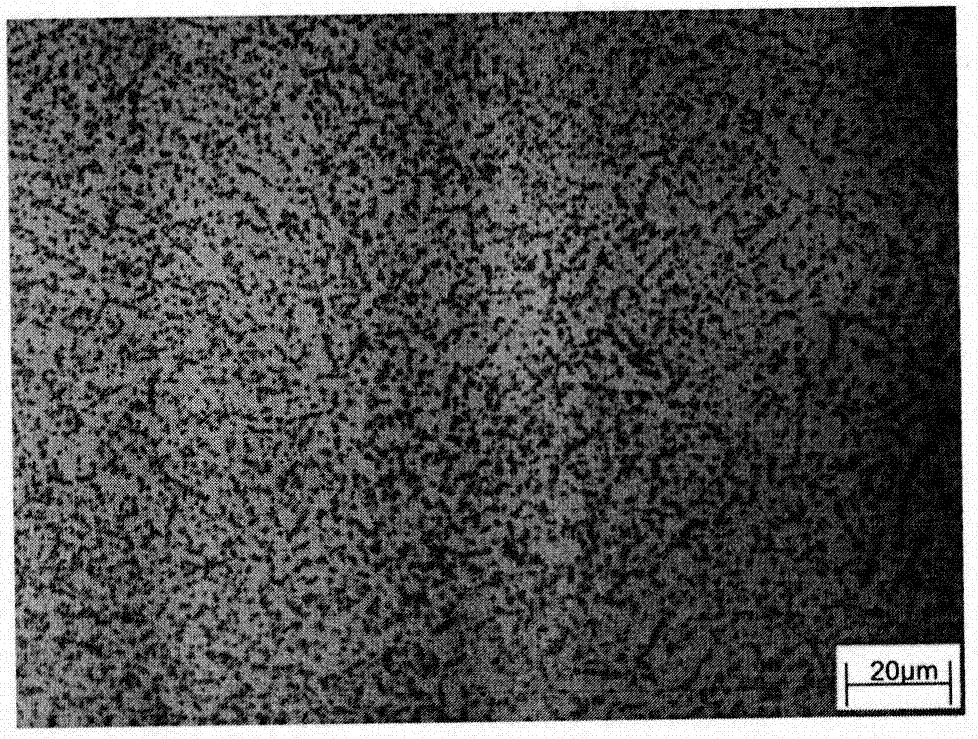
本发明属于钢合金领域,具体涉及一种高韧性、高热稳定性zw866压铸用热作模具钢及其制备方法。
背景技术:
:h13钢是国际上广泛使用的热作模具钢,因其具有良好的的热强性、热疲劳性能及综合力学性能,常被用于压铸模具。h13型热作模具钢在平衡态下可形成m23c6、m6c、mc型碳化物,并且在一定条件下向稳定碳化物转变。压铸模具使用过程中硬度的降低主要是由于二次碳化物粒子的粗化所引起的,nb元素的微量添加,可形成高熔点、稳定、细小、均匀分布的m(c、n)型碳化物或与v结合形成复合(nb、v)c型碳化物,且在高温过程中存在m23c6型碳化物向稳定、细小、弥散分布的mc型碳化物转变,可有效抑制奥氏体晶粒的长大及二次碳化物粒子的粗化,从而提高了热作模具钢冲击韧性及热稳定性。技术实现要素:本发明通过提出一种高韧性、高热稳定性zw866压铸用热作模具钢及其制备方法。其中zw866为本发明热作模具钢的牌号名称。采用成分优化设计、合理设计微观结构及所述的制备工艺,两次高温扩散技术、三维换向锻造技术、超细化处理技术、周期球化退火技术的应用,有效改善大块状液析碳化物、带状组织及球化组织均匀性、二次碳化物形态及分布均匀性,为淬火提供良好的预备组织,从而提高热作模具钢韧性及热稳定性能,解决
背景技术:
存在的上述问题。具体通过如下技术手段实现:一种高韧性、高热稳定性压铸用热作模具钢,所述热作模具钢按质量百分比含量计为:c0.35-0.45%,si0.80-1.20%,mn0.30-0.50%,cr4.80-5.50%,mo1.30-1.50%,v0.80-1.20,nb0.005-0.08%,p≤0.015%,s≤0.003%,余量为fe和不可避免的杂质。所述高韧性、高热稳定性压铸用热作模具钢的显微组织为均匀细小的球状珠光体组织,其显微结构为铁素体基体上均匀分布的球状二次碳化物,其密度为每1mm2铁素体基体面积上分布着(2.45~2.65)×104个球状二次碳化物,碳化物平均粒径为500nm-1μm,所述球状二次碳化物为m23c6型碳化物、m6c型碳化物和/或复合型碳化物,所述m23c6型碳化物主体为cr,所述m6c型碳化物主体为mo。作为优选,所述热作模具钢按质量百分比含量计为:c0.38-0.42%,si0.90-1.10%,mn0.35-0.45%,cr5.00-5.20%,mo1.35-1.45%,v0.90-1.05,nb0.008-0.05%,p≤0.012%,s≤0.001%,余量为fe和不可避免的杂质。作为优选,所述热作模具钢按质量百分比含量计,杂质元素控制量为:残余气体含量o≤12ppm,n≤80ppm,h≤1.0ppm,残余元素含量pb≤0.003%,sn≤0.010%,as≤0.010%,sb≤0.005%,bi≤0.005%,ti≤0.005%,als0.015-0.030%。上述高韧性、高热稳定性zw866压铸用热作模具钢的制备方法,包括以下步骤:a电极坯料冶炼及浇注:按照所述高韧性、高热稳定性压铸用热作模具钢的化学成分及质量百分比进行配料,采用eaf/bof+lf+vd(rh)方式进行冶炼,采用连铸或模铸方式进行铸造,得到连铸或模铸电极。b电渣冶炼:采用保护气氛电渣炉,将所述成分的热作模具钢连铸电极拼焊或模铸电极在氩气保护下进行电渣重熔,通过恒熔速工艺控制,提高电渣锭纯净度,改善结晶组织、成分偏析及致密度,进一步降低o含量。c高温扩散:采用两次高温扩散,将电渣锭在1220-1280℃下进行一次高温扩散,保温时间10-30h,出炉预变形后中间坯在1220-1280℃下进行进行二次高温扩散,保温时间10-25h,有效溶解及扩散大块高熔点一次碳化物。d三维换向锻造:中间坯在1200-1260℃保温2-5h,分别进行x、y、z三个方向的镦粗、拔长,最终沿z向拔长至成品,其中x、y为相互垂直的两个直径方向,z为原始电渣锭轴向,开锻温度1050-1200℃,终锻温度800-950℃,有效改善钢材带状及各向异性。e,超细化处理热处理:将步骤d锻后的工件进行控冷操作,冷却至400~600℃,冷却速度为20~50℃/min(优选25~40℃/min),然后重新加热至1050~1150℃的固溶温度,保温5~20h,然后采用水空交替的控时冷却方式继续进行冷却,最终冷却至芯部300~500℃后出水空冷。f周期球化退火:250-400℃装炉,并升温至830-880℃,保温8-25h,再随炉缓慢冷却至700-760℃,保温15-40h,重复多次上述830-880℃/700-760℃工艺,最后随炉缓冷至350-600℃出炉空冷至室温,获得均匀、细小的球化组织。上述制备方法中,通过两次高温扩散、三维换向锻造工艺,有效改善大块及链状液析碳化物,减小带状偏析,提高球化组织均匀性,从而提高冲击韧性。提高热稳定性的关键在于,nb元素的微量添加,形成稳定的mc型碳化物,在奥氏体化过程,nb及其碳化物溶于奥氏体中,并在后续回火过程中弥散析出mc型碳化物,并在模具使用过程中逐渐增加,有效抑制二次碳化物的粗化,从而提高热稳定性。优选地,步骤a中,连铸电极坯浇注过程采用末端电磁搅拌,减小原料截面成分偏析。优选地,步骤b中,可根据实际情况,选择合适的渣系及熔速,通过保护气氛电渣,可有效控制电渣锭偏析、纯净度及气体含量。优选地,步骤c中,高温扩散温度的选择尤为重要,扩散温度过低,达不到溶解扩散大颗粒液析碳化物的目的,扩散温度过高会造成过热或过烧,影响材料的高温塑性及综合力学性能,高温扩散需选择适当的温度进行,并与电渣锭质量匹配。优选地,步骤d中,三维锻造每个方向的锻比≥4,且锻造温度需低于高温扩散温度,保证中心组织锻造效果,最后一火锻比≥1.9,保证晶粒破碎效果,防止锻造粗晶。步骤e中,锻后冷却过程需控制冷却速度,冷却速度过慢会导致冷却过程二次碳化物沿晶界析出,冷却速度过快会导致表层及近表层出现马氏体、贝氏体等非平衡态组织,在后续超细化处理加热过程产生组织遗传。固溶温度的选择不能过高,否则会导致晶粒粗大,影响球化组织均匀性及冲击韧性,超细化处理冷速选择要以中心冷却为准,确保中心组织满足要求。优选地,步骤f中,700-760℃保温为二次碳化物析出长大过程,保温时间的选择很重要,保温时间过短会导致二次碳化物颗粒较细或有的碳化物未来得及形核,碳化物分布均匀性较差,保温时间过长会导致二次碳化物过分长大,影响综合力学性能。作为对产品使用状态下的组织评价,在步骤f后取样继续进行如下步骤:g:将步骤f得到的成品在中心取30*30*20mm试样,在1010~1050℃进行奥氏体化,保温20~50min,油冷至室温,然后在580~620℃的温度下至少回火2次,每次回火的时间为1.8~2.5h;获得碳化物弥散分布、组织均匀细小的回火索氏体组织。作为对产品使用状态下的性能评价,在步骤f后取样继续进行如下步骤:g’:将步骤f得到的成品在中心取9*12*65mm试样毛坯,在1020~1040℃进行奥氏体化,保温20~40min,油冷,然后在580~620℃的温度下至少回火2次,每次回火的时间为1.8~2.5h,使得最终回火硬度为45±1hrc,然后将得到的试样毛坯精加工至7*10*55mm的试样,进行室温无缺口冲击。本发明的效果在于:1,本方法所制备的材料组织为球化组织,一方面降低硬度,利于模具加工,另一方面为模具淬火提供良好的预备组织。均匀细小的二次碳化物颗粒分布于铁素体基体上的,有利于奥氏体化过程碳化物的充分溶解,减少基体中未溶碳化物数量及尺寸。通过对nb元素的微量添加,形成稳定的mc型碳化物,结合特定的制备方法,在奥氏体化过程,nb及其碳化物溶于奥氏体中,并在后续回火过程中弥散析出mc型碳化物,并在模具使用过程中逐渐增加,有效抑制二次碳化物的粗化,从而提高热稳定性。2,通过两次高温扩散技术,分别对电渣锭及中间坯进行高温扩散,有效改善枝晶偏析及溶解高熔点一次碳化物,从而提高成分、组织均匀性。3,通过三维换向锻造技术,对坯料x、y、z三个方向分别进行镦拔,可有效的破碎铸态组织、碳化物及消除方向性,有效改善大块及链状液析碳化物,减小带状偏析,从而改善带状组织均匀性、冲击韧性及等向性。4,通过超细化处理技术、周期球化退火技术,在较高的奥氏体化温度下,有效溶解未溶碳化物,得到均匀的奥氏体组织,在水空交替冷却方式下,有效抑制碳化物沿晶析出,最后经周期球化退火,有效控制二次球状碳化物尺寸及在铁素体基体的分布,获得均匀细小的球化组织。5,通过nb元素的微量添加,形成稳定的mc型碳化物,在奥氏体化过程,nb及其碳化物溶于奥氏体中,并在后续回火过程中弥散析出mc型碳化物,并在模具使用过程中逐渐增加,有效抑制二次碳化物的粗化,从而提高热稳定性。zw866在500℃、550℃、600℃下热稳定性明显优于普通h13(图5-7)。附图说明图1本发明热作模具钢的带状组织(50×)。图2本发明热作模具钢的球化退火组织(500×)。图3本发明热作模具钢的回火组织(500×)。图4实施例与对照例热作模具钢无缺口冲击功对比。图5实施例与对照例热作模具钢在500℃热稳定性曲线。图6实施例与对照例热作模具钢在550℃热稳定性曲线。图7实施例与对照例热作模具钢在600℃热稳定性曲线。具体实施方式本发明各实施例和对照例热作模具钢的化学成分百分含量见表1和表2。表1各实施例热作模具钢化学成分百分含量(%)实施例csimnpscrmovnb10.381.000.390.0100.00075.171.430.970.05820.400.970.400.0100.00095.151.400.980.02430.391.020.370.0110.00105.131.421.010.01840.400.980.410.0100.00085.191.410.950.008表2对照例热作模具钢化学成分百分含量(%)对照例csimnpscrmov10.390.980.420.0100.00095.181.400.9820.401.000.400.0110.00085.151.420.96实施例按以上化学成分配比所列实施例1-4,并按h13化学成分配比对照例1-2,根据上述a-f制备方案及优选方案制备出不同成分配比的热作模具钢实施例及对照例。试验例1-退火显微组织根据实施例制备的热作模具钢材料,无明显带状偏析,达到sep1614-1996标准sa1级,带状组织如图1所示。球化退火组织均匀,无大块铁素体偏析,二次碳化物颗粒细小均匀分布,退火组织达到nadca#207-2016标准as4级,球化组织见图2。试验例2-回火显微组织上述所制备的热作模具钢材料在中心取30*30*20mm试样,在1030℃进行奥氏体化,保温30min,油冷,在600℃至少回火2次,每次回火2h。获得碳化物弥散分布、组织均匀细小的回火索氏体组织,回火组织见图3。试验例3-冲击韧性上述所制备的热作模具钢材料在中心取9*12*65mm试样毛坯3个,在1030℃进行奥氏体化,保温30min,油冷,在600℃至少回火2次,每次回火2h,最终回火硬度45±1hrc。试样毛坯精加工至7*10*55mm试样,进行室温无缺口冲击。对比试样无缺口冲击功/j实施例1328实施例2342实施例3353实施例4332对照例1285对照例2298试验例4-热稳定性如图5、6和7所示,上述所制备的热作模具钢材料取样30*30*20mm试样,在1030℃进行奥氏体化,保温30min,油冷,在600℃至少回火2次,每次回火2h,最终回火硬度46hrc。两组试样分别在500℃、550℃、600℃保温1-100h,获得实施例3、4和对照例1、2在不同温度下的热稳定性曲线。当前第1页12