侧边设置有固定连接块18,第一固定插杆17与顶端托板9之间通过插设在第一固定插杆17端部的第二固定插杆19固定相连,第二固定插杆19的底端穿过固定连接块18。
34.在本实施方式中,为了使得弹簧收集箱的安装更加简洁快速,通过在顶端托板9的顶端开设有顶端安装槽14,将顶端安装槽14 的内部滑动设置有弹簧收集仓15,通过弹簧收集仓15来对加工后的弹簧进行收集,且为了使得弹簧收集仓15在顶端托板9的顶端更加的固定。
35.通过在弹簧收集仓15的侧边设置有第一固定插杆17,第一固定插杆17能够插入到内壁通孔16内部,在通过对第一固定插杆 17的端部插设上第二固定插杆19,使得第二固定插杆19的底端插设到固定连接块18内部,从而在第二固定插杆19对第一固定插杆17的固定作用下,使得弹簧收集仓15能够稳定的固定在顶端安装槽14的内部。
36.结合图1、图4所示,在本实施方式中,顶端托板9顶端的侧边铰接设置有弹簧阻挡板20,顶端托板9顶端的侧边设置有支撑连接板21,支撑连接板21上铰接设置有支撑铰接杆22,支撑铰接杆22的杆身上套设有缓冲弹簧23,缓冲弹簧23的一端与弹簧阻挡板20相连,缓冲弹簧23的另一端与支撑铰接杆22杆身相连。
37.在本实施例中,当加工后的弹簧经过切割冲击装置5的切割冲击之后,会飞出短暂的距离,且通过对设置在顶端托板9顶端上弹簧收集仓15距离的调节,使得弹簧收集仓15的
位置正好位于弹簧飞出掉落的位置,进而使得弹簧的收集更加方便,还通过在弹簧收集仓15顶端的侧边铰接设置的弹簧阻挡板20,通过在弹簧阻挡板20的侧边设置有支撑铰接杆22。
38.通过在支撑铰接杆22上设置的缓冲弹簧23与弹簧阻挡板20 的侧面相连,进而对弹簧阻挡板20进行弹性支撑,使一些受到冲击力过大的成型弹簧能够在弹簧阻挡板20的阻挡作用下进入到弹簧收集仓15内部,从而避免弹簧掉落到地面上散乱分布,更加方便人们对于弹簧的收集储存工作的展开。
39.本实用新型的工作原理是:
40.在弹簧加工前,用户需要通过推动驱动滑块8,使得驱动滑块8在支撑底座1上的底端滑槽7内部滑动,进而滑动到弹簧掉落位置的下方,在通过启动升降伸缩杆10,使得升降伸缩杆10 能够进行短距离的伸长,从而使与升降伸缩杆10顶端相连的顶端托板9能够得到一定的升高,进而将放置在顶端托板9顶端的弹簧收集仓15能够升高到指定的弹簧收集位置。
41.接着,通过将弹簧收集仓15滑动插设在顶端安装槽14内部,将弹簧收集仓15端部的第一固定插杆17穿出内壁通孔16,在通过对第一固定插杆17的端部插设上第二固定插杆19,使得第二固定插杆19的底端穿出固定连接块18,进而在第二固定插杆19 的插设下对第一固定插杆17进行固定,使得弹簧收集仓15能够稳定牢固的固定在顶端托板9上。
42.最后,当加工后的弹簧经过切割冲击装置5的切割冲击之后,会飞出短暂的距离,且通过对设置在顶端托板9顶端上弹簧收集仓15距离的调节,使得弹簧收集仓15的位置正好位于弹簧飞出掉落的位置,进而使得弹簧的收集更加方便,还通过在弹簧收集仓15顶端的侧边铰接设置的弹簧阻挡板20。
43.通过在弹簧阻挡板20的侧边设置有支撑铰接杆22,通过在支撑铰接杆22上设置的缓冲弹簧23与弹簧阻挡板20的侧面相连,进而对弹簧阻挡板20进行弹性支撑,使一些受到冲击力过大的成型弹簧能够在弹簧阻挡板20的阻挡作用下进入到弹簧收集仓15内部,从而避免弹簧掉落到地面上散乱分布,更加方便人们对于弹簧的收集储存工作的展开。
44.本文中所描述的具体实施例仅仅是对本实用新型精神作举例说明。本实用新型所属技术领域的技术人员可以对所描述的具体实施例做各种各样的修改或补充或采用类似的方式替代,但并不会偏离本实用新型的精神。
45.尽管本文较多地使用支撑底座1、固定侧板2、弹簧强压机构 3、弹簧弯折装置4、切割冲击装置5、智能控制箱6、底端滑槽7、驱动滑块8、顶端托板9、升降伸缩杆10、侧边支撑杆11、中部滑槽12、稳定连接杆13、顶端安装槽14、弹簧收集仓15、内壁通孔16、第一固定插杆17、固定连接块18、第二固定插杆19、弹簧阻挡板20、支撑连接板21、支撑铰接杆22、缓冲弹簧23等术语,但并不排除使用其它术语的可能性。使用这些术语仅仅是为了更方便地描述和解释本实用新型的本质,把它们解释成任何一种附加的限制都是与本实用新型精神相违背的。