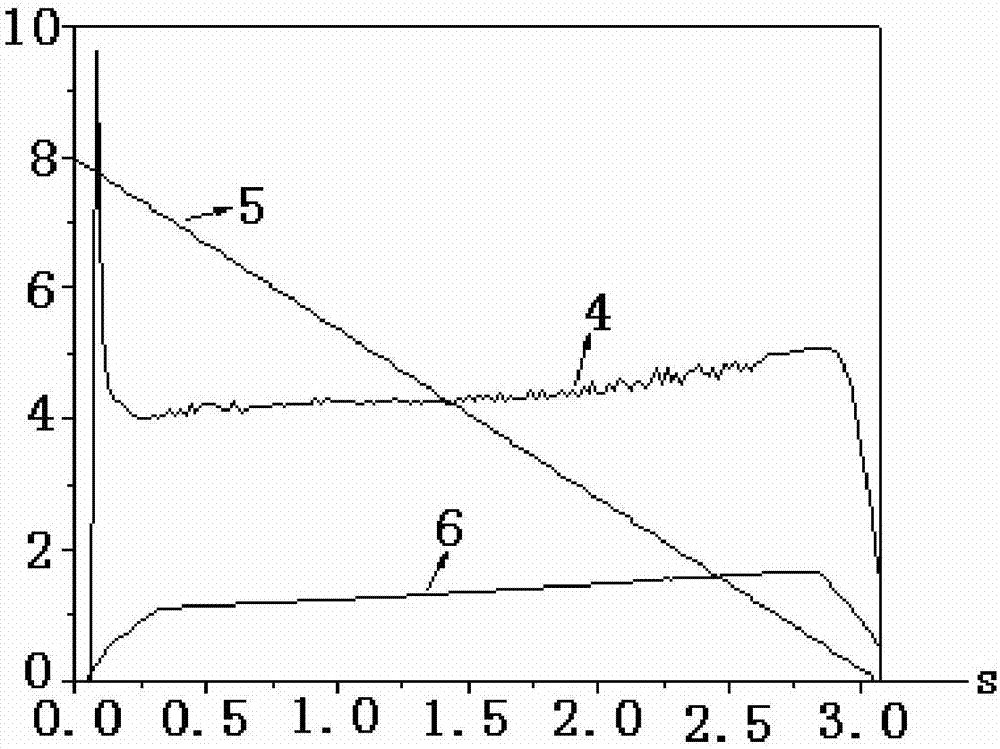
本发明涉及粉末冶金铜基刹车材料领域,具体是一种高速直线刹车用铜基粉末冶金摩擦材料及其制备方法。
背景技术:
:高速直线刹车是指机械负载较大、制动速度高的且与摩擦对偶作相对直线运动的一种制动形式,其中直线运行速度越高工况环境越复杂,对制动摩擦副材料的性能要求也就越高。与盘式制动和鼓式制动的实际应用相比,直线刹车的摩擦瞬时温度非常高,单位体积荷载更大,受高速直线运动的冲击力也很强。因此对摩擦材料的导热性、抗氧化性、强度、摩擦系数稳定性、耐腐蚀性、抗冻性等都要求较高。铜基摩擦材料因为其良好的导热性、自润滑性、在干湿条件下均有稳定的摩擦性能在机械加工、交通运输和航空航海等领域具有广泛应用的前景。然而铜基摩擦材料仍然存在硬度低,磨损率高,尤其是在高能载、高速度条件下因为摩擦温度过高而出现强度衰减的现象,限制了铜基摩擦材料在高速重载下的应用。近些年来,国内针对改善铜基摩擦材料的这种特性也做了广泛的研究,但关于直线刹车要求的这种高冲击力的摩擦材料目前还未有相关的应用。该摩擦材料难以从国外购买,且国内未能掌握核心技术。国内cn104384504a针对现有技术存在的不足,提供一种具有硬度,抗压强度,抗弯强度,摩擦系数和磨损量等综合性能较好的铜基粉末冶金摩擦材料及其制备方法。cn103438132a主要应用于高速列车的制动,但发明的是一种高速列车铜基粉末冶金摩擦材料与闸片钢背的连接方法,并不包含铜基粉末冶金摩擦材料配方及其制备工艺。专利cn105063459a公开了一种高速列车制动用铜基粉末冶金摩擦材料及其制备方法。在mm-1000ⅲ摩擦磨损试验机上模拟380km/h高速列车的制动工况,其平均摩擦系数为0.35~0.42,但未表明其良好的耐腐蚀性能。cn104480342a公开了一种高摩擦系数耐腐蚀铜基刹车材料及其制备方法,其材料最大承受荷载为6.6mpa,动摩擦系数大于0.32。目前,国内外相关资料未对在多种工况(高能载、高速度、高冲击力和适用各种恶劣环境)条件下使用的铜基摩擦材料有相应报道。技术实现要素:为克服现有技术中存在的不能满足高能载、高速度、高冲击力和耐腐蚀性工况要求的不足,本发明提出了一种高速直线刹车用铜基粉末冶金摩擦材料及其制备方法。本发明提出的铜基粉末冶金摩擦材料由50~60%的电解铜粉、8~1%的还原铁粉、8~10%的石墨、2~5%的硅铬合金、2~5%的二硫化钼、2~5%的二氧化硅、1~3%的氧化镧、3~5%的鉻铁和8~12%的铜纤维组成。所述的百分比为质量百分比。所述电解铜粉中铜含量≥99.8%。所述还原铁粉中fe含量≥98.5%。所述石墨为+80目鳞片状,并且该石墨中c含量≥99.99%5。所述硅铬合金中cr含量≥30%,si的含量≥40%。所述二硫化钼为mf1#或mf2#。所述二氧化硅中sio2的含量≥97%。所述氧化镧中la2o3的含量≥99.5%。所述鉻铁中cr的含量≥60%。所述铜纤维中cu为的含量≥99.8%。所述二氧化硅为-100~+200目;所述氧化镧为-400目;所述鉻铁为-200目;所述铜纤维的直径0.02~0.07mm。本发明提出的制备所述高速直线刹车用铜基粉末冶金摩擦材料的具体过程是:步骤1,铜粉和铁粉的还原;所述将铜粉和铁粉的还原温度:铜粉为350~450℃,铁粉为600~700℃,保温时间均为2~3h,得到还原后的铜粉和还原铁粉。合格的铜粉为玫瑰红色海绵状,铁粉为银灰色海绵状。步骤2,球磨;将还原合格的铜粉和铁粉分别放入球磨机中球磨0.5~1h。球磨时,钢球:铜粉/铁粉=10:1。所述的比例为质量比。步骤3,烘干;将石墨粉、二硫化钼粉和二氧化硅粉分别放入烘箱内烘干。烘干温度为120℃~150℃保温3.5~4.0h。步骤4,过筛:对烘干的二氧化硅粉、石墨粉分别过筛,取-100~+200目的二氧化硅粉,取+80目的石墨粉。步骤5,配料、混料:按配方先称取鉻铁、硅鉻合金和氧化镧,混合球磨后得到预混合料。向该预混合料中加入5%浓度的羧甲基纤维素水溶液,并且所述羧甲基纤维素水溶液的用量为预混合料总质量的三倍。当出料口温度上升至130℃时,启动料泵;当泵压达到2mpa后,打开喷雾造粒干燥机的喷枪,调节喷嘴直径0.7mm,开始造粒。造好的颗粒放置一旁备用。称取铁粉、铜粉、二氧化硅、二硫化钼、铜纤维、石墨并依次倒入料盒中;按5ml/s的速度加入混合油初步搅拌均匀;混合油的加入量为每公斤混合料加10ml;将初步搅拌均匀的物料装入到双锥型混合机中混合20~24h;将所述造好的颗粒加入到双锥型混料机中混合3~4h,得到均匀的混合料。所述混合油用机油和汽油按1:1的比例混合而成,所述的比例为质量比;所述双锥型混合机转速为40~45r/min。步骤6,压制:根据产品的设计要求称取得到的混合料,倒入模具中并刮平,冷压成型,得到密度为6.0~6.4g/cm3的铜基粉末冶金摩擦材料的压坯。铜基粉末冶金摩擦材料压坯的单位面积上压力400~600mpa,保压时间为200~240min。步骤7,烧结:将得到的铜基粉末冶金摩擦材料的压坯与摩擦材料的钢背用胶带纸组装成为组装件。将各组装件叠放形成料柱。料柱中各组装件之间用石墨垫板隔开。将叠放后的组装件装入加压烧结炉中进行烧结。对所述加压烧结炉在通氢气或氨分解气的条件下升温至700℃,加压15~22kg/cm2并保压,继续升温至890~990℃并保温200~240min。烧结结束后,水冷却到60℃以下卸压,出炉,得到铜基粉末冶金摩擦材料。本发明通过对铜基粉末冶金刹车材料的配方进行调整,用氧化镧改性铬铁粉和硅铬合金强化摩擦组元,并以羧甲基纤维素作为颗粒粘结剂加快发生化学反应,得到满足高能载、高速度、高冲击力和耐腐蚀性等工况要求的刹车材料,具有摩擦系数稳定、抗腐蚀性好的特点。经测试,本发明的平均摩擦系数μcp>0.35,摩擦材料线性磨损量≤0.0195mm/面·次,适用于高速直线刹车的铜基摩擦材料。与现有技术相比较,本发明取得的有益效果为:1、本发明利用粉末冶金制备技术,科学地设计材料的各种成分组成,详细地给出了铜基粉末冶金摩擦材料各种原材料的配比及原材料还原、球磨、烘干、过筛、配料、混料、压制、烧结等整个生产过程中的工艺方案及参数。2、本发明通过科学设计材料的各种成分组成,发挥了铜合金基体、润滑组元、固体组元等系统匹配效应,提供了一种具有良好机械强度,适用于正压力为6.6kg/cm2,中、高速范围(22.2~83.3m/s)的工况条件,并具有平均摩擦系数为0.35~0.50,线性磨损量≤0.0195mm/面·次的一种高速直线刹车用铜基粉末冶金摩擦材料及其制备方法。3、按照本发明制造的粉末冶金铜基摩擦材料,具有强度高、密度大、膨胀率低、变形量小、耐磨性良好等优点。采用该粉末冶金铁基摩擦材料制成的摩擦层厚度小于10mm的超厚型制动零件与30crmnsia(hrc34-42)钢材料制成的对偶件组成粉末冶金铜基摩擦材料摩擦副,在中高速(22.2~83.3m/s)以及湿润条件下使用时,摩擦系数均能达到0.35以上。4、按照本发明制造的摩擦材料与30crmnsia钢材料制成的对偶件组成摩擦副,在摩擦磨损性能上优于国内设计的铜基摩擦材料在高速条件下使用时的各项性能指标。摩擦过程未出现摩擦层脱落、掉块、卡滞、粘结等现象,曲线平稳,制动稳定可靠。5、本发明通过材料设计、制造工艺研究、以及小样对比试验等方面的研制和验证等工作,研究获得一种新型高强度的铜基摩擦材料,满足摩擦系数>0.35,磨损量≤0.0195mm/面·次的高性能要求。6、本发明通过使用氧化镧不但可以润湿硅铬合金和铬铁粉形成一种过渡层,而且还能通过原子取代的方式强化铜基体的强度,制备的铜基摩擦材料的硬度为40~55hb,硬度相比于未添加氧化镧的铜基摩擦材料提高了40~50%,磨损率降低了50~80%。附图说明图1是本发明获得的铜基粉末冶金摩擦材料制成的试样在惯量0.025kg·m2、正向压力0.594kn、转速2123rpm下测定的摩擦磨损性能试验曲线;图中曲线1是随刹车时间测定的摩擦系数曲线,曲线2是随刹车时间测定的转速曲线,曲线3是刹车时给定的正向压力曲线。图2是本发明获得的铜基粉末冶金摩擦材料制成的试样在惯量0.025kg·m2、正向压力0.594kn、转速7860rpm下测定的摩擦磨损性能试验曲线;图中曲线4是随刹车时间测定的摩擦系数曲线,曲线5是随刹车时间测定的转速曲线,曲线6是刹车时给定的正向压力曲线。图3是在图2的参数和在潮湿环境下测定的摩擦磨损性能试验曲线;图中曲线7是随刹车时间测定的摩擦系数曲线,曲线8是随刹车时间测定的转速曲线,曲线9是刹车时给定的正向压力曲线。图4是本发明的流程图。具体实施方式本发明是一种高速直线刹车用铜基粉末冶金摩擦材料,由50~60%的电解铜粉、8~1%的还原铁粉、8~10%的石墨、2~5%的硅铬合金、2~5%的二硫化钼、2~5%的二氧化硅、1~3%的氧化镧、3~5%的鉻铁和8~12%的铜纤维组成。所述的百分比为质量百分比。本发明通过5个实施例具体说明其技术方案。各实施例的组分见表1:本发明提出的各实施实例的组分见表1;各组分的百分比为质量百分比。表1所述电解铜粉中铜的含量≥99.8%,执行标准为gb/t5246-2007。所述还原铁粉中fe的含量≥98.5%,执行标准为gb/t4136-94。所述石墨中中c的含量≥99.99%,执行标准为gb/t3518-95。该石墨为+80目鳞片状。所述硅铬合金中cr的含量≥30%,si的含量≥40%,执行标准为gb4009-2008。所述二硫化钼为mf1#或mf2#,执行标准为q/jdc31-2009。所述二氧化硅中sio2的含量≥97%,执行标准为02jx010-11。该二氧化硅为-100~+200目。所述氧化镧中la2o3的含量≥99.5%,执行标准gb/t4154-2006。该氧化镧为-400目。所述鉻铁中cr的含量≥60%,执行标准为gb/t5683-87。该鉻铁为-200目。所述铜纤维中cu为的含量≥99.8%。铜纤维的直径0.02~0.07mm。本发明还提出了一种制备所述铜基粉末冶金摩擦材料的方法。所述的铜基粉末冶金摩擦材料是指一种由金属基粉末与非金属的添加剂经过配料混合、压制成具有一定强度的压坯、在氢气或氨分解气气氛的烧结炉中且低于基体材料熔点的温度下加压烧结使粉末之间形成冶金结合,并在干湿条件下进行摩擦制动的粉末冶金摩擦材料。制备所述铜基粉末冶金摩擦材料的具体过程是:步骤1,铜粉和铁粉的还原:将铜粉和铁粉分别置于还原炉中,在氢气作为保护气氛下进行还原,以消除所述铜粉和铁粉中的氧含量及加工硬化现象。还原温度:铜粉为350~450℃,铁粉为600~700℃,保温时间均为2~3h,得到还原后的铜粉和还原铁粉。合格的铜粉为玫瑰红色海绵状,铁粉为银灰色海绵状。本发明提出的各实施例的还原温度工艺参数见表2:表2实施例12345铜粉的还原温度℃400350420450380铁粉的还原温度℃620600650700680步骤2,球磨:将还原合格的铜粉和铁粉分别放入球磨机中球磨0.5~1h,钢球:铜粉/铁粉=10:1。所述的比例为质量比。步骤3,烘干:将石墨粉、二硫化钼粉和二氧化硅粉分别放入烘箱内,在120℃~150℃保温3.5~4.0h,以去除所述各粉末中的水分。本发明提出的各实施例的烘干工艺参数见表3:表3实施例12345烘干温度℃150140120150130保温时间h33.5433.5步骤4,过筛:对烘干的二氧化硅粉、石墨粉分别过筛,取-100~+200目的二氧化硅粉,取+80目的石墨粉。步骤5,配料、混料:按配方先称取鉻铁、硅鉻合金和氧化镧,混合球磨后得到预混合料。向该预混合料中加入5%浓度的羧甲基纤维素水溶液,并且所述羧甲基纤维素水溶液的用量为预混合料总质量的三倍。当出料口温度上升至130℃,启动料泵,当泵压达到2mpa后,打开喷雾造粒干燥机的喷枪,调节喷嘴直径0.7mm,开始造粒。造好的颗粒放置一旁备用。称取铁粉、铜粉、二氧化硅、二硫化钼、铜纤维、石墨并依次倒入料盒中;按5ml/s的速度加入混合油初步搅拌均匀;混合油的加入量为每公斤混合料加10ml;将经过初步搅拌均匀的物料装入到双锥型混合机中混合20~24h。混合结束后,将所述步骤5中造好的颗粒加入到双锥型混料机中混合3~4h,得到均匀的混合料。双锥型混合机转速为40~45r/min。所述混合油用机油和汽油按1:1的比例混合而成,所述的比例为质量比。本发明提出的各实施例混合的工艺参数见表4:表4实施例12345物料与混合油的混合时间h2023222421颗粒的混合时间h33.5433.5步骤6,压制:根据产品的设计要求称取得到的混合料,倒入模具中,并用刮平器刮平,在5000kn的液压机上冷压成型,得到密度为6.0~6.4g/cm3的铜基粉末冶金摩擦材料的压坯。铜基粉末冶金摩擦材料压坯的单位面积上压力400~600mpa,保压时间为10s。步骤7,烧结:将得到的铜基粉末冶金摩擦材料的压坯与摩擦材料的钢背用胶带纸组装成为组装件。将各组装件叠放形成料柱。料柱中各组装件之间用石墨垫板隔开。将叠放后的组装件装入加压烧结炉中进行烧结。对所述加压烧结炉在通氢气或氨分解气的条件下升温至700℃,加压15~22kg/cm2并保压,继续升温至890~990℃并保温200~240min。烧结结束后,水冷却到60℃以下卸压,出炉,得到铜基粉末冶金摩擦材料。本发明各实施例的压制工艺参数和烧结工艺参数见表5:表5实施例12345烧结温度℃890985970960975烧结压力kg/cm21518171922压力mpa400550500600450保温时间/min240230220200230使用上述各实施例中铜基粉末冶金摩擦材料所生产的粉末层厚度为10mm的块状粉末冶金摩擦材料制品的有效摩擦面积为58.24cm2。该块状粉末冶金摩擦材料制品的长度为104mm,宽度为56mm,正向承载的压力为8720n,转速为2122~7960r/min。该铜基粉末冶金摩擦材料制品与30crmnsi(hrc34-42)导向制动槽盖板组成摩擦副。平均摩擦系数>0.35,线性磨损量≤0.0195mm/面·次。本实施例模拟具体工况条件,通过试样试件的试验验证本发明的效果。(1).试验机:mm-3000型摩擦磨损性能试验台;(2).摩擦材料制品试样试件规格:20mm×15mm;(3).对偶材料:30crmnsi,硬度hrc34-42;(4).试验条件:摩擦材料制品j=0.025kg·m2,f=0.594kn,n=7960rpm;(5).试验环境:干燥环境,潮湿环境(6).试验结果:通过在mm-3000型摩擦磨损性能试验台上进行摩擦磨损性能试验,本发明获得的铜基摩擦材料制成的试样在惯量0.025kg·m2、正向压力0.594kn、转速7960rpm,平均摩擦系数μcp>0.35,单位面积吸收动能ws≥3260.69j/cm2,平均制动距离s≤126.82m,摩擦制动时间s≤2.80s,摩擦材料线性磨损量≤0.0195mm/面·次。按照上述各实施例中配方所生产的铜基粉末冶金摩擦材料主要物理机械性能见表6:表6当前第1页12