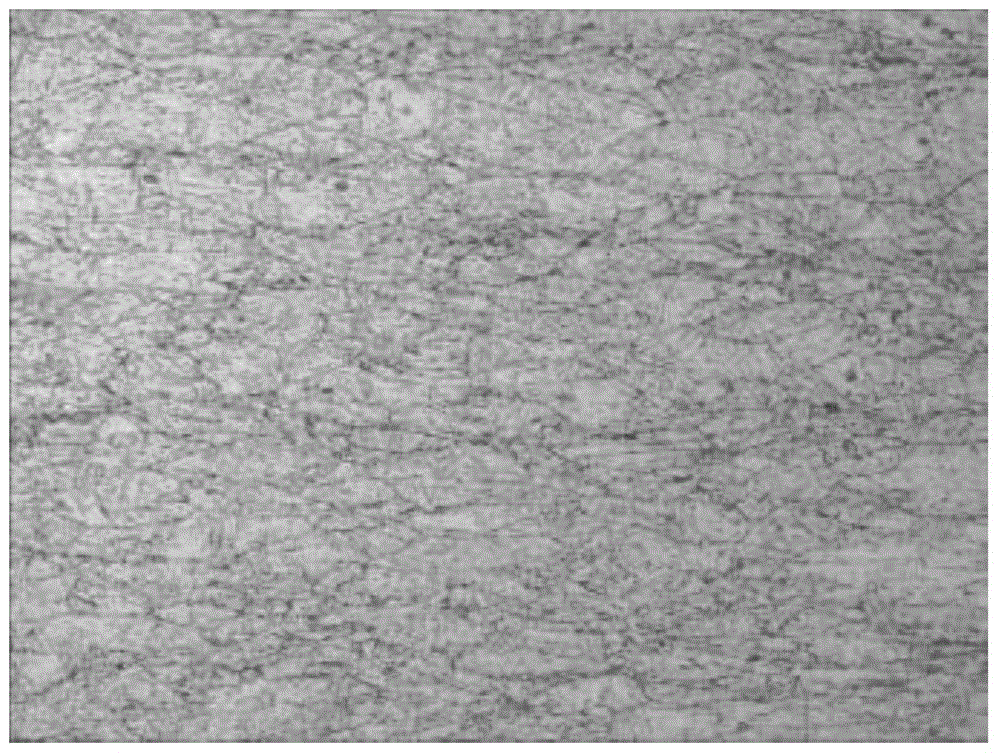
本专利属于高强度焊接结构钢技术领域,特别是涉及一种高Ti700MPa级工程机械用宽厚钢板及生产方法。
背景技术:在工程机械和钢结构领域,近年来对低屈强比的高强度钢板需求量逐渐增加,同时对钢板的焊接性能、冷加工性能等提出了更高的要求。Ti是低合金高强度钢中的重要微合金元素之一。根据添加的Ti含量一般分为三类:微Ti含量(0.010%-0.020%),中等Ti含量(0.020%-0.040%),高Ti含量(0.040%-0.15%)。微Ti含量重要用于钢的微Ti处理工艺,对于改善钢坯质量,限制加热过程奥氏体晶粒长大,改善低温韧性等方面具有良好的作用。中等Ti含量主要用于优化焊接过程中TiN的析出物的尺寸和分布,改善焊接热影响区低温韧性。高Ti含量主要通过TiC粒子和Ti(C,N)粒子在不同阶段的沉淀析出改善钢板的组织和性能。具体可以表现为:(1)加热过程高温奥氏体化时稳定的TiN和Ti(C,N)粒子,抑制奥氏体的过分长大;(2)高温轧制过程中TiC和Ti(C,N)粒子的形变诱导析出,细化奥氏体再结晶晶粒,在相同的变形量和变形温度的条件下获得更为细小的再结晶晶粒;(3)轧后奥氏体/铁素体相变过程TiC粒子的相间沉淀以及后续TiC在铁素体相中的过饱和析出的沉淀强化作用。钛化合物稳定性递减顺序为TiN→Ti4C2S2→Ti(CN)→TiC,即当钛量较低时,几乎全部用于形成TiN(ω(Ti)≈3.4×ω(N)),不能形成Ti4C2S2,钢中的硫以MnS形态存在。而当钛量增加超过3.4×ω(N),开始形成Ti4C2S2。此时MnS与Ti4C2S2并存.当钛含量增加到可将钢中的氮和硫元素全部被固定时,即ω(Ti)=3.4ω×(N)+3×ω(s)时,MnS将全部被Ti4C2S2所代替,此时钛的析出强化作用很小。当钛含量继续增加时,多余的钛将形成TiC,TiC粒子在相间或相变后在铁素体内析出.其尺寸非常细小(10nm以下),能产生强烈的沉淀强化效果。因此高Ti强化的钢板其强化效果决定于钢中高温时固溶Ti的含量,称之为有效Ti含量(有效Ti含量可以使用以下公式进行估算,Tieff=Tit-3.42×N-3×S,公式中各元素采用重量百分比带入)。目前Ti作为主要强化合金元素添加的工艺大多数是使用在热连轧过程中,在中厚板的成分设计中作为主要的合金元素来使用的鲜有报道。如申请号为CN200610123458.1、CN200910038833.6、CN201010034472.0、CN201210567654.3的专利中均报道了一种使用Ti作为主要合金元素,采用热连轧+高温卷曲技术生产高强度热轧卷板的技术。涉及高强度耐候钢板、高强度双相钢、高强度汽车板以及工程机械用钢板等领域。申请号为CN200710031549.7和CN200710032112.5的专利分别给出了700MPa和550MPa级别钢板Ti加入量的确定方法。是基于热轧卷板生产工艺建立Ti加入量、杂质元素含量与钢板强度之间的经验公式。公开号为CN102676927A的专利中给出了一种高Ti微合金化中厚板及其制备方法。其中其Mn含量为0.30-1.80wt%,与本专利中的Mn元素含量有明细差异。
技术实现要素:本发明的目的在于提供一种高Ti700MPa级工程机械用宽厚钢板及生产方法,采用Ti替代目前钢中常用的Nb元素,利用其与Nb类似的形变诱导析出作用促进再结晶过程中钢的原奥氏体晶粒细化;同时采用Ti的析出物作为主要强化元素利用析出强化提高钢的强度。本发明中所涉及到的高Ti含量700MPa级工程机械用宽厚钢板的化学成分为:C:0.04~0.09%,Si:0.05~0.40%,Mn:1.80~2.30%,P:≤0.013%,S:≤0.003%,Ti:0.06~0.13%,N:≤0.0050%;余量为Fe及不可避免的杂质。本发明中的各元素作用碳(C):C作为间隙原子,在钢中强化明显固溶强化作用,可以显著提高钢的强度,但较高的C含量损害钢的低温冲击韧性和焊接性能。C可以与钢中的Mo、V、Nb、Ti等元素形成析出物,通过析出强化提高钢才强度。在强水冷条件下,C可以提高钢的淬透性,得到高强度的马氏体组织。本发明中C元素的主要作用是与固溶的Ti元素结合,在奥氏体/铁素体相变过程中生成TiC粒子,考虑到钢的低温韧性和焊接性能,碳含量范围设定为0.04~0.09%。硅(Si):Si是作为脱氧剂加入钢中的,固溶的Si原子可以明显提高铁素体的强度,但Si含量提高会明显降低HAZ区韧性。因此本钢种Si含量设定为0.05~0.40%。锰(Mn):Mn元素在钢中具有一定的固溶强化作用,在低碳钢中当Mn含量达到1.8%以上时,可以明显促进针状铁素体、准多边形铁素的生成。本发明中Mn含量设定为1.80~2.30%。钛(Ti):Ti是本发明中的最为重要的合金元素,在本设计中形变诱导析出和奥氏体/铁素体转变过程中相间沉淀的TiC粒子作为主要的析出强化因素。当Ti含量较高时,除去高温区与生成的TiN、Ti4C2S2、Ti(C,N)粒子外,剩余固溶的Ti在较低温度形变过程中以TiC的形式在形变带内部析出(30-50nm),可以抑制钢的再结晶晶粒长大从而提高钢板未再结晶温度,促进奥氏体扁平化。在奥氏体到铁素体相变过程中TiC在铁素体中的固溶度降低,在相变过程中奥氏体/铁素体相界面前沿TiC粒子呈点状析出(<10nm),TiC析出物见图1。由于钢中的Ti与N、S等元素结合力强,高温下已经形成氮化物和硫化物的Ti元素在后续过程中无法转变为有用的TiC粒子,因此钢中的实际Ti含量和起到强化作用的有效Ti含量之间存在以下关系,(Tieff=Tit-3.42×N-3×S,公式中各元素采用重量百分比带入)。钢中S元素典型含量约为0.0020%,N元素典型含量约为0.0040%,通过公式可知Tieff=Tit-0.02(%),同时考虑到铁素体中约有0.02%的Ti无法形成TiC析出,且TiC形式析出的Ti需要达到0.02%以上时才能有较好的析出强化作用,因此钢中的Ti含量添加必须大于0.06%。同时Ti含量达到0.13%时,TiC析出量过多导致钢中的析出强化强烈,显著降低钢板的韧性。因此此设计中Ti的含量为0.06-0.13%。磷(P):P为钢中主要杂质元素之一,P含量的增加会显著降低钢的塑性和焊接性能,因此对于高强度等级钢板其P含量大多控制在0.013%以下。硫(S):S在通常的钢中会与Mn结合形成MnS夹杂物,在高Ti含量的钢中在高温时先于Mn与Ti结合形成Ti4C2S2粒子,从而降低钢中有效Ti的含量。因此本设计中S含量≤0.003%铝(Al):Al是钢中的主要脱氧元素,与N元素结合所得到的AlN颗粒可以细化奥氏体晶粒尺寸。但钢中的AlN也是主要的夹杂物来源之一,因此Al含量一般控制在0.04%以下。氮(N):N在钢中与Ti、Al等元素结合形成氮化物,成为夹杂物的来源之一,降低钢的韧性。本设计中由于添加的Ti含量明显高于普通钢种,形成大颗粒TiN粒子的几率明显提高,因此本设计中N含量需要控制在0.005以下。本发明的生产工艺及其控制的技术参数如下:(1)冶炼工艺采用铁水脱硫→转炉冶炼→LF精炼→RH精炼工艺路线。严格控制板坯成分C:0.04~0.09%,Si:0.05~0.40%,Mn:1.80~2.30%,P:≤0.013%,S:≤0.003%,Ti:0.06~0.13%,N:≤0.0050%。本发明通过严格控制Ti合金的添加时机,控制钢水N含量,抑制在钢液凝固过程中生成的大颗粒TiN粒子。本发明通过严格控制S含量,使硫化物夹杂降低到较低水平,再通过合理的Ca/S比,使剩余的少量硫化物夹杂球化。本发明中Ca/S为1.5-2之间。执行LF精炼以及RH精炼,RH处理时间21min-23min,深真空时间≥18min,严格控制钢中[H]和[N]含量,保证钢液洁净度。(2)板坯加热工艺采用连铸坯生产,板坯加热1150~1220℃,保温时间3~6小时,既保证Ti合金可以充分固溶。(3)轧制工艺采用再结晶区和未再结晶区两阶段轧制。第一阶段为再结晶区轧制,开轧温度1050℃~1150℃,保证第一阶段轧制单道次压下率逐渐增加,且最后三道次压下率为25%-35%总压下率大于60%,终轧温度保证在完全再结晶温度以上。一阶段轧制通过反复大压下量变形,充分利用形变诱导析出和大变形量的交互作用细化高温奥氏体晶粒。第二阶段为未再结晶区轧制,开轧温度低于奥氏体未再结晶温度,且终轧温度高于铁素体析出温度。对于本专利开轧温度840℃~870℃,终轧温度770~800℃,待温厚度为板厚的3~4.5倍,二阶段轧制压下率≥65%。精轧阶段的大压缩比变形,促进TiC在形变带内析出并抑制形变带的软化和亚晶晶粒长大;同时多道次变形在原有促进原有奥氏体中形成大量形变带,提高奥氏体内部缺陷密度,获得压扁的奥氏体晶粒从而提高铁素体相变形核率,如图2。(4)冷却工艺轧后钢板采用在线超快冷设备进行冷却,冷却速率20-25℃/s范围内,通过快速冷却工艺将钢板冷却至500-600℃的范围内,获得准多边形铁素体+针状铁素体的混合组织,如图3。LF精炼时间,保证钢中S含量控制在20ppm以下,RH深真空时间≥18min,保证钢中N含量控制在30ppm以下,控制钢中残余O含量在15ppm以下。保证钢中有效Ti含量(Tieff)不低于0.06%(Tieff=Tit-3.42×N-3×S,公式中各元素采用重量百分比带入)。本发明通过精确控制Ti含量,结合热机械轧制及在线超快速冷却技术,无需通过后续热处理,获得优异的力学性能的700MPa级别10-40mm规格宽厚钢板,其抗拉强度(Rm)700-750MPa,屈服强度(Rp0.2)580-630MPa,-20℃冲击功≥220J,-60℃冲击功≥170J,韧脆转变温度≤-75℃,铁素体晶粒度评级结果≥13级,屈强比≤0.86。本发明的生产的钢板具有良好的低温冲击韧性和良好的焊接性能;钢板进行斜Y冷裂纹敏感性和HAZ最高硬度试验,表明钢板在0℃时仍然具有良好的焊接工艺性能。本发明的有益效果:仅采用经济的Ti为主要的合金元素,通过合理的轧制和快速冷却工艺,获得良好的组织与析出物的匹配,从而降低钢的碳当量、良好的焊接性能,同时降低了钢板的生产成本。附图说明图1为1#钢中不同阶段获得的TiC粒子。图2为2#钢所获得的原奥氏体组织。图3为2#钢所获得的准多边形铁素体+针状铁素体的混合组织。具体实施方式依照本发明的生产方法生产的钢板的实施例如以下各表。表1为本发明实施例钢的化学成分,表2为本发明实施例的工艺条件,表3为本发明实施例的力学性能,表4为本发明实施例的抗氢制开裂性能。表1实施例化学成分,wt%实施例规格/mmCSiMnPSAlsolTiCEQN/ppm1160.0750.211.950.0100.0030.0230.0590.40262250.0770.281.890.0130.0030.0290.0790.39283300.0810.231.970.0090.0020.020.1010.4133表2实施例的工艺条件按照GB/T228和GB/T229测定本发明实施例的屈服强度为586MPa~610MPa,抗拉强度为707MPa~735MPa,延伸率>18%,-20℃冲击功≥220J,-60℃冲击功≥170J,具有良好的强度和韧性匹配。分别按照GB4675.1-84《斜Y坡口焊接裂纹试验方法》和GB4675.5-2008《焊接性试验—焊接热影响区最高硬度试验方法》对钢板进行焊接冷裂纹敏感性和最高硬度试验。同时根据焊接评定结果对实际钢板实施对焊试验,并测量焊接接头的力学性能。表4为1#钢板的焊接评定试验工艺参数设置;表5为焊接评定试验结果;表6为对焊试验的工艺参数;表7为焊接接头的力学性能检测结构。通过试验表明钢板具有良好的焊接性能。表3本发明实施例的力学性能表4本发明1#实施例的焊接评定工艺参数表5本发明1#实施例的焊接评定试验结果表6本发明1#实施例的实际钢板焊接工艺参数表7本发明1#实施例的实际钢板焊接接头力学性能