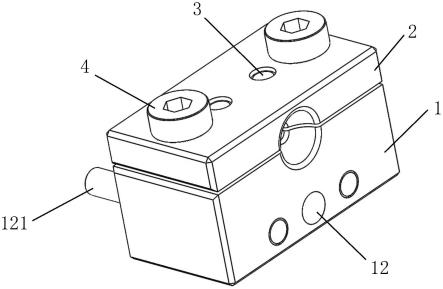
1.本实用新型涉及锻打模具领域,更具体地,涉及一种分体式锻打模具。
背景技术:2.随着模具行业的发展、科技的进步,锻打类产品日益增多,要求产品做到无异物、油污、飞边等锻打缺陷的同时,也要求尺寸上的超精准、生产过程的稳定性,对于锻打模具的设计及制造是不小的挑战。模具结构是保证产品质量的重要组成部分,其设计的好坏会影响模具开模后产品的品质。
3.在现有的技术中,生产此类锻打模具通常做法是使用整体钢材,制作成镂空形式,利用金属镂空口的弹性变形完成往复运动,实现制作过程。在产品连续生产的过程中,一旦金属因为疲劳强度问题发生断裂,产品即已经发生损坏,且在连续生产过程中不易发现模具损坏,对连续生产的产品造成大批不良。因此,研发一种可以连续稳定生产的锻打模具是个亟待解决的问题。
4.公开于本实用新型背景部分的信息仅仅旨在增加对本实用新型的总体背景的理解,而不应当被视为承认或以任何形式暗示该信息构成已为本领域一般技术人员所公知的现有技术。
技术实现要素:5.本实用新型的目的是提供一种锻打模具,其能够克服现有技术的上述缺点。
6.为达上述目的,本实用新型提供一种锻打模具,包括:下锻打部件、上锻打部件、成对的引导组件以及成对的复位组件,其中,下锻打部件固定至锻打机,并且所述下锻打部件的顶面的中部设有第一锻打部;上锻打部件能够上下移动地安装至所述下锻打部件,并且所述上锻打部件的底面的中部设有与所述第一锻打部相对应的第二锻打部;成对的引导组件分别设置在第一锻打部和第二锻打部的两侧,以引导上锻打部件的上下移动;成对的复位组件分别设置在第一锻打部和第二锻打部的两侧,以使向下移动后的上锻打部件复位至最大向上移动位置。
7.前述的锻打模具,其中,所述复位组件位于所述引导组件的外侧。
8.前述的锻打模具,其中,所述复位组件的每一个包括:连接孔、第一容纳孔、第二容纳孔、连通孔、复位弹簧以及限位螺钉,连接孔设置在所述下锻打部件的下部;第一容纳孔设置在所述连接孔的上方且与连接孔成阶梯形式,并且所述第一容纳孔的上端与下锻打部件的顶面平齐;第二容纳孔设置在所述上锻打部件的下部并与所述第一容纳孔相对应;连通孔设置在所述第二容纳孔的上方,所述连通孔与所述第二容纳孔成阶梯形式且共同贯穿所述上锻打部件;复位弹簧位于第一容纳孔和第二容纳孔中;限位螺钉穿过所述连通孔以及位于第一容纳孔和第二容纳孔中的所述复位弹簧而与所述连接孔接合,以使得上锻打部件和下锻打部件之间具有预定间隙。
9.前述的锻打模具,其中,所述第一容纳孔的内壁表面与所述复位弹簧的外周表面
之间隔开预定距离a,所述第二容纳孔的内壁表面与所述复位弹簧的外周表面之间隔开预定距离b,其中a>0,b≥0。
10.前述的锻打模具,其中,所述引导组件的每一个包括:引导杆和引导孔,引导杆设置在所述下锻打部件中;引导孔设置在所述上锻打部件中,并使得所述引导杆插入到所述引导孔中。
11.前述的锻打模具,其中,所述引导组件的每一个进一步包括安装孔,所述安装孔设置在所述下锻打部件中并与所述引导孔相对应,所述引导杆与安装孔之间为过盈配合。
12.前述的锻打模具,其中,所述引导杆的位于所述上锻打部件中的部分的外周表面设置有凹槽。
13.前述的锻打模具,其中,所述第一锻打部和所述第二锻打部共同形成锻打通道,所述锻打通道为平截圆锥体结构,并且锻打通道的前部的直径大于后部的直径。
14.前述的锻打模具,其中,进一步包括扩大部,其设置在所述锻打通道的前部。
15.前述的锻打模具,其中,所述下锻打部件进一步包括多个穿孔,通过所述穿孔将下锻打部件固定至所述锻打机。
16.本实用新型的有益效果为:本实用新型的结构在限位螺钉及复位弹簧的共同作用下促使锻打过程中锻打模具往复运动且实现位置固定;结构设计新颖巧妙,改进锻打模具行业以往固有的撞针使用金属弹性实现往复运动的原有设计理念,避免由于连续生产使金属疲劳的断裂而产生的弊端。
附图说明
17.图1为本实用新型示例性实施方案的锻打模具的立体示意图。
18.图2为本实用新型示例性实施方案的锻打模具的分解示意图。
19.图3为本实用新型示例性实施方案的锻打模具的俯视示意图。
20.图4为本实用新型示例性实施方案的锻打模具的a-a截面图。
21.图5为本实用新型示例性实施方案的锻打模具的b-b截面图。
22.附图标记说明:
[0023]1ꢀꢀꢀꢀꢀꢀꢀꢀꢀꢀ
下锻打部件
[0024]2ꢀꢀꢀꢀꢀꢀꢀꢀꢀꢀ
上锻打部件
[0025]3ꢀꢀꢀꢀꢀꢀꢀꢀꢀꢀ
引导组件
[0026]4ꢀꢀꢀꢀꢀꢀꢀꢀꢀꢀ
复位组件
[0027]
11
ꢀꢀꢀꢀꢀꢀꢀꢀꢀ
第一锻打部
[0028]
21
ꢀꢀꢀꢀꢀꢀꢀꢀꢀ
第二锻打部
[0029]
31
ꢀꢀꢀꢀꢀꢀꢀꢀꢀ
引导杆
[0030]
32
ꢀꢀꢀꢀꢀꢀꢀꢀꢀ
引导孔
[0031]
33
ꢀꢀꢀꢀꢀꢀꢀꢀꢀ
安装孔
[0032]
34
ꢀꢀꢀꢀꢀꢀꢀꢀꢀ
凹槽
[0033]
41
ꢀꢀꢀꢀꢀꢀꢀꢀꢀ
连接孔
[0034]
42
ꢀꢀꢀꢀꢀꢀꢀꢀꢀ
第一容纳孔
[0035]
44
ꢀꢀꢀꢀꢀꢀꢀꢀꢀ
第二容纳孔
[0036]
45
ꢀꢀꢀꢀꢀꢀꢀꢀꢀ
连通孔
[0037]
43
ꢀꢀꢀꢀꢀꢀꢀꢀꢀ
复位弹簧
[0038]
46
ꢀꢀꢀꢀꢀꢀꢀꢀꢀ
限位螺钉
[0039]
12
ꢀꢀꢀꢀꢀꢀꢀꢀꢀ
穿孔
[0040]
111
ꢀꢀꢀꢀꢀꢀꢀꢀ
第一扩大部分
[0041]
121
ꢀꢀꢀꢀꢀꢀꢀꢀ
定位导柱
[0042]
211
ꢀꢀꢀꢀꢀꢀꢀꢀ
第二扩大部分。
[0043]
应当理解的是,附图并非按比例地绘制,而是展示了稍微简化后呈现的说明本实用新型的基本原理的各种特征。在本实用新型的附图中,相同的附图标记表示本实用新型的相同的或等同的部分。
具体实施方式
[0044]
下面将详细地参考本实用新型的各种实施方案,这些实施方案的示例显示在附图中并且描述如下。尽管将结合本实用新型的示例性实施方案来描述本实用新型,但是将理解的是,本说明书并非旨在将本实用新型限制于那些示例性实施方案。正相反,本实用新型旨在不但覆盖本实用新型的示例性实施方案,而且覆盖包括在如所附权利要求所定义的本实用新型的精神和范围之内的各种替代形式、修改形式、等效形式以及其它实施方案。
[0045]
下文中,本实用新型的各种示例性实施方案将参考附图更具体地描述。
[0046]
参见图1至图5所示,本实用新型涉及一种锻打模具,包括:下锻打部件1、上锻打部件2、成对的引导组件3以及成对的复位组件4,其中,下锻打部件1固定至锻打机(未示出),并且下锻打部件1的顶面的中部设有第一锻打部11;上锻打部件2能够上下移动地安装至下锻打部件1,并且上锻打部件2的底面的中部设有与第一锻打部11相对应的第二锻打部21;成对的引导组件3分别设置在第一锻打部11和第二锻打部21的两侧,以引导上锻打部件2的上下移动;成对的复位组件4分别设置在第一锻打部11和第二锻打部21的两侧,以使向下移动后的上锻打部件2复位至最大向上移动位置。
[0047]
在本实用新型的附图中示出了包括一对引导组件3和一对复位组件4的示例,但本实用新型不限于此,其可以根据实际应用情况而设置有多对引导组件3和多对复位组件4。
[0048]
在下文中,将以一对引导组件3和一对复位组件4为示例进行详细描述。
[0049]
在本实用新型的一个实施方案中,复位组件4可以位于引导组件3的外侧,所述外侧是指靠近下锻打部件1和上锻打部件2的侧端面的一侧,如图中所示。
[0050]
在本实用新型的另一个实施方案中,复位组件4和引导组件3的位置可以互换,即引导组件3可以位于复位组件4的外侧。本实用新型不限于此,复位组件4和引导组件3的位置可以根据实际应用情况进行各种调整,于此不再赘述。
[0051]
进一步地,所述复位组件4的每一个包括:连接孔41、第一容纳孔42、第二容纳孔44、连通孔45、复位弹簧43以及限位螺钉46,连接孔41设置在下锻打部件1的下部;第一容纳孔42设置在连接孔41的上方且与连接孔41成阶梯形式,并且第一容纳孔42的上端与下锻打部件1的顶面平齐;第二容纳孔44设置在上锻打部件2的下部并与第一容纳孔42相对应;连通孔45设置在第二容纳孔44的上方,连通孔45与第二容纳孔44成阶梯形式且共同贯穿上锻打部件2;复位弹簧43位于第一容纳孔42和第二容纳孔44中;限位螺钉46穿过连通孔45以及
位于第一容纳孔42和第二容纳孔44中的所述复位弹簧43而与连接孔41接合,以使得上锻打部件2和下锻打部件1之间具有预定间隙。
[0052]
第一容纳孔42的内壁表面与复位弹簧43的外周表面之间隔开预定距离a,第二容纳孔44的内壁表面与复位弹簧43的外周表面之间隔开预定距离b,其中a>0,b≥0。
[0053]
在本实用新型的优选实施方案中,连接孔41、第一容纳孔42、第二容纳孔44、连通孔45、复位弹簧43的外周以及限位螺钉46的杆部的形状均设置为圆柱形,在此情况下,第一容纳孔42的径向直径大于复位弹簧43的径向直径,第二容纳孔44的径向直径略大于或等于复位弹簧43的径向直径,由此,在上锻打部件2的上下移动的过程中(即锻打过程中),可以防止复位弹簧43的位于第二容纳孔44中的部分左右晃动,同时减少复位弹簧43的位于第一容纳孔42中的部分与第一容纳孔42之间的摩擦,从而提高锻打效果,降低待锻打产品损坏的风险。
[0054]
进一步地,在上述优选实施方案中,第一容纳孔42的径向直径大于连接孔41的径向直径,第二容纳孔44的径向直径大于连通孔45的径向直径。优选地,第一容纳孔42的径向直径大于第二容纳孔44的径向直径。
[0055]
当本实用新型的锻打模具组装完成后(如图4中所示),限位螺钉46的杆部的从第一容纳孔42的下端到限位螺钉46的头部的底面之间的部分称之为第一部分p1,限位螺钉46的杆部的其余部分称之为第二部分p2。其中限位螺钉46的杆部的第一部分p1的轴向长度大于连通孔45、第二容纳孔44以及第一容纳孔42的轴向长度之和,并且限位螺钉46的杆部的第一部分p1的径向直径大于第二部分p2的径向直径。
[0056]
此外,连接孔41的内壁表面设置有内螺纹,限位螺钉46的杆部的第二部分p2设置有外螺纹,所述内螺纹与所述外螺纹接合,从而使限位螺钉46的杆部的第二部分p2与连接孔41接合。
[0057]
进一步地,复位弹簧43为压缩弹簧,并且复位弹簧43的原长大于第二容纳孔44和第一容纳孔42的轴向长度之和。
[0058]
通过如上所述设置的限位螺钉46和复位弹簧43,使得上锻打部件2和下锻打部件1之间具有预定间隙s,并且向下移动后的上锻打部件2可以复位至最大向上移动位置。
[0059]
参见图1至图5,引导组件3的每一个包括:引导杆31和引导孔32,引导杆31设置在下锻打部件1中;引导孔32设置在上锻打部件2中,并使得引导杆31插入到引导孔32中。
[0060]
在本实用新型的一个实施方案中,引导组件3的每一个可以进一步包括安装孔33,安装孔33设置在下锻打部件1中并与引导孔32相对应,并且引导杆31与安装孔33之间为过盈配合。
[0061]
在本实用新型的另一个实施方案中,引导杆31与下锻打部件1可以一体成型,并且引导杆31的上部突出于下锻打部件1的顶面,从而插入到引导孔32中。
[0062]
进一步地,引导杆31的位于上锻打部件2中的部分的外周表面可以设置有凹槽34。所述凹槽34中可以放置有润滑剂,从而使锻打过程更顺畅。
[0063]
第一锻打部11和第二锻打部21共同形成锻打通道,所述锻打通道可以是平截圆锥体结构,并且锻打通道的前部的直径大于后部的直径。锻打通道的前部相比于锻打通道的后部更靠近开始要锻打的产品。
[0064]
在本实用新型的优选实施方案中,锻打模具可以进一步包括扩大部,其设置在所
述锻打通道的前部。如图中所示,扩大部由第一扩大部分111和第二扩大部分211构成,其中,所述第一扩大部分111设置于下锻打部件1,且位于第一锻打部11的前部;所述第二扩大部分211设置于上锻打部件2,且位于第二锻打部21的前部。在锻打过程中,所述扩大部使待锻打的产品可以更容易地插入到锻打通道中。
[0065]
进一步地,下锻打部件1可以进一步包括多个穿孔12,通过所述穿孔12可以将下锻打部件1固定至锻打机。
[0066]
在本实用新型的附图中,示出了包括三个穿孔12的示例,在此情况下,可以通过两个定位导柱121和一个模具锁紧螺钉(未示出)而将本实用新型中的锻打模具固定至锻打机,也可以通过三个模具锁紧螺钉而将本实用新型中的锻打模具固定至锻打机,本实用新型的穿孔数量与固定方式不以此为限。
[0067]
在下文中,将以本实用新型中的锻打模具锻打电极体为例,对锻打模具的结构和原理进行进一步地描述。
[0068]
将锻打模具按照图中所示的方式组装完成并固定至锻打机,将待锻打的电极体的前段置于扩大部中,启动锻打机,使待锻打的电极体向锻打通道行进,同时锻打机的撞针撞击上锻打部件,通过撞针的撞击力使上锻打部件向下移动,由第一锻打部和第二锻打部形成的锻打通道锻打待锻打的电极体,在撞针的一次撞击完成后,撞针复位,在复位组件的作用下使向下移动后的上锻打部件复位至最大向上移动位置,不断重复此锻打步骤,随着待锻打的电极体行进,锻打通道的直径不断缩小,锻打过程持续进行,直至完成整个电极体的锻打。
[0069]
前面的对本实用新型具体的示例性实施方案所呈现的描述出于说明和描述的目的。它们并非旨在穷举,或者将本实用新型限制为公开的精确的形式,且显然的是,根据以上教导,可以进行很多修改和变化。示例性实施方案的选择和描述是为了解释本实用新型的某些原理及其实际应用,从而使得本领域技术人员能够制造并利用本实用新型的各种示例性实施方案及其不同替代形式和修改形式。本实用新型的范围旨在通过所附权利要求及其等效形式来限定。