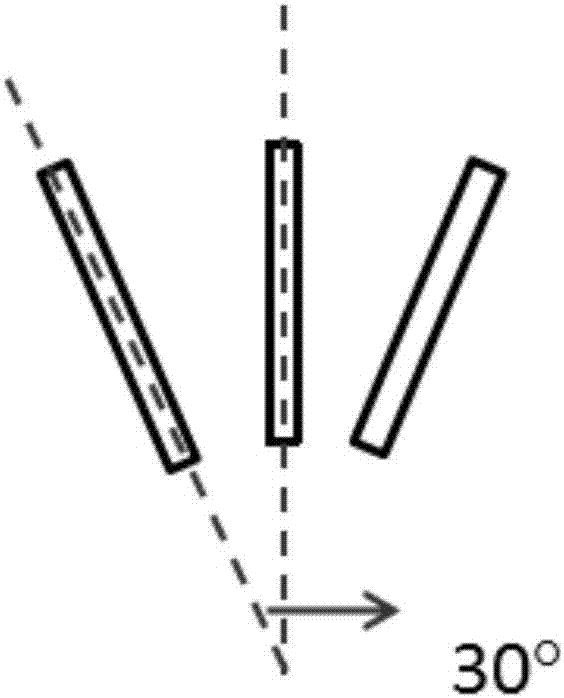
本发明涉及新材料粉体生产装置
技术领域:
,具体是一种亚微米及纳米金属粉体的生产设备。
背景技术:
:纳米材料的生产技术是纳米材料技术发展、研究和应用的关键,目前纳米材料的制备技术多达几十种。纳米金属粉体作为纳米材料一种广泛应用的材料,特别是在高品质纳米金属粉体的制备上,实现产业化最好方法有蒸发-冷凝法和高温氢还原法。蒸发-冷凝法生产过程可控,系统密闭,生产过程无废气废水,而且粉体性能优良,是生产高品质亚微米及纳米金属粉体最好的方法。1984年,gleiter首次使用蒸发-冷凝法制备了超细镍粉,该方法是利用电弧、高频电场或等离子体等高温热源将金属原料在高真空或者低压惰性气体中,加热气化或升华,然后快速冷凝成超细粉体,该方法可制备各种超细金属粉体,特点为表面光洁,粒径可控,球形度好。在随后的30多年,各国研究者在gleiter的研究基础上进行再度研发,通过设备的升级,加热方式的改变,理论基础的深入研究,蒸发-冷凝法的技术得到了长足的发展。根据加热方式不同,蒸发-冷凝法具体可分为电阻加热法、高频感应加热法、激光加热法,电子束加热法及等离子体加热法等,其不同加热方法的简要比较,如表1所示。表1蒸发-冷凝法不同加热方式的比较表加热方式气氛系统压力(pa)产量设备要求电阻加热惰性气体133~13332低低高频感应加热惰性气体133~6500低低电子束加热惰性气体133低高激光束加热惰性气体1300~14000低高等离子体加热惰性气体26000~100000中等低从表1可知,等离子体加热法因蒸发效率快,设备要求较低,所制备的超细粉体形核速率快,是目前蒸发-冷凝法中最好的制备超细金属粉的方法之一。在等离子体加热蒸发-冷凝法法制备金属粉末工艺中,一般采用高频等离子体、感应等离子体、转移弧等离子体或者非转移弧等离子体加热方法来蒸发金属得到金属蒸气,随后急冷金属蒸气得到超微细金属粉末。在高频等离子体、感应等离子体、非转移弧等离子体蒸发金属设备制备超微细金属粉末工艺中,一般采用一定粒度(50~300μm)的金属粉作为原料,金属粉直接加入到等离子体弧中,金属粉在高频等离子体弧的高温作用下,金属粉被蒸发变成金属蒸气,然后金属蒸气聚冷得到超微细金属粉末。但由于进料的金属粉有一定的粒度分布,高频等离子体、感应等离子体、非转移弧等离子体因能量不足,不仅蒸发量较低,而且会有部分粒径比较大的金属粒子蒸发不完全,残留在超微细金属粉中。这部分残留的金属粒子粒径远远大于超微细金属粉的粒径,造成产品质量的下降。在等离子体转移弧蒸发金属设备制备超微细金属粉末工艺中,一般等离子体转移弧直接作用在金属液面上,利用等离子体转移弧的高温蒸发金属得到金属蒸气,然后金属蒸气急冷得到超微细金属粉末。但由于受到直流等离子体转移弧与金属液面热量传递的限制,与金属液面的接触面小,造成金属蒸发效率低,金属粉体产量低,能量的消耗大,成本高。本发明要解决的技术问题是,提供一种能提高金属蒸发效率又无残留金属大颗粒在超微细金属粉中的金属蒸发设备,这种设备可以用于亚微米及纳米金属粉的生产,特别是生产高熔点亚微米及纳米金属粉体材料。技术实现要素:本发明的目的在于提供一种亚微米及纳米金属粉体的生产设备,以解决上述
背景技术:
中提出的问题。为实现上述目的,本发明提供如下技术方案:一种亚微米及纳米金属粉体的生产设备,包括:等离子体发生器、等离子体转移弧炬、金属粉加料设备、密封不锈钢外壳、陶瓷坩埚、电极石墨棒、废料取料口、金属蒸气过渡区、粉体收集器;等离子体转移弧炬安装在密封不锈钢外壳的上方,电极石墨棒贯穿陶瓷坩埚以及密封不锈钢外壳的底部;陶瓷坩埚放置在密封不锈钢外壳内的底部;密封不锈钢外壳的侧面设有金属蒸气过渡区,且金属蒸气过渡区的另一端连接有粉体收集器;金属粉加料设备位于多把等离子体转移弧炬中间,且贯穿密封不锈钢外壳顶部;等离子体发生器的负极与等离子体转移弧炬电连接,等离子体发生器的正极与电极石墨棒电连接。作为本发明进一步的方案:密封不锈钢外壳底部的一侧设有废料取料口。作为本发明进一步的方案:等离子体转移弧炬产生等离子体转移弧,所述等离子体转移弧的产生的介质气体包括氩气、氮气、氢气、氨气中的一种或多种。作为本发明进一步的方案:所述等离子体转移弧炬的安装数目为3~8把。作为本发明进一步的方案:等离子体转移弧炬与密封不锈钢外壳上方垂直方向的夹角为10~60°。作为本发明进一步的方案:通过金属粉加料设备进料的金属粉为高熔点金属粉或低熔点金属粉,其中高熔点金属粉包括钽粉、钽合金粉、钨合金粉、钛粉、钛合金粉,粒径为50~300μm;低熔点金属粉包括镍粉、镍合金粉、铜粉、铜合金粉、铝粉、铝合金粉、锡合金粉与不锈钢粉,粒径为50~300μm。作为本发明进一步的方案:陶瓷坩埚的直径为150-350mm,放在等离子体转移弧炬的中心下的80-250mm处。作为本发明进一步的方案:粉体收集器内放置冷却系统。作为本发明进一步的方案:冷却系统包括气相冷却系统和液相冷却系统;其中生产不易氧化的金属粉采用气相冷却系统,不易氧化的金属粉包括镍粉、铜粉、钴粉,气相冷却系统的气体为氮气、氩气、氦气中的一种或者多种;生产易氧化的金属粉采用液相冷却系统,易氧化的金属粉包括钛粉、铝粉、锂粉,液相冷却系统的介质包括但不限于水、酒精、柴油、煤油、癸烷。作为本发明进一步的方案:金属蒸气过渡区、密封不锈钢外壳、粉末收集器均含有通冷却水的水夹层。与现有技术相比,本发明的有益效果是:本发明可以利用超高温等离子体转移弧直接蒸发较大粒径的金属粉,有效提高能量利用效率和增加金属蒸发量,适合各种10~1000nm金属粉体的生产,特别是高熔点金属粉体和易氧化的金属粉。具体特点如下所述:1)采用3~8把等离子体转移弧炬作为加热源进行加热蒸发,能量利用率高,蒸发效率更快,产量很大,避免了大部分金属颗粒进入陶瓷坩埚中造成了浪费,产量可到5~30kg/h,2)生产设备通用性强,可适合各种10~1000nm金属粉的生产,生产成本低,容易实现大规模工业化生产。3)适合亚微米及纳米级高熔点金属的生产,以及易氧化的纳米级钛粉、铝粉、锂粉等的生产。附图说明图1是本发明亚微米及纳米金属粉体的生产设备的结构示意图。图2是实施例1生产106nm钽粉用6把等离子体转移弧炬布局的主视图;图3是实施例1生产106nm钽粉用6把等离子体转移弧炬布局的俯视图;图4是实施例1所生产106nm钽粉sem图。图5是实施例2所生产82nm铝粉sem图。图6是实施例3所生产289nm镍粉sem图。图7是液相冷却系统流程图。图8是气相冷却系统流程图。图中:1-等离子体发生器;2-等离子体转移弧炬;4-金属粉加料设备;5-金属粉;6-等离子体转移弧;7-密封不锈钢外壳;8-陶瓷坩埚;9-电极石墨棒;10-废料取料口;11-金属蒸气过渡区;12-粉体收集器。具体实施方式下面将结合本发明实施例,对本发明实施例中的技术方案进行清楚、完整地描述,显然,所描述的实施例仅仅是本发明一部分实施例,而不是全部的实施例。基于本发明中的实施例,本领域普通技术人员在没有做出创造性劳动前提下所获得的所有其他实施例,都属于本发明保护的范围。请参阅图1,本发明中,一种亚微米及纳米金属粉体的生产设备,包括:等离子体发生器1、等离子体转移弧炬2、金属粉加料设备4、密封不锈钢外壳7、陶瓷坩埚8、电极石墨棒9、废料取料口10、金属蒸气过渡区11、粉体收集器12。等离子体转移弧炬2安装在密封不锈钢外壳7的上方,电极石墨棒9贯穿陶瓷坩埚8以及密封不锈钢外壳7的底部;陶瓷坩埚8放置在密封不锈钢外壳7内的底部,密封不锈钢外壳7底部的一侧设有废料取料口10;密封不锈钢外壳7的侧面设有金属蒸气过渡区11,且金属蒸气过渡区11的另一端连接有粉体收集器12;金属粉加料设备4位于多把等离子体转移弧炬2中间,与电极石墨棒9相对,且贯穿密封不锈钢外壳7顶部。等离子体发生器1的负极与等离子体转移弧炬2电连接,等离子体发生器1的正极与电极石墨棒9电连接。本发明的原理是利用多把等离子体转移弧炬2产生超高温的等离子体转移弧6直接蒸发金属粉加料设备4下落的较大粒径的金属粉5,随后通过急冷得到亚微米及纳米级金属粉体,适合各种10~1000nm金属粉体的工业化生产,特别是高熔点金属粉体和易氧化的金属粉。密封不锈钢外壳7内有介质气体,等离子体转移弧6的产生的介质气体可以是氩气、氮气、氢气或者氨气,也可以是上述气体的混合气体。等离子体转移弧6具有能量密度高(能量密度可达105~106w/cm2),温度高(弧柱中心温度30000k~300000k),焰流速度大(可达300~800m/s)等优点。所述等离子体转移弧炬2,其安装数目根据所生产金属熔点、粒径以及产量设置为3~8把,等离子体转移弧炬2与密封不锈钢外壳7上方垂直方向的夹角,可根据生产情况,选用10~60°放置。所述等离子体转移弧炬2中心放置了金属粉加料设备4,大粒径的金属粉5通过金属粉加料设备4加入到多把等离子体转移弧炬2产生的等离子体转移弧6中。进料的金属粉5可以为高熔点金属粉和低熔点金属粉,其中高熔点金属粉包括钽及钽合金粉、钨合金粉、钛及钛合金粉,粒径为50~300μm;低熔点金属粉包括镍及镍合金粉、铜及铜合金粉、铝及铝合金粉、锡合金粉与不锈钢粉,粒径为50~300μm,经过生产所得的亚微米及纳米金属粉粒径为10~1000nm。电极石墨棒9与等离子体发生器1、等离子体转移弧炬2以及等离子体转移弧6构成回路。陶瓷坩埚8的直径为150-350mm,放在等离子体转移弧炬2的中心下的80-250mm处,用于收集未蒸发的进料金属残留粉。金属蒸气蒸发进入金属蒸气过渡区11,并连接粉体收集器12,金属蒸气过渡区11为调节金属蒸气的冷却速度和形核长大的空间,粉体收集器12内放置冷却系统,用于收集金属粉末。收集粉体性质的不同,冷却系统包括气相冷却系统和液相冷却系统。其中生产不易氧化的金属粉,如镍粉、铜粉、钴粉等,气相冷却系统的气体可以为氮气、氩气、氦气中的一种或者多种;生产易氧化的金属粉,如钛粉、铝粉、锂粉等,液相冷却系统的介质包括水、酒精、柴油、煤油、癸烷等有机溶剂。所述的密封不锈钢外壳7,其含有一定厚度的保温材料,作用是防止内部高温区域外界空气接触,并减少热损失,提高蒸发效率。所述的金属蒸气过渡区11、密封不锈钢外壳7、粉末收集器12均含有通冷却水的水夹层。具体应用如以下实施例所述。实施例1106nm钽电容用钽粉的生产采用6把等离子体转移弧炬2,相隔60°放置,等离子体弧炬与竖直方向的放置夹角为30°,如图2-3所示。将平均粒径为25~100μm的不规则钽原料粉加入金属粉加料设备4,检查系统密封性完毕后,开启开启鼓风机,使得系统内的氩气循环,开启等离子体发生器1,功率控制在400~500kw,随后同时启动金属粉加料设备4,进料速度控制在5~10kg/h。大粒径钽粉,通过金属粉加料设备4进入超高温等离子体转移弧中心,在6把等离子体转移弧炬2的作用下,大粒径钽粉瞬间蒸发,并在氩气保护下从金属蒸气过渡区11进入气相冷却系统,气相系统流程图如图8所示。在冷却系统中,金属蒸气冷却长大形成纳米钽粉,然后纳米钽粉和氩气通过气固分离器,收集到金属粉末,气体循环使用。少量未蒸发的进料大颗粒钽粉,再掉入在设备内放置的陶瓷坩埚8中,陶瓷坩埚8的直径为150-350mm,放在等离子体转移弧炬2的中心下的80-250mm处。所得钽粉通过比表面仪检测,其平均粒径为106nm,另有样品在扫描电子显微镜下观察形貌,如图4。实施例282nm固体推进剂用高活性铝粉的生产采用3把等离子枪,相隔120°放置,等离子体弧炬与竖直方向的放置夹角为30°。将平均粒径为15~100μm的喷雾法所生产大粒径铝粉加入金属粉加料设备4,检查系统密封性完毕后,开启开启鼓风机,使得系统内的氩气循环,开启等离子体发生器1,功率控制在200~250kw,随后同时启动金属粉加料设备4,进料速度控制在8~16kg/h。大粒径铝粉,通过金属粉加料设备4进入超高温等离子体转移弧中心,在3把等离子体转移弧炬2的作用下,粉瞬间蒸发,并在氩气保护下从金属蒸气过渡区11进入液相冷却系统,液相系统流程图如图7所示,液相介质采用煤油。在冷却系统中,金属蒸气瞬间冷却成纳米铝粉,然后纳米铝粉和煤油通过高速离心机进行液固分离,收集到铝粉,煤油循环使用。少量未蒸发的进料大颗粒铝粉,再掉入在设备内放置的陶瓷坩埚8中,陶瓷坩埚8的直径为150-350mm,放在等离子体转移弧炬2的中心下的80-250mm处。所得铝粉通过比表面仪检测,其平均粒径为82nm,另有样品在扫描电子显微镜下观察形貌,如图5所示。实施例3289nm电子元器件电极材料用镍粉的生产采用3把等离子枪,相隔120°放置,等离子体弧炬与竖直方向的放置夹角为30°,如图2所示。将平均粒径为25~100μm的镍粉加入金属粉加料设备4,检查系统密封性完毕后,开启开启鼓风机,使得系统内的氮气循环,开启等离子体发生器1,功率控制在250~400kw,随后同时启动金属粉加料设备4,进料速度控制在15~25kg/h。大粒径镍粉,通过金属粉加料设备4进入超高温等离子体转移弧中心,在3把等离子体转移弧炬2的作用下,瞬间蒸发,并在氮气保护下从金属蒸气过渡区11进入气相冷却系统,气相系统流程图如图5所示。在冷却系统中,金属蒸气冷却长大形成将镍粉,然后镍粉和氮气通过气固分离器,收集到金属粉末,气体循环使用。少量未蒸发的进料大颗粒镍粉,再掉入在设备内放置的陶瓷坩埚8中,陶瓷坩埚8的直径为150-350mm,放在等离子体转移弧炬2的中心下的80-250mm处。所得镍粉通过比表面仪检测,其平均粒径为289nm,另有样品在扫描电子显微镜下观察形貌,如图6所示。对于本领域技术人员而言,显然本发明不限于上述示范性实施例的细节,而且在不背离本发明的精神或基本特征的情况下,能够以其他的具体形式实现本发明。因此,无论从哪一点来看,均应将实施例看作是示范性的,而且是非限制性的,本发明的范围由所附权利要求而不是上述说明限定,因此旨在将落在权利要求的等同要件的含义和范围内的所有变化囊括在本发明内。此外,应当理解,虽然本说明书按照实施方式加以描述,但并非每个实施方式仅包含一个独立的技术方案,说明书的这种叙述方式仅仅是为清楚起见,本领域技术人员应当将说明书作为一个整体,各实施例中的技术方案也可以经适当组合,形成本领域技术人员可以理解的其他实施方式。当前第1页12