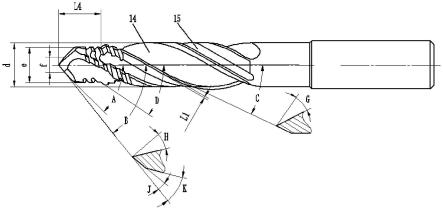
1.本实用新型涉及钻削工具技术领域,尤其涉及一种具有阶梯的麻花钻头。
背景技术:2.复合材料是由两种或者两种以上的材料组成的多相材料,既兼备了各组成材料的主要特点,又拥有了它们所没有的新性能,被广泛应用于航空航天领域。复合材料构件在其制造、装配过程中需进行大量钻削加工,由于复合材料属典型的难加工材料,在加工中极易产生加工损伤,如因约束不足,材料不能被有效去除,导致撕裂、毛刺、分层等损伤频发,使得复合材料构件的加工报废率大大提升,极大的影响加工效率及成本。
3.刀具的几何结构直接影响刀具的性能与加工效果,针对复合材料制孔,国内外研究人员开发了多种不同几何结构的制孔刀具。柳德春、周安善发明的“新副刃多刃尖航空钻”,专利申请号200910132775.3,它涉及一种适合钻削航空、航天工业中常用的高强度碳纤维复合材料、高硅铝合金等材料复合材料的多刃尖钻头,该刀具具有多条折线刃和微阶梯,同时副切削刃上具有凹槽结构,通过该结构设计可改善麻花钻的钻削性能,实现高效、高质量的钻削,然而该刀具主切削刃由多条折线刃组成,在大直径或者大进给制孔时存在折线刃连接处容易崩缺,且无法保证制孔质量。湖南科技大学苏飞等人公开了一种“具有圆弧刃刀片的碳纤维增强复合材料专用钻头”,专利申请号201711047792.8,该钻头为聚晶金刚石片焊接钻头,整体为三尖双顶角结构,钻扩一体,这样的结构设计有效地避免碳纤维增强复合材料钻削过程中毛刺、分层等现象的出现,一定程度降低制孔缺陷,提高加工效率、加工质量和刀具寿命,从而提高产品的合格率,但是聚晶金刚石片制造工艺难度、成本均较高,且在加工高强度纤维时,由于两边刀尖的切削速度较快,很容易磨损或崩缺,刀具寿命难以保障。大连理工大学公开了“一种碳纤维增强复合材料制孔的多阶梯多为微钻头”,专利申请号201610412512.8,该钻头包含多阶梯多微刃结构,通过分段钻削减小切削力,降低损伤,但刀具结构复杂致使磨削工艺繁琐,部分参数设计不合理,刀具制作成本高,如刃带设计过宽钻削过程中摩擦加剧,导致钻削温度上升。上述专利均结构复杂,生产难度大,可制造性不足,寿命与制造成本不匹配,因此需要一种均衡可制造性、制孔质量、刀具寿命的复合材料制孔刀具。
技术实现要素:4.本实用新型提供了一种具有阶梯的麻花钻头,包括切削本体,所述切削本体上设有主切削刃、副切削刃,所述主切削刃构成钻尖切削区,所述副切削刃上分布有多级阶梯,所述多级阶梯由多个阶梯组成,所述副切削刃上的多级阶梯构成阶梯切削区,所述多级阶梯上设有微齿结构。
5.作为本实用新型的进一步改进,所述切削本体上还设有主排屑槽、副排屑槽,所述主切削刃为两个,两个所述主切削刃形成双顶角结构。
6.作为本实用新型的进一步改进,所述双顶角结构的内刃顶角为102
°
~108
°
,所述
双顶角结构的外刃顶角为76
°
~86
°
,所述双顶角结构的横刃为0.1~0.3mm,横刃为两后刀面在钻尖的交线。
7.作为本实用新型的进一步改进,所述副切削刃为右螺旋,所述副切削刃的螺旋角为20
°
~40
°
,所述副切削刃的刃带宽l1为0.1-0.5mm,所述副切削刃前角为10
°
~20
°
。
8.作为本实用新型的进一步改进,所述多级阶梯包括第一阶梯和第二阶梯。
9.作为本实用新型的进一步改进,所述切削本体的直径为d,所述第一阶梯的直径e为(0.3~0.8)d。
10.作为本实用新型的进一步改进,第二阶梯顶角设置为70
°
~90
°
。
11.作为本实用新型的进一步改进,所述切削本体的直径为d,所述微齿结构由微齿和微齿槽组成,每个微齿的微齿宽为0.04d+(0.1~1)mm,微齿槽宽为0.06d+(0.1~1)mm,微齿槽深为0.06d+(0.1~2)mm。
12.作为本实用新型的进一步改进,所述微齿结构由微齿和微齿槽组成,微齿和微齿槽沿麻花钻头轴线呈螺旋分布,微齿的上齿边为切削刃。
13.作为本实用新型的进一步改进,微齿的螺旋角为30~90
°
,微齿槽同麻花钻头轴线夹角60~90
°
。
14.作为本实用新型的进一步改进,所述微齿结构由微齿和微齿槽组成,微齿和微齿槽沿麻花钻头轴线呈螺旋分布,所述微齿槽与所述主排屑槽连通。
15.作为本实用新型的进一步改进,所述主排屑槽为两个,所述副排屑槽为两个,所述副切削刃为四个。
16.作为本实用新型的进一步改进,该麻花钻头还包括柄部,所述柄部与所述切削本体相连。
17.本实用新型的有益效果是:本实用新型的麻花钻头,适合于复合材料的高质量、高效率加工,本实用新型的麻花钻头解决了复合材料在制孔中容易产生分层、毛刺、撕裂等损伤问题。
附图说明
18.图1是本实用新型麻花钻头结构示意图;
19.图2是本实用新型的切削本体结构示意图;
20.图3是图1的剖面示意图;
21.图4是垂直状态的麻花钻头结构示意图。
具体实施方式
22.如图1至4所示,本实用新型公开了一种具有阶梯的麻花钻头,适合于复合材料的高质量、高效率加工。本实用新型解决复合材料在制孔中容易产生分层、毛刺、撕裂等损伤问题。
23.该麻花钻头由切削本体10和柄部20组成,切削本体10包含钻尖切削区和阶梯切削区,其中阶梯切削区由多级阶梯组成,阶梯数量与切削本体10的直径大小相关,每级阶梯分布着一定数量的微齿结构13,每级阶梯微齿数目可以不相等,具体为:所述切削本体10上设有主切削刃11、副切削刃12、,所述主切削刃11构成钻尖切削区,所述多级阶梯由多个阶梯
组成,所述副切削刃12上分布有多级阶梯,所述副切削刃12上的多级阶梯构成阶梯切削区,所述多级阶梯上设有微齿结构13。
24.多级阶梯包括1~n级阶梯,n为大于等于2的正整数。
25.在图1中,内刃直径用f表示。
26.所述切削本体10上还设有主排屑槽14、副排屑槽15。
27.作为本实用新型的优选实施例,麻花钻头为二阶梯微齿麻花钻头,具体结构为两个主切削刃11、两个主排屑槽14,两个副排屑槽15,四个副切削刃12。两个主切削刃11经修磨后形成双顶角结构,内刃顶角a为102
°
~108
°
,外刃顶角b为76
°
~86
°
,横刃为0.1~0.3mm,以上参数设置可以保证麻花钻头锋利性,降低钻削轴向力,使得麻花钻头轻松钻入材料,减少出、入口初始毛刺、分层、撕裂损伤的发生。
28.所述副切削刃12为右螺旋,所述副切削刃12的螺旋角c为20
°
~40
°
(优选为30
°
),所述切削本体10的直径为d,所述副切削刃12的刃带宽l1为0.1~0.5mm,所述副切削刃12前角为10
°
~20
°
(优选为14
°
),以上参数设置可以减小麻花钻头钻入过程中复材表面的剥离撕裂,抑制入口撕裂损伤的发生,同时,因为麻花钻头制孔过程中,麻花钻头刃带会一直同孔内表面(孔壁)摩擦,小刃带设计可以减少钻削过程中钻头与孔壁的摩擦,减少切削热的产生,从而保证孔壁质量与钻头寿命。
29.副切削刃12前角用g表示。
30.该麻花钻头由二级阶梯组成,二级阶梯是指多级阶梯包括第一阶梯和第二阶梯,第一阶梯和第二阶梯均设置在所述副切削刃12上。第一阶梯的直径e为(0.3~0.8)d,这样的设计可以保证制孔过程,由第一阶梯和第二阶梯分别承担材料去除量,降低钻削轴向力,进而减小初始制孔损伤的产生,尤其适合大孔径或大板厚制孔。第二阶梯顶角d设置为70
°
~90
°
,这样的设置可以保证二阶梯切削区主切削刃在制孔过程中,可以同时切削掉第一阶梯主切削刃在钻入、钻出时造成的撕裂与毛刺,进一步保证了制孔出入口质量。钻尖位置设有主切削刃11,也称为第一阶梯主切削刃,同样第二阶梯切削区(即第一阶梯和第二阶梯交接位置)也有对应的切削刃,称之为二阶梯切削区主切削刃。
31.微齿结构13是由若干个分布于麻花钻头每级阶梯副切削刃上的微齿和微齿槽组成,每个微齿的微齿宽l2为0.04d+(0.1~1)mm,微齿槽宽l3为0.06d+(0.1~1)mm,微齿槽深为0.06d+(0.1~2)mm,使得在每级制孔过程中产生的毛刺可以回弹入微齿结构并被微齿切削刃剪断,可有效去除出、入口毛刺,降低复材制孔损伤。
32.微齿和微齿槽沿钻头轴线呈螺旋分布,微齿螺旋角e为30~90
°
,微齿槽同麻花钻头轴线夹角,即微齿槽角度f呈60~90
°
,微齿的上齿边为切削刃,以上参数设置均衡了微齿刃口的锋利性与可制造性,该螺旋角的设置使得微齿切削刃更长,即微齿上齿边更长,对毛刺的切削时间更长,切削能力、毛刺去除率均有提升。同时,该微齿槽角度的设置,微齿切削刃对毛刺的挤压、铰除作用更强烈,毛刺切削更有效。微齿槽同主排屑槽连通,微齿槽螺旋角的设置可以提升了微齿槽排屑性能,即促进切屑顺着微齿槽流向主排屑从而排出。同时,在麻花钻头制作过程中,微齿槽是由砂轮磨削形成的,该角度的设置更有利于砂轮磨削实现,可以提高可制造性。
33.在图1中,主切削刃11前角用h表示,主切削刃11第一后角用j表示,主切削刃11第二后角用k表示,第一阶梯长度用l4表示。
34.在图2中,第二阶梯后角用m表示。
35.在图3中,第一阶梯的微齿槽深度用l5表示,第二阶梯的微齿槽深度用l6表示,横刃长度用l7表示,芯厚用l8表示。
36.该麻花钻头具有两个主排屑槽14,两个副排屑槽15,四个副切削刃12,这样的设置使得微齿结构13在每条副切削刃12上的上齿边均具有切削刃,使得在制孔过程中回弹入微齿结构13的毛刺获得多次剪切,极大的提升了毛刺的铰除能力。同时复合材料在制孔过程中,由于材料本身特性存在纤维回弹,缩孔的现象,四个副切削刃12的设计可以有效的切除回弹纤维,同时使得在钻削过程中整个麻花钻头径向支撑和受力都更稳定,进而保证孔径精度,同时在钻削过程中提供更多的支撑,进而提升钻削稳定性、孔壁表面粗糙度。
37.该麻花钻头在钻削过程中每级阶梯进行材料去除量分摊,降低钻削轴向力,进而减小初始制孔损伤的产生。同时后一级阶梯主切削刃能够切削掉前一阶梯在钻入、钻出时造成的撕裂与毛刺。钻出过程中形成的初始毛刺,即未切断纤维,随着切削的继续进行回弹至副切削刃的微齿结构13中,通过多个副切削刃多微齿结构的切削刃进行多轮二次剪切,从而去除毛刺,保证孔径精度、孔壁质量,可实现低损伤一刀制孔。根据被加工复合材料的板厚、制孔孔径、发生损伤难易程度以及纤维切削难易程度进行阶梯结构和微齿结构的数量的设计,使之可以满足各种工况下的高效率无损伤制孔。
38.以上内容是结合具体的优选实施方式对本实用新型所作的进一步详细说明,不能认定本实用新型的具体实施只局限于这些说明。对于本实用新型所属技术领域的普通技术人员来说,在不脱离本实用新型构思的前提下,还可以做出若干简单推演或替换,都应当视为属于本实用新型的保护范围。