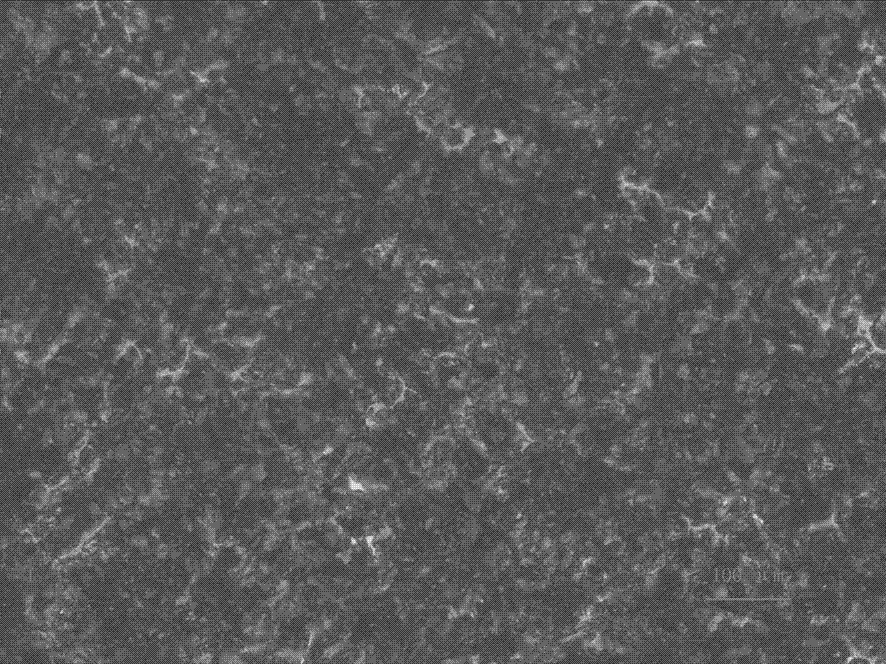
本发明属于发动机气缸套技术领域,具体涉及一种刮碳环及其制备方法。
背景技术:随着发动机功率提升和运行时间延长,尤其是使用重油的柴油发动机,与气缸套配合的活塞表面极易积累大量积炭,这些积累的积炭一方面影响了发动机的稳定运行,另一方面导致润滑油消耗的迅速上升,进而提升运行成本,在此背景下刮碳环技术应运而生。现有技术中,在气缸套内设置刮碳环主要有两类结构形式,一种是通过在气缸套内合适位置喷涂复合材料形成刮碳环,另外一种是设计单独的与气缸套配套的刮碳环配件。喷涂工艺制备的刮碳环由于对于复合材料要求较高,加上结构本身的缺陷,目前应用的已经较为有限。而单独设计的刮碳环配件,由于与气缸套配合较为紧密,且易于更换和维修,因而是目前活塞表面除碳的主要方式。但是现有技术中的刮碳环配件存在结构本身硬度低、易损坏的缺陷,因而十分有必要对刮碳环的配方及制备工艺进行适当研究和改进。
技术实现要素:本发明目的是提供一种采用离心铸造工艺制备的刮碳环,所制备的刮碳环具有抗拉强度高、不易损坏的优点。本发明的技术方案详述如下。一种刮碳环,采用离心铸造工艺制备而成,其金相结构为A型石墨+95%以上珠光体+少量铁素体,以重量百分比计,该刮碳环的化学组成具体为:碳2.6~3.0%、硅1.7~2.2%;磷0.25~0.5%、硫<0.1%、锰0.5~1.0%、硼0.25~0.5%、铜0.3~0.6%、铬<0.2%、钼0.3~0.7%、镍0.3~0.6%;余量为Fe。所述刮碳环,以重量百分比计,该刮碳环的化学组成具体可以为:碳2.75%、硅1.8%;磷0.3%、硫0.05%、锰0.7%、硼0.38%、铜0.4%、铬0.1%、钼0.4%、镍0.35%;余量为Fe。所述刮碳环,以重量百分比计,该刮碳环的化学组成具体还可以为:碳2.9%、硅2.1%;磷0.3%、硫0.05%、锰0.7%、硼0.3%、铜0.5%、铬0.1%、钼0.47%、镍0.5%;余量为Fe。所述刮碳环的制备方法,采用离心铸造工艺,具体包括如下步骤:(1)熔炼原料,具体为:按比例称取规定的原料,采用中频感应电炉1450℃~1500℃熔炼,出铁液时采用顺流孕育方式加入占出炉铁液重量0.3~0.5%的粒度为0.8~1.8mm的硅钡孕育剂;(2)浇注模具,获得刮碳环铸件毛坯,具体为:采用水冷金属型湿涂料离心铸造工艺生产刮碳环铸件,铁液注入浇注机时采用顺流孕育方式加入占注入浇注机铁液重量0.05~0.12%的粒度为0.5~0.8mm的硅钡孕育剂,具体参数为,浇铸温度1410℃~1430℃,浇注机转速1200~1500r/min,模具预热温度350℃~400℃,涂料厚度0.5~0.8mm,出模温度800℃~850℃;单个刮碳环铸件毛坯壁厚6~9mm;浇铸时铸件可为一切多毛坯,即,可在一个毛坯上制取多个刮碳环;(3)精加工,获得刮碳环铸件,具体为:对步骤(2)中所得刮碳环铸件毛坯进行内孔、外圆的切削加工,工艺流程如下:粗车外圆→粗铰内孔→去应力退火→修车→精铰内孔→精车→倒角;其中的精车工序优选采用全功能数控机床,可实现一次装夹,同时完成内孔、外圆及端面的加工,而且具有加工精度高、加工质量好、生产效率高的优点。对本发明所提供的刮碳环进行检测表明,其金相结构为A型石墨+95%以上珠光体+少量铁素体,其中石墨尺寸4~7级,磷共晶明亮、中等均匀网状分布;进一步检测实验表明,该刮碳环抗拉强度可达到350MPa以上,硬度大于240HB,弹性模量大于140GPa,能够较好满足实际使用需求。总体而言,本发明所提供的刮碳环具有生产周期短、成本低、抗拉强度高等优点,初步应用实验表明,能够较好去除活塞表面积炭,降低润滑油消耗,且使用寿命较长,具有较好的实用价值和推广应用意义。附图说明图1为实施例1所制备的刮碳环的金相结构图;图2为图1中金相结构的100×放大图;图3为图1中金相结构的500×放大图。具体实施方式下面通过实施例对本发明做进一步的解释说明。实施例1以重量百分比计,本实施例所提供的刮碳环的化学组成具体为:元素CSiPSMnBCuCrMoNi铁重量百分比(%)2.751.80.30.050.70.380.40.10.40.35余量本实施例所述刮碳环采用离心铸造工艺制备而成,具体制备步骤简述如下。(1)熔炼原料,具体为:按比例称取规定的原料,采用中频感应电炉1460℃熔炼,出铁液时采用顺流孕育方式加入占出炉铁液重量0.35%的粒度为1.0mm的硅钡孕育剂;(2)浇注模具,获得刮碳环铸件毛坯,具体为:采用水冷金属型湿涂料离心铸造工艺生产刮碳环铸件,铁液注入浇注机时采用顺流孕育方式加入占注入浇注机铁液重量0.08%的粒度为0.6mm的硅钡孕育剂,具体参数为,浇铸温度1420℃,浇注机转速1300r/min,模具预热温度365℃,涂料厚度0.6mm,出模温度820℃;单个刮碳环铸件毛坯壁厚6~9mm;浇铸时铸件为一切多毛坯,即,可在一个毛坯上制取多个刮碳环;(3)精加工,获得刮碳环铸件,具体为:对步骤(2)中所得刮碳环铸件毛坯进行内孔、外圆的切削加工,工艺流程如下:粗车外圆→粗铰内孔→去应力退火→修车→精铰内孔→精车→倒角;其中的精车工序采用全功能数控机床,可实现一次装夹,同时完成内孔、外圆及端面的加工。对所制备的刮碳环毛坯制样检测,使用BX51RF金相显微镜检测金相,使用HB-3000B电子布氏硬度计检测硬度,使用WDW300KN万能试验机检测抗拉强度、弹性模量。金相检测结果如图1~3所示,从图中可以看出,该刮碳环的金相为A型石墨+95%以上珠光体+少量铁素体,石墨尺寸4~7级,磷共晶明亮、中等均匀网状分布。硬度检测结果表明,该刮碳环的硬度大于255HB。抗拉强度和弹性模量检测表明,其抗拉强度达到370MPa以上,弹性模量大于158GPa。实施例2以重量百分比计,本实施例所提供的刮碳环的化学组成具体为:元素CSiPSMnBCuCrMoNi铁重量百分比(%)2.92.10.30.050.70.30.50.10.470.5余量本实施例所述刮碳环采用离心铸造工艺制备而成,具体制备步骤简述如下。(1)熔炼原料,具体为:按比例称取规定的原料,采用中频感应电炉1480℃熔炼,出铁液时采用顺流孕育方式加入占出炉铁液重量0.4%粒度为1.5mm的硅钡孕育剂(2)浇注模具,获得刮碳环铸件毛坯,具体为:采用水冷金属型湿涂料离心铸造工艺生产刮碳环铸件,铁液注入浇注机时采用顺流孕育方式加入占注入浇注机铁液重量0.11%粒度为0.7mm的硅钡孕育剂,具体参数为,浇铸温度1425℃,浇注机转速1400r/min,模具预热温度390℃,涂料厚度0.7mm,出模温度845℃;单个刮碳环铸件毛坯壁厚6~9mm;浇铸时铸件为一切多毛坯,即,可在一个毛坯上制取多个刮碳环;(3)精加工,获得刮碳环铸件,具体为:对步骤(2)中所得刮碳环铸件毛坯进行内孔、外圆的切削加工,工艺流程如下:粗车外圆→粗铰内孔→去应力退火→修车→精铰内孔→精车→倒角;其中的精车工序采用全功能数控机床,可实现一次装夹,同时完成内孔、外圆及端面的加工。对所制备的刮碳环毛坯制样检测,使用BX51RF金相显微镜检测金相,使用HB-3000B电子布氏硬度计检测硬度,使用WDW300KN万能试验机检测抗拉强度、弹性模量。检测结果显示,该刮碳环的金相同样为A型石墨+95%以上珠光体+少量铁素体,石墨尺寸4~7级,磷共晶明亮、中等均匀网状分布;其硬度大于250HB;其抗拉强度达到375MPa以上,弹性模量大于160GPa。