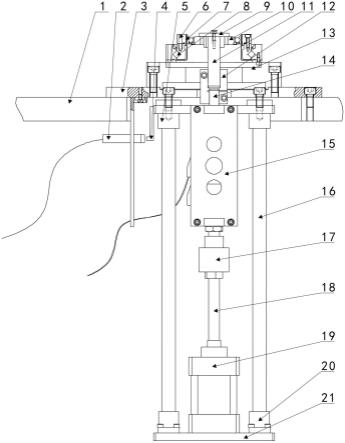
1.本实用新型涉及一种谐波减速机装配用机构,尤其涉及一种谐波减速机动态装配用支撑驱动机构,属于谐波减速机的生产领域。
背景技术:2.谐波减速机是独立的闭式传动装置,用来减低转速和增大转矩,以满足工作需要,具有精度高、传动比大、承载能力强、体积小、重量轻、传动效率高、寿命长、传动平稳、无冲击、噪声小的优点,在航空、航天、机床、仪表、电子设备、交通运输、石油化工机械、纺织机械、农业机械以及医疗器械等方面得到日益广泛的应用,特别是在高动态性能的伺服系统中,采用谐波齿轮传动更显示出其优越性。谐波减速机的产品性能不仅依赖于设计、制造过程,同样也对装配过程有很高的要求,任何一个环节如未能得到有效控制,都将影响谐波减速机的应用。
3.谐波减速机是一种靠波发生器装配上柔性轴承使柔性齿轮产生可控弹性变形,并与刚性齿轮相啮合来传递运动和动力的齿轮传动装置,谐波减速机主要由波发生器、柔轮、刚轮三个基本构件组成,在装配时与滚子轴承连接,这里的滚子轴承为十字形,所以也称为十字交叉滚子轴承。在谐波减速机的装配过程中,波发生器与柔轮之间,柔轮齿面与刚轮齿面啮合顺畅相当关键,是确保谐波减速机传动精度、重复定位精度、无振动、无异响的关键性因素。
4.谐波减速机的传统装配方式有两种:
5.第一种装配方式如下:以滚子轴承为基准,先将刚轮与滚子轴承装配好,再装配柔轮。具体过程如下:以刚轮的外止口放入到滚子轴承的内止口里面,这里完全靠内外止口的机加精度,只要止口配合到位之后就对角锁紧;然后再将柔轮从下往上装入,特别注意的是柔轮是圆形,此时柔轮的齿并不能与刚轮啮合,直接往上插入会干涩,硬压破坏齿面,导致柔轮报废,需要将波发生器装入柔轮,将柔轮撑开成椭圆形,保证椭圆长轴端的齿与刚轮的齿顺利啮合。
6.第二种装配方式如下:以滚子轴承为基准,先将柔轮与滚子轴承装配好,再装刚轮。具体过程如下:先把柔轮跟滚子轴承装好,需要校正柔轮与滚子轴承的同轴度,以端盖定位抱紧外圆的方式进行外圆同轴度的调整,然后拧紧螺钉;最后装入刚轮,刚轮还是靠外止口定位后拧紧,这种方式的好处是避免了先装刚轮时柔性与刚轮不完全啮合造成的受力不均匀导致的偏心。
7.上述两种装配方式都需要在静止状态直接对刚轮与柔轮的紧固螺钉进行拧紧,存在安装零件有可能歪斜从而导致转动到某个点干涩、旋转力矩增大等情况,装配好的谐波减速机可能发生振动、异响、传动精度差、温升过高等情况,甚至有可能出现电机过载报警的情况。
技术实现要素:8.本实用新型的目的就在于为了解决上述问题而提供一种谐波减速机动态装配用支撑驱动机构。
9.本实用新型通过以下技术方案来实现上述目的:
10.一种谐波减速机动态装配用支撑驱动机构,所述谐波减速机包括波发生器、柔轮和刚轮,所述谐波减速机在装配时与滚子轴承(即十字交叉滚子轴承)连接,所述谐波减速机动态装配用支撑驱动机构包括轴承安装板、驱动轴、伺服电机和控制器,横向的所述轴承安装板用于安装所述滚子轴承,所述轴承安装板设有竖向的安装板通孔,所述伺服电机位于所述轴承安装板的下方且其转轴的轴向为竖向,竖向的所述驱动轴的下端与所述伺服电机的转轴连接,所述驱动轴的上端穿过所述安装板通孔后用于与所述波发生器连接,所述伺服电机的控制输入端与所述控制器的控制输出端对应连接。
11.作为优选,为了便于安装并能够实现波发生器的高度调节功能以扩大适用范围,所述谐波减速机动态装配用支撑驱动机构还包括工作台、固定板、电机安装板、气缸、底座和接近开关,横向的所述固定板安装在横向的所述工作台上,所述轴承安装板安装在所述固定板上,竖向的所述气缸安装在所述底座上,所述气缸上部的活塞杆的上端与所述电机安装板的下端连接,所述伺服电机安装在所述电机安装板上,所述工作台和所述固定板分别设有用于所述电机安装板以及所述伺服电机的转轴穿过的竖向通孔,所述工作台的下方安装有所述接近开关,所述电机安装板的一侧安装有与所述接近开关配合的接近件,所述接近开关的信号输出端与所述控制器的信号输入端连接,所述气缸的控制输入端与所述控制器的控制输出端对应连接。
12.作为优选,为了实现对伺服电机移动的精确导向功能并避免因气缸的活塞杆与伺服电机的转轴不同轴导致部件损坏的问题,所述谐波减速机动态装配用支撑驱动机构还包括浮动接头、导向柱和直线轴承,所述气缸上部的活塞杆的上端与所述浮动接头的下端连接,所述浮动接头的上端与所述电机安装板的下端连接,两个竖向的所述导向柱的下端分别与所述底座连接并位于所述气缸的相对两侧,两个所述导向柱的上端分别与所述固定板连接,两个所述直线轴承分别套装在两个所述导向柱上,所述电机安装板的两侧分别设有连接板并通过该两个连接板与两个所述直线轴承连接,所述接近件靠近其中一个所述导向柱。
13.作为优选,为了便于快速连接驱动轴与波发生器,所述驱动轴的上端设有螺孔,安装螺钉由上而下穿过压紧板的中心通孔后与所述驱动轴的螺孔连接。
14.作为优选,为了提高驱动轴与伺服电机的转轴之间的连接精度,所述驱动轴的下端通过刚性联轴器与所述伺服电机的转轴连接。
15.本实用新型的有益效果在于:
16.本实用新型通过设计能够安装滚子轴承的轴承安装板和能够驱动波发生器旋转的驱动轴和伺服电机,在装配时先将刚轮与滚子轴承之间的连接螺钉安装好且不旋紧,在波发生器开始旋转并带动刚轮与柔轮都正常转动后再逐步锁紧连接螺钉,即可实现波发生器与柔轮之间、柔轮齿面与刚轮齿面之间啮合更加顺畅的目的,从而提高谐波减速机的装配精度和一次性装配合格率;通过设计相互配合的电机安装板、气缸、接近开关和接近件,能够根据实际需要改变驱动轴与波发生器之间的最佳连接位置,通过多次试验即可根据谐
波减速机的实际尺寸确定波发生器的最佳位置,从而进一步提高谐波减速机的装配精度和一次性装配合格率,避免装配好的谐波减速机发生振动、异响、传动精度差、温升过高等情况,谐波减速机传动更加平稳且无卡滞现象,并能够适应不同型号、尺寸的谐波减速机装配需求。
附图说明
17.图1是本实用新型所述谐波减速机动态装配用支撑驱动机构使用时的局剖主视结构示意图。
18.图中,1-工作台,2-接近开关,3-固定板,4-接近件,5-直线轴承,6-刚轮,7-柔轮,8-滚子轴承,9-压紧板,10-波发生器,11-驱动轴,12-刚性联轴器,13-轴承安装板,14-转轴,15-电机安装板,16-导向柱,17-浮动接头,18-活塞杆,19-气缸,20-支承座,21-底座。
具体实施方式
19.下面结合附图对本实用新型作进一步说明:
20.如图1所示,本实用新型所述谐波减速机包括波发生器10、柔轮7和刚轮6,所述谐波减速机在装配时与滚子轴承8连接,本实用新型所述谐波减速机动态装配用支撑驱动机构包括轴承安装板13、驱动轴11、伺服电机(图中被电机安装板15挡住而不可视)和控制器(图中未示出),横向的轴承安装板13用于安装滚子轴承8,轴承安装板13设有竖向的安装板通孔(图中未标记),所述伺服电机位于轴承安装板13的下方且其转轴14的轴向为竖向,竖向的驱动轴11的下端与所述伺服电机的转轴14连接,驱动轴11的上端穿过所述安装板通孔后用于与波发生器10连接,所述伺服电机的控制输入端与所述控制器的控制输出端对应连接。
21.如图1所示,本实用新型还公开了以下多种更加优化的具体结构:
22.为了便于安装并能够实现波发生器的高度调节功能以扩大适用范围,本实用新型所述谐波减速机动态装配用支撑驱动机构还包括工作台1、固定板3、电机安装板15、气缸19、底座21和接近开关2,横向的固定板3安装在横向的工作台1上,轴承安装板13安装在固定板3上,竖向的气缸19安装在底座21上,气缸19上部的活塞杆18的上端与电机安装板15的下端连接,所述伺服电机安装在电机安装板15上,工作台1和固定板3分别设有用于电机安装板15以及所述伺服电机的转轴14穿过的竖向通孔,工作台1的下方安装有接近开关2,电机安装板15的一侧安装有与接近开关2配合的接近件4,接近件4的具体材质和形状根据接近开关2的具体类型而定,比如可以为金属、遮光板等,接近开关2的信号输出端与所述控制器的信号输入端连接,气缸19的控制输入端与所述控制器的控制输出端对应连接。
23.为了实现对伺服电机移动的精确导向功能并避免因气缸19的活塞杆18与伺服电机的转轴14不同轴导致部件损坏的问题,所述谐波减速机动态装配用支撑驱动机构还包括浮动接头17、导向柱16和直线轴承5,气缸19上部的活塞杆18的上端与浮动接头17的下端连接,浮动接头17的上端与电机安装板15的下端连接,两个竖向的导向柱16的下端分别通过支承座20与底座21连接并位于气缸19的相对两侧,两个导向柱16的上端分别与固定板3连接,两个直线轴承5分别套装在两个导向柱16上,电机安装板15的两侧分别设有连接板(图中未标记)并通过该两个连接板与两个直线轴承5连接,接近件4靠近其中一个导向柱16。
24.为了便于快速连接驱动轴11与波发生器10,驱动轴11的上端设有螺孔,安装螺钉由上而下穿过压紧板9的中心通孔后与驱动轴11的螺孔连接。
25.为了提高驱动轴11与伺服电机的转轴14之间的连接精度,驱动轴11的下端通过刚性联轴器12与所述伺服电机的转轴14连接。
26.如图1所示,利用本装置辅助装配谐波减速机的过程如下:
27.首先进行谐波减速机的组装:以滚子轴承8为基准,先将柔轮7与滚子轴承8装配好并用螺钉固定,调头装入波发生器10后将刚轮6放入,刚轮6的外止口与滚子轴承8的内止口对正,在刚轮6上装入与滚子轴承8连接的连接螺钉并使连接螺钉处于松驰状态。
28.然后将组装好的谐波减速机放在轴承安装板13的上面,并用螺钉将滚子轴承8与轴承安装板13连接好;通过控制器控制气缸19动作,使其活塞杆18上升,活塞杆18带动浮动接头17、电机安装板15、接近件4、伺服电机和驱动轴11同步向上移动,当接近件4靠近接近开关2时,控制器得到信号并控制气缸19停止,此时驱动轴11的上端穿过波发生器10的中心通孔并与其上表面齐平,将压紧板9置于驱动轴11的上方,并用螺钉由上而下穿过压紧板9的中心通孔后与驱动轴11上端的螺孔连接;然后通过控制器控制伺服电机启动,转轴14旋转并通过刚性联轴器12带动驱动轴11同步旋转,驱动轴11带动波发生器10旋转,波发生器10通过齿轮带动柔轮7和刚轮6旋转,其中刚轮6的转速因谐波减速机的减速比例而减小,在此过程中,刚轮6在转动过程中根据与柔轮7的配合情况,两者之间进行自适应的相对位置调整,以达到柔轮7的齿面与刚轮6的齿面啮合的最佳状态;当柔轮7与刚轮6的啮面达到最佳适应位置后,此时波发生器10仍然以100rpm/min的速度转动,根据谐波减速机的减速比特性,此时刚轮6的转速只有每分钟几转,相当缓慢,在此种情况下对刚轮6上的连接螺钉分2次进行拧紧,第一次以规定力矩1/2左右的力实施暂时拧紧,然后再按照规定力矩拧紧,在确保连接螺钉的扭力值达到规定要求后,控制伺服电机停止,取下压紧板9和对应螺钉,再次启动气缸19使其活塞杆18向下移动直到复位,再取下谐波减速机,完成谐波减速机的高精度、高效率装配。
29.上述实施例只是本实用新型的较佳实施例,并不是对本实用新型技术方案的限制,只要是不经过创造性劳动即可在上述实施例的基础上实现的技术方案,均应视为落入本实用新型专利的权利保护范围内。