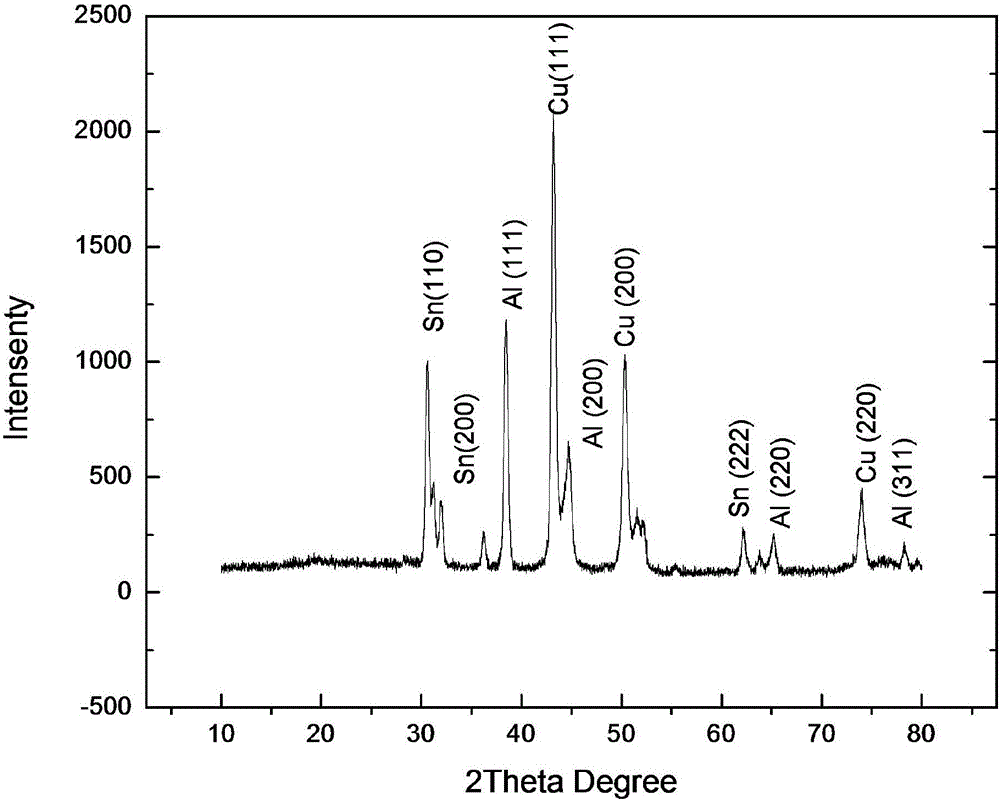
本发明涉及滑动轴承技术领域,更具体的涉及一种双技术协同制备轴瓦减摩镀层的方法。
背景技术:
对于高速、重载、高精度、结构上需要剖分的场合,如汽轮机、离心式压缩机、柴油机、大型电机等,需采用滑动轴承,轴瓦是滑动轴承中的重要零件,是最重要的承力部件之一,也是发动机中最易失效的部件。
滑动轴承的主要作用有:1、支持轴及轴上零件,保持轴的旋转精度;2、减少转轴与支承之间的摩擦磨损。轴承中起支承轴颈作用的零件是轴瓦,因此,轴瓦的性能好坏直接影响着发动机的性能。随着汽车工业的发展,人们对发动机的功率和转速指标要求越来越高,因而对轴瓦、衬套等耐磨零件的服役条件进一步恶化,性能要求也越来越苛刻。发动机工作时,轴瓦需承受高达700MPa的负荷,远高于合金衬层和钢背的屈服极限(100-300MPa),易导致轴瓦弹张量消失,并最终导致轴瓦抱轴;在交变应力作用下,轴瓦会出现涂层、合金衬层开裂和剥落,因而也易导致轴瓦咬合失效。特别是在发动机突然启动或瞬时加速时,润滑油膜不能及时形成,曲轴和轴瓦之间处于干摩擦状态,轴瓦和曲轴极易损坏。国外不断从改善润滑条件、优化结构、提高材料性能等方面努力,以提高轴瓦的使用寿命。
传统的轴瓦其结构形式上一般由依次设置的钢背层、轴承合金层、镍栅层以及减摩层组成,其中基底层在钢背层上,镍栅层镀在基底层上,减摩层镀在镍栅层上。减摩层一般采用铅锡铜三元合金。这种轴瓦能在一定程度上满足发动机的基本要求,但是应用在强化的柴油机上,由于减摩层的抗疲劳强度低,不能满足汽车柴油机的发展需要,轴瓦的抗疲劳强度、耐腐蚀性及耐磨性都有待提高。同时,由于轴瓦中含有铅等有害金属元素,轴瓦对环境产生一定的破坏,不具有环保型性能,不符合社会的发展需要。传统的轴瓦减摩层一般是通过电镀的方法沉积而成的。这种电镀在生产的过程中,对环境及操作人员非常有害,而且电镀出来的轴瓦其性能要求有一定的局限性。
技术实现要素:
本发明提供一种双技术协同制备轴瓦减摩镀层的方法,利用电弧离子镀和磁控溅射离子镀技术协同制备轴瓦减摩镀层,实现了大厚度轴瓦镀层的高速沉积,其轴瓦镀层具有致密性好、抗疲劳强度高、耐磨性优良和环保的特点。
具体的,本发明中双技术协同制备轴瓦减摩镀层的方法,包括以下步骤:
步骤1:将轴瓦基体安装到磁控溅射设备内,并在轴瓦基体和靶材之间建立水平正交电磁场;
步骤2:将磁控溅射设备内部进行抽真空,使真空度达到10-3Pa以下的设定值;
步骤3:当磁控溅射设备内部真空度达到设定值后,向水平正交电磁场中通入惰性气体,并转动轴瓦基体进行辉光清洗;
步骤4:辉光清洗后进行弧光清洗,弧光清洗时采用镍靶;
步骤5:对轴瓦基体的内圆面使用电弧离子镀制备镍栅层,制备镍栅层时使用镍靶,利用水平正交电磁场对镍靶进行轰击,镍靶离子被击出后沉积到轴瓦基体的内圆面,形成一层镍栅层;
步骤6:对形成镍栅层的轴瓦基体,同时使用电弧离子镀和磁控溅射离子镀进行处理,在镍栅层上进行复合镀膜,形成轴瓦减摩镀层,其中,电弧离子镀采用的靶材为铝铜合金靶,磁控溅射离子镀采用的靶材为锡靶和碳靶;
步骤7:将形成轴瓦减摩镀层的轴瓦基体随炉冷却至温度低于180℃后,打开磁控溅射设备并取出带有轴瓦减摩镀层的轴瓦基体。
优选的,步骤1中,水平正交电磁场中电场由直流电源提供电能,脉冲偏压电源范围为0-1500V,所述轴瓦基体为铝基轴承合金。
优选的,步骤3中,辉光清洗时,工作压力为3.50Pa,惰性气体流量为170sccm,轴瓦基体脉冲偏压为800V,占空比为20%,清洗时间为5min。
优选的,步骤4中,弧光清洗时,工作压力为2.00Pa,惰性气体流量为100sccm,轴瓦基体脉冲偏压为900V,镍靶电流为50A,清洗时间为4min。
优选的,所述镍靶纯度为99.9%。
优选的,步骤5中,工作压力为2.00Pa,惰性气体流量为100sccm,轴瓦基体偏压为900V,占空比为10%,镍靶电流为50-90A,电弧离子镀镍栅层沉积时间为10min。
优选的,步骤6中,采用纯度为99.9%的铝铜合金靶进行电弧离子镀,铝铜合金靶电流为45-90A,采用纯度均为99.9%的锡靶和碳靶进行磁控溅射离子镀,锡靶电流为0.15-1.0A,碳靶电流为0.8-3.0A,轴瓦基体偏压为300-500V,占空比为50-80%,镀膜时间为30-60min,每隔5min记录一次数据。
优选的,所述惰性气体选用纯度为99.99%以上的氩气或氦气。
优选的,形成的轴瓦减摩镀层各含量成分的质量分数为:11.5-19.5%Sn,3.0-8.0%C,0.75-1.25%Cu,不可避免的杂质元素<5%,其余为Al。
优选的,形成的轴瓦减摩镀层厚度为5-30μm。
本发明的有益效果为:
(1)生产的轴瓦镀层的致密性好,其致密度大大高于传统的电镀减摩层;抗疲劳强度很高,其抗疲劳强度在110-140MPa,大大优于传统镀层;轴瓦的耐磨性优良,是铅锡铜合金的两倍以上;硬度较高,是水镀生产镀层硬度的2-3倍。
(2)利用电弧离子镀和磁控溅射离子镀技术协同制备轴瓦减摩镀层,实现了大厚度轴瓦镀层的高速沉积。
(3)镀层本身不含铅等有毒元素,因而轴瓦具有很好的环保性能;镀层的沉积过程也是环保的,沉积过程不是在水中进行,而是在高真空环境下进行,整个过程只需加入媒介气体氩气或氦气,不会对环境造成破坏;对人的身体健康也是环保的,整个过程均可采用自动智能化控制。
(4)本发明中双技术协同制备轴瓦减摩镀层的方法,几乎对所有的材料都可以通过真空PVD的方法获得一层薄膜,突破了电镀的局限性。
(5)水平正交电磁场内加入惰性气体,惰性气体的加入,增加了正交电磁场中的各离子、电子碰撞的时间和机率,有利于气相沉积顺利进行和镀膜的效果。
附图说明
为了更清楚地说明本发明实施例或现有技术中的技术方案,下面将对实施例或现有技术描述中所需要使用的附图作简单地介绍,显而易见地,下面描述中的附图仅仅是本发明的一些实施例,对于本领域普通技术人员来讲,在不付出创造性劳动的前提下,还可以根据这些附图获得其他的附图。
图1为本发明实施例1提供的轴瓦减摩镀层的膜基临界载荷图;
图2为本发明实施例1提供的轴瓦减摩镀层的XRD图谱;
图3为本发明实施例1提供的轴瓦减摩镀层的洛氏压痕图。
具体实施方式
下面将结合本发明实施例中的附图,对本发明实施例中的技术方案进行清楚、完整地描述,显然,所描述的实施例仅仅是本发明一部分实施例,而不是全部的实施例。基于本发明中的实施例,本领域普通技术人员在没有做出创造性劳动前提下所获得的所有其他实施例,都属于本发明保护的范围。
实施例1
本发明实施例1提供的双技术协同制备轴瓦减摩镀层的方法,包括以下步骤:
步骤1:将轴瓦基体安装到磁控溅射设备内,并在轴瓦基体和靶材之间建立水平正交电磁场,水平正交电磁场中电场由直流电源提供电能,脉冲偏压电源范围为0-1500V,所述轴瓦基体为通过浇注或烧结到钢背上的铝基轴承合金;
步骤2:将磁控溅射设备内部进行抽真空,使真空度达到10-3Pa以下的设定值;
步骤3:当磁控溅射设备内部真空度达到设定值后,向水平正交电磁场中通入纯度为99.99%的氩气,并转动轴瓦基体进行辉光清洗,辉光清洗时,工作压力为3.50Pa,氩气流量为170sccm,轴瓦基体脉冲偏压为800V,占空比为20%,清洗时间为5min;
步骤4:辉光清洗后进行弧光清洗,弧光清洗时采用纯度为99.9%的镍靶,弧光清洗时,工作压力为2.00Pa,氩气流量为100sccm,轴瓦基体脉冲偏压为900V,镍靶电流为50A,清洗时间为4min;
步骤5:对轴瓦基体的内圆面使用电弧离子镀制备镍栅层,制备镍栅层时使用纯度为99.9%的镍靶,利用水平正交电磁场对镍靶进行轰击,镍靶离子被击出后沉积到轴瓦基体的内圆面,形成一层镍栅层,具体的,工作压力为2.00Pa,氩气流量为100sccm,轴瓦基体偏压为900V,占空比为10%,镍靶电流为50A,电弧离子镀镍栅层沉积时间为10min;
步骤6:对形成镍栅层的轴瓦基体,同时使用电弧离子镀和磁控溅射离子镀进行处理,在形成的镍栅层上进行复合镀膜,形成轴瓦减摩镀层,其中,采用纯度为99.9%的铝铜合金靶进行电弧离子镀,铝铜合金靶电流为45A,采用纯度均为99.9%的锡靶和碳靶进行磁控溅射离子镀,锡靶电流为0.15A,碳靶电流为0.8A,轴瓦基体偏压为300V,占空比为50%,镀膜时间为30min,每隔5min记录一次数据;
步骤7:将形成轴瓦减摩镀层的轴瓦基体随炉冷却至温度低于180℃后,打开磁控溅射设备并取出带有轴瓦减摩镀层的轴瓦基体,并清理磁控溅射设备腔室。
利用扫描电子显微镜测量制备的轴瓦减摩镀层厚底为5μm。
经测定,实施例1中制备的轴瓦减摩镀层各含量成分的质量分数为:11.5%Sn,3.0%C,0.75%Cu,不可避免的杂质元素<5%,其余为Al。
对实施例1中制备的轴瓦减摩镀层进行载荷试验,由图1可知轴瓦减摩镀层与轴瓦基体的膜基结合力为46N,结合性能良好;对实施例1中制备的轴瓦减摩镀层进行XRD检测,由图2可知轴瓦减摩镀层主要由铝、锡、铜和碳元素组成,其中,铝、锡和铜三种元素以晶体形态存在,碳元素以非晶体形态存在;图3为轴瓦减摩镀层的洛氏压痕图,由图3看出轴瓦减摩镀层压痕表面局部存在小面积应变影响区,同时只有少量的裂纹出现,说明轴瓦减摩镀层的韧性良好。
实施例2
本发明实施例2提供的双技术协同制备轴瓦减摩镀层的方法,包括以下步骤:
步骤1:将轴瓦基体安装到磁控溅射设备内,并在轴瓦基体和靶材之间建立水平正交电磁场,水平正交电磁场中电场由直流电源提供电能,脉冲偏压电源范围为0-1500V,所述轴瓦基体为通过浇注或烧结到钢背上的铝基轴承合金;
步骤2:将磁控溅射设备内部进行抽真空,使真空度达到10-3Pa以下的设定值;
步骤3:当磁控溅射设备内部真空度达到设定值后,向水平正交电磁场中通入纯度为99.99%的氩气,并转动轴瓦基体进行辉光清洗,辉光清洗时,工作压力为3.50Pa,氩气流量为170sccm,轴瓦基体脉冲偏压为800V,占空比为20%,清洗时间为5min;
步骤4:辉光清洗后进行弧光清洗,弧光清洗时采用纯度为99.9%的镍靶,弧光清洗时,工作压力为2.00Pa,氩气流量为100sccm,轴瓦基体脉冲偏压为900V,镍靶电流为50A,清洗时间为4min;
步骤5:对轴瓦基体的内圆面使用电弧离子镀制备镍栅层,制备镍栅层时使用纯度为99.9%的镍靶,利用水平正交电磁场对镍靶进行轰击,镍靶离子被击出后沉积到轴瓦基体的内圆面,形成一层镍栅层,具体的,工作压力为2.00Pa,氩气流量为100sccm,轴瓦基体偏压为900V,占空比为10%,镍靶电流为70A,电弧离子镀镍栅层沉积时间为10min;
步骤6:对形成镍栅层的轴瓦基体,同时使用电弧离子镀和磁控溅射离子镀进行处理,在形成的镍栅层上进行复合镀膜,形成轴瓦减摩镀层,其中,采用纯度为99.9%的铝铜合金靶进行电弧离子镀,铝铜合金靶电流为70A,采用纯度均为99.9%的锡靶和碳靶进行磁控溅射离子镀,锡靶电流为0.60A,碳靶电流为2.0A,轴瓦基体偏压为400V,占空比为65%,镀膜时间为45min,每隔5min记录一次数据;
步骤7:将形成轴瓦减摩镀层的轴瓦基体随炉冷却至温度低于180℃后,打开磁控溅射设备并取出带有轴瓦减摩镀层的轴瓦基体,并清理磁控溅射设备腔室。
利用扫描电子显微镜测量制备的轴瓦减摩镀层厚底为18μm。
经测定,实施例1中制备的轴瓦减摩镀层各含量成分的质量分数为:15.0%Sn,6.0%C,1.10%Cu,不可避免的杂质元素<5%,其余为Al。
实施例3
本发明实施例3提供的双技术协同制备轴瓦减摩镀层的方法,包括以下步骤:
步骤1:将轴瓦基体安装到磁控溅射设备内,并在轴瓦基体和靶材之间建立水平正交电磁场,水平正交电磁场中电场由直流电源提供电能,脉冲偏压电源范围为0-1500V,所述轴瓦基体为通过浇注或烧结到钢背上的铝基轴承合金;
步骤2:将磁控溅射设备内部进行抽真空,使真空度达到10-3Pa以下的设定值;
步骤3:当磁控溅射设备内部真空度达到设定值后,向水平正交电磁场中通入纯度为99.99%的氦气,并转动轴瓦基体进行辉光清洗,辉光清洗时,工作压力为3.50Pa,氦气流量为170sccm,轴瓦基体脉冲偏压为800V,占空比为20%,清洗时间为5min;
步骤4:辉光清洗后进行弧光清洗,弧光清洗时采用纯度为99.9%的镍靶,弧光清洗时,工作压力为2.00Pa,氦气流量为100sccm,轴瓦基体脉冲偏压为900V,镍靶电流为50A,清洗时间为4min;
步骤5:对轴瓦基体的内圆面使用电弧离子镀制备镍栅层,制备镍栅层时使用纯度为99.9%的镍靶,利用水平正交电磁场对镍靶进行轰击,镍靶离子被击出后沉积到轴瓦基体的内圆面,形成一层镍栅层,具体的,工作压力为2.00Pa,氦气流量为100sccm,轴瓦基体偏压为900V,占空比为10%,镍靶电流为90A,电弧离子镀镍栅层沉积时间为10min;
步骤6:对形成镍栅层的轴瓦基体,同时使用电弧离子镀和磁控溅射离子镀进行处理,在形成的镍栅层上进行复合镀膜,形成轴瓦减摩镀层,其中,采用纯度为99.9%的铝铜合金靶进行电弧离子镀,铝铜合金靶电流为90A,采用纯度均为99.9%的锡靶和碳靶进行磁控溅射离子镀,锡靶电流为1.0A,碳靶电流为3.0A,轴瓦基体偏压为500V,占空比为80%,镀膜时间为60min,每隔5min记录一次数据;
步骤7:将形成轴瓦减摩镀层的轴瓦基体随炉冷却至温度低于180℃后,打开磁控溅射设备并取出带有轴瓦减摩镀层的轴瓦基体,并清理磁控溅射设备腔室。
利用扫描电子显微镜测量制备的轴瓦减摩镀层厚底为30μm。
经测定,实施例1中制备的轴瓦减摩镀层各含量成分的质量分数为:19.5%Sn,8.0%C,1.25%Cu,不可避免的杂质元素<5%,其余为Al。
尽管已描述了本发明的优选实施例,但本领域内的技术人员一旦得知了基本创造性概念,则可对这些实施例作出另外的变更和修改。所以,所附权利要求意欲解释为包括优选实施例以及落入本发明范围的所有变更和修改。
显然,本领域的技术人员可以对本发明进行各种改动和变型而不脱离本发明的精神和范围。这样,倘若本发明的这些修改和变型属于本发明权利要求及其等同技术的范围之内,则本发明也意图包含这些改动和变型在内。