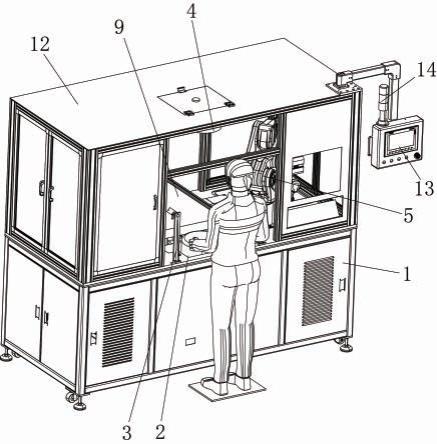
1.本实用新型涉及冲孔机技术领域,尤其是一种智能型锅具冲孔机。
背景技术:2.锅具组装手柄时,需对锅体进行冲孔,装铆钉后将手柄铆接固定。传统的操作方法采用人工操作冲孔的方式,有漏冲孔的风险。
3.人工作业进行冲孔操作时受人为因素影响,操作手法不可控,品质无法保证,会造成锅体掉漆,损伤锅体,同时疲劳式作业,生产效率低,安全隐患高。
4.市场上存在一些自动化设备,用于代替人工作业,但该种自动化设备需人工识别校对位置后,才能将产品放置于设备中作业,且不同产品切换需调整模具,通用性、柔性化程度低。
5.因此,申请人做进一步的改进。
技术实现要素:6.本实用新型针对现有技术中的不足,提供了一种智能型锅具冲孔机。
7.为解决上述技术问题,本实用新型通过下述技术方案得以解决:
8.一种智能型锅具冲孔机,包括机体,所述机体上配置有
9.锅具工位,用于放置锅具;
[0010] ccd识别系统,其固定于所述机体顶部并位于所述锅具工位上方;
[0011]
机械手单元,其安装于所述机体内的操作平台上,用于锅具位置的转移;
[0012]
冲孔工装,其安装于所述机体内的操作平台上,包括有用于放置锅具的槽口以及用于对锅具冲孔作业的冲头单元,所述冲头单元包括气缸及与所述气缸配合连接的冲头;及
[0013]
下料传送带,其配置于所述机体的操作平台上。
[0014]
上述方案中,优选的,所述机体一侧开设有操作窗口,所述锅具工位位于所述操作窗口侧边处。
[0015]
上述方案中,优选的,所述机体上设置有至少两个导柱,所述锅具工位滑动设置于所述导柱上并连接有滚珠丝杠,所述滚珠丝杠与设置于机体上的马达传动连接。
[0016]
上述方案中,优选的,所述锅具工位两侧安装有安全光栅。
[0017]
上述方案中,优选的,所述机械手单元为六轴机器人,其包括有用于吸取锅具的吸盘。
[0018]
上述方案中,优选的,所述机体内的操作平台两侧分别安装有对应的所述机械手单元以及所述冲孔工装。
[0019]
上述方案中,优选的,所述冲孔工装还包括有架体、设置于所述架体上的电机以及与所述电机输出端相连并可由其带动转动的机壳,所述架体固定安装于所述操作平台上,所述槽口开设于所述机壳上,所述机壳上开设于用于安装所述冲头的通道,所述气缸固定
安装于所述机壳上;
[0020]
所述电机与ccd识别系统电性连接。
[0021]
上述方案中,优选的,所述操作平台上设置有用于感应锅具是否放置到位的若干感应器。
[0022]
上述方案中,优选的,所述机体内位于所述操作平台下方设置有废料回收槽,所述操作平台上位于所述机壳下方开设有通孔,所述废料回收槽位于所述通孔正下方。
[0023]
上述方案中,优选的,所述机体上还设置有设备操作界面、数据监控画面、报警指示灯及安全保护罩,设备操作界面与ccd识别系统电性连接。
[0024]
本实用新型的有益效果是:
[0025]
本实用新型采用机器人取放产品,ccd识别自动对锅体进行定位,放于冲孔工装内进行冲孔作业;冲孔工装采用伺服马达控制,通过 ccd识别系统后自动调整冲孔角度;设备运用范围广,可适用铝制品,不锈钢拉伸锅等不同类型锅体。
附图说明
[0026]
图1为本实用新型示意图。
[0027]
图2为本实用新型操作平台上各部件示意图。
[0028]
图3为本实用新型机械手单元与冲孔工装的示意图。
[0029]
图4为本实用新型锅具工位与ccd识别系统的示意图。
[0030]
图5为本实用新型冲孔工装中的机壳示意图。
具体实施方式
[0031]
下面结合附图与具体实施方式对本实用新型作进一步详细描述:
[0032]
参见图1-图5,一种智能型锅具冲孔机,包括机体1,机体1包括有操作平台11,操作平台11上设置各部件,各部件由安全保护罩12罩设在内,安全保护罩12的前向侧具有操作窗口,安全保护罩的后向侧具有出料口。
[0033]
如图1所示,在机体1上还设置有设备操作界面13、数据监控画面及报警指示灯14,设备操作界面13及数据监控画面可安装于安全保护罩12上,使其安装高度更适应于操作人员查看,其中,设备操作界面13上具有控制单元,控制单元与操作平台11上的各可动作的部件电性连接,报警指示灯14可安装于设备操作界面13上。
[0034]
如图1、图2所示,机体1上具有锅具工位2,锅具工位2用于放置锅具,具体的,锅具工位2位于操作窗口一侧,操作人员可站立于此处,将需要打孔的锅具放置到锅具工位2上。
[0035]
本实施例中,锅具工位2可升降调整,以根据实际需要调整,作为其中一种实施方式,机体1上设置有至少两个导柱21,如图4所示,导柱21可设置有四个,锅具工位2滑动设置于导柱21上并连接有滚珠丝杠22,滚珠丝杠22与设置于机体1上的马达23传动连接,通过马达23带动滚珠丝杠22的螺杆转动,带动螺母及与螺母连接的锅具工位2升降。
[0036]
为提升操作人员的操作安全性,本实施例中,锅具工位2两侧安装有安全光栅3,如图1、图2所示。
[0037]
在机体1顶部位于锅具工位上方设置有ccd识别系统4,ccd识别系统4具体为ccd影像自动识别系统,用于识别锅具规格和型号,锅具规格和型号可预先存储入系统中,ccd识
别系统4可与控制单元或设备操作界面电性连接。
[0038]
本实施例中,在机体1的操作平台11上设置有机械手单元5及冲孔工装6,为提升操作效率,可在操作平台11两侧分别设置对应的机械手单元5和冲孔工装6,如图2所示。
[0039]
机械手单元5用于锅具位置的转移,本实施例中,机械手单元5为六轴机器人,其包括有用于吸取锅具的吸盘51;冲孔工装6用于锅具的打孔作业。
[0040]
冲孔工装6包括架体61、电机62、机壳63及冲头单元,架体61固定安装于操作平台11上,电机62安装于架体61上,电机62可为伺服电机,电机62的输出端与机壳63相连,以使机壳63可由电机62控制带动其转动,本实施例中,电机62与ccd识别系统电性连接,通过ccd识别系统识别锅具规格和型号,促使电机62运行,带动机壳63旋转已自动调整打孔角度。
[0041]
如图5所示,机壳63上包括有用于放置锅具的槽口631,锅具放置于槽口631上时的状态参见图3所示,冲头单元包括气缸64及与气缸64配合连接的冲头65,气缸64固定安装于机壳63上,冲头65则安装于机壳63上开设的通道632处。
[0042]
冲头65对锅具冲孔后,会产生废料,本实施例中,在机体1内位于操作平台11下方设置有废料回收槽7,具体的,在操作平台11上位于机壳63下方开设有通孔111,废料回收槽7则安装于该通孔111的正下方,每间隔一定时间,打开机体1的门取出废料回收槽7倒去废料再放回即可。
[0043]
为确定冲头单元冲孔时,锅具已放置到位,本实施例中,在操作平台11上设置有若干感应器8,具体的,如图3所示,可在锅具放置位置两侧分别设置对应的感应器8,一为信号发动感应器,一为信号接收感应器,在锅具放置到位后,两者之间信号被阻隔,依次判断锅具是否放置到位。
[0044]
本实施例中,机体的操作平台上还设置有下料传送带9,用于输送打孔完毕的锅具。
[0045]
具体实施流程如下:
[0046]
1.人工将锅具放于锅具工位上,ccd识别系统识别锅具规格及型号;
[0047]
2.冲孔工装根据 ccd识别系统识别反馈的信号,自动调整冲孔角度;
[0048]
3.六轴机器人将锅具产品移位至冲孔工装处,进行冲孔作业;
[0049]
4.锅具冲孔完毕后,六轴机器人将锅具放于下料传送带,下料传送带可连接包装线进行包装;
[0050]
5.机器人回到初始位,循环步骤1。
[0051]
以往锅具冲孔采用人工作业,采用机器人智能冲孔机后可满足冲孔技术标准要求,提高产能及品质,同时避免产品磕碰损伤涂层这一行业难题。
[0052]
以往人工锅具冲孔需要手动作业,人工放不到位,冲孔位置偏,冲孔有毛边,采用机器人智能双工位冲孔机后,程序自动保存,自动调用,这就无需经验丰富的操作人员进行操作,可大幅降低人工支出成本。
[0053]
采用 ccd识别系统,六轴机器人真空吸附取放产品,还可以根据软件设定的产品规格和型号,伺服机构可自动调整冲孔角度和位置。
[0054]
采用机器人智能双工位冲孔机,解决了行业内锅具在包装工序段,冲孔设备通型性,柔性化的问题,同时可提高产量,让产品包装工艺更流畅,数字化更高。
[0055]
以上实施例仅用以说明本实用新型的技术方案,而非对其限制;尽管参照前述实
施例对本实用新型进行了详细的说明,本领域的普通技术人员应当理解:其依然可以对前述各实施例所记载的技术方案进行修改,或者对其中部分技术特征进行等同替换;而这些修改或者替换,并不使相应技术方案的本质脱离本实用新型各实施例技术方案的精神和范围。