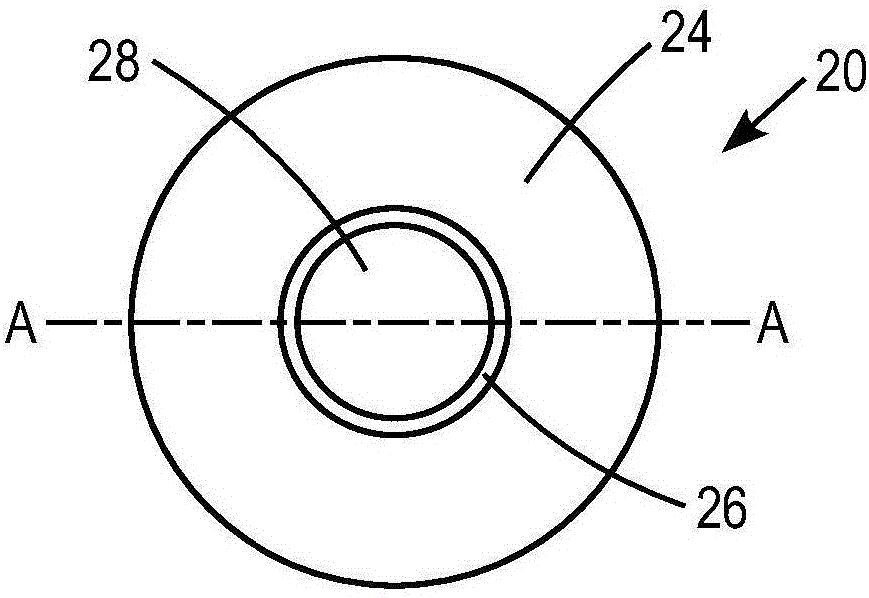
一种多晶金刚石复合片、切割件及制造切割件的方法技术领域本发明涉及在复合片切割器中使用的多晶金刚石(PCD)及其复合片切割器。PCD复合片切割器通常包括由基底或柱材或支柱支撑或者与基底或柱材或支柱连贯接合的金刚石层或片。具体地,本发明涉及如下的PCD,该PCD具有由在烧结之前并入PCD中作为金刚石内连续或分散块的金属或金属化合物连续结构例如本体金属箔制成的薄金属层。本发明还涉及制造所述金刚石的方法,和制造包括所述金刚石的复合片切割器的方法。
背景技术:在下文的背景技术探讨中,提到某些结构和/或方法。然而,下文提及某些结构和/或方法不应该被视为是承认这些结构和/或方法构成现有技术。申请人明确地保留证明这些结构和/或方法并不构成现有技术的权利。现用的切割器包括通常由碳化钨制成的基底、柱材或支柱支撑的或者与所述基底、柱材或支柱连贯接合的PCD层或片。碳化钨由于其优异的机械性质如耐磨性和抗压强度而通常被选择用于所述基底。在金刚石层在高温高压(HPHT)下的烧结阶段期间,通常发生金刚石层与基底的粘结。烧结的PCD层由具有大量直接金刚石-金刚石结合或接触的金刚石粒子作为主相构成。在例如三元晶粒袋或晶界的金刚石粒子间隙中,存在还被称为金属相或催化剂溶剂相的粘结相。该二次相也形成与金刚石网络混合的网络。该粘结相充当金刚石-金刚石结合生长的催化剂或溶液。粘结相通常包括至少一种活性金属,例如但不限于钴(Co)、镍(Ni)和铁(Fe)。其它的次生相通常在粘结相中或在粘结相与金刚石粒子之间形成。这些相可以包括在烧结处理期间形成的金属碳化物。这些相可形成隔离岛并嵌入粘结相中而没有明显的边界,这可增加在金刚石片内的裂隙扩展。通常用于烧结现用切割件的方法是HPHT法,其实例显示在图11和图12中。具体地,该方法包括将金刚石粒子112和任选的烧结助剂114加入金属容器110中。然后,将通常是碳化钨(WC)的碳化物支柱118插入金属容器110中与包括任选烧结助剂的金刚石进料116接触。使包括容器110、金刚石进料116和碳化物支柱118的组合件120经受HPHT处理。在HPHT处理期间,最初存在于碳化物支柱中的粘结剂将由于高温124和高压122而熔化并被挤压到金刚石复合片中。粘结相的流动也称为掠过,这是由于如下事实,即,熔化的粘结剂(箭头126代表熔化的粘结剂的方向)在渗透的同时将形成前锋面128,其将粘结剂和其它材料从支柱带入金刚石进料中。当金刚石被移位的粘结相浸没或包围时,经由溶液-输送-再沉淀的液体烧结机理发生金刚石烧结。在此,形成金刚石-金刚石结合且构造了金刚石网络。因此,在烧结之后,形成具有在界面处粘结在一起的金刚石层102和碳化物支柱104的复合片100。来自支柱的粘结剂也将一定量的溶解物质从支柱带入金刚石层中。所述物质的量很大程度上取决于压力和温度。粘结剂携带的物质包括例如钨和碳。溶解的钨将与溶剂金属和/或来自金刚石进料和碳化物支柱的碳反应。取决于压力、温度和组成,在工艺完成时,反应产物可以作为固溶体物质保留在粘结相中或在冷却到室温之后作为基于碳化物的相沉淀出来。该粘结相及其它沉淀的次生相保留在在晶粒之间的烧结金刚石层中且形成网络。另外,在钻孔应用中,PCD切割器经受可能导致切割器碎裂和开裂的高冲击负载。开裂源于在高应力点处产生的微裂隙。如果这些裂隙到达在PCD内的较韧相,则它们可以被偏转或阻止,由此改进PCD的冲击韧性。已经提出了几种方法来提供该改进的冲击韧性。例如,美国专利6,974,624公开了PCD-WC复合切割器,其中PCD被包在蜂巢状WC壳中。另外,欧洲专利0699642公开了用纤维强化PCD以改进冲击韧性。如果纤维经受得住烧结处理,则它们在PCD内充当韧性相且阻止或偏转在PCD内的裂隙。然而,没有一种现有技术解决了用于在烧结处理期间形成的切割器的常规金刚石层的所有缺点。
技术实现要素:所公开的制造方法至少通过在烧结之前在PCD中并入由金属或金属化合物的连续结构例如金属箔制成的薄金属层来制造具有改进的冲击韧性和抗断裂性的PCD和含有所述PCD的切割器。本发明的第一方面包括金刚石复合片,其包括至少两个由至少一个金属碳化物箔部分所分隔的多晶金刚石(PCD)部分。本发明的第二方面包括切割件,其包括基底和金刚石片,该金刚石片包括至少两个多晶金刚石(PCD)部分和至少一个分隔两个金刚石部分的薄金属层部分。本发明的第三方面包括制造切割件的方法,其包括将金刚石粉末放置在反应容器中,将薄金属层放置在所述反应容器中在所述金刚石粉末和粘结剂上面或周围,将另外的金刚石粉末放置在所述反应容器中在所述薄金属层上面或周围,和将含有粘结剂的预烧结的基底放置到所述反应容器中在所有金刚石粉末和薄金属层组件上面。将组装的反应容器置于反应器中且使其经受高温高压(HTHP)烧结处理。应理解,上述的发明内容与以下的具体实施方式都是示例性和说明性的,并旨在提供所要求保护的本发明的进一步解释。附图说明可结合附图阅读下文的具体实施方式,在附图中,相同的附图标记表示相同的元件,且其中:图1显示根据本发明第一实施方式的切割器的透视图。图2A显示根据本发明第二实施方式的切割器的俯视图。图2B显示沿线A-A切开的图2A切割器的截面图。图3显示根据第三实施方式的切割器的透视图。图4A显示根据本发明第四实施方式的切割器的俯视图。图4B显示沿线B-B切开的图4A切割器的截面图。图5显示根据本发明第五实施方式的切割器的透视图。图6A显示根据本发明第六实施方式的切割器的俯视图。图6B显示沿线C-C切开的图6A切割器的截面图。图7显示根据本发明第七实施方式的切割器的截面图。图8显示根据本发明第八实施方式的切割器的截面图。图9为用于制造图1切割器的示例性组装步骤的图示。图10为用于制造图1切割器的示例性烧结步骤的图示。图11为用于制造现有技术切割器的组装步骤的图示。图12为用于制造现有技术切割器的烧结步骤的图示。图13显示根据本发明第九实施方式的切割器的截面图。图14A-14C为根据本发明第十实施方式的切割器的截面的照片。图15A-15B为根据本发明第十一实施方式的切割器的截面的照片。具体实施方式本发明公开了改进的多晶金刚石(PCD)和改进的切割器,该切割器含有所述改进的PCD作为其顶层或片。所述切割器可用作例如但不限于在刮刀钻头中使用的超硬磨料切割件。所述改进的PCD特别是包括较好的冲击韧性和抗断裂性,这可引起含有所述改进的PCD的切割器的寿命增加。在较好冲击韧性和抗断裂性方面的改进至少部分地归因于在烧结之前在金刚石层中添加至少一个薄金属层。含有所述改进的PCD的切割器的第一实施方式示出在图1中。切割器10包括基底12、第一金刚石层14、箔层16和第二金刚石层18。箔层16为在烧结之前分隔第一和第二金刚石层(14,18)的金属层。在烧结处理期间,粘结剂元素掠过至箔层16。随着粘结剂元素与金属层反应,该金属层转化成金属化合物。该反应过程允许粘结剂经金属箔移动且在该箔的另一侧继续掠过的过程。该反应过程的动力学和最终产物取决于参与该反应过程的元素和化合物。作为该反应过程的特定实例,其中溶解有碳的诸如钴的粘结剂将与钽箔反应以形成碳化钽。随着该反应进行,富钴反应前锋经钽箔前进且在其后沉积碳化钽。最后,富钴前锋将从箔的另一侧显露出来且继续掠过金刚石粉末。可以放置金属碳化物箔部分以使得在该金属碳化物箔部分的每侧上存在相同量的金刚石,或者可选地,可以放置金属碳化物箔部分以使得在该金属碳化物箔部分下面或上面的金刚石部分较大。在一些实施方式中,该箔层在烧结阶段期间充当过滤器。当粘结剂掠过箔时,溶解于粘结剂中的元素例如钨及其它添加剂将到达箔材料。它们在粘结剂中的浓度因此降低且随后PCD将具有减少量的沉淀物例如碳化钨,这可改进PCD的断裂韧性。另外,并入金刚石片中的所得金属/金属碳化物层提供具有较韧相的金刚石片,其可以偏转或阻止在高应力点处产生的微裂隙。通过偏转或阻止微裂隙,该箔层通过减少源于所述微裂隙的开裂而提供具有改进的冲击韧性的金刚石片。所述改进的冲击韧性和减少的开裂可以导致切割器寿命得到改进。在某些实施方式中,所述基底包括诸如碳化物的基底材料。示例性碳化物包括碳化钨、碳化钛或碳化钽或者其组合。用作基底的特定碳化物为碳化钨。所述基底还可以包括较小百分数的添加剂例如立方碳化物,例如碳化铌、碳化钒、碳化铪、碳化铬和碳化锆。所述基底还包括随所述基底材料并入的粘结剂。在与切割器的其它层组装和烧结之前,将基底预成型至由基底材料和粘结剂形成的烧结支柱中,并压成所要的支柱形状。在烧结阶段期间,一些来自烧结支柱的粘结剂将掠过进入金刚石层和薄金属层中。所述粘结剂元素可以为本领域中已知作为PCD和基底材料用粘结剂的任何元素,包括例如碳化物。示例性粘结剂元素包括金属例如钴、镍、铁,或含有这些金属中的一种或多种的合金,以及准金属例如硅。在某些实施方式中,所述粘结剂元素包括钴。所述粘结剂元素还可以包括在碳化物和/或超硬磨料材料的粘结相中使用的任何已知添加剂。添加剂可包括选自第IVB至VIIIB族的过渡金属,例如铬、钼、镁、钒、钛、锆、铪、铌或钽或者其组合。在某些实施方式中,所述添加剂可包括铬、钼或钒或者其组合。所述薄金属层包括过渡金属,所述过渡金属例如包括难熔金属例如钽、钼、铌、钛、锆、钨、钒或铬或者其组合。难熔金属在烧结温度下不熔化且掠过金刚石。当将钴用作烧结支柱中的粘结剂材料时,所述金属的选择可取决于在烧结温度下其与钴的反应速率。在某些实施方式中,所述薄金属层包括例如钽、钼、铌或锆或者其组合。用作薄金属层的特定金属为钽。所述薄金属层可以是连续薄片例如金属箔,或者其可以由金属粉末形成。在使用金属粉末的情况下,所述粉末可以在烧结之前与压制剂混合并在放置于金刚石进料中之前压制成所要形状。所述压制剂可以包括通常用于形成金属粉末生坯的任何粘结剂材料。示例性压制剂包括蜡或聚乙二醇(PEG)。所述压制剂在烧结之前被烧掉。在某些实施方式中,所述薄金属层和所得金属碳化物箔具有约.00001至约0.010英寸的厚度。在更特定的实施方式中,所述厚度为约0.0005至约0.005英寸。在更特定的实施方式中,所述厚度为约0.001至约0.002英寸。图2A-8和13-15B示出了在金刚石部分之间具有金属碳化物箔部分的不同构造和布置的其它实施方式。上述薄金属层、基底或金刚石部分的组成或尺寸的任何描述同样适合以下描述的实施方式中的任一个。图2A和图2B示出了切割件的第二实施方式。切割件20包括基底22、第一金刚石部分24、金属碳化物箔部分26和第二金刚石部分28。第一金刚石部分24与基底22直接接触且包围金属碳化物箔部分26,金属碳化物箔部分26进一步包围第二金刚石部分28。在烧结期间的该构造中,在基底22中的熔化粘结剂掠过整个第一金刚石部分24且开始与薄金属层反应,直到该薄金属层转化成金属碳化物。在形成金属碳化物之后,熔化的粘结剂能够穿过箔部分以开始烧结第二金刚石部分28。金属碳化物箔部分26充当过滤器,以使得与第一金刚石部分24相比,较少基底粒子到达第二金刚石部分28。另外,金属碳化物箔部分26使金刚石部分变坚韧且减少裂隙的扩展。图3示出了切割件的第三实施方式。切割件30包括基底32、第一金刚石部分34、第一金属碳化物箔部分35、第二金刚石部分36、第二金属碳化物箔部分37和第三金刚石部分38。类似于第一实施方式,在烧结阶段期间,来自基底32的熔化粘结剂掠过第一金刚石部分34,然后与第一薄金属层反应。然后,在转化成金属碳化物之后,熔化粘结剂掠过第一金属碳化物箔部分35以烧结第二金刚石部分36,之后与第二薄金属层接触并反应。然后,在转化成金属碳化物之后,熔化粘结剂掠过第二金属碳化物箔部分37以烧结第三金刚石部分38。在另外的实施方式中,可以使垂直交替的金刚石部分和金属碳化物箔部分重复,以使得存在多于三个金刚石部分和多于两个金属碳化物箔部分。在又另外的实施方式中,存在五个或更多个金刚石部分和四个或更多个金属碳化物箔部分。在还另外的实施方式中,可以加入任何数量的金刚石部分和金属碳化物箔部分。实际数量可以受切割件的尺寸以及单个部分的厚度限制。在存在多于一个金属碳化物箔部分的任何实施方式中,所述多个金属碳化物箔部分可以全部相同,全部不同,或者其组合。金属碳化物箔部分在尺寸、形状或组成方面可以不同,其包括在箔中使用的金属方面或者在加到所述金属中的添加剂或压制剂方面的不同。另外,可以放置所述金属碳化物箔部分以使得在各金属碳化物箔部分的每侧上存在相同量的金刚石,或者可选地,可以放置所述金属碳化物箔部分以使得在各金属碳化物箔部分下面或上面的金刚石部分较大。图4A和图4B示出了切割件的第四实施方式。切割件40包括基底42、第一金刚石部分44、第一金属碳化物箔部分45、第二金刚石部分46、第二金属碳化物箔部分47和第三金刚石部分48。将所述金刚石部分和金属碳化物箔部分嵌套以使得来自第一金刚石部分至第三金刚石部分的每部分包围后一部分。该嵌套通过形成薄金属层杯而实现,所述薄金属层杯放置在先前布置的金刚石粉末内,其中后加入的金刚石粉末被加到该薄金属层杯中。以此方式,类似于第二实施方式,在烧结期期间,来自基底42的熔化粘结剂掠过第一金刚石部分44以形成包围第一薄金属层的烧结的金刚石部分。熔化的粘结剂一到达第一薄金属层且与其反应以形成第一金属碳化物箔部分45,熔化的粘结剂就穿过第一金属碳化物箔部分以烧结第二金刚石部分46。熔化的粘结剂一到达第二薄金属层且与其反应以形成第二金属碳化物箔部分47,熔化的粘结剂就穿过第二金属碳化物箔部分47以烧结第三金刚石部分48。在另外实施方式中,可重复填充有金刚石部分的金属碳化物箔部分的嵌套以使得存在多于三个金刚石部分且存在多于两个金属碳化物箔部分。在又另外的实施方式中,所述嵌套可包括五个或更多个金刚石部分和四个或更多个金属碳化物箔部分。在还另外的实施方式中,可以嵌套任何数量的金刚石部分和金属碳化物箔部分。实际数量可以受切割件的尺寸以及单个部分的厚度限制。根据上述第四实施方式包括金刚石和金属碳化物箔部分的嵌套的实施方式,可如在图4A和4B中所示的进行嵌套,其中金刚石部分在除顶面之外的所有侧面上被包围。可选地,所述金刚石部分可以被由金属碳化物箔部分分隔的外部金刚石部分完全包围。虽然上述嵌套通过形成杯形的金属碳化物箔部分示出,但包围金刚石部分的任何形状可以替代所图示的杯形。并且各杯的尺寸或在所述金属碳化物箔部分与内部金属碳化物箔部分之间的各金属碳化物箔部分的内部体积,对于各内部金属碳化物箔部分可保持相等、逐渐变小或变大或者其组合。图5示出了切割件的第五实施方式。切割件50包括基底52、第一金刚石部分54、金属碳化物箔部分56和第二金刚石部分58。在该实施方式中,金属碳化物箔部分56靠近金刚石基底界面放置以使得在切割件中的大部分金刚石存在于第二金刚石部分58中,其基于金属碳化物箔部分56的过滤功能而含有较少基底粒子。图6A和6B示出了切割件的第六实施方式。切割件60包括基底62、第一金刚石部分64、第一金属碳化物箔部分65、第二金刚石部分66、第二金属碳化物箔部分67和第三金刚石部分68。在该实施方式中,第一金属碳化物箔部分65类似于第一实施方式、第三实施方式和第五实施方式为平面的,而第二金属碳化物箔部分67具有类似于第二实施方式和第四实施方式的杯形。上文对于前五个实施方式阐明的所有可选方案也可用于该实施方式,例如包括,所述切割件可以含有多个平面的金属碳化物箔部分和/或多个包围内部金刚石部分的金属碳化物箔部分。图7示出了切割件的第七实施方式。切割件70包括基底72、第一金刚石部分74、金属碳化物箔部分76和第二金刚石部分78。在该实施方式中,存在类似于第二实施方式的包围金属碳化物箔部分。然而,与第二实施方式相反,该金属碳化物箔部分位于切割件的一侧而不是中心。第二金刚石部分位于切割件的一侧,可提供具有第二金刚石部分的优点的切割件的切割刃,其中将接合切割件的顶部和周面的边缘用作切割刃。在另外的实施方式中,包围金属碳化物箔部分的其它位置可以根据切割件的预定用途来选择。例如,可以基于在切割件使用期间可能引起裂隙扩展的内力来确定布置。图8示出了切割件的第八实施方式。切割件80包括基底82、第一金刚石部分84、第一金属碳化物箔部分85、第二金属碳化物箔部分86、第二金刚石部分87和第三金刚石部分88。在该实施方式中,存在两个类似于第七实施方式的包围金属碳化物箔部分。第一金刚石部分84与基底82直接接触,而第一金属碳化物箔部分85在切割件的一侧上包围第二金刚石部分87,且第二金属碳化物箔部分86在切割件的相对侧上包围第三金刚石部分88。该实施方式提供上文对于第七实施方式所描述的许多优势。另外,由于具有多于一个由金属碳化物箔部分包围的金刚石部分,该切割件能够利用在切割件相对侧上的有利金刚石部分转位。在另外的实施方式中,为了另外的可转位性,可在切割件的不同侧上形成多于两个包围金属碳化物箔部分。在又另外的实施方式中,可在切割件的不同侧上形成四个或更多个包围金属碳化物箔部分。在还另外的实施方式中,可在相对于切割件的不同侧、中心或任何其它位置形成包围金属碳化物箔部分。所述位置可特别是基于切割件的尺寸和形状来确定,其中具有较少基底粒子的金刚石部分是所希望的,且其中帮助防止裂隙扩展的金属碳化物箔部分是最有用的。还预期上述实施方式的组合。例如,一个或多个平面的金属碳化物箔部分可以分布在包围金属碳化物箔部分内。同样,例如,一个或多个平面的金属碳化物箔部分可以分布在包围金属碳化物箔部分的下面或上面。另外,例如,嵌套和未嵌套的包围金属碳化物箔部分的组合可以分布在切割件的整个金刚石层中。在另外的实施方式中,没有基底的金刚石复合片可以以与如上文对于包括基底的切割件类似的方式形成。单独的金刚石复合片可以如上所述形成,其后是除去基底的步骤。可选地,所述金刚石复合片可以以如上所述的类似的方法形成,只是没有将基底放置于反应容器中。相反,单独的粘结剂元素将在烧结期间熔化并掠过进入金刚石粉末中且如上所述与金属箔反应。上文描述的所有元素和实施方式也可以适合于不与基底连接的金刚石复合片。图9和10示出了用于形成根据至少第一实施方式的切割件的示例性方法。图9示出了包括获得反应容器如金属杯90的组装步骤的图示。将第一金刚石粉末92与任选第一烧结助剂93一起放置到金属杯90的底部。在该情况下形成平面片材形式的薄金属层94。虽然如上所解释的,但该薄金属层可以是杯形或可包围物体的其它形状。薄金属层94可以是连续的金属片材或与压制剂混合的金属粉末以形成连续的片材。薄金属层94放置在金属杯90中,以分隔第一金刚石粉末和任选第一烧结助剂与放置薄金属层94之后加入的第二金刚石粉末96和任选第二烧结助剂97。一加入所有薄金属层和金刚石层,就将包含硬质材料和粘结剂材料的预烧结的基底98放置于金属杯90中,以形成最后的组合件100。所述基底的特定界面模式可被设计成减轻在HPHT处理之后的残余应力。这种界面模式的实例示出在图9中。图10示出了烧结步骤的图示。将最后的组合件100放置于HPHT烧结设备中,以便施加足以烧结金刚石部分且使金刚石部分与基底整体粘结的热102和压力101。在特定的实施方式中,所述HPHT烧结处理使组合件100经受约40至约75千巴的压力和约1300℃至约1700℃的温度。在某些实施方式中,所述压力为约55至约70千巴,且所述温度为约1430℃至约1630℃。在所述烧结处理期间,存在于预烧结的基底98中的熔化粘结剂掠过进入第二金刚石粉末96中。移位的熔化粘结剂104在图10中由箭头和移动线表示。在熔化粘结剂穿过第二金刚石粉末的同时,第二金刚石粉末被烧结且变成第二金刚石部分105。熔化粘结剂一到达薄金属层94,其就与该金属反应以形成金属碳化物箔106。在形成金属碳化物箔106之后,熔化粘结剂能够穿过第一金刚石粉末92。在熔化粘结剂穿过第一金刚石粉末的同时,第一金刚石粉末被烧结且变成第一金刚石部分。通过所述方法形成的完全烧结的切割件108类似于第一实施方式的切割件10,其包括例如相同的组分。在上述方法中,所述反应容器可以包含钼、铌、钽、钒、铪或钨或者其组合。在某些实施方式中,所述反应容器由与所述薄金属层相同的金属形成。可选地,所述反应容器可以由与所述薄金属层不同的金属形成。在一些实施方式中,所述反应容器具有双杯设计。双杯设计通过较好地保持其形状且较好地避免在反应器元素与用以形成切割件的材料之间的有害反应而具有改进的保持其完整性的能力。在另外的实施方式中,所述金属容器具有厚度例如为约0.003至约0.01英寸的厚壁,以更有效地经受金属磨蚀和/或抵抗开裂。图13示出了切割件的第九实施方式。切割件130包括基底132、第一金刚石部分134、金属碳化物箔部分136和第二金刚石部分138。在该实施方式中,金属碳化物箔部分136形成包围第二金刚石部分138的袋。图14A-C为根据本发明第十实施方式的切割件的照片。图14A显示切成两半的切割件,其中这两半的顶面彼此面对。该切割件与第九实施方式的类似之处在于,在第一金刚石部分内发现形成袋的金属碳化物。该袋包围第二金刚石部分。图14B为图14A切割件在较高水平放大倍数下的视图。图14C处于更高的放大倍数下且仅显示图14A切割件的两半之一的一部分。更高放大倍数的图14C明确显示,第一金刚石部分含有精细的金刚石粒子,而第二金刚石部分含有较粗糙的金刚石粒子。所述金刚石粒子差异由形成包围第二金刚石部分的袋的金属碳化物箔层引起。图15A和15B为根据本发明第十一实施方式的切割件的照片。图15A显示切成两半的切割件,其中这两半之一的顶面向上。图15A的切割件类似于图1的实施方式。在图15A中,在照片底部部分上的略白色为基底,紧靠在基底上面的灰色部分为第一金刚石部分,薄白色层为金属碳化物箔部分,且在该金属碳化物箔部分上面的第二灰色层为第二金刚石部分。在该照片顶部的暗灰色部分只是在其上拍摄该切割件的背景,而不是切割件的一部分。图15B提供图15A切割件的较高放大倍数的照片。较高放大倍数的图15B明确显示,与第二金刚石部分相比,第一金刚石部分含有较多的白点。在所述金刚石部分内的白点为碳化钨。该碳化钨由溶解于在基底中的钴粘结剂中的钨所沉淀。随着熔化钴在烧结期间从第一金刚石部分移动到第二金刚石部分,其必须穿过在中间的钽箔。在第二金刚石部分中的白点存在明显不同,这显示出,随着钴穿过钽箔,钨被“滤出”。虽然结合本发明的优选实施方式进行了描述,但本领域技术人员应该理解,在不背离如所附权利要求书所限定本发明的主旨和范围的情况下,可进行本说明书没有具体描述的添加、删除、改进和替换。