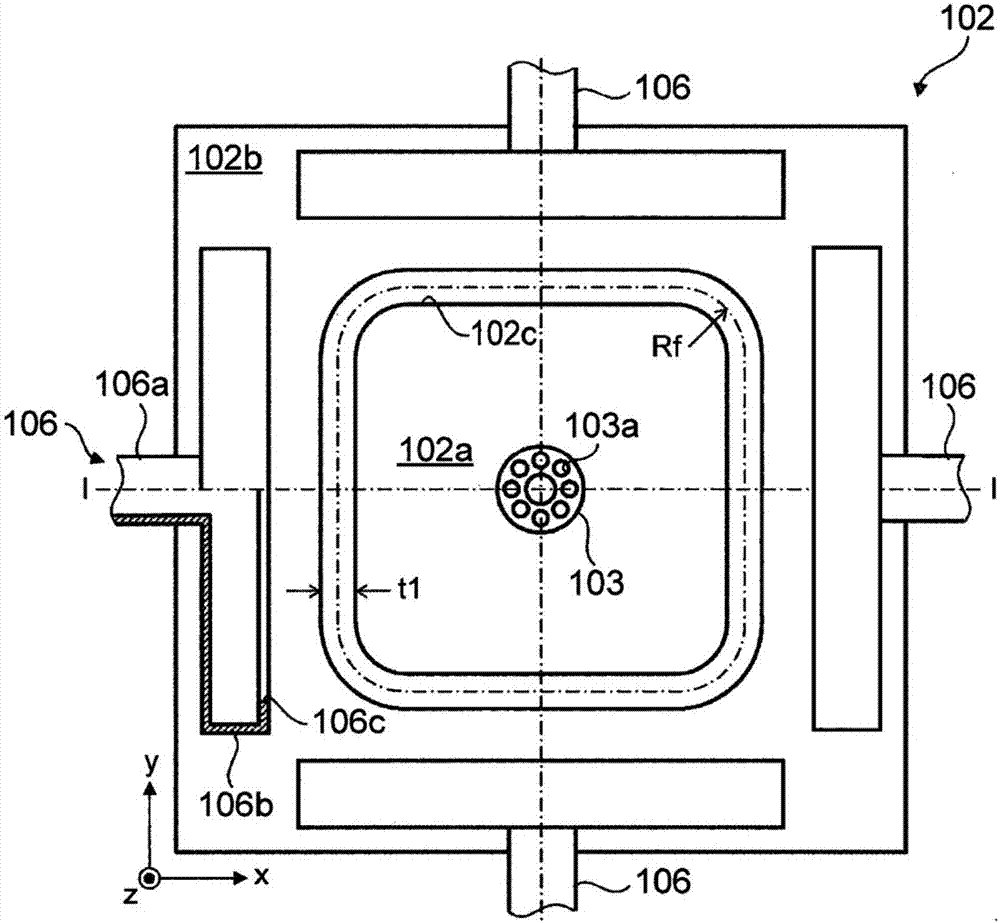
本发明涉及上引式连续铸造方法和上引式连续铸造装置。
背景技术:日本专利申请公报No.2012-61518(JP2012-61518A)提出了一种不需要模具的自由铸造方法,该方法是一种开创性的上引式连续铸造方法。如JP2012-61518A中描述的,启动器首先被浸入到熔融金属的表面(即,熔融金属表面)中,并且随后当启动器被上引时,熔融金属借助于熔融金属的表面张力和表面膜而跟随启动器也被上引。在此,通过将熔融金属上引穿过布置在熔融金属表面附近的形状确定构件并且对所上引的熔融金属进行冷却,能够连续地铸造具有期望的截面形状的铸件。通过一般的连续铸造方法,截面形状和纵向方向上的形状两者均由模具确定。具体地,通过连续铸造方法,凝固的金属(即,铸件)必须穿过模具,因此所铸造的铸件获得沿纵向方向线性延伸的形状。与此相反,自由铸造方法中的形状确定构件仅确定铸件的截面形状。纵向方向上的形状没有被确定。因此,通过在将启动器上引的同时使启动器(或形状确定构件)沿水平方向移动,能够获得纵向方向上具有各种形状的铸件。例如,JP2012-61518A描述了一种在纵向方向上形成为Z字形形状或螺旋形形状而不是线性形状的中空铸件(即,管状件)。本发明人发现了下面描述的问题。通过JP2012-61518A中所描述的自由铸造方法,由于熔融金属被上引穿过形状确定构件,因此凝固分界定位成比形状确定构件高,正如上文所描述的。在此,从生产率的角度来看,优选的是增大铸造速度(即,上引速度),但当铸造速度增大时,凝固分界升高。当凝固分界升高时,已经被上引穿过形状确定构件的熔融金属的表面面积增大,并且因此,表面张力增大。因此,如果在铸造由形状确定构件确定的截面形状具有圆角部分的铸件时增大铸造速度,则所铸造的铸件的圆角部分的曲率半径最终将比由形状确定构件最初确定的期望的曲率半径大。即,通过根据相关技术的上引式连续铸造方法,当铸造由形状确定构件确定的截面形状具有圆角部分的铸件时,铸造速度不能被增大,这会阻碍生产率并且因此是成问题的。
技术实现要素:本发明提供了下述上引式连续铸造方法和上引式连续铸造装置:该上引式连续铸造方法和上引式连续铸造装置提供由形状确定构件确定的截面形状具有圆角部分的铸件的优异的生产率。本发明的第一方面涉及一种上引式连续铸造方法,该上引式连续铸造方法包括将保持在保持炉中的熔融金属上引穿过形状确定构件,该形状确定构件确定所铸造的铸件的截面形状。由形状确定构件确定的截面形状包括圆角部分,并且由该形状确定构件确定的该圆角部分的曲率半径的值比铸件的圆角部分的曲率半径的设计值小。根据这种结构,除了增大铸造速度以外,能够使铸件的圆角部分的曲率半径为期望值,因此由形状确定构件确定的截面形状具有圆角部分的铸件的生产率得到提高。当确定由形状确定构件确定的圆角部分的曲率半径的值时,可以由计算机执行以如下铸造速度进行的铸造仿真,在该铸造速度下,铸件的圆角部分的曲率半径变得比由形状确定构件确定的圆角部分的曲率半径大,并且由形状确定构件确定的圆角部分的曲率半径的值可以基于通过该铸造仿真获得的铸件的圆角部分的曲率半径而确定。另外,可以改变由形状确定构件确定的圆角部分的曲率半径并且可以重复执行以所述铸造速度进行的铸造仿真,使得通过该铸造仿真获得的铸件的圆角部分的曲率半径更接近设计值。根据这种结构,形状确定构件的圆角部分的曲率半径能够适于以更高的速度铸造。在确定由形状确定构件确定的圆角部分的曲率半径的值之前,可以执行用于确定铸造速度的初步铸造仿真,并且该铸造速度可以基于通过该初步铸造仿真获得的凝固分界的位置而确定。此外,可以改变铸造速度并且可以重复执行初步铸造仿真,使得通过该初步铸造仿真获得的凝固分界的位置落在参考范围内。根据这种结构,形状确定构件的圆角部分的曲率半径能够适于以甚至更高的速度铸造。在上述上引式连续铸造方法中,可以利用铸造仿真的铸造条件由实际设备执行铸造,可以判定由该实际设备铸造的铸件的圆角部分的曲率半径是否在参考范围内,并且当铸件的圆角部分的曲率半径不在参考范围内时,可以改变铸造条件。本发明的第二方面涉及一种上引式连续铸造装置,该上引式连续铸造装置包括:保持炉,该保持炉保持熔融金属;以及形状确定构件,该形状确定构件布置在保持于该保持炉中的熔融金属的熔融金属表面上,并且该形状确定构件确定通过使所述熔融金属穿过该形状确定构件而铸造的铸件的截面形状。由形状确定构件确定的截面形状包括圆角部分,并且由该形状确定构件确定的该圆角部分的曲率半径的值比铸件的圆角部分的曲率半径的设计值小。根据这种结构,能够使铸件的圆角部分的曲率半径为期望值,因此由形状确定构件确定的截面形状具有圆角的铸件的生产率得到提高。根据本发明,能够提供下述上引式连续铸造方法和上引式连续铸造装置:该上引式连续铸造方法和上引式连续铸造装置能够提供由形状确定构件确定的截面形状具有圆角部分的铸件的优异的生产率。附图说明下面将参照附图对本发明的示例性实施方式的特征、优势以及技术和工业意义进行描述,在附图中,相同的附图标记表示相同的元件,并且在附图中:图1是示出了根据本发明的第一示例性实施方式的自由铸造装置的结构形式的截面图;图2是根据第一示例性实施方式的形状确定构件的平面图;图3是铸件以及形状确定构件的熔融金属通道部的平面图;图4是示出了用于确定由形状确定构件确定的圆角部分的曲率半径的方法的流程图;图5是铸造仿真结果的一个示例的立体图;图6是示出了通过铸造仿真获得的铸件的圆角部分的曲率半径(水平轴线)与由形状确定构件确定的圆角部分的曲率半径(竖向轴线)之间的关系的曲线图;以及图7是示出了用于确定实际设备中的铸造条件的方法的流程图。具体实施方式在下文中,将参照附图对实施本发明的具体示例性实施方式进行详细描述。然而,本发明不限于这些示例性实施方式。另外,为了清楚起见,描述和附图被适当地简化。(第一示例性实施方式)首先,将参照图1对根据本发明的第一示例性实施方式的自由铸造装置(上引式连续铸造装置)进行描述。图1是示出了根据第一示例性实施方式的自由铸造装置的结构形式的截面图。如图1中所示,根据第一示例性实施方式的自由铸造装置包括熔融金属保持炉101、形状确定构件102(内形状确定构件102a和外形状确定构件102b)、内冷却气体喷嘴103、支承杆104、致动器105、外冷却气体喷嘴106和上引机108。当然,图1中示出的右手xyz坐标系是用于描述性的目的以便示出构成元件的位置关系。图1中的x-y平面形成水平平面,并且z轴方向是竖向方向。更具体地,z轴的正向方向是竖向向上的。其他附图中示出的右手xyz坐标系是相同的。熔融金属保持炉101保持诸如例如铝或铝合金之类的熔融金属M1,并且将熔融金属M1保持处于预定温度,在该预定温度下,熔融金属M1具有流动性。在图1中的示例中,在铸造期间,熔融金属没有被补充到熔融金属保持炉101中,因此熔融金属M1的表面(即,熔融金属表面MMS的水平高度)随着铸造的进行而降低。然而,在铸造期间,熔融金属也可以在需要时被补充到熔融金属保持炉101中,使得熔融金属表面MMS的水平高度保持恒定。在此,凝固分界SIF的位置能够通过升高熔融金属保持炉101的设定温度而升高,并且能够通过降低熔融金属保持炉101的设定温度而降低。当然,熔融金属M1可以是除铝以外的其他金属或合金。形状确定构件102由内形状确定构件102a和外形状确定构件102b形成。图2是形状确定构件102的平面图。在此,图1中的内形状确定构件102a和外形状确定构件102b的截面图与沿着图2中的线I-I截取的截面图对应。形状确定构件102由例如陶瓷或不锈钢制成,并且布置在熔融金属表面MMS上。形状确定构件102确定所铸造的铸件M3的截面形状。内形状确定构件102a确定管状铸件的内部形状,并且外形状确定构件102b确定铸件M3的外部形状。在图1中的示例中,形状确定构件102(即,内形状确定构件102a和外形状确定构件102b)的下侧的主平面(下表面)布置成与熔融金属表面MMS接触。因此,能够防止形成在熔融金属表面MMS上的氧化膜和漂浮在熔融金属表面MMS上的异物混入到铸件M3中。然而,形状确定构件102的下表面还可以布置成与熔融金属表面MMS相距预定距离(例如,大约0.5mm)。当形状确定构件102布置成与熔融金属表面MMS隔开时,形状确定构件102的热变形和熔蚀被抑制,因此形状确定构件102的耐用性得到改善。如图2中所示,外部形状确定构件102b具有例如矩形平面形状,并且在其中央具有矩形开口部分,该矩形开口部分具有四个圆角部分。内形状确定构件102a具有例如矩形平面形状,并且布置在外形状确定构件102b的开口部分的中央。内形状确定构件102a与外形状确定构件102b之间的间隙形成熔融金属通道部102c,熔融金属穿过该熔融金属通道部102c。因此,图1中示出的铸件M3是在水平面中具有矩形截面形状并具有四个圆角部分的中空铸件(即,为方形管件)。熔融金属通道部102c形成为具有宽度t1的环形形状。内冷却气体喷嘴103布置在内形状确定构件102a的中央。如图1中所示,熔融金属M1借助于熔融金属M1的表面张力和表面膜而跟随铸件M3被上引,并且穿过形状确定构件102的熔融金属通道部102c。即,通过使熔融金属M1穿过形状确定构件102的熔融金属通道部102c,来自形状确定构件102的外力被施加至熔融金属M1,使得铸件M3的截面形状被确定。在此,借助于熔融金属的表面张力和表面膜而跟随铸件M3从熔融金属表面MMS被上引的熔融金属将称为“被保持的熔融金属M2”。另外,铸件M3与被保持的熔融金属M2之间的边界是凝固分界SIF。图2还示出了布置成比形状确定构件102高(朝向z轴方向的正向侧更远)的四个外冷却气体喷嘴106。稍后将对这些外冷却气体喷嘴106的细节进行描述。另外,铸件M3的截面形状(即,熔融金属通道部102c的平面形状)不被具体地限制,只要其具有圆角部分即可。铸件M3可以是诸如具有圆角部分的多边形柱状件之类的实心铸件。内冷却气体喷嘴103是用于对被保持的熔融金属M2进行冷却的冷却装置。如由图1中的黑色箭头所示,被保持的熔融金属M2通过内冷却气体喷嘴103将冷却气体(例如,空气、氮气、氩气等)喷射在铸件M3上而被间接地冷却。另外,内冷却气体喷嘴103连接至内形状确定构件102a的中央部分,并且支承内形状确定构件102a。如图1和图2中所示,内冷却气体喷嘴103在从内形状确定构件102a突出的端部中具有多个喷射孔103a。铸件M3通过喷射孔103a将冷却气体(比如空气、氮气、氩气等)朝向铸件M3的内周表面喷射而从内部被冷却。在图2中的示例中,设置有八个喷射孔103a,但喷射孔103a的数目不被具体地限制并且可以适当地设定。支承杆104支承外形状确定构件102b。内冷却气体喷嘴103和支承杆104使内形状确定构件102a与外形状确定构件102b之间的位置关系能够被保持。内冷却气体喷嘴103和支承杆104连接至致动器105。因此,通过致动器105,能够在保持该位置关系的同时上下(即,沿竖向方向,即,z轴方向)移动内形状确定构件102a和外形状确定构件102b。根据这种结构,形状确定构件102能够在熔融金属表面MMS的水平高度随着铸造的进行而降低时向下移动。外冷却气体喷嘴106也是用于对被保持的熔融金属M2进行冷却的冷却装置。如由图1中的黑色箭头所示,被保持的熔融金属M2通过外冷却气体喷嘴106将冷却气体(例如,空气、氮气、氩气等)喷射在铸件M3上而被间接地冷却。凝固分界SIF的位置能够通过增大冷却气体的流量而降低,并且能够通过减小冷却气体的流量而升高。外冷却气体喷嘴106也能够与形状确定构件102的运动一致地上下(即,沿竖向方向,即,沿z轴方向)移动。如图2中所示,四个外冷却气体喷嘴106沿着在从上方观察时具有矩形形状的熔融金属通道部102c的每侧各延伸有一个外冷却气体喷嘴106。定位在图2中的左侧的外气体冷却喷嘴106的下半部分(在y轴方向上的负向侧)以截面图示出。如图1和图2中所示,外冷却气体喷嘴106各自包括入口管106a、主体部106b和缝隙106c。每个主体部106b均是管状构件,该管状构件的两个端部均是封闭的。这些主体部106b沿着熔融金属通道部102c的每侧各延伸有一个主体部106b。沿主体部106b的长度方向延伸的缝隙106c设置在主体部106b的面向铸件M3的侧部上。通过入口管106a引入的冷却气体从设置在主体部106b中的缝隙106c被喷射在铸件M3的外周表面上。启动器ST固定至上引机108。铸件M3在经由启动器ST被上引机108上引的同时被冷却气体冷却。因此,铸件M3通过位于凝固分界SIF附近的被保持的熔融金属M2从上侧(即,z轴方向上的正向侧)朝向下侧(即,z轴方向上的负向侧)相继地凝固而形成。凝固分界SIF的位置能够通过增大上引机108的上引速度而升高,并且能够通过减小上引速度而降低。另外,被保持的熔融金属M2能够通过在将被保持的熔融金属M2上引的同时使上引机108水平地(沿x轴方向和y轴方向)移动而被倾斜地(diagonally)上引。因此,铸件M3的纵向形状能够自由地改变。铸件M3的纵向形状还可以通过使形状确定构件102水平地移动而不是通过使上引机108水平地移动来自由地改变。接下来,将参照图3对根据该示例性实施方式的形状确定构件102进一步地进行描述。图3是形状确定构件102的熔融金属通道部102c以及铸件M3的平面图。铸件M3由实线表示并且熔融金属通道部102c由虚线表示。如图3中所示,通过根据该示例性实施方式的形状确定构件102,熔融金属通道部102c的圆角部分的中心线的曲率半径Rf比铸件M3的圆角部分的中心线的目标曲率半径(铸件M3的圆角部分的曲率半径的设计值)Rt小。因此,如果铸造速度增大并且凝固分界SIF升高,则能够获得具有目标曲率半径Rt的铸件M3。因此,与现有技术相比,通过使用根据该示例性实施方式的形状确定构件102,铸造速度可以更快,从而使生产率能够得以提高。如图3中所示,铸件M3的厚度t2比熔融金属通道部102c的宽度t1小。另一方面,通过根据相关技术的形状确定构件102,熔融金属通道部102c的圆角部分的中心线的曲率半径Rf与铸件M3的圆角部分的中心线的目标曲率半径Rt相等(match)。因此,如果铸造速度增大并且凝固分界SIF升高,则铸件M3的圆角部分的曲率半径Rc最终将比目标曲率半径Rt大。因此,当使用相关技术的形状确定构件102时,铸造速度不能够被增大。所铸造的铸件M3的圆角部分的曲率半径Rc与目标曲率半径Rt之间的差随着凝固分界SIF变得更高(即,随着铸造速度的增大)而增大。接下来,将参照图4对用于在根据第一示例性实施方式的自由铸造方法(即,上引式连续铸造方法)中确定由形状确定构件102确定的圆角部分的曲率半径Rf的方法进行描述。图4是示出了用于确定由形状确定构件102确定的圆角部分的曲率半径Rf的方法的流程图。如图4中所示,当确定由形状确定构件102确定的圆角部分的曲率半径Rf时,可以使用由计算机进行的铸造仿真。这使由形状确定构件102确定的圆角部分的曲率半径Rf能够适于更高速度的铸造。首先,在铸造仿真中,使由形状确定构件102确定的圆角部分的曲率半径Rf与铸件M3的圆角部分的目标曲率半径Rt相等(步骤ST1)。在图4中,由形状确定构件102确定的圆角部分的曲率半径Rf简单地表示为“形状确定构件102的角Rf”等。接下来,熔融金属温度、冷却条件和铸造速度被适当地设定,并且执行铸造仿真(步骤ST2)。步骤ST2中的铸造仿真是用于确定铸造速度的初步仿真。在此,例如,熔融金属温度可以设定成与实际铸造装置(即,实际设备)的熔融金属温度大致相同。另外,例如由于期望增大铸造速度,冷却条件(即,冷却气体流量)可以设定为相对较大的值,在该值下,可以在实际设备中进行铸造。接下来,判定通过铸造仿真获得的凝固分界SIF的位置(即,凝固分界高度)是否在参考范围内(步骤ST3)。在此,随着铸造速度的增大并且铸件M3的圆角部分的曲率半径Rc变得比由形状确定构件102确定的圆角部分的曲率半径Rf大,圆角部分的凝固分界SIF变得比直线部分的凝固分界SIF高。因此,凝固分界SIF的位置优选地由铸件M3的直线部分确定。铸造速度越快,凝固分界SIF的位置也越高,因此从生产率的角度来看,高位置的凝固分界SIF是优选的。然而,如果凝固分界SIF的位置变得太高,则被保持的熔融金属M2最终将撕裂,并且因此将不再能够被铸造。从该角度来看,可以确定凝固分界SIF的位置的参考范围。被保持的熔融金属M2的撕裂也可以通过铸造仿真来进行模拟。如果凝固分界SIF的位置不在参考范围内(即,步骤ST3中的否),则改变铸造速度(步骤ST4)。更具体地,如果凝固分界SIF的位置(高度)超出参考范围,则减小铸造速度。另一方面,如果凝固分界SIF的位置(高度)低于参考范围,则增大铸造速度。随后,该过程返回至步骤ST2,并且再次执行铸造仿真。如果凝固分界SIF的位置在参考范围内(即,步骤ST3中的是),则该值被选定为铸造速度(步骤ST5)。当然,在该选定的铸造速度下,通过铸造仿真获得的铸件M3的圆角部分的曲率半径Rc将变得比由形状确定构件102确定的圆角部分的曲率半径Rf(即,铸件M3的圆角部分的目标曲率半径Rt)大。接下来,改变由形状确定构件102确定的圆角部分的曲率半径Rf并且执行铸造仿真(步骤ST6)。首先,使由形状确定构件102确定的圆角部分的曲率半径Rf比铸件M3的圆角部分的目标曲率半径Rt小。接下来,判定通过铸造仿真获得的铸件M3的圆角部分的曲率半径Rc是否在参考范围内(步骤ST7)。在此,铸件M3的圆角部分的曲率半径的参考范围可以根据铸件M3的圆角部分的目标曲率半径Rt适当地设定。如果铸件M3的圆角部分的曲率半径Rc不在参考范围内(即,步骤ST7中的否),则过程返回至步骤ST6,并且改变由形状确定构件102确定的圆角部分的曲率半径Rf,并且再次执行铸造仿真。更具体地,如果铸件M3的圆角部分的曲率半径Rc超出参考范围,则甚至更大程度地减小由形状确定构件102确定的圆角部分的曲率半径Rf。另一方面,如果铸件M3的圆角部分的曲率半径Rc低于参考范围,则增大由形状确定构件102确定的圆角部分的曲率半径Rf。如果铸件M3的圆角部分的曲率半径Rc在参考范围内(即,步骤ST7中的是),则该值被选定为由形状确定构件102确定的圆角部分的曲率半径Rf(步骤ST8)。根据这些步骤能够确定由形状确定构件102确定的圆角部分的曲率半径Rf。图5是铸造仿真结果的一个示例的立体图。考虑到对称性,该铸件仿真是在图3中的仅右上1/4上执行的。如图5中所示,铸件M3的圆角部分的曲率半径Rc以及凝固分界SIF的位置能够从铸造仿真获知。图6是示出了通过铸造仿真获得的铸件M3的圆角部分的曲率半径Rc(水平轴线)与由形状确定构件102确定的圆角部分的曲率半径Rf(竖向轴线)之间的关系的曲线图。该结果是针对铸件M3的厚度为3mm且冷却气体流量为20L/min的情况,铸件M3比如为图3中示出的铸件。在图6中示出的示例中,当铸造速度V≤0.2mm/s时,由形状确定构件102确定的圆角部分的曲率半径Rf与铸件M3的圆角部分的曲率半径Rc相等。另一方面,当铸造速度V超过0.2mm/s时,铸件M3的圆角部分的曲率半径Rc变得比由形状确定构件102确定的圆角部分的曲率半径Rf大。即,当铸造速度V超过0.2mm/s时,需要使由形状确定构件102确定的圆角部分的曲率半径Rf比铸件M3的圆角部分的目标曲率半径Rt小。另外,需要使由形状确定构件102确定的圆角部分的曲率半径Rf与铸件M3的圆角部分的目标曲率半径Rt之间的差随着铸造速度的增大而增大。接下来,将参照图7对用于确定实际设备的铸造条件的方法进行描述。图7是示出用于确定实际设备的铸造条件的方法的流程图。用于确定实际设备的铸造条件的方法的该流程图遵循图4中示出的用于确定由形状确定构件102确定的圆角部分的曲率半径Rf的方法的流程图。首先,准备形状确定构件102(步骤ST11),该形状确定构件102的圆角部分的曲率半径Rf通过图4中所示的方法确定。接下来,利用图4中所示的铸造仿真的铸造条件,由实际设备执行铸造(步骤ST12)。随后,判定由实际设备铸造的铸件M3的圆角部分的曲率半径Rc是否在参考范围内(步骤ST13)。如果铸件M3的圆角部分的曲率半径Rc不在参考范围内(即,步骤ST13中的否),则改变铸造条件(步骤ST14)。更具体地,如果铸件M3的圆角部分的曲率半径Rc超出参考范围,则需要降低凝固分界SIF的位置。因此,降低熔融金属温度,或者减小铸造速度,或者增大冷却气体流量。另一方面,如果铸件M3的圆角部分的曲率半径Rc低于参考范围,则需要升高凝固分界SIF的位置。因此,升高熔融金属温度,或者增大铸造速度,或者减小冷却气体流量。随后,过程返回至步骤ST13,并且通过实际设备再次执行铸造。如果铸件M3的圆角部分的曲率半径Rc在参考范围内(即,步骤ST13中的是),则该条件被选定为铸造条件(步骤ST15)。实际设备的铸造条件能够通过这些步骤而确定。如步骤ST12中所示,铸造仿真中使用的铸造条件能够作为起始点使用,因此能够减少由实际设备执行的用以确定铸造条件的铸造次数。本发明不限于上述示例性实施方式,并且可以在不背离本发明的精神的情况下适当地修改。