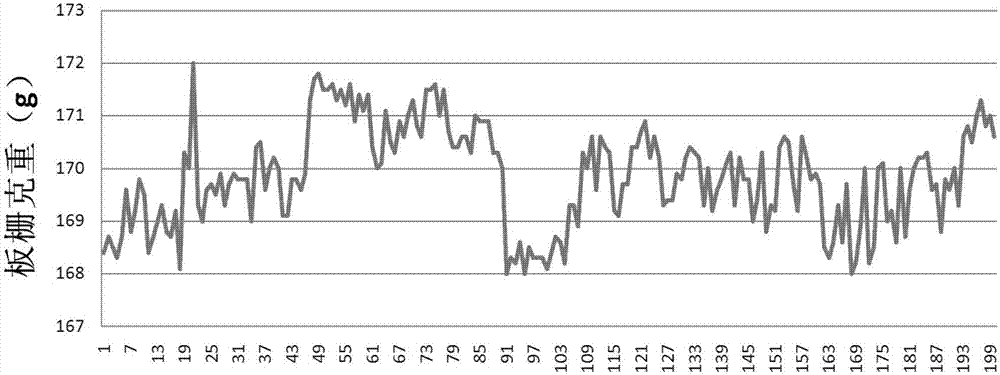
本发明涉及蓄电池生产
技术领域:
,特别是涉及一种铅蓄电池板栅浇铸用脱模剂及其制备方法。
背景技术:
:板栅是铅酸蓄电池的核心组件之一,在铅酸蓄电池中,板栅作为活性物质的载体,起着骨架支撑和粘附活性物质的作用,同时,板栅还作为电流的传导体起着集流、汇流和输流的作用,另外,板栅还作为极板的均流体能够使电流均匀分布在活性物质中。目前,板栅的加工工艺主要有浇铸和压铸,而绝大部分板栅是由铅基合金通过重力浇铸制成,即将配置好的铅基合金熔化后浇铸到板栅的模具中。在浇铸时,脱模剂是必不可少的辅助产品,一方面,脱模剂使得板栅更加容易从模具中脱出;另一方面,由于模具是金属制成,故存在散热快的特点,加之模具内腔沟槽比较窄浅,使得熔化的合金液体难以充满模具,因此,在模具表面和浇铸合金之间喷涂脱模剂可以保证合金的流动性,保证浇铸板栅的成型率。因此,脱模剂的好坏直接影响板栅浇铸的质量,脱模剂配置不好,不仅影响脱模效率,影响生产效率,还可能导致板栅浇铸时产生气孔或裂纹等,影响电流传导性能。现有脱模剂配方的主要成分是软木粉,起到保温及隔离作用,使铅液在流动过程中保持比较稳定的温度,避免铅液温度忽高忽低,使板栅不能成型。软木粉颗粒属于较大添加原料,并且软木粉高温耐受性差,使用中不断积碳,易碳化脱落,附着性或者说黏性较差,造成脱模剂耐用性较差,且由于软木粉易脱落,所以需要频繁刷膜,喷涂脱模剂,影响生产效率,造成产品稳定性较差;板栅表层孔率粗糙,造成电池极板过快被硫酸腐蚀而失效,缩短电池循环寿命。比如授权公告号为cn102873265b的中国发明专利公开了一种浇铸铅酸蓄电池板栅用脱模剂及其配制方法,该脱模剂由以下物质及重量比例组成:水100±2份,软木粉4.2±0.1份,硅酸钠2.4±0.05份,磷酸0.5±0.03份,熟胶粉0.45±0.02份,气相二氧化硅0.08±0.02份。上述浇铸铅酸蓄电池板栅用脱模剂的配制方法,包括以下步骤:(1)将配方量的去离子水、硅酸钠、熟胶粉加入到铝桶内进行加热至温度80±2℃;(2)缓缓将配方量的软木粉、气相二氧化硅加入到所得溶液中并不断搅拌,直至软木粉和气相二氧化硅均匀分散在水中;(3)继续加热小火煮沸30分钟;(4)停止加热后将配方量的磷酸加入其中并充分搅拌2~3分钟技术实现要素:本发明针对现有技术中存在的不足,提供了一种耐用性好、板栅克重稳定性好的铅蓄电池板栅浇铸用脱模剂及其制备方法。一种铅蓄电池板栅浇铸用脱模剂,包括以下质量份的原料:优选的,所述的铅蓄电池板栅浇铸用脱模剂,包括以下质量份的原料组成:优选的,所述水的电导率≤10μs/cm。优选的,所述软木粉的细度为500目。优选的,所述火山灰的细度为800目。优选的,使用时,所述酚醛树脂先溶于有机溶剂中配成溶液。一般使用浓度为12%~15%的酚醛树脂溶液,市场上销售预配的酚醛树脂溶液浓度多为12%或15%。溶解所用的有机溶剂需要是水溶性的,因为本发明脱模剂以水作为溶剂,该有机溶剂可以是甲醇、乙醇(分析纯)、丙酮等,提高溶液混合均匀性。本发明还提供了所述的铅蓄电池板栅浇铸用脱模剂的制备方法,包括以下步骤:(1)将软木粉和火山灰混合均匀;(2)将步骤(1)的混合物投入加热的水中混合均匀,降温至室温;(3)加入硅酸钠并搅拌均匀;(4)熟成;(5)加入酚醛树脂并搅拌均匀;(6)静置24~48h。优选的,步骤(2)中加热的水温度为60℃~76.7℃。优选的,熟成时间为24h。该制备方法先采用粉末状的软木粉和火山灰混合亲和,再加入60℃~76.7℃热水时能够充分渗透软木粉和火山灰的微孔结构,使调配后脱模剂稠度、浓度均匀,提高脱模剂附着在加热模具上的抗炭化。后续分步加入配比比例的溶液,提高调配脱模剂混合速度,提高混合均匀性。本发明铅蓄电池板栅浇铸用脱模剂通过加入耐高温、黏性高、不易碳化、颗粒较小的火山灰,降低脱模剂的过快脱落,增加脱模剂的耐用性,延长板栅浇铸时喷模的时间间隔,提高工作效率、提高板栅克重的稳定性。加入水性酚醛树脂,具有耐热性、耐燃性、耐水性和绝缘性优点,耐酸性较好,耐碱性差,机械和电气性能良好,脱模容易,转移率低,合成时加入不同组分,可获得功能各异的改性酚醛树脂,具有不同的优良特性,如耐碱性、耐磨性、耐油性、耐腐蚀性等。附图说明图1为实施例1脱模剂生产的200片板栅的克重分布图。图2为对比例1脱模剂生产的200片板栅的克重分布图。具体实施方式实施例1按以下步骤制备脱模剂:(1)先称量细度为500目的软木粉50g和细度为800目的火山灰(美国hess公司生产,下同)20g,将两种粉末干搅拌2分钟,混合均匀;(2)将电导率≤10μs/cm的蒸馏水加热到温度为60℃~76.7℃,然后将步骤(1)的混合物慢慢投入加热的1000g水中,连续搅拌15分钟以上混合均匀,然后静置6小时以上使降温至室温;(3)将称取好的20g的硅酸钠投入并搅拌均匀,搅拌时间10分钟;(4)静置,熟成24小时,等待软木粉和溶剂的渗透;(5)加入称取好的浓度为12%酚醛树脂溶液15g(含酚醛树脂1.8g)并搅拌均匀,搅拌时间10分钟;(6)静置24小时,使软木粉和溶剂完全渗透。实施例2按以下步骤制备脱模剂:(1)先称量细度为500目的软木粉40g和细度为800目的火山灰15g,将两种粉末干搅拌2分钟,混合均匀;(2)将电导率≤10μs/cm的蒸馏水加热到温度为60℃~76.7℃,然后将步骤(1)的混合物慢慢投入加热的1000g水中,连续搅拌15分钟以上混合均匀,然后静置6小时以上使降温至室温;(3)将称取好的25g的硅酸钠投入并搅拌均匀,搅拌时间10分钟;(4)静置,熟成24小时,等待软木粉和溶剂的渗透;(5)加入称取好的浓度为12%酚醛树脂溶液16.7g(含酚醛树脂2g)并搅拌均匀,搅拌时间10分钟;(6)静置24小时,使软木粉和溶剂完全渗透。实施例3按以下步骤制备脱模剂:(1)先称量细度为500目的软木粉60g和细度为800目的火山灰25g,将两种粉末干搅拌2分钟,混合均匀;(2)将电导率≤10μs/cm的蒸馏水加热到温度为60℃~76.7℃,然后将步骤(1)的混合物慢慢投入加热的1000g水中,连续搅拌15分钟以上混合均匀,然后静置6小时以上使降温至室温;(3)将称取好的15g的硅酸钠投入并搅拌均匀,搅拌时间10分钟;(4)静置,熟成24小时,等待软木粉和溶剂的渗透;(5)加入称取好的浓度为15%酚醛树脂溶液10g(含酚醛树脂1.5g)并搅拌均匀,搅拌时间10分钟;(6)静置24小时,使软木粉和溶剂完全渗透。对比例1作为对比实验的脱模剂制备方法:(1)量取1000g电导率≤10μs/cm的蒸馏水倒入铝锅中。(2)称取骨胶14g、聚乙烯醇4g加入铝锅中,将铝锅放在熔铅炉中加热。(3)加热至沸腾,边加热边不断搅拌,使固体物质充分溶解。(4).趁热往清液中加入细度为500目的软木粉60g,边加入边搅拌均匀,冷却至室温备用。(5)贮存期以脱模剂不腐臭为原则,但最多不得超过72h。实施例4(1)将实施例1~3中制备的脱模剂作为实验组,将对比例1中制备的脱模剂作为对照组,然后分别进行试生产,结果如表1所示,相对于对照组来说,实验组喷模次数大大减少,补模(补模是指在生产过程中,出现板栅克重开始不稳定时,进行脱模剂的补充补模。)次数也减少,说明实验组脱模剂耐用性更好。表1(2)分别统计实验组中实施例1制备的脱模机和对照组(对比例1制备的脱模剂)的重复1中生产的前200片板栅,结果如图1(实施例1)和图2(对比例1)以及表2所示,经统计分析,实验组的极差(最大值与最小值的差值)为2.6g,比对照组的4.0g小,且实验组的标准差为0.67,也比对照组的0.95小,说明使用实验组的脱模剂生产板栅的克重较为稳定。表2实施例1对比例1平均值169.3g169.9g最大值170.9g172.0g最小值168.3g168.0g极差2.6g4.0g标准差0.670.95当前第1页12