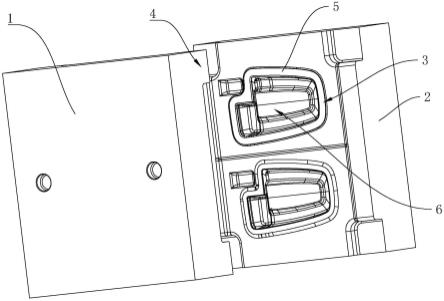
1.本实用新型属于模具技术领域,涉及一种汽车车门高强度轻量化铝合金铰链锻压成型模。
背景技术:2.车门加强板是对门体结构进行局部加强而设置的版构件,具体使用于车门内板面上安装车门附件机构的部位,提高安装部位的刚度和连接强度,在门体安装铰链处、车门开度限位器处和门锁处等部位设置1.2mm~1.6mm厚的加强板,与车门内板焊接(或与车门内板焊接),以便将车门的局部集中复核能有效的传到车门板件的较大板面上,从而强化门体的局部刚度和车门的安装刚度。现有的车门板一般采用压铸模具进行制造,在压铸过程中,产品容易发生折叠、欠肉的缺陷,表面质量较为一般,需要进行二次加工,成型周期较长
3.为了克服现有技术的不足,人们经过不断探索,提出了各种各样的解决方案,如中国专利公开了一种轿车车门外板铝合金压铸模具[申请号:201710078614.5],包括一上模及一下模,其中该上模具形似轿车车门外板结构件状,该下模具有一模穴,且该模穴适于容置该上模具;其特征是将该上模与该下模压合外、内壁间隙为0.05mm至0.1mm之间;所述上、下模通过运用pro/e、catia、ug-nx以及autocad软件,根据铝合金模具的设计级数计算,选用2500t压铸机对其进行模具设计,设计出车门外板成形所需的压铸模,并通过cae有限元分析进行验证;在上、下模上设计多点式浇注口及渣包和排气系统。但是该方案在压铸过程中,产品仍然容易发生折叠、欠肉的缺陷,表面质量较为一般,需要进行二次加工,成型周期较长的缺陷。
技术实现要素:[0004]
本实用新型的目的是针对上述问题,提供一种汽车车门高强度轻量化铝合金铰链锻压成型模。
[0005]
为达到上述目的,本实用新型采用了下列技术方案:
[0006]
一种汽车车门高强度轻量化铝合金铰链锻压成型模,包括压铸上模和压铸下模,所述的压铸上模底部设有压铸成型凸部,所述的压铸下模内设有防欠肉压铸成型组件,所述的防欠肉压铸成型组件与压铸成型凸部的位置相对应且形状相配适,所述的压铸上模上设有合模对位部,所述的合模对位部与压铸下模相卡接配合,所述的合模对位部与压铸成型凸部交错设置。
[0007]
在上述的汽车车门高强度轻量化铝合金铰链锻压成型模中,所述的防欠肉压铸成型组件包括设置于压铸下模内的若干车门成型凹腔,所述的车门成型凹腔内设有防欠肉中心凸部,所述的防欠肉中心凸部与压铸成型凸部的位置相对应,所述的车门成型凹腔与压铸成型凸部的位置相对应且形状相配适。
[0008]
在上述的汽车车门高强度轻量化铝合金铰链锻压成型模中,所述的若干车门成型凹腔沿压铸下模中心线对称设置,所述的防欠肉中心凸部包括设置于车门成型凹腔内的防
欠肉中心凸板,所述的防欠肉中心凸板顶部呈平整状,所述的防欠肉中心凸板的厚度小于车门成型凹腔的深度。
[0009]
在上述的汽车车门高强度轻量化铝合金铰链锻压成型模中,所述的防欠肉中心凸板与车门成型凹腔之间的连接处设有弧面,所述的车门成型凹腔内还设有车门凸块成型部,所述的车门凸块成型部与防欠肉中心凸板交错设置。
[0010]
在上述的汽车车门高强度轻量化铝合金铰链锻压成型模中,所述的车门凸块成型部包括设置于车门成型凹腔内的车门凸块成型凹槽,所述的车门凸块成型凹槽与防欠肉中心凸板交错设置,所述的车门凸块成型凹槽的深度大于车门成型凹腔的深度。
[0011]
在上述的汽车车门高强度轻量化铝合金铰链锻压成型模中,所述的压铸成型凸部包括设置于压铸上模底部的若干压铸成型凸框板,所述的压铸成型凸框板与车门成型凹腔的位置相对应且形状相配适。
[0012]
在上述的汽车车门高强度轻量化铝合金铰链锻压成型模中,所述的压铸成型凸框板内设有上部辅助成型腔,所述的上部辅助成型腔与防欠肉中心凸板的位置相对应。
[0013]
在上述的汽车车门高强度轻量化铝合金铰链锻压成型模中,所述的压铸下模上还设有外设夹持定位部,所述的外设夹持定位部与车门成型凹腔交错设置。
[0014]
在上述的汽车车门高强度轻量化铝合金铰链锻压成型模中,所述的外设夹持定位部包括设置于压铸下模上的若干外设夹持凹槽,所述的外设夹持凹槽呈方形。
[0015]
在上述的汽车车门高强度轻量化铝合金铰链锻压成型模中,所述的合模对位部包括设置于压铸上模上的若干合模对位侧块,所述的压铸下模上设有若干合模对位侧开槽,所述的合模对位侧块与合模对位侧开槽相卡接配合。
[0016]
与现有的技术相比,本实用新型的优点在于:
[0017]
1、本实用新型在压铸过程中,先将物料放置于压铸上模和压铸下模之间,再将压铸上模和压铸下模相互靠近,通过合模对位部与压铸下模之间的卡接配合,提高了合模的精度,压铸质量较高,使得压铸成型凸部与防欠肉压铸成型组件相抵接配合形成完整的型腔,进行压铸,在压铸过程中,通过防欠肉压铸成型组件可避免在压铸过程中产品发生折叠、欠肉的缺陷,提高了产品的表面质量,无需进行二次精磨加工,缩短了成型周期,实用性较强。
[0018]
2、本实用新型通过在防欠肉中心凸板与车门成型凹腔之间的连接处设有弧面,产品交接处流畅,确保物料的流畅度,且避免产品边缘出现凸起,无需进行二次打磨。
[0019]
本实用新型的其它优点、目标和特征将部分通过下面的说明体现,部分还将通过对本实用新型的研究和实践而为本领域的技术人员所理解。
附图说明
[0020]
图1是本实用新型的爆炸示意图。
[0021]
图2是本实用新型另一个方向的爆炸示意图。
[0022]
图3是压铸下模的结构示意图。
[0023]
图4是压铸上模的结构示意图。
[0024]
图中:压铸上模1、压铸下模2、压铸成型凸部22、防欠肉压铸成型组件3、合模对位部4、车门成型凹腔5、防欠肉中心凸部6、防欠肉中心凸板7、车门凸块成型部8、车门凸块成
型凹槽9、压铸成型凸框板10、上部辅助成型腔11、外设夹持定位部12、外设夹持凹槽13、合模对位侧块14、合模对位侧开槽15。
具体实施方式
[0025]
下面结合附图对本实用新型进行进一步说明。
[0026]
如图1-4所示,一种汽车车门高强度轻量化铝合金铰链锻压成型模,包括压铸上模1和压铸下模2,所述的压铸上模1底部设有压铸成型凸部22,所述的压铸下模2内设有防欠肉压铸成型组件3,所述的防欠肉压铸成型组件3与压铸成型凸部22的位置相对应且形状相配适,所述的压铸上模1上设有合模对位部4,所述的合模对位部4与压铸下模2相卡接配合,所述的合模对位部4与压铸成型凸部22交错设置。
[0027]
在本实施例中,在压铸过程中,先将物料放置于压铸上模1和压铸下模2之间,再将压铸上模1和压铸下模2相互靠近,通过合模对位部4与压铸下模2之间的卡接配合,提高了合模的精度,压铸质量较高,使得压铸成型凸部22与防欠肉压铸成型组件3相抵接配合形成完整的型腔,进行压铸,在压铸过程中,通过防欠肉压铸成型组件3可避免在压铸过程中产品发生折叠、欠肉的缺陷,提高了产品的表面质量,无需进行二次精磨加工,缩短了成型周期,实用性较强。
[0028]
结合图1-4所示,所述的防欠肉压铸成型组件3包括设置于压铸下模2内的若干车门成型凹腔5,所述的车门成型凹腔5内设有防欠肉中心凸部6,所述的防欠肉中心凸部6与压铸成型凸部22的位置相对应,所述的车门成型凹腔5与压铸成型凸部22的位置相对应且形状相配适。
[0029]
具体地说,在压铸过程中,车门成型凹腔5与压铸成型凸部22相互抵接配合,形成型腔,防欠肉中心凸部6用以成型车门中心凸部结构,通过防欠肉中心凸部6可避免在压铸过程中产品发生折叠、欠肉的缺陷,提高了产品的表面质量,无需进行二次精磨加工,缩短了成型周期,实用性较强。
[0030]
结合图1、图2所示,所述的若干车门成型凹腔5沿压铸下模2中心线对称设置,所述的防欠肉中心凸部6包括设置于车门成型凹腔5内的防欠肉中心凸板7,所述的防欠肉中心凸板7顶部呈平整状,所述的防欠肉中心凸板7的厚度小于车门成型凹腔5的深度。
[0031]
本实施例中,防欠肉中心凸板7用以成型车门中心凸部结构,通过防欠肉中心凸板7可避免在压铸过程中产品发生折叠、欠肉的缺陷,防欠肉中心凸板7顶部呈平整状,可减少毛刺的产生,提高了产品的表面质量,无需进行二次精磨加工,缩短了成型周期,实用性较强,防欠肉中心凸板7的厚度小于车门成型凹腔5的深度,不影响合模的精度。
[0032]
所述的防欠肉中心凸板7与车门成型凹腔5之间的连接处设有弧面,所述的车门成型凹腔5内还设有车门凸块成型部8,所述的车门凸块成型部8与防欠肉中心凸板7交错设置。
[0033]
本实施例中,防欠肉中心凸板7与车门成型凹腔5之间的连接处设有弧面,产品交接处流畅,确保物料的流畅度,且避免产品边缘出现凸起,无需进行二次打磨,车门凸块成型部8用以成型车门凸块结构。
[0034]
结合图3所示,所述的车门凸块成型部8包括设置于车门成型凹腔5内的车门凸块成型凹槽9,所述的车门凸块成型凹槽9与防欠肉中心凸板7交错设置,所述的车门凸块成型
凹槽9的深度大于车门成型凹腔5的深度。
[0035]
本实施例中,车门凸块成型凹槽9用以成型车门凸块结构,车门凸块成型凹槽9的深度大于车门成型凹腔5的深度,确保凸块的厚度。
[0036]
所述的压铸成型凸部22包括设置于压铸上模1底部的若干压铸成型凸框板10,所述的压铸成型凸框板10与车门成型凹腔5的位置相对应且形状相配适。
[0037]
本实施例中,在合模时,压铸成型凸框板10与车门成型凹腔5相互靠近,形成密封的压铸腔室。
[0038]
所述的压铸成型凸框板10内设有上部辅助成型腔11,所述的上部辅助成型腔11与防欠肉中心凸板7的位置相对应。
[0039]
本实施例中,上部辅助成型腔11用以辅助成型车门的上部结构。
[0040]
结合图3所示,所述的压铸下模2上还设有外设夹持定位部12,所述的外设夹持定位部12与车门成型凹腔5交错设置。
[0041]
本实施例中,外设夹持定位部12方便在开模后,外接夹持设备通过外设夹持定位部12对压铸下模2进行夹持移动,清理清洗残留在车门成型凹腔5内的杂质,操作简单方便。
[0042]
结合图1、图3所示,所述的外设夹持定位部12包括设置于压铸下模2上的若干外设夹持凹槽13,所述的外设夹持凹槽13呈方形。
[0043]
本实施例中,外设夹持凹槽13方便在开模后,外接夹持设备通过外设夹持凹槽13对压铸下模2进行夹持移动,清理清洗残留在车门成型凹腔5内的杂质,操作简单方便。
[0044]
结合图1、图2所示,所述的合模对位部4包括设置于压铸上模1上的若干合模对位侧块14,所述的压铸下模2上设有若干合模对位侧开槽15,所述的合模对位侧块14与合模对位侧开槽15相卡接配合。
[0045]
本实施例中,在合模时,将合模对位侧块14和合模对位侧开槽15相互靠近,通过合模对位侧块14与合模对位侧开槽15之间的卡接配合,提高了合模的精度,压铸质量较高。
[0046]
本实用新型的工作原理是:
[0047]
在压铸过程中,先将物料放置于压铸上模1和压铸下模2之间,再将压铸上模1和压铸下模2相互靠近,通过合模对位侧块14与合模对位侧开槽15之间的卡接配合,提高了合模的精度,压铸质量较高,使得压铸成型凸框板10与车门成型凹腔5相互靠近,形成密封的压铸腔室,进行压铸,
[0048]
在压铸过程中,通过防欠肉中心凸板7可避免在压铸过程中产品发生折叠、欠肉的缺陷,防欠肉中心凸板7顶部呈平整状,可减少毛刺的产生,提高了产品的表面质量,无需进行二次精磨加工,缩短了成型周期,实用性较强,防欠肉中心凸板7的厚度小于车门成型凹腔5的深度,不影响合模的精度,
[0049]
防欠肉中心凸板7与车门成型凹腔5之间的连接处设有弧面,产品交接处流畅,确保物料的流畅度,且避免产品边缘出现凸起,无需进行二次打磨,车门凸块成型部8用以成型车门凸块结构,
[0050]
车门凸块成型凹槽9用以成型车门凸块结构,车门凸块成型凹槽9的深度大于车门成型凹腔5的深度,确保凸块的厚度,
[0051]
上部辅助成型腔11用以辅助成型车门的上部结构,
[0052]
外设夹持凹槽13方便在开模后,外接夹持设备通过外设夹持凹槽13对压铸下模2
进行夹持移动,清理清洗残留在车门成型凹腔5内的杂质,操作简单方便。
[0053]
本文中所描述的具体实施例仅仅是对本实用新型精神作举例说明。本实用新型所属技术领域的技术人员可以对所描述的具体实施例做各种各样的修改或补充或采用类似的方式替代,但并不会偏离本实用新型的精神。
[0054]
尽管本文较多地使用压铸上模1、压铸下模2、压铸成型凸部22、防欠肉压铸成型组件3、合模对位部4、车门成型凹腔5、防欠肉中心凸部6、防欠肉中心凸板7、车门凸块成型部8、车门凸块成型凹槽9、压铸成型凸框板10、上部辅助成型腔11、外设夹持定位部12、外设夹持凹槽13、合模对位侧块14、合模对位侧开槽15等术语,但并不排除使用其它术语的可能性。使用这些术语仅仅是为了更方便地描述和解释本实用新型的本质,把它们解释成任何一种附加的限制都是与本实用新型精神相违背的。