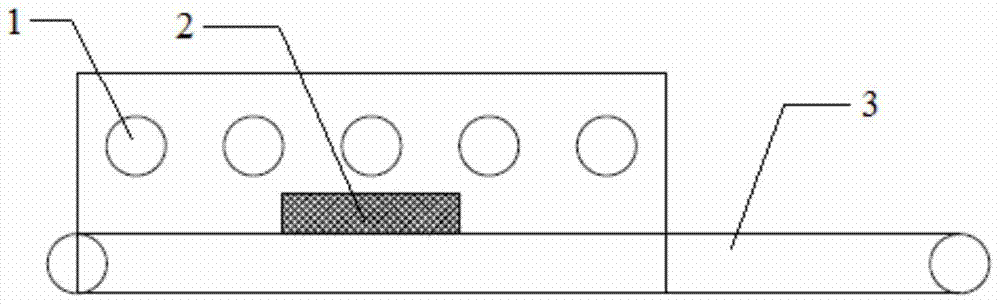
一种镁合金淬火-时效一体装置技术领域本发明涉及一种镁合金淬火-时效一体装置,主要用于大截面尺寸的变形稀土镁合金的淬火。
背景技术:镁合金作为最轻的结构金属材料,越来越多地应用于航空航天及汽车工业领域当中。目前,铸造镁合金的用量远大于变形镁合金,其主要原因在于铸造镁合金具有良好流动性能,易于成形,因此也是镁合金最大的应用领域。不过,传统铸造镁合金具有其先天的弱点,就是铸造缺陷较多,强度较低,性能差异较大,不能作为大型承力构件来使用,虽然近些年开发出了较多的精密成形手段,但是作为大型结构材料而言,精密程度及制造装备远没有达到需求,因此,现阶段,铸造镁合金的发展遇到了瓶颈。相比而言,变形镁合金具有非常优异的性能,如多样稳定的力学性能,较好的耐蚀性能等。近年来,由于国家对镁合金的大力支持,使得新型合金的开发与应用获得重视,随之而来的是工程化过程中实际问题的凸显,比如变形稀土镁合金,在整个过程中常见的问题有大型铸锭熔炼过程中的元素偏析、铸锭凝固收缩开裂、塑性变形失效、在线余热淬火应力开裂以及残余应力导致的加工变形等。这些问题在实验室阶段均可以很好的被解决,但体积增大后,材料的尺寸效应问题显得尤为突出,切实解决上述问题,是镁合金开发的重中之重,也是镁合金是否能够真正获得应用的关键技术。由于镁合金室温滑移系仅有3个,塑性变形能力较差,因此,镁合金通常情况下将在高温下进行变形,那么变形后的淬火处理就是十分值得关注的问题。与铝合金不同,镁合金的淬透性研究非常有限,由于镁合金的发展历史较短,目前仍集中在新型合金的开发中,真正工程化应用的变形镁合金还很有限,而能够工程化应用的变形镁合金导热性能又相对优良,如AZ系及ZK系合金,淬透性问题没有上升到必须研究的层面。镁合金的很多特点,特别是新开发的镁合金物理化学性质的认识情况还处于起步阶段,导致镁合金淬火时效的相关技术发展滞后,大规格新型镁合金的开发及应用受到了前所未有的限制,成品率降低,生产费用升高,阻碍了镁合金的生产与应用。
技术实现要素:基于此,本发明的目的在于提供一种镁合金淬火-时效一体装置,以期能够提高镁合金生产效率,减少大尺寸截面的镁合金型材淬火过程中发生的开裂情况。为实现上述目的,本发明采用以下技术方案:一种镁合金淬火-时效一体装置,包括通过传动装置依次衔接的热空气淬火装置、热介质淬火装置和热介质时效装置,其中,热空气淬火装置包括箱体和用于输送镁合金材料的轨道,该箱体侧壁开设数个热空气喷射孔;热介质淬火装置包括淬火介质槽和位于槽内的空心旋转轮盘,该旋转轮盘上设有数个用以容纳镁合金材料的空间,该淬火介质槽内设有温控装置和加热装置;热介质时效装置与所述热介质淬火装置形状相同,尺寸比热介质淬火装置大,包括时效介质槽和位于槽内的空心旋转轮盘,该旋转轮盘上设有数个用以容纳镁合金材料的空间,该时效介质槽内设有温控装置和加热装置。其中,所述热空气淬火装置的轨道延伸至与热介质时效装置用于容纳镁合金材料的空间相对应的位置,并通过推进杆实现镁合金材料的转移。所述热介质淬火装置与热介质时效装置衔接的位置设有向衔接位置循环喷射介质的喷射装置,该喷射装置的介质输送管路与热介质时效装置的时效介质槽连接,该介质输送管路上设有油泵及冷却器。所述热介质为淬火油或矿物油。采用该装置对镁合金材料进行淬火时,将从挤压桶或热处理炉中出来的镁合金材转移至热空气淬火装置中,实现一级降温;通过推进杆将镁合金材料推入热介质淬火装置中,并开动旋转轮盘,将镁合金材料浸入液面以下,根据初始热空气温度,设定介质的温度;镁合金材料在淬火介质中旋转周数不超过5周;通过传动装置,将镁合金材料拖入到热介质时效装置中,打开外循环,以达到温度均衡的效果,当达到热处理时间后,镁合金材料出炉。本发明的优点在于:本发明的装置可以实现淬火及时效两种工艺的同时实现,不仅可以缩短工时,还可以减少工序,降低镁合金材料的淬火开裂概率。附图说明图1为本发明的镁合金淬火-时效一体装置的侧面结构示意图。图2为本发明中热空气淬火装置的结构示意图。图3为本发明中热空气淬火装置的侧面结构示意图。图4为本发明中热介质淬火装置的结构示意图。图5为本发明中热介质时效装置的结构示意图。具体实施方式下面结合附图和实施例对本发明做进一步说明,但本发明的实施方式不限于此。如图1所示,本发明的镁合金淬火-时效一体装置,包括通过传动装置依次衔接的热空气淬火装置A、热介质淬火装置B和热介质时效装置C三个部分。如图1、2、3所示,热空气淬火装置包括箱体和用于输送镁合金材料2的轨道3,该箱体侧壁开设数个热空气喷射孔1,该箱体的进料口处设有推杆15,用于将镁合金材料推入轨道3。如图1、4所示,热介质淬火装置包括淬火介质槽6和位于槽内的空心旋转轮盘4,该旋转轮盘4由电机16驱动旋转,该旋转轮盘4上设有数个用以容纳镁合金材料的空间5;淬火介质槽6内设有温控装置(图中未示出)和加热装置7。如图1、5所示,热介质时效装置形状与所述热介质淬火装置相同,尺寸比热介质淬火装置大;包括时效介质槽8和位于槽内的空心旋转轮盘9,该旋转轮盘9由电机17驱动旋转,该旋转轮盘9上设有数个用以容纳镁合金材料的空间10;时效介质槽8内设有温控装置(图中未示出)和加热装置11。在热介质淬火装置与热介质时效装置衔接的位置设有向衔接位置循环喷射热介质的喷射装置12,该喷射装置12的介质输送管路与热介质时效装置的时效介质槽8连接,该介质输送管路上设有油泵14及冷却器13。本发明中的热空气淬火装置,主要是将空气加热,其温度范围为室温至500℃,以一定的压强喷射到样品表面,使其尽快降低温度,喷射压强需控制在5-50MPa。此热空气淬火装置可根据实际需求进行分段对接,实现不同温度的连续变化。作为热空气淬火装置与热介质淬火装置之间的传动装置,可以选择将热空气淬火装置的轨道延伸至与热介质时效装置用于容纳镁合金材料的空间相对应的位置,并通过推进杆实现镁合金材料向热介质淬火装置的转移。本发明中的热介质淬火装置,主要是空心旋转轮盘在电机的驱动下进入淬火介质中,淬火介质包括淬火油或者矿物油,其温度范围最高可达到350℃。在旋转轮盘中等分空洞,用以容纳镁合金材料。当镁合金材料由上一装置中过度到本环节时,轮盘开始在淬火介质中旋转。电机可以控制旋转速度,整个淬火介质槽中有温控及加热装置,同时可以根据实际情况进行液面调节。本发明中的热介质时效装置,是在热介质淬火装置的基础上进行改造获得的,两者又有不同之处,首先,该装置的尺寸要大于淬火装置,主要是因为淬火后的时效时间长,因此,必须增加镁合金材料在介质内的时间,较大的周长是完成该功能的重点;其次,在与淬火介质衔接的部分要有喷射装置,喷射效果以覆盖镁合金材料为宜,该部分的作用是为了让样品在旋转过程中,完全浸入到介质中,不因镁合金材料衔接而露出液面,另外,时效装置中同样有温控和加热装置,加热装置可以是在时效槽四壁安装的电阻丝,冷却装置主要是依靠外循环冷却。时效介质温度可以保证在室温至300℃。当镁合金材料从挤压桶或热处理炉中出来后,进入热空气淬火装置中,实现一级降温。然后由推进杆将镁合金材料推入热介质淬火装置中,并开动旋转轮盘,将镁合金材料浸入液面以下,根据初始热空气温度,设定热介质的温度。轮盘转速不宜过慢,否则将会导致镁合金材料出现粗大的析出相。样品在淬火介质中旋转周数不超过5周。然后传动装置,将其拖入到热介质时效装置中,由于起始淬火后温度较高,因此刚入时效介质时会加热介质,因此,在镁合金材料数量增多后,介质温度会明显升高,因此需要打开外循环,以达到温度均衡的效果。当达到热处理时间后,镁合金材料出炉。采用本发明的装置,淬火过程为热空气淬火和热介质淬火的两级冷却,实现了冷却递进。热空气淬火装置可根据需要进行自由组合,实现温度的梯度变化,另外,热介质淬火装置及热介质时效装置,也可以根据具体需要进行多级组合。淬火及时效同时进行是该装置最大的优势之一,可以有效缩短工时,实现规模化生产。实施例1采用本发明的装置对挤压后的EW75高性能稀土镁合金进行淬火:挤压后的EW75镁合金,截面尺寸为250×150mm,长度为2000mm,挤压后初始温度为480℃,进入热空气淬火装置,该装置由三段组成,空气温度分别为450℃、400℃及350℃,每段持续时间约为1min。然后进入热介质淬火装置,该装置的旋转轮盘有六个圆孔,每个孔尺寸为Φ400mm,保证棒材能够顺利进入。然后轮盘开始旋转,旋转1周,转速为1周/2min;此时的热介质为矿物油,温度达到300℃。随后,材料进入热介质时效装置,热介质时效装置中的介质为淬火油,温度为220℃,转速为1周/h,EW75合金在介质中旋转6周后取出,自然空冷。