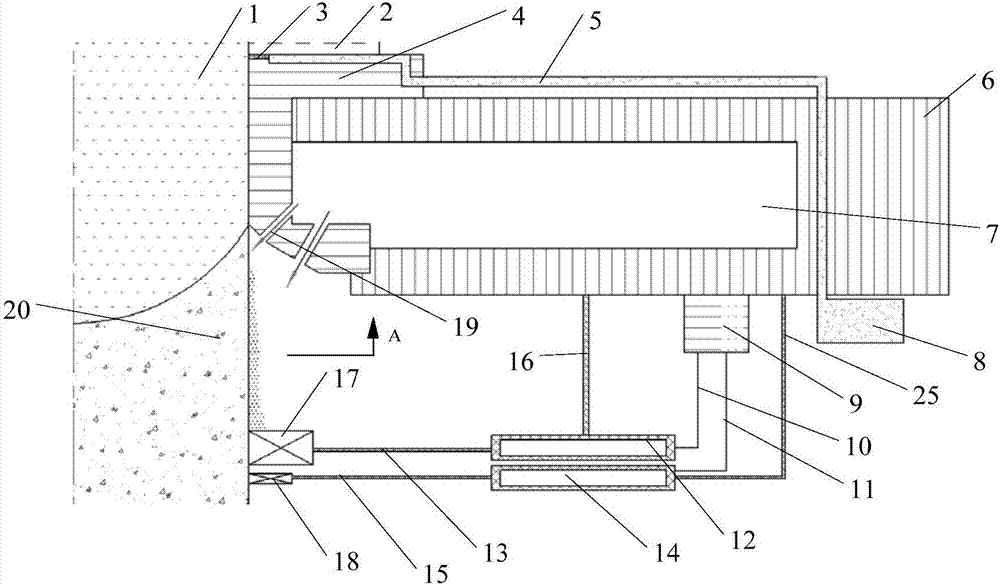
本发明属于铝合金铸造技术领域,特别涉及一种铝合金铸锭的高速半连续铸造装置及方法。
背景技术:
传统的半连续铸造装置,由于冷却速率较低,结晶器润滑较差,铸造速度受到很大限制,严重影响了铝合金铸锭的生产效率,并且组织性能以及表面质量都不理想。
在现有铸造工艺下,普通的结晶器冷却方式多为单排水眼并且水眼的角度和大小的选择难以使水流冷却效率最大化,损失了一部分二冷水的冷却效果;高速铸造条件下熔体凝固后与结晶器内套的摩擦力增大,使用普通的铸造设备易出现拉漏和拉裂;而普通的铸造设备在高速铸造条件下,在铸锭凝固后难以达到进一步强冷却的效果,可能会使铸锭发生回热,对于需要强冷却的铝合金铸锭十分不利,所以普通铸造方式和设备难以实现高速和强冷却的铸造过程。
对于铝合金而言,在普通铸造条件下,由于铸造速度较慢,冷却速率低,铝合金铸锭晶粒粗大,偏析严重,非平衡相粗大,力学性能较低,铸锭表面易出现偏析瘤等铸造缺陷,严重影响了铸锭的组织性能。铸造速率的提升所带来冷却速率的增加,能明显细化铝合金的晶粒,增强半连续铸造过程熔体的流动,改善铸锭的表面质量;因此通过改进传统铸造方法,增加铸锭内表面的润滑,提高铸造速度,是改善铸锭性能的有效方法。
技术实现要素:
为了解决现有铝合金在普通铸造条件下表面质量较差,偏析严重,晶粒粗大,合金性能较低问题,本发明提供一种铝合金铸锭的高速半连续铸造装置及方法,通过改进传统铸造方法,增加铸锭内表面的润滑,大幅度提高半连续铸造速度,以及新型二冷水阻隔装置有效增强铸锭的冷却,消除表面缺陷,减轻宏观偏析,同时达到细化晶粒,改善铸锭组织性能的效果。
本发明的铝合金铸锭的高速半连续铸造装置包括热顶、结晶器内套、结晶器外套、冷却水腔和引锭头,其中结晶器内套下方设有二冷水阻隔器,结晶器外套下方的输油管进口处设有油脂定量阀用于控制润滑油输送量,结晶器内套的内壁上的多个输油管出口通道在同一水平面上沿圆周均匀分布,输油管出口通道内部填充有多孔石墨;所述的二冷水阻隔器由金属部分和橡胶圈组成,金属部分由圆环平板和环形挡板构成,其中环形挡板由圆环平板的外侧向上向外延伸,橡胶圈与圆环平板的内侧固定在一起,橡胶圈内径与铸锭的直径相配合;整个二冷水阻隔器由左右两个形状相同的阻隔器半体构成,每个阻隔器半体与一个活塞杆固定连接在一起,与活塞杆配套的活塞缸通过电缆与一个驱动装置装配在一起;二冷水阻隔器下方设有温度检测器,用于检测铸锭表面的温度,其检测点与二冷水阻隔器的橡胶圈顶面的高度差为30~50mm。
上述装置中,温度检测器与一个活塞杆固定连接在一起,与该活塞杆配套的活塞缸通过电缆与驱动装置装配在一起。
上述装置中,结晶器内套下方设有两排二冷水眼与冷却水腔连通,其中上排二冷水眼与水平面的夹角θ1为30°~45°,下排二冷水眼与水平面的夹角θ2为50°~75°;二冷水眼的内径为1~3mm。
上述装置中,输油管的内径为1~2mm,输油管从结晶器外套内部延伸至结晶器内套内部;每个输油管出口通道对应一个输油管,每个输油管进口处设置一个油脂定量阀;每个输油管出口通道为高度0.5~1mm,深度2~4mm,宽度1~5mm的立方体空腔。
上述的温度探测器的测量范围为10~600℃。
上述装置中,二冷水阻隔器的圆环平板的顶面与结晶器内套的底面的垂直高度差为100~200mm。
上述的环形挡板与水平面的夹角θ3为30°~60°。
本发明的铝合金铸锭的高速半连续铸造方法是采用上述装置,包括以下步骤:
1、向热顶浇注铝合金熔体,开始进行半连续铸造,同时将润滑油输送到结晶器内套的内壁,对结晶器内壁进行润滑,减小铸锭凝固壳与结晶器内表面的摩擦力;通过油脂定量阀控制润滑油的输送量为10~30ml/min;
2、控制半连续铸造速度为200~400mm/min,半连续铸造过程中通过两排二冷水眼向铸锭表面喷射二冷水;当半连续铸造速度超过200mm/min时,调整润滑油的输送量,使其随铸造速度成比例上升,上升比例按每铸造速度每提高100mm/min,润滑油输送量上升25~30ml/min,半连续铸造过程中润滑油在压力下通过多孔石墨均匀渗透到结晶器内表面;
3、当铸锭长度达到300~400mm时,通过与温度检测器连接的活塞杆将温度检测器靠近铸锭,检测铸锭表面温度;
4、当铸锭表面温度大于0.8t1时,通过与阻隔器半体连接的活塞杆将两个阻隔器半体夹持在铸锭上,构成二冷水阻隔器,使沿铸锭表面流下的二冷水在二冷水阻隔器处形成水池加强冷却;然后当铸锭表面温度小于0.5t1时,通过与阻隔器半体连接的活塞杆将两个阻隔器半体从铸锭表面移开,使二冷水沿铸锭表面流下;所述的t1为铝合金的非平衡固相线温度;
5、重复步骤4的操作直至完成铸造。
上述方法中,进行半连续铸造时,铝合金的浇注温度高于铝合金的液相线30~100℃。
上述方法中,完成铸造后获得的铝合金圆棒铸锭的外径为30~200mm。
本发明的原理是:通过二冷水隔断装置,可以快速的阻断二次冷却水形成一个冷却水池强化对铸锭进行冷却,并通过温度探测器探测铸锭达到预定温度时停止阻隔,使二冷水流下;二冷水阻隔器围成与铸锭外形尺寸相同装置,保证能和铸锭紧密接触,不漏水;通过二冷水眼改进在结晶器内套设置上下两排水眼,通过控制二冷水眼的角度和大小,增加二冷水冷却效率。
本发明的优点是:一、铸造速度的大幅上升有效提高了铸造过程的生产率;二、通过多孔石墨对润滑油的供给很好的解决了高速dc铸造过程结晶器的润滑问题,大幅度提升了铸锭表面质量并保证了高速dc铸造过程的顺利进行;三、通过对结晶器二冷水眼的角度和直径的控制,使二冷水获得最佳冷却效果;四、通过在结晶器下方增加二冷水阻隔装置,进一步增加对铸锭的冷却;五、高速dc铸造下的铸锭无铸造缺陷,微观组织均匀,未出现偏析层,晶粒得到明显细化,力学性能提升。
附图说明
图1为本发明实施例1中的铝合金铸锭的高速半连续铸造装置剖面结构示意图;
图2为图1的二冷水阻隔器部分局部放大图;
图3为图2的a-a向剖面图;
图4为图3水眼部分结构剖面图;
图5为图1中的二冷水眼角度结构示意图;
图6为图1中的二冷水阻隔器俯视结构示意图;
图7为图6中的二冷水阻隔器的阻隔器半体ⅱ的垂直截面示意图;
图中:1、熔体,2、热顶,3、输油管出口通道(填充多孔石墨),4、结晶器内套,5、输油管,6、结晶器外套,7、冷却水腔,8、油脂定量阀,9、驱动装置ⅰ,10、电缆ⅰ,11、电缆ⅲ,12、活塞缸ⅰ,13、活塞杆ⅰ,14、活塞缸ⅲ,15、活塞杆ⅲ,16、连接杆ⅰ,17、二冷水阻隔器,17-1、圆环平板,17-2、环形挡板,17-3、橡胶圈,18、温度检测器,19、二冷水眼,19-1、上排二冷水眼,19-2、下排二冷水眼,20、铸锭,21、引锭头,22、阻隔器半体ⅰ,23、阻隔器半体ⅱ,24、活塞杆ⅱ,25连接杆ⅲ;
图8为本发明实施例中的铸锭产品外观照片图;图中:(a)实施例1,(b)实施例2,(c)实施例3;
图9为本发明实施例中的铸锭产品金相组织照片图:图中:(a)实施例1,(b)实施例2,(c)实施例3。
具体实施方式
本发明实施例中的二冷水阻隔器的金属部分的材质选用不锈钢。
本发明实施例中的二冷水阻隔器的橡胶圈选用耐热温度不低于500℃的橡胶。
本发明实施例中选用的铝合金为a390铝合金、al-23%si铝合金或al-18%mg2si铝合金,其非平衡固相线温度分别为为505℃、574℃和584℃。
本发明实施例中采用的多孔石墨为市购产品。
本发明实施例中采用油脂定量阀为市购产品。
本发明实施例中输油管出口的数量为8个。
本发明实施例中二冷水眼的数量为70~90个。
本发明实施例中观测金相组织采用的设备为leicadmr金相显微镜。
本发明实施例中采用的温度检测器为市购k型热电偶接触式温度检测器,测量精度不低于0.5℃。
本发明实施例中二冷水的流量为100~250l/min。
本发明实施例中铝合金铸锭的直径为30~200mm。
本发明实施例例中的各活塞缸通过连接杆固定在结晶器外套底部。
本发明实施例中驱动装置固定在结晶器外套底部。
本发明实施例中环形挡板与圆环平板的高度差h1为30~100mm。
本发明实施例中圆环平板的宽度h2为10~30mm。
本发明实施例中橡胶圈的宽度h3为10~20mm。
本发明实施例中橡胶圈和圆环平板式粘接固定在一起。
本发明实施例中采用的除气剂为六氯乙烷和氧化铝按质量比3:1混合制成,用量按除气剂占铝合金熔体总质量的0.5%加入。
实施例1
铝合金铸锭的高速半连续铸造装置结构如图1所示,局部放大结构如图2所示,a-a向结构如图3所示,包括热顶2、结晶器内套4、结晶器外套6、冷却水腔7和引锭头21,其中结晶器内套4下方设有二冷水阻隔器17,结晶器外套6下方的输油管进口处设有油脂定量阀8用于控制润滑油输送量,结晶器内套4的内壁上的8个输油管出口通道3在同一水平面上沿圆周均匀分布,输油管出口3通道内部填充有多孔石墨;
二冷水阻隔器17结构如图6和7所示,由金属部分和橡胶圈17-3组成,金属部分由圆环平板17-1和环形挡板17-2构成,其中环形挡板17-2由圆环平板17-1的外侧向上向外延伸,橡胶圈17-3与圆环平板17-1的内侧固定在一起,橡胶圈17-3内径与铸锭20的直径相配合;整个二冷水阻隔器17由左右两个形状相同的阻隔器半体:阻隔器半体ⅰ22和阻隔器半体ⅱ23构成阻隔器半体ⅰ22与活塞杆ⅰ13固定连接在一起,与活塞杆ⅰ13配套的活塞缸ⅰ12通过电缆与驱动装置ⅰ9装配在一起;阻隔器半体ⅱ23与活塞杆ⅱ24固定连接在一起,与活塞杆ⅱ24配套的活塞缸ⅱ通过电缆与驱动装置ⅱ装配在一起;
二冷水阻隔器17下方设有温度检测器18,用于检测铸锭表面的温度,其检测点与二冷水阻隔器17的橡胶圈顶面的高度差为30mm;
温度检测器18与活塞杆ⅲ15固定连接在一起,与活塞杆ⅲ15配套的活塞缸ⅲ14通过电缆与驱动装置ⅰ9装配在一起;
其中活塞缸ⅰ13通过连接杆ⅰ16固定在结晶器外套6底部,活塞缸ⅱ通过连接杆ⅱ固定在结晶器外套6底部,活塞缸ⅲ14通过连接杆ⅲ25固定在结晶器外套6底部;
结晶器内套4下方设有两排二冷水眼19与冷却水腔7连通,其中上排二冷水眼19-1与水平面的夹角θ1为30°,下排二冷水眼19-2与水平面的夹角θ2为50°;各二冷水眼19的内径为1mm;
输油管5的内径为1mm,输油管5从结晶器外套6内部延伸至结晶器内套4内部;每个输油管出口3通道对应一个输油管5,每个输油管5进口处设置一个油脂定量阀8;每个输油管出口通道3为高度0.5mm,深度2mm,宽度1mm的立方体空腔;
温度探测器的测量范围为10~600℃;
二冷水阻隔器17的圆环平板17-1的顶面与结晶器内套4的底面的垂直高度差为100mm;
环形挡板17-2与水平面的夹角θ3为60°;
铸造方法是采用上述装置,包括以下步骤:
采用的铝合金为a390铝合金;其非平衡固相线温度(t1)以505℃计算;
按照元素质量百分比准备原料,将金属铝和铝硅合金置于坩埚电阻炉中,在800~850℃熔炼;完全熔化后,加入金属cu和mg锭熔炼,并保温1h;在730~750℃时加入除气剂除气精炼10min,去除浮渣,在800~820℃静置20min,获得铝合金熔体;
向热顶浇注铝合金熔体,开始进行半连续铸造,浇注温度高于铝合金液相线温度100℃,同时将润滑油输送到结晶器内套的内壁,对结晶器内壁进行润滑,减小铸锭凝固壳与结晶器内表面的摩擦力;通过油脂定量阀控制润滑油的输送量为10ml/min;
控制半连续铸造速度为300mm/min,半连续铸造过程中通过两排二冷水眼向铸锭表面喷射二冷水;润滑油输送量上升25ml/min,即35ml/min,半连续铸造过程中润滑油在压力下通过多孔石墨均匀渗透到结晶器内表面;
当铸锭长度达到300mm时,通过与温度检测器连接的活塞杆将温度检测器靠近铸锭,检测铸锭表面温度;
当铸锭表面温度大于0.8t1时,通过与阻隔器半体连接的活塞杆将两个阻隔器半体夹持在铸锭上,构成二冷水阻隔器,使沿铸锭表面流下的二冷水在二冷水阻隔器处形成水池加强冷却;然后当铸锭表面温度小于0.5t1时,通过与阻隔器半体连接的活塞杆将两个阻隔器半体从铸锭表面移开,使二冷水沿铸锭表面流下;
重复前一个步骤的操作直至完成铸造;
获得的铝合金铸锭外观如图8(a)所示,金相组织观测结果如图9(a)所示,由图可见铸锭表面质量良好,无铸造缺陷,初生硅分布均匀。
实施例2
装置结构同实施例1,不同点在于:
(1)温度检测点与二冷水阻隔器的橡胶圈顶面的高度差为40mm;
(2)θ1为40°,θ2为60°;各二冷水眼的内径为3mm;
(3)输油管的内径1.5mm,输油管出口通道高度0.8mm,深度3mm,宽度3mm;
(4)二冷水阻隔器的圆环平板的顶面与结晶器内套的底面的垂直高度差为150mm;
(5)θ3为45°;
铸造方法同实施例1,不同点在于:
(1)采用的铝合金为al-23%si铝合金;其非平衡固相线温度(t1)以574℃计算;
(2)按照元素质量百分比准备原料将金属铝和铝硅合金置于坩埚电阻炉中,750~780℃熔炼,保温1h,在750~760℃加入除气剂除气精炼10min,去除浮渣,在760~770℃静置15min,获得铝合金熔体;
(3)通过油脂定量阀控制润滑油的输送量为20ml/min;
(4)浇注温度高于液相线60℃,半连续铸造速度400mm/min;润滑油的输送量上升2×30=60ml/min,即80ml/min;
(5)当铸锭长度达到350mm时,检测铸锭表面温度;
(6)获得的铝合金铸锭外观如图8(b)所示,金相组织观测结果如图9(b)所示,由图可见铸锭表面质量良好,无铸造缺陷,初生硅分布均匀。
实施例3
装置结构同实施例1,不同点在于:
(1)温度检测点与二冷水阻隔器的橡胶圈顶面的高度差为50mm;
(2)θ1为45°,θ2为75°;各二冷水眼的内径为2mm;
(3)输油管的内径2mm,输油管出口通道高度1mm,深度4mm,宽度5mm;
(4)二冷水阻隔器的圆环平板的顶面与结晶器内套的底面的垂直高度差为200mm;
(5)θ3为30°;
铸造方法同实施例1,不同点在于:
(1)采用的铝合金为al-18%mg2si铝合金;其非平衡固相线温度(t1)以584℃计算;
(2)按照元素质量百分比准备原料,将金属铝和其他合金成分原料置于坩埚电阻炉中,在750~770℃熔炼,保温1h,在740~760℃加入除气剂除气精炼10min,去除浮渣,在730~740℃静置15min,获得铝合金熔体;
(3)通过油脂定量阀控制润滑油的输送量为30ml/min;
(4)浇注温度高于液相线30℃,半连续铸造速度200mm/min;润滑油的输送量保持不变;
(5)当铸锭长度达到400mm时,检测铸锭表面温度;
(6)获得的铝合金铸锭外观如图8(c)所示,金相组织观测结果如图9(c)所示,由图可见铸锭表面质量良好,无铸造缺陷,初生mg2si分布均匀,与采用传统方法铸造同种铝合金相比,上述方法在高速铸造(400mm/min)时,抗拉强度由195mpa提升到261mpa,延伸率由1.3%提升至4.6%。