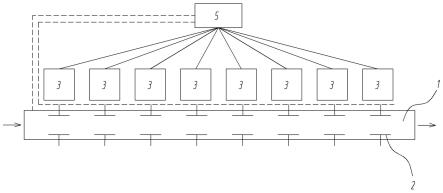
1.本实用新型涉及一种铣削系统,特别涉及一种动力电池在线铣削系统。
背景技术:2.汽车动力电池包是新能源汽车获取动力的唯一来源,目前的汽车动力电池包一般包括若干个电池模组,每个电池组又由若干个电池单体封装而成。随着新能源新车使用年限的增加,动力电池包往往会出现一些问题,导致新能源汽车的续航能力大幅度下降,这时通常是通过更换动力电池包的方式以解决上述问题。在实践中我们发现,旧的电池包中往往是由于某一个或几个电池单体出现故障,进而导致整个电池包出现问题。也就是说,旧的电池包中还有很大部分电池单体是处于正常状态的,对于正常状态的电池单体则具有很高的回收再利用价值。若想对旧电池包中的电池单体进行回收利用,那么就必须对电池包进行拆解,电池包拆解中的难度较大的就是对电池组的拆解,而且对电池组的拆解方式大多采用人工的方式,工作效率低,而且还容易损伤电池组内的电池单体,同时降低了有效回收率。
3.公开号为cn112570907a的中国专利文献,其公开了一种用于动力电池拆解的激光切割导流排装置,包括输送机、阻挡组件、定位组件、移载组件、机器人、激光切割头、ccd定位与激光测距组件、吸尘管、电池组和激光器,定位组件固定安装在输送机上,移载组件固定安装在输送机上的中间位置,阻挡组件固定安装在移载组件上,机器人固定安装在输送机后方的中间位置上,机器人的自由端与激光切割头传动连接,以实现对动力电池导流排进行快速安全切割的目的。该拆解方式存在问题在于:单个动力电池组的拆解时间过长,导致下游产线等待时间过长,拆解质量低下,进而导致整条动力电池拆解线的工作效率降低,同时激光切割容易过渡切割,进而对电池造成损伤,降低了有效回收率。面对新能源汽车日益增长的新局势,目前的电池拆解方式已经难于应付。
技术实现要素:4.本实用新型所要解决的技术问题是克服现有技术的不足,提供了一种拆解效率高、成本低,还能保证拆解质量的动力电池在线铣削系统。
5.本实用新型所采用的技术方案是:本实用新型包括动力电池输送线,沿着所述动力电池输送线的输送方向上设置有若干个定位装置和若干台视觉铣削机器人,所述定位装置和所述视觉铣削机器人一一对应,每一台所述视觉铣削机器人的自由端均设置有铣削机构;所述一种动力电池在线铣削系统还包括控制模块,所述动力电池输送线、若干个所述定位装置、若干台所述视觉铣削机器人均与所述控制模块电性连接。
6.进一步,所述定位装置包括左压紧机构和右压紧机构,所述左压紧机构和所述右压紧机构分别设置在所述动力电池输送线的两侧,所述左压紧机构和所述右压紧机构共同夹紧在所述动力电池输送线上的动力电池。
7.进一步,所述定位装置和所述视觉铣削机器人的数量均为八,八台所述视觉铣削
机器人均设置在所述动力电池输送线的一侧。
8.进一步,所述动力电池输送线的一侧设置有防护栏,所述防护栏与所述动力电池输送线的一侧围成工作区域,八台所述视觉铣削机器人均位于所述工作区域内。
9.进一步,所述动力电池输送线为双层输送线,所述双层输送线包括上下平行设置的上输送线和下输送线,所述上输送线用于输送动力电池,所述下输送线用于回流所述动力电池拆卸下来的零部件。
10.进一步,八台所述视觉铣削机器人协作拆除至少一组动力电池。
11.进一步,八台所述视觉铣削机器人协作拆除一组动力电池,八台所述视觉铣削机器人的第一台所述视觉铣削机器人开始铣削动力电池,第一台所述视觉铣削机器人工作一段时间后停止铣削,第一台所述视觉铣削机器人将已经完成的工序数据发送到所述控制模块,所述控制模块再将工序数据发送给第二台所述视觉铣削机器人并让第二台所述视觉铣削机器人接着第一台所述视觉铣削机器人未完成的工序继续铣削,第三台所述视觉铣削机器人接着第二台所述视觉铣削机器人未完成的工序继续铣削,以此类推,直至第八台所述视觉铣削机器人完成全部铣削工序。
12.进一步,每台所述视觉铣削机器人的工作时间均相等。
13.进一步,当一台或几台所述视觉铣削机器人发生故障不能工作时,所述控制模块将完成一组动力电池铣削的时间均分至剩余未发生故障的所述视觉铣削机器人,未发生故障的所述视觉铣削机器人继续完成一组动力电池铣削工作。
14.本实用新型的有益效果是:由于本实用新型采用统一的控制模块协调多台所述视觉铣削机器人一起工作,包括动力电池输送线,沿着所述动力电池输送线的输送方向上设置有若干个定位装置和若干台视觉铣削机器人,所述定位装置和所述视觉铣削机器人一一对应,每一台所述视觉铣削机器人的自由端均设置有铣削机构;所述一种动力电池在线铣削系统还包括控制模块,所述动力电池输送线、若干个所述定位装置、若干台所述视觉铣削机器人均与所述控制模块电性连接,所以,本实用新型的拆解效率高,不会出现等待时间过长,也不会出现个别故障导致整线停机停产的现象,相对与人工拆卸来说,本实用新型的工作时间更长,可以很好地降低成本,还能保证拆解质量。
附图说明
15.图1是本实用新型的原理结构图;
16.图2是本实用新型的立体图;
17.图3是本实用新型的俯视图;
18.图4是所述视觉铣削机器人的结构示意图。
具体实施方式
19.如图1至图4所示,在本实施例中,本实用新型包括动力电池输送线1,沿着所述动力电池输送线1的输送方向上设置有若干个定位装置2和若干台视觉铣削机器人3,所述定位装置2和所述视觉铣削机器人3一一对应,每一台所述视觉铣削机器人3的自由端均设置有铣削机构4;所述一种动力电池在线铣削系统还包括控制模块5,所述动力电池输送线1、若干个所述定位装置2、若干台所述视觉铣削机器人3均与所述控制模块5电性连接,本实用
新型采用统一的控制模块5协调多台所述视觉铣削机器人3一起工作,再通过控制所述动力电池输送线1和所述定位装置2实现自动化操作。
20.在本实施例中,所述定位装置2包括左压紧机构21和右压紧机构22,所述左压紧机构21和所述右压紧机构22分别设置在所述动力电池输送线1的两侧,所述左压紧机构21和所述右压紧机构22共同夹紧在所述动力电池输送线1上的动力电池6。
21.在本实施例中,所述定位装置2和所述视觉铣削机器人3的数量均为八,八台所述视觉铣削机器人3均设置在所述动力电池输送线1的一侧。
22.在本实施例中,所述动力电池输送线1的一侧设置有防护栏7,所述防护栏7与所述动力电池输送线1的一侧围成工作区域8,八台所述视觉铣削机器人3均位于所述工作区域8内。所述防护栏7的设计能有效保证工作人员的安全。
23.在本实施例中,所述动力电池输送线1为双层输送线,所述双层输送线包括上下平行设置的上输送线9和下输送线10,所述上输送线9用于输送动力电池6,所述下输送线10用于回流所述动力电池6拆卸下来的零部件。
24.在本实施例中,八台所述视觉铣削机器人3协作拆除一组动力电池6,八台所述视觉铣削机器人3的第一台所述视觉铣削机器人3开始铣削动力电池6,第一台所述视觉铣削机器人3工作一段时间后停止铣削,第一台所述视觉铣削机器人3将已经完成的工序数据发送到所述控制模块5,所述控制模块5再将工序数据发送给第二台所述视觉铣削机器人3并让第二台所述视觉铣削机器人3接着第一台所述视觉铣削机器人3未完成的工序继续铣削,第三台所述视觉铣削机器人3接着第二台所述视觉铣削机器人3未完成的工序继续铣削,以此类推,直至第八台所述视觉铣削机器人3完成全部铣削工序。
25.在本实施例中,每台所述视觉铣削机器人3的工作时间均相等。
26.在本实施例中,当一台或几台所述视觉铣削机器人3发生故障不能工作时,所述控制模块5将完成一组动力电池6铣削的时间均分至剩余未发生故障的所述视觉铣削机器人3,未发生故障的所述视觉铣削机器人3继续完成一组动力电池6铣削工作。
27.本实用新型的工作原理:组动力电池6放置在所述动力电池输送线1的入口,当所述组动力电池6到达第一个所述定位装置2时,第一个所述定位装置2的左压紧机构21和右压紧机构22共同夹紧所述组动力电池6,第一台所述视觉铣削机器人3开始铣削动力电池6,第一台所述视觉铣削机器人3工作一段时间后停止铣削,第一台所述视觉铣削机器人3将已经完成的工序数据发送到所述控制模块5,所述控制模块5再将工序数据发送给第二台所述视觉铣削机器人3并让第二台所述视觉铣削机器人3接着第一台所述视觉铣削机器人3未完成的工序继续铣削,第三台所述视觉铣削机器人3接着第二台所述视觉铣削机器人3未完成的工序继续铣削,以此类推,直至第八台所述视觉铣削机器人3完成全部铣削工序。当一台或几台所述视觉铣削机器人3发生故障不能工作时,所述控制模块5将完成一组动力电池6铣削的时间均分至剩余未发生故障的所述视觉铣削机器人3,未发生故障的所述视觉铣削机器人3继续完成一组动力电池6铣削工作,从而实现不停机不停产。
28.虽然本实用新型的实施例是以实际方案来描述的,但是并不构成对本实用新型含义的限制,对于本领域的技术人员,根据本说明书对其实施方案的修改及与其他方案的组合都是显而易见的。