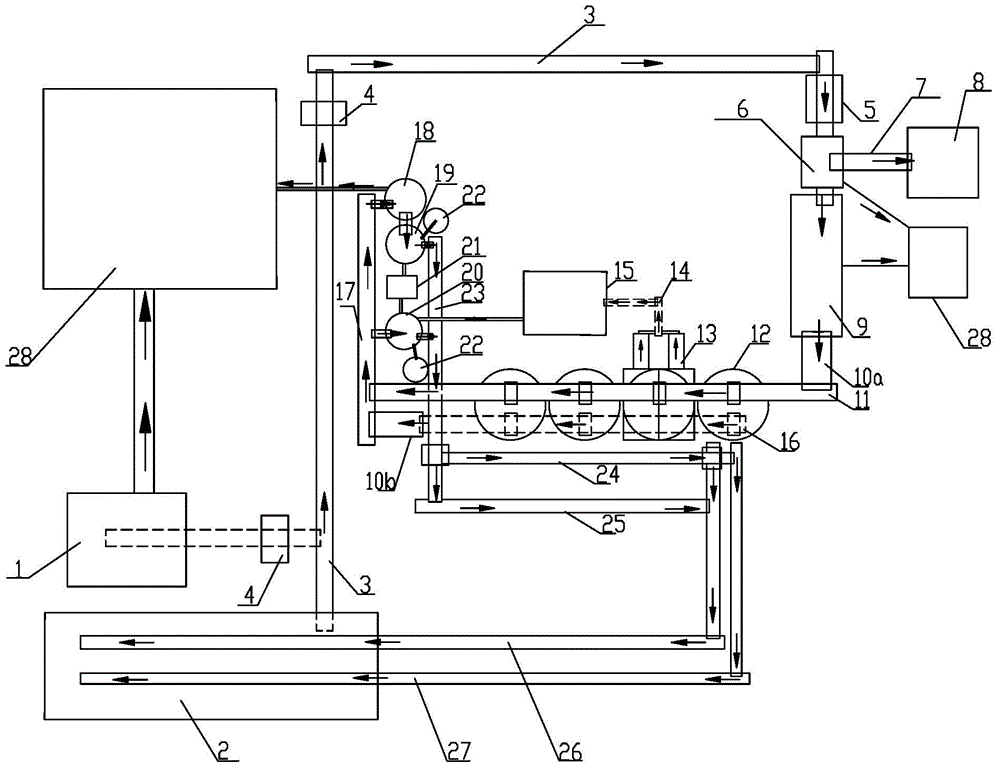
本发明涉及砂型铸造砂处理技术领域,具体指一种大型铸钢件湿型粘土砂处理系统及砂处理方法。
背景技术:我国是制造大国,铸造作为机械产品基础的制造方法,各类铸件产量呈上升趋势,其中砂型铸造占到较大比例,砂型铸造的型砂主要为水玻璃砂、树脂砂、湿型粘土砂、覆膜砂等,常见的砂处理系统(如:水玻璃砂处理系统,树脂砂处理系统等)工作环境恶劣、设备运行工况差,砂处理系统运行过程中,普遍存在以下问题:1、旧砂回收困难:铸钢件的浇注温度约1760℃左右,水玻璃砂在铸件浇注后,水玻璃在高温作用下,形成水玻璃烧结层,很难进行回收;树脂砂在高温作用下,树脂烧结后以气态散发,因此,水玻璃砂处理系统、树脂砂处理系统一般不具有砂再生能力。因此,水玻璃砂和树脂砂的消耗非常大,产品的生产成本高,环境污染大。2、砂温控制困难:旧砂主要是来自于铸型开箱落砂和生产场地上的散落砂,铸型开箱落砂后的旧砂温度很高(特别是夏天),不适合直接使用,通常情况下,需要较长旧砂冷却时间或专用场地冷却,影响生产组织和型砂质量。3、型砂质量波动大:回用砂中含有大量的粉尘、细小的废砂、金属杂物等,常见砂处理系统,无法控制回用砂含泥量,影响型砂质量和产品质量。在型砂混制过程中,型砂的相关参数不能适时检测、监控,等造型后或铸件生产出来才能发现问题,增加产品质量风险和生产成本。4、功能简单:常见的砂处理系统工艺流程(见图1)是原砂采购、旧砂输送、型砂混制、型砂输送功能的简单组合,无法满足现代化铸造生产对砂处理的效率、质量、柔性、集约、安全环保的要求。5、工作环境差:砂型铸造生产过程和开箱落砂过程中会产生大量的粉尘,工作岗位粉尘浓度超标严重,水玻璃、树脂砂生产后产生的废砂多且得不到有效处理,直接排废对环境污染大,很难到达环境保护和职业安康要求。
技术实现要素:本发明的目的在于克服上述不足,提供一种大型铸钢件湿型粘土砂处理系统及砂处理方法,对旧砂进行回收和再生,提高型砂的生产质量,大大减少生产成本。为实现上述目的,本发明所设计的大型铸钢件湿型粘土砂处理系统,其特殊之处在于:包括设置在铸件开箱区和外模造型区下方的旧砂皮带输送装置,设置在旧砂皮带输送装置上的磁选机,设置在旧砂皮带输送装置输送终端的六角精细筛分装置;所述六角精细筛分装置出口与双向给料机进口相连接,所述双向给料机出口一端通过废砂输送皮带与废砂存储斗的进口相连,所述双向给料机出口另一端与双盘冷却器的进口相连,所述双盘冷却器出口与第一旧砂斗提机连接;所述第一旧砂斗提机输出端与第一皮带输送装置输入端相连接,所述第一皮带输送装置经过砂存储斗的进口端上方,所述砂存储斗出口一端与第二皮带输送装置输入端相连接,所述砂存储斗出口另一端与砂再生机进口相连接,所述砂再生机通过再生砂输送管道与再生砂存储斗进口相连接,所述再生砂存储斗出口通过输送管道与面砂混砂机的入口相连接;所述第一皮带输送装置输送终端与第三皮带输送装置输入端相连接,所述第二皮带输送装置输送终端与所述第三皮带输送装置输入端之间设有第二旧砂斗提机,所述第三皮带输送装置输出端的一端与面砂混砂机的入口相连,所述第三皮带输送装置输出端的另一端与背砂圆盘给料机的入口相连,所述背砂圆盘给料机的出口与背砂混砂机的入口相连,所述面砂混砂机和背砂混砂机之间还设有恒压供水装置,所述面砂混砂机和背砂混砂机入口位置还均连接有辅料库,所述面砂混砂机和背砂混砂机出砂口位置下方设有第四皮带输送装置;所述第四皮带输送装置输出端通过面砂皮带输送装置和背砂皮带输送装置分别与外模造型区的造型机入口相连。进一步地,所述第四皮带输送装置输出端一端与第五皮带输送装置的输入端相连,所述第四皮带输送装置输出端另一端与第六皮带输送装置的输入端相连,所述第五皮带输送装置的输出端一端与面砂皮带输送装置输入端相连,所述第五皮带输送装置的输出端另一端与背砂皮带输送装置输入端相连,所述第六皮带输送装置输出端与所述背砂皮带输送装置输入端相连,所述面砂皮带输送装置和背砂皮带输送装置的输出端分别与外模造型区的造型机入口相连。这样,一般情况下,型砂从第四皮带输送装置输出端出来后直接进入第五皮带输送装置,然后再分别进入到背砂皮带输送装置或面砂皮带输送装置,但是当第五皮带输送装置进行检修或者发生故障时,也可以通过第六皮带输送装置来输送型砂。进一步地,所述铸件开箱区、双盘冷却器和背砂圆盘给料机均通过管道与除尘器相连接。优选地,所述磁选机的数量为两个。另外本发明还提供一种利用上述大型铸钢件湿型粘土砂处理系统进行砂处理的方法,其特殊之处在于:包括以下步骤:步骤1)旧砂回收:铸件开箱区和外模造型区的旧砂通过落砂机落入旧砂皮带输送装置,在旧砂皮带输送装置上设有磁选机,用于清理旧砂中的浇冒口、冷铁、芯骨金属废杂物,使得旧砂达到工艺要求;步骤2)旧砂处理:在旧砂皮带输送装置的输送终端设有六角精细筛分装置,对旧砂进行破碎、筛分,将大块旧砂分离、排放,并在此过程中进行吹风冷却,对旧砂进行初步降温,筛出的废砂送入废砂存储斗;经过筛选的旧砂通过双盘冷却器,采用加水、鼓风、翻转搅拌相结合的措施将旧砂快速冷却到工艺设定温度;冷却后的旧砂一部分通过斗提机和第一皮带输送装置送至砂存储斗,另一部分依次通过斗提机、第一皮带输送装置和第三皮带输送装置直接送至面砂混砂机和背砂混砂机上方的旧砂斗中储存待用;步骤3)旧砂再生:通过砂存储斗下面的给料机构将旧砂输送至砂再生机,旧砂经过鼓风、撞击、抽风除尘、筛分,进行多级气流撞击再生,去除砂粒表面的有害物质,并通过调整风压和再生机的导向板、筛网的大小,可调整再生砂质量,满足不同工艺需求,再生砂通过气力输送管道送至再生砂存储斗,然后通过管道可直接送入面砂混砂机;湿型粘土砂系统每月需加入3%-5%的新砂,以补充因系统排废减少的数量,保证砂处理系统的运行,将需要补充的新砂输送至面砂混砂机和背砂混砂机上方的新砂斗中,通过比例调节器调配新砂与旧砂混合比例;步骤4)型砂混制:在混砂过程中,旧砂、新砂及辅料经定量后加入到面砂混砂机和背砂混砂机中,同时通过恒压供水装置进行恒压供水,充分混制,根据工艺需要制作不同的型砂,然后通过第四皮带输送装置分别送至面砂皮带输送装置和背砂皮带输送装置,最后再送至外模造型区的造型机上方的砂斗中待用;步骤5)相关检测及型砂质量控制:通过面砂混砂机和背砂混砂机上设置的在线检测装置,对型砂中的紧实度、水分含量、膨润土含量进行适时测定,测定结果显示在系统控制室,并通过外模造型区的型砂人工检测室,测定型砂水分含量、膨润土含量、湿压强度、干拉强度、透气性等数据,两者形成对比,根据数据进行分析、总结,及时修正设定参数,满足工艺要求;步骤6)系统除尘:在现场粉尘较大的区域设置除尘器,通过管道和空气动力,采用离线脉冲式布袋除尘器集中处理粉尘。在上述技术方案中,铸钢件砂型铸造采用面砂、背砂相结合工艺,背砂要求比较低,冷却后的旧砂可直接混制成背砂,而面砂主要是用来成型产品外轮廓,要求更高,而旧砂中砂粒表面存在大量的惰性膜、灰分、死粘土等有害物,为了满足面砂混制工艺要求,保证型砂质量,有效去除旧砂中影响型砂工艺性能的有害物,故旧砂需经过再生后用作面砂;辅料库主要用于添加膨润土、淀粉等一些辅料。本发明相对于水玻璃砂处理系统和树脂砂处理系统,具有如下有益效果:其一,旧砂回收利用率高:本系统将铸造车间内部各个工序(如:开箱落砂、造型、制芯等)散落砂回收到系统中,通过冷却设备、再生设备等回收利用,其旧砂回用率高达95%以上,大大降低了生产成本。其二,型砂质量稳定:双盘冷却器对旧砂温度进行检测,根据工艺要求自动加水搅拌降温,并自动检测控制旧砂湿度,为混砂单元提供质量稳定的回用砂。混砂单元配置型砂质量自动检测设施具备在线检测和自动调整混砂配比及人工干预配比功能,结合现场型砂试验室人工检测比对,型砂混制质量控制可靠。其三,自动化程度高:对用砂网络实行集中控制供应、单元模块化运行管理,手动/自动结合操作,场地多点控制,适用于生产场地工艺布局复杂、功能复杂、柔性要求高、安全及质量管理难度大的大型铸造车间,系统运行经济、可靠,维护便利。高度自动化运行管理显著降低员工劳动强度、改善员工工作环境,减少人工成本。其四,工艺适应性好:可根据型砂工艺要求,混制各类型型砂,从旧砂回用、旧砂破碎、旧砂冷却、旧砂再生、型砂混制等单元进行严格控制,满足各种特定型砂工艺要求。其五,工作环境好:输送系统、各受料/卸料点封闭除尘,工作岗位、现场粉尘污染控制有效,除尘系统风速、风量设置合理,回用砂、再生砂含泥量、有效土含量稳定,型砂混制质量稳定可控。附图说明图1为现有技术中常见的砂处理系统工艺流程图;图2为本发明的大型铸钢件湿型粘土砂处理系统结构示意图;图中,开箱区1、外模造型区2、旧砂皮带输送装置3、磁选机4、六角精细筛分装置5、双向给料机6、废砂输送皮带7、废砂存储斗8、双盘冷却器9、第一旧砂斗提机10a、第二旧砂斗提机10b、第一皮带输送装置11、砂存储斗12、砂再生机13、再生砂输送管道14、再生砂存储斗15、第二皮带输送装置16、第三皮带输送装置17、背砂圆盘给料机18、背砂混砂机19、面砂混砂机20、恒压供水装置21、辅料库22、第四皮带输送装置23、第五皮带输送装置24、第六皮带输送装置25、背砂皮带输送装置26、面砂皮带输送装置27、除尘器28;箭头表示砂或粉尘流向图。具体实施方式下面结合附图和具体实施例对本发明作进一步的详细描述:如图1所示常见的砂处理系统工艺流程图,已在背景技术中作了详细说明,于此不再赘述。如图2所示的大型铸钢件湿型粘土砂处理系统,包括设置在铸件开箱区1和外模造型区2下方的旧砂皮带输送装置3,设置在旧砂皮带输送装置3上的两个磁选机4,设置在旧砂皮带输送装置3输送终端的六角精细筛分装置5;所述六角精细筛分装置5出口与双向给料机6进口相连接,所述双向给料机6出口一端通过废砂输送皮带7与废砂存储斗8的进口相连,所述双向给料机6出口另一端与双盘冷却器9的进口相连,所述双盘冷却器9出口与第一旧砂斗提机10a连接;所述第一旧砂斗提机10a输出端与第一皮带输送装置11输入端相连接,所述第一皮带输送装置11经过砂存储斗12的进口端上方,所述砂存储斗12出口一端与第二皮带输送装置16输入端相连接,所述砂存储斗12出口另一端与砂再生机13进口相连接,所述砂再生机13通过再生砂输送管道14与再生砂存储斗15进口相连接,所述再生砂存储斗15出口通过输送管道与面砂混砂机20的入口相连接;所述第一皮带输送装置11输送终端与第三皮带输送装置17输入端相连接,所述第二皮带输送装置16输送终端与所述第三皮带输送装置17输入端之间设有第二旧砂斗提机10b,所述第三皮带输送装置17输出端的一端与面砂混砂机20的入口相连,所述第三皮带输送装置17输出端的另一端与背砂圆盘给料机18的入口相连,所述背砂圆盘给料机18的出口与背砂混砂机19的入口相连,所述面砂混砂机20和背砂混砂机19之间还设有恒压供水装置21,所述面砂混砂机20和背砂混砂机19入口位置还均连接有辅料库22,所述面砂混砂机20和背砂混砂机19出砂口位置下方设有第四皮带输送装置23;所述第四皮带输送装置23输出端一端与第五皮带输送装置24的输入端相连,所述第四皮带输送装置23输出端另一端与第六皮带输送装置25的输入端相连,所述第五皮带输送装置24的输出端一端与面砂皮带输送装置27输入端相连,所述第五皮带输送装置24的输出端另一端与背砂皮带输送装置26输入端相连,所述第六皮带输送装置25输出端与所述背砂皮带输送装置26输入端相连,所述面砂皮带输送装置27和背砂皮带输送装置26的输出端分别与外模造型区2的造型机入口相连;这样,型砂从第四皮带输送装置23输出端出来后直接进入第五皮带输送装置24,然后再分别进入到背砂皮带输送装置26或面砂皮带输送装置27,但是当第五皮带输送装置进行检修或者发生故障时,也可以通过第六皮带输送装置来输送型砂;所述铸件开箱区1、双盘冷却器9和背砂圆盘给料机18均通过管道与除尘器28相连接。本发明的大型铸钢件湿型粘土砂处理系统进行砂处理的方法,具体包括以下步骤:步骤1)旧砂回收:铸件开箱区1和外模造型区2的旧砂通过落砂机落入旧砂皮带输送装置3,在旧砂皮带输送装置3上设有磁选机4,用于清理旧砂中的浇冒口、冷铁、芯骨金属废杂物,使得旧砂达到工艺要求;步骤2)旧砂处理:在旧砂皮带输送装置3的输送终端设有六角精细筛分装置5,对旧砂进行破碎、筛分,将大块旧砂分离、排放,并在此过程中进行吹风冷却,对旧砂进行初步降温,筛出的废砂送入废砂存储斗8;经过筛选的旧砂通过双盘冷却器9,采用加水、鼓风、翻转搅拌相结合的措施将旧砂快速冷却到工艺设定温度;冷却后的旧砂一部分通过第一旧砂斗提机10a和第一皮带输送装置11送至砂存储斗12,另一部分依次通过第一旧砂斗提机10a、第一皮带输送装置11和第三皮带输送装置17直接送至面砂混砂机20和背砂混砂机19上方的旧砂斗中储存待用;步骤3)旧砂再生:通过砂存储斗12下面的给料机构将旧砂输送至砂再生机13,旧砂经过鼓风、撞击、抽风除尘、筛分,进行多级气流撞击再生,去除砂粒表面的有害物质,并通过调整风压和砂再生机13的导向板、筛网的大小,可调整再生砂质量,满足不同工艺需求,再生砂通过气力输送管道14送至再生砂存储斗15,然后通过管道可直接送入面砂混砂机20;湿型粘土砂系统每月需加入3%-5%的新砂,以补充因系统排废减少的数量,保证砂处理系统的运行,将需要补充的新砂输送至面砂混砂机20和背砂混砂机19上方的新砂斗中,通过比例调节器调配新砂与旧砂混合比例;步骤4)型砂混制:在混砂过程中,旧砂、新砂及辅料经定量后加入到面砂混砂机20和背砂混砂机19中,同时通过恒压供水装置21进行恒压供水,充分混制,根据工艺需要制作不同的型砂,然后送至外模造型区2的造型机上方的砂斗中待用;步骤5)相关检测及型砂质量控制:通过面砂混砂机20和背砂混砂机19上设置的在线检测装置,对型砂中的紧实度、水分含量、膨润土含量进行适时测定,测定结果显示在系统控制室,并通过外模造型区2的型砂人工检测室,测定型砂水分含量、膨润土含量、湿压强度、干拉强度、透气性等数据,两者形成对比,根据数据进行分析、总结,及时修正设定参数,满足工艺要求;步骤6)系统除尘:在现场粉尘较大的区域设置除尘器28,通过管道和空气动力,采用离线脉冲式布袋除尘器集中处理粉尘。