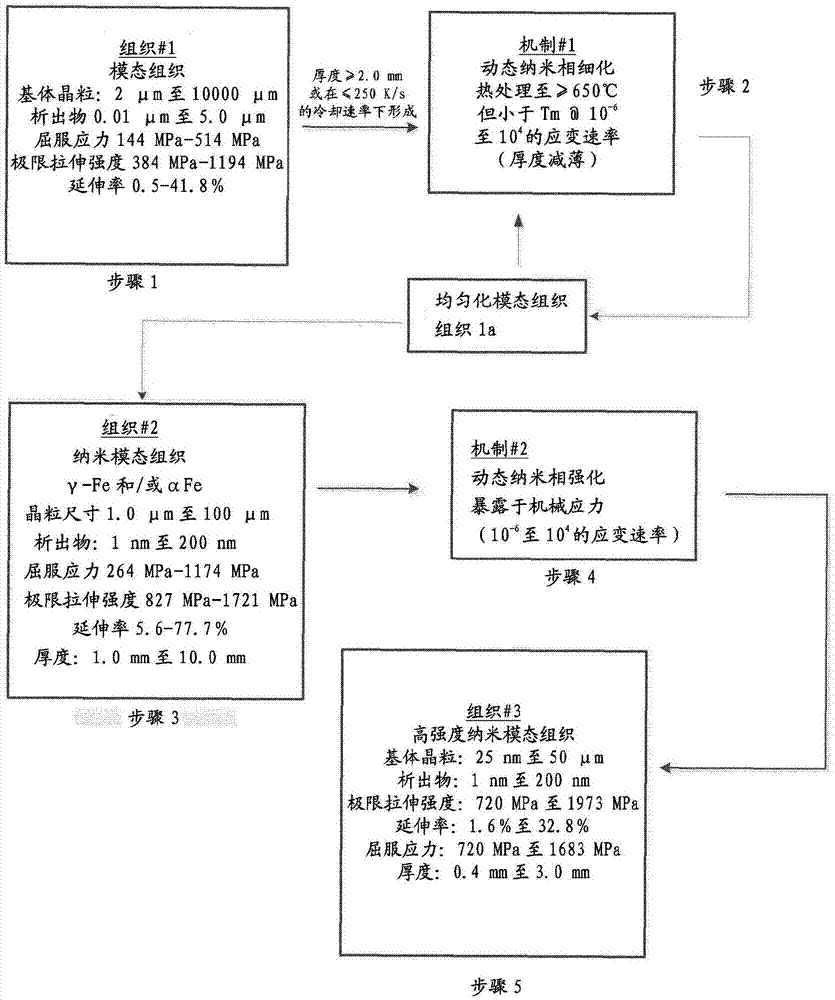
本申请要求2015年12月28日提交的美国临时申请62/271,512的权益。
技术领域:
本发明涉及在拉延过程中防止金属合金的延迟开裂,其可由氢侵蚀发生。该合金应用于在车辆中使用的零件或部件,例如白车身、车架、底盘或面板。
背景技术:
:铁合金(包括钢)占全世界金属制备的绝大多数。自从工业革命形成人类技术发展的支柱之前,钢铁的发展驱动了人类进步。特别地,钢通过使建筑到达更高、使桥梁跨越更长距离和使人类旅行得更远而改进了人类的日常生活。因此,钢的制备随着时间持续提高,目前美国每年制备大约1亿吨,其估值$750亿。基于测量的性质(特别是失效之前的拉伸应力和最大拉伸应变),这些钢合金可分为三个等级。这三个等级是:低强度钢(LSS)、高强度钢(HSS)和先进高强度钢(AHSS)。低强度钢(LSS)通常按照表现出小于270MPa的拉伸强度分类并且包括如无晶隙钢和低碳钢这样的类型。高强度钢(HSS)按照表现出从270至700MPa的拉伸强度分类并且包括如高强度低合金钢、高强度无晶隙钢和烘烤硬化钢这样的类型。先进高强度钢(AHSS)钢由大于700MPa的拉伸强度分类并且包括如马氏体钢(MS)、双相(DP)钢、转变诱发塑性(TRIP)钢和复相(CP)钢这样的类型。随着强度水平提高,钢的最大拉伸延伸率(延展性)的趋势是负的,伴随在高拉伸强度下延伸率降低。例如,LSS、HSS和AHSS的拉伸延伸率分别在25%至55%、10%至45%和4%至30%范围。在车辆中钢的使用也高,其中先进高强度钢(AHSS)目前为17%并且预测在接下来的年份中增长300%[美国钢铁协会,(2013),Profile2013,Washington,D.C.]。随着目前市场趋势和政府法规将车辆推向更高效率,AHSS因其提供高强度质量比的能力而越来越受追捧。钢的可成形性对于汽车应用具有独特重要性。用于下一代车辆的预测零件需要材料能够塑性变形(有时严重地),使得将获得复杂的几何形状。高可形成性钢通过允许计设较复杂零件几何形状(促进期望的重量减小)为零件设计者提供益处。可进一步将可成形性分为两种不同形式:边缘可成形性和块体可成形性。边缘可成形性是边缘待成形为某一形状的能力。边缘(为自由表面)受缺陷(例如由片材边缘的产生所致的片材中的组织改变或裂纹)支配。在成形操作过程中这些缺陷不利地影响边缘可成形性,导致边缘处有效延展性降低。在另一方面块体可成形性受固有延展性、组织、和成形操作过程中金属的相关应力状态支配。块体可成形性主要受可用的变形机制(例如位错、孪晶和相转变)影响。当这些可用的变形机制在材料内饱和时,块体可成形性最大化,其中由于这些机制的可用性和数量提高而产生改进的块体可成形性。可通过各种方法(包括但不限于拉伸测试、打压测试、弯曲测试、和拉延测试)测量块体可成形性。AHSS材料中高强度经常导致有限的块体可成形性。特别地,对于大量钢材料而言,缺少通过杯式拉延(cupdrawing)限制拉延比(其中DP980材料通常实现小于2的拉延比),由此限制了它们在车辆应用中的潜在用途。对于许多AHSS材料而言氢辅助延迟开裂也是限制因素。关于氢辅助延迟开裂的特性存在许多理论,但是已经确认的是其在钢中发生必须存在三个部分:材料具有大于800MPa的拉伸强度、高连续应力/载荷、和氢离子浓度。仅当所有三个部分存在时才会发生氢辅助延迟开裂。因为在AHSS材料中期望拉伸强度大于800MPa,所以在可预见的未来对AHSS材料而言氢辅助延迟开裂将仍存在问题。例如,可以冲压在车辆中使用的结构或非结构零件或部件(例如白车身、车架、底盘、或面板),并且在冲压中可存在拉延操作以实现某些目标几何形状。在完成了拉延的冲压零件或部件的这些区域然后可发生延迟开裂,导致所得零件或部件报废。概述用于改进金属性合金中抗延迟开裂性的方法,其包括:a.供应金属合金,该金属合金包含至少50原子%铁和至少四种或更多种选自Si、Mn、B、Cr、Ni、Cu、Al或C的元素,并且熔化所述合金并以≤250K/s的速率冷却或凝固为≥2.0mm的厚度,并且形成具有Tm和2至10000μm的基体晶粒的合金;b.通过加热所述合金至≥650℃和小于所述合金的Tm的温度,并且以10-6至104的应变速率向所述合金施加应力,并且冷却所述合金至环境温度,将所述合金加工成具有≤10mm厚度的片材;c.以10-6至104的应变速率向所述合金施加应力并且加热所述合金至至少600℃和小于Tm的温度,并且以具有≤3mm厚度的具有720至1490MPa拉伸强度和10.6至91.6%延伸率并具有从0至10%磁相体积%的片材形式使所述合金成形;其中步骤(c)中成形的所述合金显示临界拉延速度(SCR)或临界拉延比(DCR),其中以小于SCR的速度或以大于DCR的拉延比拉延所述合金产生第一磁相体积V1,并且其中以等于或大于SCR的速度或以小于或等于DCR的拉延比拉延所述合金产生磁相体积V2,其中V2<V1。另外,本公开内容还涉及用于改进金属性合金中抗延迟开裂性的方法,其包括:a.供应金属合金,该金属合金包含至少50原子%铁和至少四种或更多种选自Si、Mn、B、Cr、Ni、Cu、Al或C的元素,并且熔化所述合金并以≤250K/s的速率冷却或凝固为≥2.0mm的厚度,并且形成具有Tm和2至10000μm的基体晶粒的合金;b.通过加热所述合金至≥650℃和小于所述合金的Tm的温度,并且以10-6至104的应变速率向所述合金施加应力,并且冷却所述合金至环境温度,将所述合金加工成具有≤10mm厚度的片材;c.以10-6至104的应变速率向所述合金施加应力并且加热所述合金至至少600℃和小于Tm的温度,并且以具有≤3mm厚度的具有720至1490MPa拉伸强度和10.6至91.6%延伸率并具有从0至10%磁相体积%(Fe%)的片材形式成形所述合金;其中当步骤(c)中的所述合金经受拉延时,所述合金显示1%至40%的磁相体积。附图简要说明参考附图可更好地理解以下详细描述,出于说明性目的提供所述附图并且不将其视为对本发明的任何方面进行限制。图1通过板坯连铸制备片材的加工路线。图2本文合金中以小于SCR和等于或大于SCR速度在应力下组织发展的两种途径。图3本文合金中在应力下组织发展的已知途径。图4在高速变形下组织发展的新途径。图4A说明(a)在拉延杯和(b)在由拉延所致的该杯中的代表性应力。图5来自a)合金6和b)合金9的实验室铸造50mm板坯的图像。图6来自a)合金6和b)合金9的实验室铸造之后的热轧片材的图像。图7来自a)合金6和b)合金9的实验室铸造和热轧之后的冷轧片材的图像。图8来自合金1的完全处理和退火的1.2mm厚片材中显微组织的明场TEM显微照片:a)低放大倍数图像;b)高放大倍数图像。图9来自合金1的完全处理和退火的1.2mm厚片材中显微组织的背散射SEM显微照片:a)低放大倍数图像;b)高放大倍数图像。图10来自合金6的完全处理和退火的1.2mm厚片材中显微组织的明场TEM显微照片:a)低放大倍数图像;b)高放大倍数图像。图11来自合金6的完全处理和退火的1.2mm厚片材中显微组织的背散射SEM显微照片:a)低放大倍数图像;b)高放大倍数图像。图12变形之后合金1片材中显微组织的明场TEM显微照片:a)低放大倍数图像;b)高放大倍数图像。图13变形之后合金6片材中显微组织的明场TEM显微照片:a)低放大倍数图像;b)高放大倍数图像。图14合金1和合金6中拉伸变形前后磁相的体积对比,表明变形之前片材中再结晶模态组织主要是奥氏体和非磁性的,但是材料在变形过程中经历大量转变,导致高体积分数的磁相。图15以0.8mm/s采用1.78拉延比拉延并暴露于氢45分钟之后来自合金1的杯的图。图16通过暴露于100%氢45分钟之后延迟开裂的合金1的断裂表面。注意到缺少可见晶界的脆性(刻面)断裂表面。图17通过暴露于100%氢45分钟之后延迟开裂的合金6的断裂表面。注意到缺少可见晶界的脆性(刻面)断裂表面。图18通过暴露于100%氢45分钟之后延迟开裂的合金9的断裂表面。注意到缺少可见晶界的脆性(刻面)断裂表面。图19用于组织分析的样品位置;位置1杯顶部,位置2杯侧壁中部。图20以0.8mm/s拉延的来自合金1的杯底部中显微组织的明场TEM显微照片:a)低放大倍数图像;b)高放大倍数图像。图21以0.8mm/s拉延的来自合金1的杯壁中显微组织的明场TEM显微照片:a)低放大倍数图像;b)高放大倍数图像。图22以0.8mm/s拉延的来自合金6的杯底部中显微组织的明场TEM显微照片:a)低放大倍数图像;b)高放大倍数图像。图23以0.8mm/s拉延的来自合金6的杯壁中显微组织的明场TEM显微照片:a)低放大倍数图像;b)高放大倍数图像。图24在以0.8mm/s杯式拉延之后来自合金1和合金6的杯壁和底部中磁相的体积对比。图25氢中来自合金1的拉延杯中延迟开裂与拉延比的依赖关系。注意到在1.4拉延比下,没有发生延迟开裂,并且在1.6拉延比下,仅发生非常少的延迟开裂。图26氢中来自合金6的拉延杯中延迟开裂与拉延比的依赖关系。注意到在1.6拉延比下,没有发生延迟开裂。图27氢中来自合金9的拉延杯中延迟开裂与拉延比的依赖关系。注意到在1.6拉延比下,没有发生延迟开裂。图28氢中来自合金42的拉延杯中延迟开裂与拉延比的依赖关系。注意到在1.6拉延比下,没有发生延迟开裂。图29氢中来自合金14的拉延杯中延迟开裂与拉延比的依赖关系。注意到在空气中或100%氢中持续45分钟在测试的任何拉延比下没有发生延迟开裂。图30以不同拉延速度采用1.78拉延比并暴露于氢45分钟之后来自合金1的杯的图。图31氢中来自合金1的拉延杯中延迟开裂与拉延速度的依赖关系。注意到在100%氢气氛中45分钟之后在19mm/s拉延速度下降低至零裂纹。图32氢中来自合金6的拉延杯中延迟开裂与拉延速度的依赖关系。注意到在100%氢气氛中45分钟之后在9.5mm/s拉延速度下降低至零裂纹。图33以203mm/s拉延的来自合金1的杯底部中显微组织的明场TEM显微照片:a)低放大倍数图像;b)高放大倍数图像。图34以203mm/s拉延的来自合金1的杯壁中显微组织的明场TEM显微照片:a)低放大倍数图像;b)高放大倍数图像。图35以203mm/s拉延的来自合金6的杯底部中显微组织的明场TEM显微照片:a)低放大倍数图像;b)高放大倍数图像。图36以203mm/s拉延的来自合金6的杯壁中显微组织的明场TEM显微照片:a)低放大倍数图像;b)高放大倍数图像。图37在不同速度下拉延的来自合金1和合金6的拉延杯的壁和底部的Feritscope磁性测量。图38在不同速度下拉延的来自商购DP980钢的拉延杯的壁和底部的Feritscope磁性测量。图39采用不同拉延比拉延之后来自合金6的杯的图;a)0.85mm/s,b)25mm/s。图40采用不同拉延比拉延之后来自合金14的杯的图;a)0.85mm/s,b)25mm/s。图41采用Feritscope测量的拉延测试结果,显示当拉延速度从0.85mm/s提高至25mm/s时,合金6的杯中延迟开裂抑制并且合金14中拉延极限比提高。详细描述本文钢合金优选通过如图1A和1B说明的机制经历组织形成的独特途径。初始组织形成开始于熔化合金并冷却和凝固并形成具有模态组织(组织#1,图1A)的合金。较厚的铸造状态组织(例如大于或等于2.0mm的厚度)导致相对较低的冷却速率(例如小于或等于250K/s的冷却速率)和相对较大的基体晶粒尺寸。因此厚度可优选在2.0mm至500mm的范围内。在实验室铸造中模态组织优选表现出具有从2μm至10000μm的枝晶长度和/或晶粒尺寸的奥氏体基体(γ-Fe)和0.01至5.0μm尺寸的析出物。取决于起始厚度尺寸和具体合金化学组成,本文具有模态组织的钢合金典型地表现出以下拉伸性质,从144至514MPa的屈服应力,在从384至1194MPa范围内的极限拉伸强度,和从0.5至41.8的总延展性。本文具有模态组织(组织#1,图1A)的钢合金可经过纳米相细化(机制#1,图1A)通过将钢合金暴露于最终导致形成纳米模态组织(组织#2,图1A)的一个或多个热和应力循环(例如热轧)从而得到均匀化和细化。更具体地,当在大于或等于2.0mm的厚度下形成和/或在小于或等于250K/s的冷却速率下形成时,优选将模态组织加热至650℃温度至小于固相线温度的温度,和更优选的小于固相线温度(Tm)50℃,并且优选处于10-6至104的应变速率和厚度减薄。随着钢合金经历在连续施加温度和应力过程中机械变形和厚度减薄例如可在热轧过程中被构造发生的,转变为组织#2优选经过中间均匀化模态组织(组织#1a,图1A)以连续的方式发生。纳米模态组织(组织#2,图1)优选具有主要奥氏体基体(γ-Fe)并且取决于化学组成可额外地含有铁素体晶粒(α-Fe)和/或析出物例如硼化物(如果存在硼)和/或碳化物(如果存在碳)。取决于起始晶粒尺寸,在实验室铸造中纳米模态组织典型地表现出具有1.0至100μm晶粒尺寸的主要奥氏体基体(γ-Fe)和/或1.0至200nm尺寸的析出物。取决于合金化学组成、起始铸造厚度和具体加工参数,基体晶粒尺寸和析出物尺寸可比商业制备大至多5倍。本文具有纳米模态组织的钢合金典型地表现出以下拉伸性质,从264至1174MPa的屈服应力,在从827至1721MPa范围内的极限拉伸强度,和从5.6至77.7%的总延展性。因此优选通过热轧形成组织#2,并且厚度减薄优选提供1.0mm至10.0mm的厚度。因此,可理解施加至模态组织(初始在2.0mm至500mm范围内)的厚度减薄是这样的:厚度减薄导致在1.0mm至10.0mm范围内的减小的厚度。当本文具有纳米模态组织(组织#2,图1A)的钢合金在环境/接近环境温度下(例如25℃下+/-5℃)经受应力(优选经过冷轧并且优选以10-6至104的应变速率)时,动态纳米相强化机制(机制#2,图1A)被激活,导致形成高强度纳米模态组织(组织#3,图1A)。厚度现在优选减小至0.4mm至3.0mm。高强度纳米模态组织典型地表现出铁素体基体(α-Fe),其取决于合金化学组成可额外地含有奥氏体晶粒(γ-Fe)和可包括硼化物(如果存在硼)和/或碳化物(如果存在碳)的析出物晶粒。在实验室铸造中高强度纳米模态组织典型地表现出25nm至50μm的基体晶粒尺寸和1.0至200nm尺寸的析出物晶粒。本文具有高强度纳米模态组织的钢合金典型地表现出以下拉伸性质,从720至1683MPa的屈服应力,在从720至1973MPa范围内的极限拉伸强度,和从1.6至32.8%的总延展性。当经受退火例如在合金熔点以下加热,伴随铁素体晶粒返回奥氏体的转变(其导致形成再结晶模态组织(组织#4,图1B))时高强度纳米模态组织(组织#3,图1A和图1B)有能力经历再结晶(机制#3,图1B)。还发生纳米级析出物的部分溶解。取决于合金化学组成,材料中硼化物和/或碳化物的存在是可能的。对于完全转变而言优选的温度范围发生在从650℃和小于具体合金的Tm。当再结晶时,组织#4含有(与在再结晶之前发现的对比)少数的位错或孪晶,并且可在一些再结晶晶粒中发现堆垛层错。注意到在从400至650℃的较低温度下,可发生回复机制。在实验室铸造中再结晶模态组织(组织#4,图1B)典型地表现出具有0.5至50μm晶粒尺寸的主要奥氏体基体(γ-Fe)和1.0至200nm尺寸的析出物晶粒。取决于合金化学组成、起始铸造厚度和具体加工参数,基体晶粒尺寸和析出物尺寸可比商业制备大至多2倍。因此晶粒尺寸可在0.5μm至100μm范围内。本文具有再结晶模态组织的钢合金典型地表现出以下拉伸性质:从142至723MPa的屈服应力,在从720至1490MPa范围内的极限拉伸强度,和从10.6至91.6%的总延展性。通过板坯连铸制备片材图1C现在说明在板坯连铸中如何优选实现图1A和1B中的机制和组织。其开始于通过熔化合金的铸造工序,通过在大于合金熔点范围内的温度下加热本文的合金并在合金的熔化温度以下冷却,其对应于优选在1x103至1x10-3K/s范围内冷却从而形成组织1(模态组织)。铸造状态厚度将取决于具有单或双带式铸造的制备方法,厚度典型地在2至40mm范围内,薄板坯连铸典型地厚度在20至150mm范围内并且厚板坯连铸典型地厚度在大于150至500mm范围内。因此,总体上如前所述铸造状态厚度可落在2至500mm范围内,并且在其中以1mm增量的所有值。因此,铸造状态厚度可为2mm、3mm、4mm等,直至500mm。优选完成热轧来自厚板坯工艺的凝固板坯,由此提供动态纳米相细化,使得铸造板坯降低至中间厚度板坯(有时称作转移条(transferbar))。转移条将优选具有在50mm至300mm范围内的厚度。然后优选采用可变数量的热轧机架(strand)(每个铸造机器典型地1或2个)来热轧转移条以制备具有纳米模态组织的热带卷材,热带卷材为厚度典型地在1至10mm范围内的钢卷材。优选在小于固相线温度(即熔点)50℃向下至650℃的温度范围施加这样的热轧。在薄板坯连铸情况下,优选在铸造之后直接热轧该铸造状态板坯来制备厚度典型地在1至10mm范围内的热带卷材。在此情况下再一次优选在小于固相线温度(即熔点)50℃向下至650℃的温度范围施加热轧。冷轧(对应于动态纳米相强化)然后可用于较薄规格的片材制备,其用于实现特定应用的目标厚度。对于AHSS而言,较薄规格通常目标在0.4mm至3.0mm范围内。为了实现这种规格厚度,在中间退火之前,可通过优选采用1至50%总压下量的单道次或多道次施加冷轧。可在各种轧机(包括Z-轧机、Z-hi轧机、连轧机、可逆式轧机等)中和采用从1至15各种数量的轧制机架完成冷轧。因此,在热轧卷材中实现的1至10mm范围内的规格厚度然后可在冷轧中降低至0.4mm至3.0mm厚度。取决于材料性质和设备能力,每道次典型的压下量为5至70%。优选地,道次数将在1至8范围内并且总压下量从10至50%。在冷轧之后,完成中间退火(确定为图1B中作为再结晶的机制3)并且工艺重复从1至9个循环直至实现最终规格目标。取决于具体工艺流程,尤其是起始厚度和热轧规格压下的量,优选施加退火来回复材料的延展性以允许额外的冷轧规格压下量。这在图1b中显示,例如其中冷轧的高强度纳米模态组织(组织#3)在小于Tm退火从而产生再结晶模态组织(组织#4)。可通过使用常规方法(例如分批退火或连续退火线)和优选在600℃直至Tm范围的温度下退火中间卷材。然后可相似地通过使用常规方法(例如分批退火或连续退火线)退火处于本文0.4mm至3.0mm厚度具有来自本文合金的最终目标规格的冷轧片材的最终卷材,从而提供再结晶模态组织。常规分批退火炉在从400至900℃的优选目标范围内工作,总退火时间长,其包括加热,达到目标温度的时间和冷却速率,且总时间为0.5至7天。连续退火优选包括退火和酸洗线或连续退火线,并且包括从600至1250℃的优选温度与从20至500s的暴露时间。因此,退火温度可落入600℃直至Tm的范围内并持续20s至几天的时间段。如所指,退火的结果产生本文作为再结晶模态组织所描述的,或如图1B中所说明的组织#4。本文描述了实验室模拟在每个加工步骤从板坯制备以上片材。在案例实施例#1中展示了经过加工的合金性质演变。最终片材产品(退火卷材)中的显微组织在加工成具有0.4mm至3.0mm、和优选处于或小于2mm厚度的退火片材之后,本文的合金形成本文确定的再结晶模态组织,其在实验室铸造中典型地表现出具有0.5至100μm晶粒尺寸的主要奥氏体基体(γ-Fe)和1.0至200nm尺寸的析出物晶粒。取决于合金化学组成可存在一些铁素体(α-Fe),并且铁素体可通常在从0至50%范围。取决于合金化学组成、起始铸造厚度和具体加工参数,基体晶粒尺寸和析出物尺寸可比商业制备大至多2倍。本文考虑的基体晶粒落入从0.5至100μm尺寸范围内。本文具有再结晶模态组织的钢合金典型地表现出以下拉伸性质:从142至723MPa的屈服应力,在从720至1490MPa范围内的极限拉伸强度,和从10.6至91.6%的总延展性。当具有0至10%磁相体积的本文具有再结晶模态组织(组织#4,图2)的钢合金经历由拉延(其中拉延是指在施加应力下合金的延伸)所致的变形时,本文认识到这可在两种条件中任一种下发生。具体地,可在小于临界速度(<SCR)的速度下或在大于或等于这样的临界速度(≥SCR)的速度下施加拉延。或者,可在大于临界拉延比(DCR)的拉延比下或在小于或等于临界拉延比(DCR)的拉延比下拉延再结晶模态组织。再一次参见图2。本文中拉延比被定义为当形成完全杯时(即没有凸缘)坯件的直径除以冲模的直径。另外,已经发现当在小于临界速度(<SCR)的速度下,或在大于临界拉延比(>DCR)的拉延比下拉延时原始存在的磁相体积水平(0至10%)将提高至“V1”量,其中“V1”在大于10%至60%的范围内。供选择地,如果在大于或等于临界速度(≥SCR)的速度下或在小于或等于临界拉延比(≤DCR)的拉延比下拉延时,磁相体积将提供“V2”量,其中V2在1%至40%的范围内。图3说明当本文具有再结晶模态组织的合金经历小于SCR或在大于临界拉延比DCR的拉延比下拉延时发生了什么和形成了两个显微组分(确定为显微组分1和显微组分2)。这两种显微组分的形成取决于奥氏体的稳定性和两种类型的机制:纳米相细化与强化机制和基于位错的机制。本文具有再结晶模态组织的合金是这样的,其含有具有相对稳定的奥氏体的区域(意味着在变形过程中不可用于转变成铁素体相)和具有相对不稳定的奥氏体相的区域(意味着在塑性变形时可用于转变成铁素体)。在小于SCR的拉延速度下或在大于临界拉延比(DCR)的拉延比下变形时,具有相对稳定的奥氏体的区域保持奥氏体属性并且被描述为在最终的混合显微组分组织(组织#5,图3)中代表显微组分1的组织#5a(图3)。用奥氏体晶粒(γ-Fe)表示显微组织中未转变的部分(图3组织#5a),其未被细化并典型地具有从0.5至100μm的尺寸。应注意考虑了组织#5a中未转变的奥氏体通过形成三维位错排列通过塑性变形而变形。将位错理解为是晶体结构内的晶体缺陷或不规则性的冶金术语,其有助于变形过程同时使材料破坏少量冶金结合而不是晶体内的所有结合。这些高度变形的奥氏体晶粒含有相对高密度的位错,由于目前已知的在变形过程中发生的位错过程其可形成排列在晶胞内的致密位错缠结,导致高分数的位错。具有相对不稳定的奥氏体的区域在小于SCR的速度下或在大于DCR的拉延比下变形时经历转变成铁素体,形成在最终的混合显微组分组织(组织#5,图3)中代表显微组分2的组织#5b(图3)。纳米相细化发生在这些区域中,导致形成细化的高强度纳米模态组织(组织#5b,图3)。因此,用具有通过纳米相细化与强化(机制#1,图2)形成的额外析出物的细化铁素体晶粒(α-Fe)代表显微组织的转变部分(图3,组织#5b)。在实验室铸造中铁素体(α-Fe)细化晶粒的尺寸从100至2000nm变化,并且析出物的尺寸在从1.0至200nm范围内。组织5a和组织5b中基体晶粒的总尺寸因此典型地从0.1μm至100μm变化。优选地,引发这种转变的应力在>142MPa至723MPa范围内。导致组织#5b形成的纳米相细化与强化机制(图3)因此是动态的过程,在其中亚稳定的奥氏体相转变成具有析出物的铁素体,通常导致基体相晶粒细化(即晶粒尺寸减小)。这发生在如前所述的奥氏体是相对不稳定的随机分布的组织区域内。注意到在相转变之后,新形成的铁素体晶粒也通过位错机制变形并且有助于所测量的总延展性。混合显微组分组织(组织#5,图3)中每个显微组分(组织#5a对组织#5b)所得的体积分数取决于合金化学组成和对初始再结晶模态组织形成的加工参数。典型地,低至5体积百分数和高至75体积百分数的合金组织将在分布的组织区域内转变,形成显微组分2且保持未转变的剩余部分代表显微组分1。因此,显微组分2可为从5至75以0.1%增量的所有单个体积百分数值(即5.0%、5.1%、5.2%、…直至75.0%)而显微组分1可为从75至5以0.1%增量的体积百分数值(即75.0%、74.9%、74.8%…降低至5.0%)。取决于合金化学组成,在材料中硼化物(如果存在硼)和/或碳化物(如果存在碳)的存在是可能的。在图2的组织#4中所指出的析出物的体积百分数预期为0.1至15%。虽然难以单独测量这些析出物的磁性性质,但是考虑了它们是非磁性的并因此没有有助于所测量的磁相体积%(Fe%)。如上所述,对于给定合金,可通过对不同奥氏体稳定性水平选择和调节合金化学组成从而控制转变区域(组织#5b)与未转变区域(组织#5a)的体积分数。通常的趋势是随着添加较多奥氏体稳定元素,将提高显微组分1的所得体积分数。奥氏体稳定元素的实例会包括镍、锰、铜、铝和/或氮。注意氮可被发现为在加工过程中来自大气的杂质元素。另外,注意到因为铁素体是磁性的并且奥氏体是非磁性的,所以存在的磁相的体积分数为评价组织#5a或组织#5b的相对存在提供了方便的方法。因此如在图3所注意到的,组织#5被指出具有对应于显微组分2含量的磁相体积V1,并且落入从>10至60%范围内。本文中磁相体积有时缩写作Fe%,应将其理解为提及存在铁素体和在合金中确定磁性响应的任何其他成分。通过feritscope便利地测量本文的磁相体积。feritscope使用采用直接放置在片材样品上的探针的磁性诱导方法并提供总磁相体积%(Fe%)的直接读数。对于本文所选择的合金而言,在案例实施例#2和#3中展示了对应于在商业制备的退火卷材中片材条件的完全处理和退火的片材中的显微组织和经过变形的显微组织发展。延迟断裂已经显示本文的钢合金在拉延之后经历氢辅助延迟断裂,其中通过冲模的作用将钢坯件拉延至成形模具中。在本文含有的钢合金变形过程中独特的组织形成经历包括具有在图3中提供的组织形成途径的形成混合显微组分组织的途径。已经发现的是当显微组分2的体积分数(按磁相体积测量)达到某一值时,延迟开裂发生。对于延迟开裂而言磁相体积百分数的量含有>10体积%或更大,或典型地从大于10%至60%体积分数的磁相。通过将速度提高至处于或大于临界速度(SCR),磁相体积百分数的量减小至1%至40%并且减小或避免延迟开裂。本文提及延迟开裂是指合金具有这样的特征:处于和/或在暴露于100%氢45分钟之后在环境温度暴露至空气24小时后合金不会开裂。考虑了通过已知为穿晶解理的特有机制发生延迟开裂,通过穿晶解理,转变的铁素体晶粒中某些冶金平面被削弱至它们分离从而引起裂纹萌生并然后通过晶粒扩展的程度。考虑了通过氢扩散至这些平面中来帮助在晶粒内特定平面的这种削弱。如本文公开的,导致延迟开裂的显微组分2的体积分数取决于合金化学组成、拉延条件和周围环境(例如正常空气或纯氢环境)。可通过磁相体积确定显微组分2的体积分数,因为起始晶粒是奥氏体并因此是非磁性的,且转变的晶粒大部分是铁素体(磁性的)(然而考虑可存在一些α-马氏体或ε-马氏体)。因为包括α-铁的转变的基体相和任何马氏体都是磁性的,因此可通过所得磁相体积(V1)监测这一体积分数。在杯式拉延情况下在钢工业目前使用的条件下在本文钢合金中的延迟断裂显示在案例实施例#4中所选的合金,伴随如案例实施例#5中描述的拉延杯中的氢含量分析和案例实施例#6中呈现的断裂分析。通过SEM和TEM分析并在案例实施例#7中描述了拉延杯中的组织转变。拉延是独特类型的变形工艺,因为在变形过程中形成独特的应力状态。在拉延操作过程中,在边缘处限制片材金属坯件,并且内部部分通过冲模被迫进入模具从而将金属拉长成为可具有各种形状(包括环形、正方形或取决于模具设计的差不多任何横截面)的拉延零件。取决于所施加的变形量和复杂冲压零件所期望的,拉延工艺可浅可深。浅拉延用来描述拉延深度小于拉延内径的工艺。拉延至大于内径的深度被称作深拉延(deepdrawing)。本文所指出合金的拉延可优选作为连续模冲压操作的一部分实现。连续模冲压是指一种金属加工方法,其通过一个或多个冲压模具操作台推挤金属带材。每个操作台可进行一个或多个操作直至制备成品零件。因此,连续模冲压操作可包括单步骤操作或包括多个步骤。拉延过程中的拉延比可被定义为当形成完全杯(即没有凸缘)时坯件的直径除以冲模的直径。在拉延工艺过程中,坯件金属需要随着冲击模具而弯曲并且然后沿模具壁向下流动。这产生独特的应力状态(尤其在拉延件的侧壁区域中),可导致三轴应力状态,包括纵向拉伸应力、周向拉伸应力和横向压缩应力。参见图4A,其在(a)中提供拉延杯的图像,以存在于侧壁(小立方块)内的材料块为例,并且在(b)中说明在拉延材料(吹胀立方块(blownupcube))的侧壁中发现的应力(包括纵向拉伸应力(A)、横向压缩应力(B)和周向拉伸应力(C))。这些应力条件然后可导致氢扩散和积累的有利位点,其潜在地导致由于在环境温度下氢扩散而可立即在形成过程中或其后(即延迟开裂)发生的开裂。因此,例如在案例实施例#8和#9中拉延工艺可对本文的钢合金中延迟断裂有显著影响。由于如图4所述变形途径的改变,随着提高拉延速度或减小拉延比,本文合金中对延迟开裂的敏感性降低(即表现出开裂的可能性)。案例实施例#10中显示随着提高速度至或大于SCR,总磁相体积(即磁相的总体积分数,可包括铁素体、ε马氏体、α马氏体或这些相的任何组合)降低。常规钢牌号例如DP980没有显示如案例实施例#11中所示的组织或性能对拉延速度的依赖性。防止延迟开裂的组织发展新途径本公开内容的主题是新现象:如图3和图4中所述存在的显微组分1和2的量和所得磁相体积百分数(Fe%)的改变。在某些拉延条件(其依赖速度和拉延比两者)下,从组织#4(再结晶模态组织)转变至组织#5(混合显微组分组织)可按如图2的概述中提供的两种方式之一发生。这种特征是指出的拉延条件导致在图4的组织#5中提供的总磁相体积%(Fe%)小于图3的组织#5中的磁相体积%(Fe%)。如图4中提供的,对于本文合金而言考虑到在图4中提供的拉延条件下,孪晶发生在奥氏体基体晶粒中。注意到孪晶是变形的冶金模式,由此在由称作孪晶晶界的镜(mirror)面分开的母相以外产生具有不同取向的新晶体。显微组分1中这些孪晶区域然后没有经历转变,其意味着显微组分1的体积分数提高并且显微组分2的体积分数相应地降低。对于如图4提供的优选拉延方法而言所得总磁相体积百分数(Fe%)为1至40Fe%。因此,通过提高拉延速度,可减小或避免本文合金中的延迟开裂,然而本文合金可变形并表现出改进的可冷成形性(案例实施例#9)。如案例实施例#11中所示商业钢牌号(例如DP980)没有显示组织或性能与拉延速度的依赖关系。另外,在本发明的广义上下文中,还观察到应优选实现1%至40%的最终磁相体积。因此,不论是否在小于临界拉延速度SCR的速度下、或在大于临界拉延比DCR的拉延比下,还是处于或大于SCR或小于或等于DCR下拉延,合金应是限制最终磁相体积为1%至40%的合金。在这种情况下,再一次减少和/或消除本文的延迟开裂。这在例如采用合金14的案例实施例#8中提供并在图29中显示,其中甚至在低拉延速度(0.8mm/s)下都没有观察到延迟开裂。额外的实例是在1.4及以下的拉延比下的图27中合金9和图28中合金42,以及在1.2及以下的拉延比下的图25中合金1。片材合金:化学组成和性质在表1中显示本文合金的化学组成,表1提供了所使用的优选原子比。表1合金化学组成如可从表1看出,本文合金是铁基金属合金,具有大于50原子%Fe,更优选大于60原子%Fe。最优选,可描述本文合金为以所指出的原子百分数包含以下元素、基本上由以下元素组成、或由以下元素组成:Fe(61.30至80.19原子%),Si(0.2至7.02原子%),Mn(0至15.86原子%),B(0至6.09原子%),Cr(0至18.90原子%),Ni(0至6.80原子%),Cu(0至3.66原子%),C(0至3.72原子%),Al(0至5.12原子%)。另外,可领会本文合金是这样的,它们包含Fe和至少四种或更多种、或五种或更多种、或六种或更多种选自以下的元素:Si、Mn、B、Cr、Ni、Cu、Al或C。最优选,本文合金是这样的,它们包含以下、基本上由以下组成、或由以下组成:60原子%或更大水平的Fe以及Si、Mn、B、Cr、Ni、Cu、Al和C。完成本文合金的实验室加工来模拟工业制备(但是以小得多的规模)的每个步骤。这种工艺中的关键步骤包括以下:铸造、隧道炉加热、热轧、冷轧和退火。铸造根据表1中对应的原子比,使用具有已知化学组成和杂质含量的可商购的铁添加剂(ferroadditive)粉末以从3000至3400克范围的装料称取合金。将装料装进置于InduthermVTC800V真空翻转铸造机中的涂覆氧化锆的氧化硅坩埚中。然后在铸造之前机器将铸造腔室和熔化腔室抽空并且然后用氩回填至大气压数次从而防止熔体氧化。熔体采用14kHzRF感应线圈加热直至完全熔融,大约5.25至6.5分钟,其取决于合金组成和装料质量。在观察到最后的固体熔化之后保持在温度下持续额外的30至45秒以提供过热并确保熔体均匀性。然后铸造机器将熔化腔室和铸造腔室抽空,翻转坩埚并将熔体倒入水冷却铜模具中的50mm厚、75至80mm宽和125mm的杯式通道中。在腔室用氩填充至大气压之前使熔体在真空下冷却200秒。在图5中显示来自两种不同合金的实验室铸造板坯的实例图片。热性质使用NetzschPegasus404差示扫描量热仪(DSC)在凝固状态铸造板坯上进行本文合金的热分析。将合金样品装入氧化铝坩埚,然后将其装入DSC。然后DSC将腔室抽空并用氩回填至大气压。然后开始恒定的氩吹扫,并且在气流路径中安装锆吸气剂以进一步减小体系中氧的量。将样品加热直至完全熔融,冷却直至完全凝固,然后以10℃/分钟再加热彻底熔化。从第二熔化获取固相线温度、液相线温度和峰值温度的测量以便确保材料处于平衡状态的代表性测量。在表1列出的合金中,熔化发生在一个或多个阶段中,其中初始熔化从~1111℃开始(取决于合金化学组成)和最终熔化温度直至1440℃(表2)。取决于合金化学组成,熔化行为的变化反映在合金凝固中的相形成。表2对于熔化行为的差热分析数据热轧在热轧之前,将实验室板坯装入LuciferEHS3GT-B18炉来加热。取决于合金熔点Tm以及炉温设定在小于Tm的~50℃,炉设定点在1100℃至1250℃之间变化。在热轧之前使板坯均热处理40分钟以确保板坯达到目标温度。在热轧道次之间将板坯返回炉4分钟以使板坯再加热。将预加热的板坯从隧道炉推出至FennModel0612自动轧机(highrollingmill)中。在使其空气冷却之前通过轧机将50mm厚板坯热轧5至8个道次。在初始道次之后每个板坯减薄在80至85%之间,至7.5和10mm之间的最终厚度。在冷却之后切割每个所得板坯并且底部190mm经过轧机热轧额外的3至4个道次,进一步减薄板材在72至84%之间,至1.6和2.1mm之间的最终厚度。在图6中显示热轧之后来自两种不同合金的实验室铸造板坯的实例图片。密度使用阿基米德方法在允许在空气和蒸馏水两者中称量的特殊构造的天平中对来自热轧材料的样品测量合金的密度。每种合金的密度在表3中列表显示并且发现密度在从7.51至7.89g/cm3范围内。这种技术的精度为±0.01g/cm3。表3合金密度冷轧在热轧之后,所得的片材用铝氧化物介质喷砂以去除轧钢皮,并且然后在FennModel0612自动轧机上冷轧。冷轧采用多道次以将片材的厚度减小至典型的1.2mm的目标厚度。将热轧片材加入以规律性降低辊间隙的轧机中直至达到最小间隙。如果材料还没有达到规格目标,则使用处于最小间隙的额外道次直至实现1.2mm厚度。由实验室轧机能力的限制所致施用了大量道次。在图7中显示来自两种不同合金的冷轧片材的实例图片。退火在冷轧之后,经由线EDM从冷轧片材切割拉伸试样。然后采用表4中所列的不同参数退火这些试样。在Lucifer7HT-K12箱式炉中进行退火1a和1b。在CamcoModelG-ATM-12FL炉中进行退火2和3。在循环结束时将空气正火的试样从炉中去除并使其在空气中冷却至室温。对于炉冷却试样,在退火结束时关掉炉以使样品随炉冷却。注意热处理被选择用于说明而不意图限制范围。可预料到直至略小于每种合金熔点的高温处理。表4退火参数拉伸性质在冷轧和采用表4中所列参数退火之后在本文片材合金上测量拉伸性质。片材厚度为`1.2mm。在Instron3369机械测试框架上利用Instron的Bluehill控制软件完成拉伸测试。所有测试在室温下进行其中底部夹具固定并且顶部夹具被设定以0.012mm/s的速率向上移动。使用Instron的先进视频伸长计收集应变数据。在以下表5至表8中显示处于冷轧和退火状态的表1中所列合金的拉伸性质。极限拉伸强度值可从720变化至1490MPa,伴随从10.6至91.6%的拉伸延伸率。屈服应力在从142至723MPa范围内。本文的钢合金中机械特性值将取决于合金化学组成和加工条件。在热处理1b之后对来自本文合金的片材完成了Feritscope测量,取决于合金化学组成其从0.3变化至3.4Fe%(表6A)。表5在热处理1a之后所选合金的拉伸数据表6在热处理1b之后所选合金的拉伸数据表6A在热处理1b之后合金中的Fe%表7在热处理2之后所选合金的拉伸数据表8在热处理3之后所选合金的拉伸数据案例实施例案例实施例#1:在不同加工步骤下合金1和合金6的性质范围从合金1和合金6铸造具有50mm厚度的实验室板坯。根据表1中的原子比,使用具有已知化学组成和杂质含量的可商购的铁添加剂粉末以从3000至3400克范围的装料称取合金。将装料装进置于InduthermVTC800V真空翻转铸造机中的涂覆氧化锆的氧化硅坩埚中。然后在铸造之前机器将铸造腔室和熔化腔室抽空并用氩回填至大气压数次从而防止熔体氧化。熔体采用14kHzRF感应线圈加热直至完全熔融,大约5.25至6.5分钟,其取决于合金组成和装料质量。在观察到最后的固体熔化之后使其加热额外的30至45秒以提供过热并确保熔体均匀性。然后铸造机器将熔化腔室和铸造腔室抽空,并且翻转坩埚和将熔体倒入水冷却铜模具中的50mm厚、75至80mm宽和125mm深的通道中。在用氩填充腔室至大气压之前使熔体在真空下冷却200秒。通过线EDM从铸造状态板坯切割拉伸试样并在张力下测试。在Instron3369机械测试框架上利用Instron的Bluehill控制软件测量拉伸性质。所有测试在室温下进行,其中底部夹具固定并且顶部夹具被设定以0.012mm/s的速率向上移动。使用Instron的先进视频伸长计收集应变数据。在表9中显示拉伸测试结果。如可见的,处于铸造状态条件的本文合金显示从168至181MPa屈服应力,从494至554MPa极限强度和从8.4至18.9%延展性。表9铸造状态下所选合金的拉伸性质采用不同压下量热轧实验室铸造板坯。在热轧之前,将实验室铸造板坯装入LuciferEHS3GT-B18炉来加热。取决于合金熔点,炉设定点在1000℃至1250℃之间变化。在热轧之前使板坯均热处理40分钟以确保板坯达到目标温度。在热轧道次之间将板坯返回炉4分钟以使板坯再加热。将预加热的板坯从隧道炉推出至FennModel0612自动轧机中。道次数取决于目标轧制压下量。在热轧之后,直接从热轧轧机将所得片材(虽然其仍是热的)装入预加热至550℃的炉中以模拟商业制备的成卷(coiling)条件。一旦装入炉中,设定炉以20℃/小时的受控速率冷却。当温度小于150℃时移除样品。取决于热轧压下量设定,热轧片材具有从6mm至1.5mm范围的最终厚度。表面研磨具有小于2mm厚度的样品以确保均匀性并且使用线-EDM切割拉伸样品。对于从2mm至6mm厚的材料,首先切割然后介质喷砂张力样品以去除轧钢皮。在表10中显示拉伸测试结果。如可见的,两种合金都没有显示性质与热轧压下量的依赖关系,其具有在从41.3至68.4%范围内的延展性,从1126至1247MPa的极限强度和从272至350MPa的屈服应力。表10在热轧之后所选合金的拉伸性质具有1.6至1.8mm最终厚度的热轧片材用铝氧化物介质喷砂以去除轧钢皮并然后在FennModel0612自动轧机上冷轧。冷轧采用多道次以将片材的厚度减小至低至1mm的目标厚度。将热轧片材加入以规律性降低辊间隙的轧机中直至达到最小间隙。如果材料还没有达到规格目标,则使用处于最小间隙的额外道次直至达到目标厚度。在表11中列出本文每种合金的冷轧条件与道次数。通过线EDM从冷轧片材切割拉伸试样并在张力下测试。在表11中显示拉伸测试结果。冷轧导致显著的强化,伴随着极限拉伸强度在从1404至1712MPa范围内。冷轧状态下本文合金的拉伸延伸率在从20.4至35.4%的范围内变化。测量屈服应力在从793至1135MPa范围内。预料到可通过较大的冷轧压下量(>40%)(在我们的案例中其受实验室轧机能力限制)在本文合金中实现较高极限拉伸强度和屈服应力。表11在冷轧之后所选合金的拉伸性质通过线EDM从冷轧片材样品切割拉伸试样并在Lucifer7HT-K12箱式炉中850℃下退火10分钟。在循环结束时将样品从炉中去除并使其在空气中冷却至室温。在表12中显示拉伸测试结果。如可见的,在冷轧之后本文合金的退火过程中的再结晶导致在从1168至1269MPa范围内的极限拉伸强度与从52.5至62.6%的拉伸延伸率的性质组合。测量屈服应力在从462至522MPa范围内。具有再结晶模态组织(组织#4,图2)的这种片材状态对应于本文拉延测试所利用的最终片材状态。表12在热处理之后所选合金的拉伸数据这个案例实施例展示了模拟商业规模片材制备的加工步骤和在对于本文拉延测试所利用的具有再结晶模态组织(组织#4,图1B)的冷扎和退火片材最终条件的每个步骤加工下对应的合金性质范围。案例实施例#2:退火片材中再结晶模态组织根据表1中原子比从合金1和合金6铸造具有50mm厚度的实验室板坯,如本申请的主体部分中所述,其随后通过热轧、冷轧和在850℃退火10分钟进行实验室加工。通过SEM和TEM检查了合金显微组织,合金处于在退火之后具有1.2mm厚度的加工片材形式(对应于商业制备的退火卷材中片材的条件)。为了制备TEM试样,首先用EDM切割样品,并且然后通过每次用减小的粒度尺寸的垫研磨来减薄。通过分别用9μm、3μm和1μm金刚石悬浮溶液抛光来完成制作具有60至70μm厚度箔材的进一步减薄。从箔材冲出直径3mm的盘状物,并且采用使用双喷抛光仪的电抛光执行最终抛光。所使用的化学溶液是混合在甲醇基底中的30%硝酸。在用于TEM观察的不充分薄的区域的情况下,可使用Gatan精确离子抛光系统(PIPS)离子研磨TEM试样。离子研磨经常在4.5keV下完成,并且倾斜角从4°减小至2°以打开薄区域。使用在200kV下操作的JEOL2100高分辨显微镜完成TEM研究。通过SEM研究TEM试样。通过SEM使用由CarlZeissSMTInc.制造的EVO-MA10扫描电子显微镜检查显微组织。在图8中显示来自合金1的退火片材中的再结晶模态组织。如可见的,在组织中存在具有尖锐和笔直边界的等轴晶粒并且晶粒不含位错,其对于再结晶模态组织是典型的。有时在晶粒中发现退火孪晶,但是堆垛层错是常见的。在TEM图像中所示堆垛层错的形成对于面心立方晶体结构的奥氏体相是典型的。图9显示从TEM试样获取的合金1中再结晶模态组织的背散射SEM图像。在合金1的情况下,再结晶晶粒的尺寸在从2μm至20μm范围。在SEM图像上看到的晶粒的不同对比度(暗或明)表明晶粒的晶体取向是随机的,因为在这种情况下对比度主要来源于晶粒取向。与合金1相似,在退火之后的合金6片材中形成再结晶模态组织。图10显示在冷轧和在850℃下退火10分钟之后合金6中显微组织的明场TEM图像。如在合金1中那样,等轴晶粒具有尖锐和笔直的边界,并且在晶粒中存在堆垛层错。表明组织是充分再结晶的。来自TEM试样的SEM图像也显示再结晶模态组织。如图11中所示,再结晶晶粒是等轴的,并且显示随机取向。晶粒尺寸在从2至20μm范围,与合金1中晶粒尺寸相似。这个案例实施例展示了在退火之后具有1.2mm厚度的加工片材(其还对应于在例如商业制备的退火卷材中片材的条件)中本文的钢合金形成再结晶模态组织。案例实施例#3:转变成细化的高强度纳米模态组织在准静态变形(在这个案例中为拉伸变形)中再结晶模态组织转变成混合显微组分组织。进行了TEM分析以显示合金1和合金6片材样品中在拉伸变形之后混合显微组分组织的形成。为了制备TEM试样,通过EDM从拉伸规格首先切割样品,并且然后通过每次用减小的粒度尺寸的垫研磨来减薄。通过用9μm、3μm和低至1μm金刚石悬浮溶液抛光来完成制作具有60至70μm厚度箔材的进一步减薄。从箔材冲出直径3mm的盘状物,并且采用使用双喷抛光仪的电抛光执行最终抛光。所使用的化学溶液是混合在甲醇基底中的30%硝酸。在用于TEM观察的不充分薄的区域的情况下,可使用Gatan精确离子抛光系统(PIPS)离子研磨TEM试样。离子研磨经常在4.5keV下完成,并且倾斜角从4°减小至2°以打开薄区域。使用在200kV下操作的JEOL2100高分辨显微镜完成TEM研究。如在案例实施例#2中所述,在来自本文合金的加工片材中形成的再结晶模态组织(主要由具有等轴晶粒(具有随机取向和尖锐边界)的奥氏体相组成)。在拉伸变形时,显微组织随着在显微组织随机分布区域中从奥氏体至具有纳米析出物的铁素体的相转变而剧烈改变。图12显示在拉伸变形之后合金1样品规格中显微组织的明场TEM图像。与在退火之后再结晶模态组织中初始基本上不含位错的基体晶粒对比,拉伸应力的施加在基体奥氏体晶粒内(例如在图12a下面部分中的区域)产生高密度位错。图12a和图12b中上面部分显示由于经过纳米相细化与强化机制而组织转变成细化的高强度纳米模态组织因而具有显著细化显微组织的组织区域。在图12b中较高放大倍数TEM图像显示100至300nm的细化晶粒与在一些晶粒中的细析出物。相似地,在拉伸变形之后在合金6片材中也形成了细化的高强度纳米模态组织。图13显示在测试之后处于拉伸规格的合金6片材显微组织的明场TEM图像。如在合金1中的那样,在未转变的基体晶粒中产生高密度位错,并且由于在变形过程中的相转变而在随机分布的组织区域中获得大量细化。使用FischerFeritscope(ModelFMP30)测量变形前后的片材样品来核实相转变。注意Feritscope测量在所测试样品中所有磁相的感应并因此测量结果可包括一种或多种磁相。如图14中所示,来自合金1和合金6两者的具有再结晶模态组织的处于退火状态的片材样品含有仅1至2%的磁相,表明显微组织主要是奥氏体和非磁性的。在变形之后,以所测试样品的拉伸规格,在两种合金中磁相的量提高至大于50%。在拉伸样品规格中磁相体积提高主要地对应于由TEM所示的组织区域中奥氏体转变成铁素体并导致混合显微组分组织的形成。这个案例实施例展示在冷变形过程中来自本文合金的加工片材中再结晶模态组织转变成混合显微组分组织,伴随在代表一种显微组分的未转变奥氏体晶粒中的高位错密度和具有代表另一种显微组分的已转变细化的高强度纳米模态组织的随机分布区域。转变区域的尺寸和体积分数取决于合金化学组成和变形条件。案例实施例#4在杯式拉延之后的延迟断裂根据表1中提供的原子比从合金1、合金6和合金9铸造具有50mm厚度的实验室板坯,并且如本申请的主体部分中所述通过热轧和冷轧进行实验室加工。通过线EDM从冷轧片材切割具有表13中所列直径的坯件。在切割之后,使用240粒度碳化硅抛光纸轻微研磨坯件边缘以去除任何大的粗糙部位并且然后使用尼龙带抛光。然后如本文所述将坯件在850℃下退火10分钟。具有1.0mm最终厚度和再结晶模态组织的来自每种合金的所得坯件被用于拉延测试。通过将坯件向上推入模具中发生拉延,并且继续向上方移动顶杆(ram)至模具中直至拉延了完全杯(即没有凸缘材料)。以代表准静态速度(即非常慢\接近静态)的0.8mm/s的顶杆速度拉延杯。表13起始坯件尺寸和所得完全杯拉延比在拉延之后,检查杯并使其放置在室内空气中45分钟。空气暴露之后检查杯并且记录延迟裂纹数(如果有的话)。将拉延杯额外暴露于100%氢45分钟。选择暴露于100%氢45分钟来模拟对于拉延件寿命而言的最大氢暴露。将拉延杯放置在气氛控制外壳中并且在转换为100%氢气之前用氮冲洗。在氢中45分钟之后,在氮中吹扫腔室10分钟。将拉延杯从该外壳去除并且记录已经发生的延迟裂纹数。在图15中显示以0.8mm/s采用1.78拉延比拉延和暴露于氢45分钟之后来自合金1的杯的实例图片。在表14中显示在空气和氢暴露之后的裂纹数。注意合金1和合金6在空气和氢暴露之后有氢辅助延迟开裂,而来自合金9的杯在空气暴露之后没有开裂。表14在空气和氢暴露之后杯中的裂纹数这个案例实施例展示氢辅助延迟开裂发生在以0.8mm/s慢速在所用拉延比下杯式拉延之后的本文合金中。裂纹数取决于合金化学组成。案例实施例#5:分析在拉延之后暴露于氢的杯根据表1中提供的原子比从合金1、合金6和合金14实验室铸造具有50mm厚度的板坯,并且如本文所述通过热轧和冷轧进行实验室加工。通过线EDM从冷轧片材切割具有85.85mm直径的坯件。在切割之后,使用240粒度碳化硅抛光纸轻微研磨坯件边缘以去除任何大的粗糙部位并且然后使用尼龙带抛光。然后如本申请的主体部分中所述将坯件在850℃下退火10分钟。具有1.0mm最终厚度和再结晶模态组织(组织#4,图2)的来自每种合金的所得片材被用于杯式拉延。通过将坯件向上推入模具中发生拉延,并且继续向上方移动顶杆至模具中直至拉延了完全杯(即没有凸缘材料)。在典型的用于此类测试的0.8mm/s的顶杆速度下拉延杯。对于所测试的坯件而言所得拉延比为1.78。将拉延杯暴露于100%氢45分钟。选择暴露于100%氢45分钟来模拟对于拉延件寿命而言的最大氢暴露。将拉延杯放置在气氛控制外壳中并且在转换为100%氢气之前用氮冲洗。在氢中45分钟之后,用氮吹扫腔室10分钟。将拉延杯从该外壳去除并迅速密封在塑料袋中。将每个现在含有拉延杯的塑料袋快速放置在用干冰包装的隔热箱内。将拉延杯从在干冰中密封的塑料袋去除,仅为了从杯底部和杯壁两者采集样品用于氢分析。将杯和分析样品两者再一次密封在塑料袋中并保持在干冰温度下。将氢分析样品保持在干冰温度下直至刚好在测试之前,此时将每种样品从干冰和塑料袋去除并通过惰性气体熔融(IGF)分析氢含量。在表15中提供每种合金杯底部和杯壁中的氢含量。对于这种IGF而言氢的检测极限为0.0003重量%氢。表15在氢暴露之后杯底部和杯壁中的氢含量注意到在杯式拉延工艺过程中经历最小变形的杯底部在暴露于100%氢45分钟之后具有最小氢含量。然而,在杯式拉延工艺过程中确实具有大量变形的杯壁在暴露于100%氢45分钟之后具有非常高的氢含量。这个案例实施例展示仅当实现特定的应力状态时氢进入材料。另外,此关键要素是氢吸收仅发生在拉延杯的大量变形的区域中。案例实施例#6:氢暴露杯的断口形貌分析如在案例实施例#4中展示的以0.8mm/s拉延速度杯式拉延之后本文纳米钢合金经历延迟开裂。通过以二次电子检测模式的扫描电子显微术(SEM)分析了来自合金1、合金6和合金9的杯中裂纹的断裂表面。图16至图18分别显示合金1、合金6和合金9的断裂表面。在所有图像中,观察到在断裂表面上缺少清晰的晶界,然而发现了大而平的穿晶刻面,表明在氢辅助延迟开裂过程中经过合金内穿晶解理而发生断裂。这个案例实施例展示氢侵蚀处于复杂三轴应力状态的杯中的已转变区域。已转变区域(即铁素体)的特定面被氢侵蚀,导致穿晶解理失效。案例实施例#7:在低速下杯式拉延过程中的组织转变作为冷塑性变形形式,杯式拉延引起本文钢合金中的显微组织改变。在这个案例实施例中,当以常在工业中用于杯式拉延测试的0.8mm/s的相对慢的拉延速度拉延合金1和合金6的杯时,在合金1和合金6的杯中展示组织转变。处于退火状态的具有再结晶模态组织和1mm厚度的来自合金1和合金6的钢片材被用于采用1.78拉延比的杯式拉延。使用SEM和TEM分析来研究来自合金1和合金6的拉延杯中的组织转变。为了对比,如图19所示研究了杯壁和杯底部。为了制备TEM试样,用EDM切割杯壁和杯底部,并且然后通过每次用减小的粒度尺寸的垫研磨来减薄。通过用9μm、3μm和低至1μm金刚石悬浮溶液抛光来完成制作具有60至70μm厚度箔材的进一步减薄。从箔材冲出直径3mm的盘状物,并且采用使用双喷抛光仪的电抛光执行最终抛光。所使用的化学溶液是混合在甲醇基底中的30%硝酸。在用于TEM观察的不充分薄的区域的情况下,可使用Gatan精确离子抛光系统(PIPS)离子研磨TEM试样。离子研磨经常在4.5keV下完成,并且倾斜角从4°减小至2°以打开薄区域。使用在200kV下操作的JEOL2100高分辨显微镜完成TEM研究。在合金1中,与退火片材中初始再结晶模态组织对比,杯的底部没有显示剧烈的组织改变。如图20中所示,通过TEM揭示了具有笔直边界的晶粒,并且堆垛层错是奥氏体相的可见、典型的特征。即杯底部维持再结晶模态组织。然而,杯壁中的显微组织显示在拉延工艺过程中显著的转变。如图21中所示,样品含有高密度位错,并且笔直的晶界不再如在再结晶组织中那样可见。在变形过程中剧烈的显微组织改变主要与奥氏体相(γ-Fe)转变成铁素体(α-Fe)有关,伴随着纳米析出物实现与在准静态拉伸测试之后混合显微组分组织非常相似的但是具有显著更高的已转变的细化高强度纳米模态组织体积分数的显微组织。相似地在合金6中,如图22中所示,杯底部经历很少塑性变形并且存在再结晶模态组织。来自合金6的杯的壁严重变形,其显示在晶粒中的高密度位错,如图23中所示。通常,可将该变形组织分类为混合显微组分组织。但是与合金1相比,奥氏体看起来在合金6中更稳定,导致在拉延之后细化的高强度纳米模态组织的更小的分数。虽然在两种合金中都有大量位错,但是合金6中由相转变引起的细化与合金1对比看起来不那么突出。显微组织改变符合来自杯壁和杯底部的Feritscope测量结果。如图24中所示,杯底部含有少量的磁相(1至2%),其表明具有奥氏体基体的再结晶模态组织是主要的。在杯壁中,合金1和合金6的杯中磁相(主要是铁素体)分别上升直至50%和38%。磁相的提高对应于相转变和细化的高强度纳米模态组织的形成。合金6中较少的转变暗示较稳定的奥氏体,其与TEM观察结果一致。这个案例实施例展示在以0.8mm/s慢速下杯式拉延过程中杯壁中发生显著的相转变成细化的高强度纳米模态组织。已转变相的体积分数取决于合金化学组成。案例实施例#8在杯式拉延之后拉延比对延迟断裂的影响根据表1中提供的原子比从合金1、合金6、合金9、合金14和合金42铸造具有50mm厚度的实验室板坯。如本申请的主体部分中所述通过热轧和冷轧来实验室加工铸造板坯。通过线EDM从冷轧片材切割具有表12中所列直径的坯件。在切割之后,使用240粒度碳化硅抛光纸轻微研磨坯件边缘以去除任何大的粗糙部位并且然后使用尼龙带抛光。然后如本文所述将坯件在850℃下退火10分钟。具有1.0mm最终厚度和再结晶模态组织的来自每种合金的所得片材坯件被用于在表16中规定的拉延比下的杯式拉延。表16起始坯件尺寸和所得完全杯拉延比具有1.0mm最终厚度和再结晶模态组织的来自各种合金的所得坯件被用于拉延测试。通过将坯件向上推入模具中发生拉延,并且继续向上方移动顶杆至模具中直至拉延了完全杯(即没有凸缘材料)。在典型的用于此类测试的0.8mm/s的顶杆速度下拉延杯。采用相同拉延参数拉延具有不同尺寸的坯件。在拉延之后,检查杯并使其放置在室内空气中45分钟。空气暴露之后检查杯并且记录延迟裂纹数(如果有的话)。将拉延杯额外暴露于100%氢45分钟。选择暴露于100%氢45分钟来模拟对于拉延件寿命而言的最大氢暴露。将拉延杯放置在气氛控制外壳中并且在转换为100%氢气之前用氮冲洗。在氢中45分钟之后,在氮中吹扫腔室10分钟。将拉延杯从该外壳去除并且记录已经发生的延迟裂纹数。分别在表17和表18中显示拉延杯暴露于空气和氢过程中发生的裂纹数。表17在空气暴露之后拉延杯中的裂纹数表18在氢暴露之后拉延杯中的裂纹数如可见的,对于合金1而言,在暴露于空气和氢两者之后在杯中在1.78拉延比下观察到可观的开裂,然而在1.4拉延比及以下该数迅速降低至零。Feritscope测量显示合金的显微组织在杯壁中经历显著的转变,其随着拉延比升高而提高。在图25中呈现合金1的结果。合金6、合金9和合金42显示在1.6或以下拉延比测量没有延迟开裂的相似行为,其展示由于合金化学组成改变而对延迟开裂较高的抵抗力。Feritscope测量还显示合金的显微组织在杯壁中经历转变,随着拉延比升高而提高,但是与合金1相比处于较小程度。在图26、图27和图28中还分别呈现合金6、合金9和合金42的结果。合金14展示在本文所有测试条件下没有延迟开裂。在图29中还呈现采用Feritscope测量的合金14的结果。如可见的,当转变相的量小于临界值(其取决于合金化学组成)时在杯中没有发生延迟开裂。例如,对于合金6临界值为约30Fe%(图25)而对于合金9其为约23Fe%(图27)。总转变量还取决于合金化学组成。在1.78的相同拉延比下,对于合金1转变的磁相体积分数测量为几乎50Fe%(图25)而在合金14中其仅为约10Fe%(图29)。明显地,在来自合金14的杯壁中没有达到转变临界值,并且在氢暴露之后没有观察到延迟开裂。这个案例实施例展示对于本文合金,存在延迟开裂与拉延比的清晰的依赖关系。对应于延迟开裂阀值的拉延比值(大于该值发生开裂)取决于合金化学组成。案例实施例#9在杯式拉延之后拉延速度对延迟断裂的影响根据表1中提供的原子比从合金1和合金6铸造具有50mm厚度的实验室板坯,并且如本申请的主体部分中所述通过热轧和冷轧进行实验室加工。通过线EDM从冷轧片材切割具有85.85mm直径的坯件。在切割之后,使用240粒度碳化硅抛光纸轻微研磨坯件边缘以去除任何大的粗糙部位并且然后使用尼龙带抛光。然后如本文所述将坯件在850℃下退火10分钟。具有1.0mm最终厚度和再结晶模态组织的来自每种合金的所得片材坯件被用于在表19中规定的8种不同速度下的杯式拉延。通过将坯件向上推入模具中发生拉延,并且继续向上方移动顶杆至模具中直至拉延了完全杯(即没有凸缘材料)。在如表19中指出的各种拉延速度下拉延杯。对于所测试的坯件所得拉延比为1.78。表19所使用的拉延速度#拉延速度(mm/s)10.822.53549519.56387768203在拉延之后,检查杯并使其放置在室内空气中45分钟。空气暴露之后检查杯并且记录延迟裂纹数(如果有的话)。将拉延杯额外暴露于100%氢45分钟。选择暴露于100%氢45分钟来模拟对于拉延件寿命而言的最大氢暴露。将拉延杯放置在气氛控制外壳中并且在转换为100%氢气之前用氮冲洗。在氢中45分钟之后,在氮中吹扫腔室10分钟。将拉延杯从该外壳去除并且记录已经发生的延迟裂纹数。分别在表20和表21中显示来自合金1和合金6的拉延杯在空气和氢暴露过程中发生的裂纹数。在图30中显示在不同拉延速度下采用1.78拉延比拉延并暴露于氢45分钟的来自合金1的杯的实例。表20在45分钟暴露之后合金1的延迟开裂响应表21在45分钟暴露之后合金6的延迟开裂响应如可见的,随着提高拉延速度,在来自合金1和合金6两者的拉延杯中裂纹数降低并且在氢暴露和空气暴露两者之后变为零。还分别在图31和图32中呈现合金1和合金6的结果。对于所有测试的合金,在暴露于100%氢气氛45分钟之后在19mm/s或更大的拉延速度下没有观察到延迟开裂。这个案例实施例展示对于本文合金而言,存在延迟开裂与拉延速度的清晰的依赖关系并且在高于临界阀值(SCR)拉延速度(其取决于合金化学组成)的拉延速度下没有观察到开裂。案例实施例#10在高速下杯式拉延过程中的组织转变显示了拉延速度影响组织转变以及拉延杯在氢辅助延迟开裂方面的性能。在这个案例实施例中,对在高速下拉延来自合金1和合金6的杯进行了组织分析。如本申请的主体部分中所述,通过热轧、冷轧和在850℃下退火10分钟来加工来自两种合金的板坯。具有1.0mm最终厚度和再结晶模态组织的所得片材被用于在如案例实施例#8中所述的不同速度下的杯式拉延。通过TEM分析了在203mm/s下拉延的杯壁和杯底部中的显微组织。为了对比,如图19中所示研究了杯壁和杯底部。为了制备TEM试样,首先用EDM切割样品,并且然后通过每次用减小的粒度尺寸的垫研磨来减薄。通过用9μm、3μm和低至1μm金刚石悬浮溶液抛光来完成制作具有60至70μm厚度箔材的进一步减薄。从箔材冲出直径3mm的盘状物,并且采用使用双喷抛光仪的电抛光执行最终抛光。所使用的化学溶液是混合在甲醇基底中的30%硝酸。在用于TEM观察的不充分薄的区域的情况下,可使用Gatan精确离子抛光系统(PIPS)离子研磨TEM试样。离子研磨经常在4.5keV下完成,并且倾斜角从4°减小至2°以打开薄区域。使用在200kV下操作的JEOL2100高分辨显微镜完成TEM研究。在203mm/s的快速拉延速度下,杯底部显示与再结晶模态组织相似的显微组织。如图33中所示,晶粒洁净仅具有很少的位错,并且晶界笔直和尖锐,其对于再结晶组织是典型的。在晶粒中还看到堆垛层错,表示奥氏体相(γ-Fe)。因为经过在850℃下退火10分钟在杯式拉延之前片材再结晶,图33中所示显微组织表明杯底部在杯式拉延过程中经历非常有限的塑性变形。在慢速(0.8mm/s)下,来自合金1的杯底部的显微组织(图20)显示大体上与在快速下的组织相似的组织即笔直的晶界和并不出乎预料的堆垛层错的存在,因为在杯底部发生最小变形。相比之下,与如在慢速下拉延的杯中所见的底部相比,在快速下拉延的杯壁高度变形。然而在不同速度下拉延的杯中揭示了不同的变形路径。如图34中所示,快速拉延杯的壁显示除奥氏体基体晶粒内位错以外高分数的变形孪晶。在0.8mm/s的慢速下拉延的情况下(图21),杯壁中显微组织没有显示出变形孪晶的证据。组织外观典型的是混合显微组分组织(组织#2,图2和图3)的组织外观。虽然在两种情况下相转变来自高密度位错的积累,并且在随机分布的组织区域内产生细化的组织,但是由于通过孪晶的有效变形导致较少程度的相转变,在这种快速拉延情况下位错的活性较不明显。图35和图36显示来自合金6在203mm/s的快速下拉延的杯底部中和杯壁中的显微组织。与合金1相似,在杯底部中存在再结晶模态组织并且孪晶支配杯壁的变形。在慢拉延(以0.8mm/s的速度)之后的杯中,在来自合金6的杯壁中没有发现孪晶而是发现了位错(图23)。图37显示对来自合金1和合金6的杯的Feritscope测量。可看到在慢拉延杯和快拉延杯两者的底部中显微组织主要是奥氏体。因为在杯式拉延过程中在杯底部处出现非常少的应力至没有应力,所以组织改变最小并且然后由起始再结晶模态组织(即图2中组织#4)的基线测量(Fe%)代表。杯底部处的Feritscope测量由图37中空心符号代表,显示在本文两种合金中以任何拉延速度磁相体积分数没有改变。然而,与此相反,两种合金的杯壁显示与变形时相转变有关的磁相的量随着拉延速度提高而降低(图37中实心符号),这与TEM研究一致。杯壁在拉延时经历大量变形,导致朝向混合显微组分组织形成的组织改变。如可见的,代表显微组分2的磁相的体积分数随着拉延速度提高而降低(图37)。注意到根据直接观察到开裂时为每种合金提供临界速度(SCR)。如分别在图31和图32中存在的裂纹数所示,对于合金1而言SCR被确定为19mm/s并且对于合金6而言SCR被确定为9.5mm/s。这个案例实施例展示在本文合金的杯式拉延过程中提高拉延速度导致变形路径的改变,其受变形孪晶支配,导致抑制奥氏体转变为细化的高强度纳米模态组织并降低磁相体积百分数。案例实施例#11在不同速度下常规AHSS杯式拉延购买具有1mm厚度的商业制备和加工的双相980(DP980)钢片材并且以接收状态条件用于杯式拉延测试。通过线EDM从冷轧片材切割具有85.85mm直径的坯件。在切割之后,使用240粒度碳化硅抛光纸轻微研磨坯件边缘以去除任何大的粗糙部位并且然后使用尼龙带抛光。所得片材坯件被用于在表17中规定的3种不同速度下的杯式拉延。具有1.0mm最终厚度和再结晶模态组织的来自每种合金的所得坯件被用于拉延测试。通过将坯件向上推入模具中发生拉延,并且继续向上方移动顶杆至模具中直至拉延了完全杯(即没有凸缘材料)。在如表22中所指出的各种拉延速度下拉延杯。所测试的坯件的所得拉延比为1.78。表22所用的拉延速度#拉延速度(mm/s)10.82763203在拉延之后,在杯壁和底部上完成Feritscope测量。在图38中显示测量结果。如可见的,磁相体积分数没有随着拉延速度提高而改变并且在整个所施加速度范围内保持恒定。这个案例实施例展示在常规AHSS杯式拉延时提高拉延速度不影响组织相组成或改变变形路径。案例实施例#12拉延极限比根据表1中提供的原子比,通过线EDM从来自两种合金(合金6和合金14)的1.0mm厚冷轧片材切割具有表23中所列直径的来自合金6和合金14的坯件。在切割之后,使用240粒度碳化硅抛光纸轻微研磨坯件边缘以去除任何大的粗糙部位并且然后使用尼龙带抛光。然后如本文所述将坯件在850℃下退火10分钟。具有1.0mm最终厚度和再结晶模态组织的来自每种合金的所得片材坯件被用于在表23中规定的拉延比下的杯式拉延。在初始状态,Feritscope测量显示Fe%对于合金6而言为0.94并且对于合金14而言为0.67。表23起始坯件尺寸和所得的完全杯拉延比在InterlakenSP225机器上使用小直径冲模(31.99mm)与36.31mm的模具直径完成测试。通过将坯件向上推入模具中发生拉延,并且继续向上方移动顶杆至模具中直至拉延了完全杯(即没有凸缘材料)。在典型的用于此类测试的0.85mm/s和在25mm/s的顶杆速度下拉延杯。采用相同的拉延参数拉延具有不同尺寸的坯件。分别在图39和图40中显示采用不同拉延比拉延的来自合金6和合金14的杯的实例。注意到未优化拉延参数所以在杯样品中观察到在顶部的一些凸耳(earing)和在侧壁上的凹坑。这发生在例如当夹持力或润滑剂未优化使得存在一些拉延缺陷时。在拉延之后,检查杯的延迟开裂和/或破裂。在图41中显示包括在拉延之后对杯壁Feritscope测量的测试结果。如可见的,在0.85mm/s慢拉延速度下在来自合金6的杯壁中磁相的量从在1.9拉延比下的34Fe%持续提高至在2.4拉延比下的46%。延迟断裂发生在所有拉延比下,其中在2.4的拉延比下杯破裂。拉延速度提高至25mm/s导致在所有拉延比下较低的Fe%,其中在2.4拉延比下具有21.5Fe%的最大值。杯破裂发生在相同的2.4拉延比下。在来自合金14的杯壁中,磁相的量在本文所有测试条件下相对较低。在来自这种合金的任何杯中没有观察到延迟开裂,并且在较高速度测试(25mm/s)情况下,破裂发生在2.5的较高拉延比下。对于合金6而言限制性拉延比(LDR)被确定为2.3并且对于合金14而言被确定为2.4。LDR被定义为在给定冲模直径下可成功拉延的坯件最大直径的比率。这个案例实施例展示在本文合金杯式拉延过程中提高拉延速度导致延迟断裂的抑制(如合金6实例上所示)和在限定了拉延极限比(DLR)的破裂之前提高拉延比(如合金14实例上所示)。拉延速度的提高导致减少的相转变为细化的高强度纳米模态组织,显著降低在对氢脆敏感的变形之后磁相的量。当前第1页1 2 3