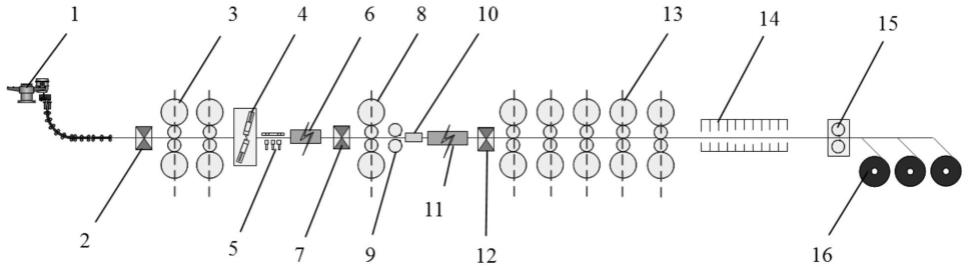
1.本实用新型属于带钢连铸连轧技术领域,涉及一种热轧带钢生产线,尤其涉及一种中、高碳钢连铸连轧无头轧制生产线。
背景技术:2.1986年德国西马克公司成功地进行薄板坯连铸机试验,1989年美国纽克钢公司在印第安那州的克劳福兹维尔建成了世界上第一个csp车间,标志着薄板坯连铸连轧技术投入了工业生产。此后,世界各钢铁/工程公司不断开发出新的薄板坯连铸连轧技术,如德国德马克公司的isp技术、奥地利奥钢联公司的conroll技术、日本住友公司的qsp技术、意大利达涅利公司的ftsr技术、意大利阿维迪公司的esp技术以及中国鞍钢的asp技术。其中csp技术应用最为普及,约占全球50%以上的市场份额。而esp则是最新的带钢无头连铸连轧工艺,其以占地面积小、结构紧凑、生产效率高等特点迅速占领了连铸连轧的新增市场。
3.薄板坯连铸连轧是获得薄规格和超薄规格热轧板的主要生产手段,随着应用时间的延长,一些生产线的问题逐渐凸显。例如,无头轧制连铸连轧生产线,由于连铸和轧钢部分刚性连接,受连铸拉坯速度的限制,轧钢段产线的速度难以提升,使得生产过程中薄板坯温降过大,无法满足部分钢种(如中碳钢、高碳钢)的生产工艺要求;连铸连轧的一个浇次开始时,连铸拉坯速度较低,轧钢段产线的速度也相应较低,造成浇次前几卷钢的工艺温度不能满足生产工艺要求,只能改判或废品处理,降低了产线的经济效益。另外,连铸连轧的一个浇次开始时,为了验证粗轧机的压下可靠性,造成楔形坯存在并进行切废坯处理,从而降低了生产线的产品收得率。
技术实现要素:4.有鉴于此,本实用新型的目的在于提供一种热轧带钢生产线,以提高产品的收得率。
5.为达到上述目的,本实用新型提供如下技术方案:
6.一种热轧带钢生产线,包括沿轧制方向依次通过辊道连接的板坯连铸机、粗轧机组、第一剪切装置、第一加热装置、中轧机组、第二加热装置、精轧机组、轧后冷却装置、高速飞剪和卷取机组;所述粗轧机组包括沿轧制方向依次设置的两个粗轧机架;所述中轧机组包括一个中轧机架。
7.可选地,所述精轧机组包括沿轧制方向依次设置的4~5个精轧机架。
8.可选地,所述精轧机组的入口处设有氧化铁皮去除装置。
9.可选地,所述氧化铁皮去除装置为高压水除鳞装置。
10.可选地,所述粗轧机组和/或中轧机组的入口处设有氧化铁皮去除装置。
11.可选地,所述氧化铁皮去除装置为高压水除鳞装置、旋转喷射除鳞装置、火焰清理式除鳞装置中的任一种。
12.可选地,所述第一剪切装置为摆剪,第一剪切装置出口处设有板坯推出及堆垛装
置。
13.可选地,所述中轧机组和第二加热装置之间设有第二剪切装置。
14.可选地,所述第二剪切装置为摆剪或转鼓飞剪,第二剪切装置出口处设有废料去除装置。
15.可选地,所述第一加热装置为纵磁感应加热炉;所述第二加热装置为横磁感应加热炉或纵磁感应加热炉。
16.本实用新型的有益效果在于:
17.1、通过在粗轧机组和第一加热装置之间、中轧机组和第二加热装置之间设置切剪切装置,用于切除板坯轧制变形产生的头部翘曲,能够防止翘曲缺陷对加热装置造成损伤。
18.2、通过将粗轧机组设置为两个粗轧机架,将中轧机组设置为一个中轧机架,能够减少浇次开始时因粗轧机压下检测造成的楔形坯切废数量,从而提高了产品的成材率。
19.3、通过第一加热装置和第二加热装置的设置,增加了补温能力,对浇次开始时低拉速生产的头几卷带钢进行补温,使其温度满足工艺温度要求并正常生产,减少了浇次内前几卷钢的改判或废品处理量。
20.4、通过第一加热装置和第二加热装置的设置,增加了补温能力,对因化学成分原因造成的低拉速生产钢种(如中碳钢和高碳钢)进行补温,使其温度满足工艺温度要求并正常生产,拓展了连铸连轧生产线的产品大纲,解决了现有无头轧制连铸连轧生产线产品品种受限的问题,从而提高了无头轧制连铸连轧生产线的市场适应性和竞争力。
21.本实用新型的其他优点、目标和特征在某种程度上将在随后的说明书中进行阐述,并且在某种程度上,基于对下文的考察研究对本领域技术人员而言将是显而易见的,或者可以从本实用新型的实践中得到教导。本实用新型的目标和其他优点可以通过下面的说明书来实现和获得。
附图说明
22.为了使本实用新型的目的、技术方案和优点更加清楚,下面将结合附图对本实用新型作优选的详细描述,其中:
23.图1为本实用新型热轧带钢生产线生产线的布置示意图。
24.附图标记:板坯连铸机1、粗除鳞装置2、粗轧机组3、摆剪4、板坯推出及堆垛装置5、第一加热装置6、中间除鳞装置7、中轧机组8、转鼓飞剪9、废料去除装置10、第二加热装置11、精除鳞装置12、精轧机组13、层流冷却装置14、高速飞剪15、卷取机16。
具体实施方式
25.以下通过特定的具体实例说明本实用新型的实施方式,本领域技术人员可由本说明书所揭露的内容轻易地了解本实用新型的其他优点与功效。本实用新型还可以通过另外不同的具体实施方式加以实施或应用,本说明书中的各项细节也可以基于不同观点与应用,在没有背离本实用新型的精神下进行各种修饰或改变。需要说明的是,以下实施例中所提供的图示仅以示意方式说明本实用新型的基本构想,在不冲突的情况下,以下实施例及实施例中的特征可以相互组合。
26.其中,附图仅用于示例性说明,表示的仅是示意图,而非实物图,不能理解为对本
实用新型的限制;为了更好地说明本实用新型的实施例,附图某些部件会有省略、放大或缩小,并不代表实际产品的尺寸;对本领域技术人员来说,附图中某些公知结构及其说明可能省略是可以理解的。
27.本实用新型实施例的附图中相同或相似的标号对应相同或相似的部件;在本实用新型的描述中,需要理解的是,若有术语“上”、“下”、“左”、“右”、“前”、“后”等指示的方位或位置关系为基于附图所示的方位或位置关系,仅是为了便于描述本实用新型和简化描述,而不是指示或暗示所指的装置或元件必须具有特定的方位、以特定的方位构造和操作,因此附图中描述位置关系的用语仅用于示例性说明,不能理解为对本实用新型的限制,对于本领域的普通技术人员而言,可以根据具体情况理解上述术语的具体含义。
28.请参阅图1,一种热轧带钢生产线,包括沿轧制方向依次通过辊道连接的板坯连铸机1、粗轧机组3、摆剪4、第一加热装置6、中轧机组8、转鼓飞剪9、第二加热装置11、精轧机组13、轧后冷却装置、高速飞剪15和卷取机组;粗轧机组3包括沿轧制方向依次设置的两个粗轧机架;中轧机组8包括一个中轧机架。第一加热装置6和第二加热装置11用于向通过其中的中间坯提供温度补偿。
29.本实用新型在粗轧机组3和第一加热装置6之间、中轧机组8和第二加热装置11之间均设有剪切装置,用于切除板坯轧制变形产生的头部翘曲,能够防止翘曲缺陷对加热装置造成损伤。
30.可选地,精轧机组13包括沿轧制方向依次设置的4~5个精轧机架;粗轧机组3、中轧机组8、精轧机组13的入口处设有氧化铁皮去除装置;粗轧机组3、中轧机组8前的氧化铁皮去除装置为高压水除鳞装置、旋转喷射除鳞装置、火焰清理式除鳞装置中的任一种;精轧机组13前的氧化铁皮去除装置为高压水除鳞装置;摆剪4出口处设有板坯推出及堆垛装置5,可将摆剪4切断后的板坯推出生产线并储存;转鼓飞剪9出口处设有废料去除装置10,可将转鼓飞剪9剪切的废钢储存并下线;第一加热装置6为纵磁感应加热炉;第二加热装置11为横磁感应加热炉或纵磁感应加热炉。
31.下面将结合实施例对本实用新型进行说明:
32.提供如图1所示的带钢生产线,包括依次通过辊道连接的板坯连铸机1、粗除鳞装置2、粗轧机组3、摆剪4、板坯推出及堆垛装置5、第一加热装置6、中间除鳞装置7、中轧机组8、转鼓飞剪9、废料去除装置10、第二加热装置11、精除鳞装置12、精轧机组13、层流冷却装置14、高速飞剪15和卷取机16。其中,粗轧机组3包括沿轧制方向依次设置的两个粗轧机架;中轧机组8包括一个中轧机架,精轧机组13包括沿轧制方向依次设置的5个精轧机架。
33.实施例一
34.铸坯原材料化学成分质量百分比分别为:c:0.047%,mn:0.12%,si:0.02%,p:0.011%,s:0.003%,als:0.023%,余量为fe和杂质。
35.将上述原材料进行冶炼后在连铸机内浇铸成坯,连铸拉速5.5m/min,连铸坯厚度95mm。
36.将连铸出口的铸坯经粗除鳞装置2并采用20mpa的高压水进行粗除鳞,再进入粗轧机组3轧制为18.5mm的中间坯,粗轧出口温度为1012℃,再依次行经摆剪4、板坯推出及堆垛装置5,然后进入第一加热装置6加热,第一加热装置6的出口温度控制为1038℃,随后进入中轧机组8轧制为9mm厚的中间坯,中间轧制机组的出口温度为913℃,中间坯离开中轧机组
后行经转鼓飞剪9和废料去除装置10,随后进入第二加热装置11加热,感应加热出口温度为1125℃,中间坯进入精轧机组13前先经精除鳞装置12进行高压水除鳞,除鳞水压力为38mpa,除鳞后的中间坯进入精轧机组13轧制,经过5机架精轧机轧制为1mm厚的成品带钢,精轧机组13的入口温度为989℃,终轧温度为853℃,精轧完成后经过层流冷却装置14对带钢进行控制冷却,开启水量为630m3/h,带钢冷却至660℃进行卷取,当卷重达到设定要求时采用高速飞剪15进行切分,3台地下卷取机16交替工作。
37.本实施例中带钢成品厚度1.0mm,抗拉强度354mpa,屈服强度275mpa,屈强比0.77,伸长率38.8%。
38.实施例二
39.铸坯原材料化学成分质量百分比分别为:c:0.65%,mn:1.05%,si:0.25%,p:0.01%,s:0.002%,als:0.022%,余量为fe和杂质。
40.将上述原材料进行冶炼后在连铸机内浇铸成坯,连铸拉速4.5m/min,连铸坯厚度105mm。
41.连铸坯进入粗轧机组3轧制为26.5mm的中间坯,粗轧出口温度为1002℃,依次行经摆剪4、板坯推出及堆垛装置5,然后进入第一加热装置6加热,第一加热装置6的出口温度控制为1042℃,随后进入中轧机组8轧制为14.6mm厚的中间坯,中间轧制机组的出口温度为948℃,中间坯离开中轧机组后行经转鼓飞剪9和废料去除装置10,随后进入第二加热装置11加热,感应加热出口温度为1149℃,中间坯进入精轧机组13前先经中间除鳞装置7进行高压水除鳞,除鳞水压力为38mpa,除鳞后的中间坯进入精轧机组13轧制,经过5机架精轧机轧制为2.3mm厚的成品带钢,精轧机组13入口温度为997℃,终轧温度为843℃,精轧完成后经层流冷却装置14对带钢进行控制冷却,开启水量为630m3/h,带钢冷却至650℃进行卷取,当卷重达到设定要求时采用高速飞剪15进行切分,3台地下卷取机16交替工作。
42.本实施例中带钢成品厚度2.3mm,抗拉强度735mpa,屈服强度455mpa,屈强比0.62,伸长率16.8%。
43.实施例三
44.铸坯原材料化学成分质量百分比分别为:c:0.01%,mn:0.1%,si:0.018%,p:0.01%,s:0.003%,als:0.021%,余量为fe和杂质。
45.将上述原材料进行冶炼后在连铸机内浇铸成坯,连铸拉速5.5m/min,连铸坯厚度95mm。
46.将连铸出口的铸坯采用20mpa的高压水进行粗除鳞,再进入粗轧机组3轧制为18.5mm的中间坯,粗轧出口温度为1012℃,再依次行经摆剪4、板坯推出及堆垛装置5,然后进入第一加热装置6加热,第一加热装置6是出口温度控制为1038℃,随后进入中轧机组8轧制为9mm厚的中间坯,中轧机组8的出口温度为913℃,中间坯离开中轧机组8后行经转鼓飞剪9和废料去除装置10,随后进入第二加热装置11加热,第二加热装置11的出口温度为1125℃,中间坯进入精轧机组13前先经中间除鳞装置7进行高压水除鳞,除鳞水压力为38mpa,除鳞后的中间坯进入精轧机组13进行铁素体轧制,经过4机架精轧机轧制为1.2mm厚的成品带钢,精轧机组13的入口温度为856℃,终轧温度为783℃,精轧完成后空冷经过层流冷却段,带钢冷却至680℃进行卷取,当卷重达到设定要求时采用高速飞剪15进行切分,3台地下卷取机16交替工作。
47.本实施例中带钢成品厚度1.2mm,抗拉强度304mpa,屈服强度195mpa,屈强比0.64,伸长率40.6%。
48.实施例四
49.铸坯原材料化学成分质量百分比分别为:c:0.017%,mn:0.1%,si:0.02%,p:0.012%,s:0.002%,als:0.023%,余量为fe和杂质。
50.一个浇次开始后,铸坯原料钢水在结晶器内凝固成坯壳,带液芯的铸坯由引锭杆牵引离开结晶器下口,经足辊、弯曲段、弧形段往下移动直至水平段,当铸坯头部到达轧钢粗轧区时,铸坯厚度105mm,拉速约为4m/mim。引锭杆尾部穿过粗轧机组3后的摆剪4时,摆剪4剪切铸坯,引锭杆脱离摆剪4后,天车将其调离。当检查铸坯质量满足要求后,第一架粗轧机架开始压下,摆剪4剪切第一块楔形坯,以检查第一架粗轧机架工作状态是否满足要求;当第一架粗轧机架压下满足要求后,第二架粗轧机架开始压下,摆剪4剪切第二块楔形坯,以检查第二架粗轧机架工作状态是否满足要求。当全部粗轧机架工作状态检查正常后,摆剪4停剪,中间坯依次穿带进入轧线,直至卷取机16卷绕并建立张力,开始连续生产。
51.由于开浇阶段连铸坯的拉坯速度较低,浇次头部2~3卷带钢的轧制过程中温度降幅较大,第一加热装置6和第二加热装置11各自提供带坯温升180℃,开浇钢卷的终轧温度835℃,卷取温度645℃,力学性能满足产品质量要求,可按正常产品出售。
52.通过以上实施例可以看出,本实用新型通过粗轧机组3、中轧机组8和精轧机组13的三阶段轧制方式,以及第一加热装置6和第二加热装置11的设置,合理设定轧制工艺和加热温度,可以减少浇次开始时因粗轧机压下检测造成的楔形坯切废数量,从而提高产品的成材率;通过第一加热装置6和第二加热装置11的设置,增加了补温能力,对浇次开始时低拉速生产的头几卷带钢进行补温,使其温度满足工艺温度要求并正常生产,减少浇次内前几卷钢的改判或废品处理量;通过第一加热装置6和第二加热装置11的设置,增加了补温能力,对因化学成分原因造成的低拉速生产钢种(如中碳钢和高碳钢)进行补温,使其温度满足工艺温度要求并正常生产,拓展了连铸连轧生产线的产品大纲,解决了现有无头轧制连铸连轧生产线产品品种受限的问题,从而提高了无头轧制连铸连轧生产线的市场适应性和竞争力。
53.最后说明的是,以上实施例仅用以说明本实用新型的技术方案而非限制,尽管参照较佳实施例对本实用新型进行了详细说明,本领域的普通技术人员应当理解,可以对本实用新型的技术方案进行修改或者等同替换,而不脱离本技术方案的宗旨和范围,其均应涵盖在本实用新型的权利要求范围当中。