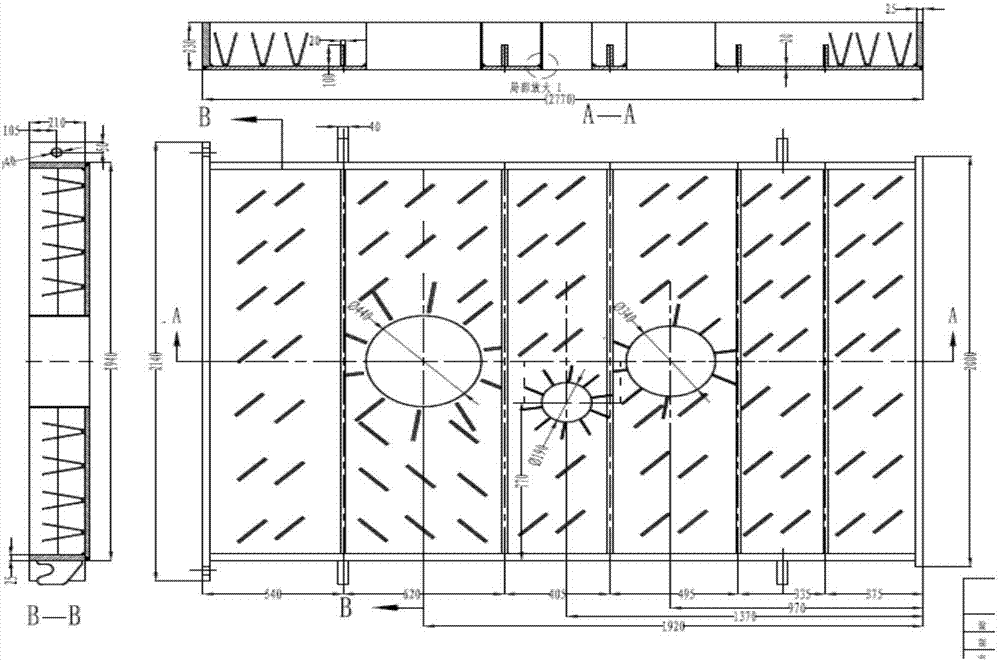
本发明涉及钢材冶炼
技术领域:
,尤其涉及一种低碳深冲钢的制备工艺。
背景技术:
:低碳深冲用热轧卷板经冷轧退火等工艺后,产品具有强度高,韧性好,易于加工成型及良好的可焊接性等优良性能,因而广泛应用于家电、船舶、汽车、桥梁、建筑、机械、压力容器等制造行业。目前,国内各钢厂生产低碳深冲钢的制造流程主要有以下几种:工艺流程1:转炉冶炼—lf炉—rh精炼—连铸浇注—钢坯清理—入炉轧制(如梅钢,马钢等);工艺流程2:转炉冶炼—rh精炼—lf炉—连铸浇注—钢坯清理—入炉轧制(此种工艺可以使用高锰合金代替低锰合金降低合金成本,如沙钢、涟钢等);工艺流程3:转炉冶炼—lf炉—连铸浇注—钢坯清理—入炉轧制(如唐钢、鞍钢等)。上述技术存在的主要缺点是工艺流程长,生产工艺的波动造成钢水质量不稳定,使钢卷起皮、重皮质量异议量在0.5%左右,而钢水提纯主要靠炉外精炼,渣量大、能耗高、铁耗高、成本高、对转炉炉衬侵蚀大,而且二氧化碳排放量高。技术实现要素:有鉴于此,本发明的目的在于提供一种工艺流程简单且能制备得到质量较好的低碳深冲钢的制备工艺。本发明提供了一种低碳深冲钢的制备工艺,包括:依次进行转炉冶炼工序、氩站工序、精炼工序、板坯连铸工序和钢坯轧制工序;所述转炉冶炼工序控制终点碳含量为0.06~0.08%,终点氧含量为200~400ppm,出钢温度为1660~1680℃。在本发明中,所述低碳深冲钢的成分优选为:0.007~0.030wt%的c;≤0.020wt%的si;≤0.30wt%的mn;≤0.020wt%的p;≤0.015wt%的s;0.020~0.060wt%的als(酸溶铝);≤0.0040wt%的n;余量为fe。在本发明中,所述低碳深冲钢的性能(拉伸性能)优选为:屈服强度优选≤210mpa;抗拉强度优选为270~350mpa;伸长率优选≥42%。在本发明中,所述转炉工序优选采用顶底复吹工艺,提高转炉供氧强度,强化全程底吹氩的搅拌效果,使终点磷含量≤0.010%,终点氮含量≤0.0015%。在本发明中,所述转炉工序优选吹炼一次拉碳成功,控制终点碳含量为0.06-0.08%,终点氧含量为200~400ppm,出钢温度控制在1660~1680℃。在本发明中,所述转炉工序优选通过自动化炼钢技术,优化钢铁料、辅料的结构,保证转炉终点成分和温度在要求范围内,为rh精炼继续脱碳提供有利条件。在本发明中,所述转炉工序出钢优选采用挡渣车操作,减少下渣量,优选控制渣层厚度≤50mm,出钢过程优选进行合金化操作。由于本发明的工艺流程中采用rh精炼工艺具有进一步脱碳的能力,所以转炉工序可以高碳出钢,避免产生大量的夹杂物。本发明中转炉出钢碳含量相对较高,使钢水过氧化程度低,脱氧合金消耗减少,钢水收得率高,减轻了对转炉炉衬的侵蚀。在本发明中,所述转炉工序出钢过程中优选加入低碱度改制渣,所述低碱度改制渣的成分优选包括:cao、al2o3和sio2;所述cao在低碱度改制渣中的质量含量优选为45~50%;所述al2o3在低碱度改制渣中的质量含量优选为20~25%;所述sio2在低碱度改制渣中的质量含量优选为8~9%。本发明采用的低碱度改制渣,改变了钢中的夹杂物形态,形成低熔点、高塑性的夹杂物。在本发明中,所述氩站工序优选为进入氩站加铝粉,从而对钢包渣进行改制,降低渣的氧化性,形成低碱度渣系,从而改变夹杂物的形态,降低夹杂物熔点,使其具有良好的塑性。在本发明中,所述rh精炼工序即钢液真空循环脱气工序。本发明优选在rh精炼工序生产前准备4炉普碳钢钢水进行循环处理。在本发明中,所述rh精炼工序过程中优选对钢包和精炼真空槽进行预热处理,预热处理的温度在400℃以上,以减少钢包和精炼过程的钢水温降,从而避免吹氧升温,增加钢中氧化物的夹杂。在本发明中,所述rh精炼过程中优选对真空槽使用前进行理化指标检验,真空槽优选使用90次后进行更换。本发明采用rh精炼方式,rh脱碳同时去除钢水中的氧,产生的气体不污染钢水,气体在上浮的过程中去除了钢中夹杂物,钢中夹杂物少,较lf炉相比,稳定了碳含量的控制,避免了电极增碳。rh精炼减少了造渣料的使用,减少电耗,可以使用高碳合金代替低碳合金,降低合金成本。本发明对rh精炼过程中顶升钢包、抽真空和将钢水抽到真空槽内进行循环的操作没有特殊的限制,采用本领域技术人员常规的操作方法进行操作即可。在本发明中,所述rh精炼过程中保证真空度优选≤67pa,进行快速脱碳、脱气操作;保证循环时间(净循环时间)优选>10min去除钢种夹杂物。在本发明中,所述板坯连铸工序优选采用中间包保护浇铸,浇铸过程进行全程保护浇铸。本发明通过改进中间包长水口的密封方式以及中间包盖的密封,使浇铸过程中隔绝空气效果更佳,浇铸过程的铝损优选≤40ppm。现有技术中,中间包盖的测温孔和取样孔采用的是方孔设计,中间包盖的材质是q345b,如图1所示,包盖在长时间高温烘烤过程中易变形。本发明对中间包盖进行改进,改进后的中间包盖测温孔和取样孔采用椭圆孔设计,材质使用q235b轧制的整张板材制作,如图2所示,这种中间包盖焊接点少,不易变形,中间包盖结构的改进使密封效果更好,更加耐用。本发明对板坯连铸工序过程中浇铸采用的中间包长水口进行改进,现有技术中采用的中间包长水口如图3所示,长水口密封圈带有折边,且密封圈在长水口的腕部内。本发明通过对中间包长水口进行改进,改进后的长水口采用氩气与密封圈联合密封的方式,带折边的密封圈会阻碍氩气的密封效果,本发明将中间包长水口的密封圈折边取消并增加密封圈的高度,使其>0.5mm,使密封圈超出长水口腕部,这种长水口密封效果更好,本发明改进后的中间包长水口如图4所示。本发明通过改进中间包盖和中间包长水口的密封,使中间包密封保护和冶金效果得到了提升,避免了中间包水口的堵塞导致钢中夹杂物在水口壁的聚集,污染钢水。在本发明中,所述板坯连铸工序采用结晶器冶金和结晶器电磁制动。本发明对结晶器冶金过程中的流场进行了优化,通过改变浸入式水口的结构,改变结晶器内的温度场,从而改变钢水的流动轨迹并延长流动时间使夹杂物上浮。现有技术中,浸入式水口底部结构为“凸形”,如图5所示,这种浸入式水口底部的温度场如图6所示。本发明优选将浸入式水口底部结构“凸形”改变为“凹形”,侧孔尺寸增大,如图7所示,改进后的浸入式水口底部的温度场如图8所示。本发明这种改进后的浸入式水口底部结构,降低了钢水的流速,减轻冲击,避免钢水向上的回流剪切力过大导致的卷渣,以及流速慢促进的夹杂物上浮。本发明为进一步减轻钢水向上的流股剪切力而采用了结晶器电磁制动技术和非正弦振动技术,进行电磁制动和结晶器振动参数的改进,避免钢水的卷渣。在本发明中,电磁制动技术的参数优选为:工作电流优选为570~590a,更优选为575~585a,最优选为580a;频率优选为1.7~1.9hz,更优选为1.75~1.85hz,最优选为1.8hz;中心磁场强度优选为590gs~610gs,更优选为595~605gs,最优选为600gs。在本发明中,结晶器振动的参数优选为:c1优选为1.7~1.8,更优选为1.75;c2优选为1.4~1.6,更优选为1.5;c3优选为130~140,更优选为135;c4优选为-9~-11,更优选为-10;c5优选为0;c6优选为0.1~0.3,更优选为0.2。本发明通过对浸入式水口+电磁制动+非正弦振动技术的改进,使钢液流股得到了改善,减少了铸坯的皮下夹杂和皮下气泡,避免了冷轧后出现条带状的起皮缺陷。起皮缺陷是指钢中夹杂着非金属物质的不规则的重叠薄片,常沿带钢辊道方向伸长,可能开口或不开口,严重影响板坯轧制后钢卷的表面质量。本发明对结晶器冶金过程中使用的保护渣进行了优化,通过对保护渣成分的优化,增加了液相渣与钢水表面的张力,对保护渣适当提高粘度,提高碱度,避免了卷渣并提高了吸附夹杂物的能力。在本发明中,所述保护渣的成分优选包括:0.38~0.42%的h2o;28~31%的sio2;33~34%的cao;1.6~1.7%的mgo;3.6~3.7%的al2o3;0.4~0.5%的fe2o3;0.3~0.4%的mno;8~9%的c。在本发明中,所述保护渣的成分更优选包括:0.4%的h2o;29.69%的sio2;33.55%的cao;1.65%的mgo;3.65%的al2o3;0.42%的fe2o3;0.31%的mno;8.08%的c。在本发明中,所述保护渣的粘度优选为0.14~0.16pa.s,更优选为0.15~0.155pa.s,最优选为0.153pa.s;所述保护渣的熔点优选为1100~1130℃,更优选为1115~1125℃,最优选为1119.1℃;所述保护渣的熔速优选为35~40s,更优选为36~38s,最优选为37s;所述保护渣的碱度优选为1.1~1.2,更优选为1.13。本发明通过优化保护渣性能,减少了卷渣,提高了吸附夹渣的效果。本发明通过上述制备工艺使夹杂物变成低熔点夹杂物,防止水口的堵塞。而且本发明提供的生产工艺使钢水的洁净度高,钢水中夹杂少,并且在连铸过程中进行了一系列的上述优化和改进,使夹杂物不易聚集,不堵塞水口。与现有技术相比,本发明无需进行钙处理操作,降低了成本。本发明对所述钢坯轧制工序的具体操作没有特殊的限制,采用本领域技术人员熟知的钢坯轧制工艺对钢坯进行轧制即可。本发明的关键点在于提供了一种改进的低碳深冲钢的生产工艺流程;对转炉、氩站、精炼钢水提纯和夹杂物形态的控制;连铸保护浇铸过程中控制方式的改进;结晶器流程优化的改进(包括优化浸入式水口+电磁制动+非正弦振动);以及所采用的保护渣成分和理化指标的优化。本发明通过对转炉、rh精炼、连铸三个工序的夹杂物控制工艺方法进行改进,解决了短流程生产低碳深冲钢的质量问题,达到生产成本降低、成品钢中夹杂物含量降低的目的,使其满足最终使用需求,提升了客户满意度。与现有技术相比,本发明缩短了生产工艺流程,减轻了转炉脱碳负担,降低精炼渣耗、能耗、二氧化碳的排放;通过转炉高碳出钢,钢水氧化性弱,并对氩站钢包渣改制,改变夹渣形态;通过rh过程工艺控制提纯钢水,减少钢中夹杂物的数量,保证钢水的纯净度,重点控制连铸过程中间包的无氧化浇铸、结晶器采用电磁制动,减轻流股冲击,结晶器流畅优化,改变钢水流动轨迹,并对结晶器振动参数优化,结晶器保护渣性能优化,充分保证上浮夹杂物的吸收,保证铸坯质量,使其夹杂物数量少、尺寸小、熔点低,分布均匀,杜绝起皮缺陷。因此,本发明提供的生产工艺解决传统生产工艺成本高、生产工艺流程长、质量不稳定、能耗高、铁耗高、耐材侵蚀严重、二氧化碳排放高等问题。附图说明为了更清楚地说明本发明实施例或现有技术中的技术方案,下面将对实施例或现有技术描述中所需要使用的附图作简单地介绍,显而易见地,下面描述中的附图仅仅是本发明的实施例,对于本领域普通技术人员来讲,在不付出创造性劳动的前提下,还可以根据提供的附图获得其他的附图。图1为现有技术中间包盖的结构示意图;图2为本发明改进后的中间包盖的结构示意图;图3为现有技术中间包长水口实物图片;图4为本发明改进后的中间包长水口实物图片;图5为现有技术浸入式水口底部结构示意图;图6为现有技术浸入式水口底部的温度场;图7为本发明改进后的浸入式水口底部结构示意图;图8为本发明改进后的浸入式水口底部的温度场。具体实施方式下面将结合本发明实施例中的附图,对本发明实施例中的技术方案进行清楚、完整地描述,显然,所描述的实施例仅仅是本发明一部分实施例,而不是全部的实施例。基于本发明中的实施例,本领域普通技术人员在没有做出创造性劳动前提下所获得的所有其他实施例,都属于本发明保护的范围。实施例按照下面的工艺流程进行低碳深冲钢的制备:转炉冶炼→氩站(钢包渣改制)→精炼(rh)→板坯连铸(结晶器冶金+结晶器电磁制动)→钢坯直接入炉轧制。转炉冶炼工序:转炉采用顶底复吹,使终点[p]≤0.010%,终点[n]≤0.0015%,吹炼一次拉碳成功,控制终点[c]含量在0.06~0.08%之间,终点[o]含量在200~400ppm,出钢温度控制在1660~1680℃之间,通过自动化炼钢技术,优化钢铁料、辅料结构,保证转炉终点成分和温度在要求范围内。出钢采用挡渣车操作,减少下渣量,控制渣层厚度≤50mm,出钢过程进行合金化操作。氩站工序:转炉出钢过程加入低碱度改制渣,其主要成分包括:cao48wt%,al2o323wt%,sio28wt%。然后进入氩站加铝粉,降低渣的氧化性,形成低碱度渣系。rh精炼工序:做好生产前的准备,在生产前准备4炉普碳钢钢水,进行循环处理。对钢包和rh真空槽进行预热,保证温度在400℃以上,真空槽耐材使用前进行理化指标检验,真空槽使用90次更换。然后进行顶升钢包,抽真空,将钢水抽到真空槽内进行循环,保证真空度≤67pa,进行快速的脱碳、脱气操作,保证净循环时间>10min。连铸工序(中间包保护浇铸+结晶器冶金+电磁制动+非正弦振动):1)中间包保护浇铸:浇铸过程进行全程保护浇铸,采用图4所示的中间包长水口的密封方式(氩气+密封圈的密封方式,密封圈无折边,密封圈高度超出水口腕部0.5mm)进行密封,以图2所示结构的中间包盖(测温孔和取样孔采用椭圆孔设计,材质为q235b)进行密封;浇铸过程的铝损≤40ppm。2)采用图7所示的凹形浸入式水口结构(浸入式水口底部具有图8所示的温度场分布);3)电磁制动技术参数:工作电流:580a频率:1.8hz中心磁场强度:600gs4)结晶器振动参数:参数c1c2c3c4c5c61.751.5135-1000.25)保护渣成分及性能对本发明实施例提供的方法制备得到的低碳深冲钢进行检测,其成分为:0.02wt%的c;0.01wt%的si;0.2wt%的mn;0.01wt%的p;0.01wt%的s;0.03wt%的als;0.003wt%的n,余量为fe。对本发明实施例提供的方法制备得到的低碳深冲钢进行性能检测,检测结果为,屈服强度为180mpa,抗拉强度为330mpa,伸长率为45%。可以看出,本发明实施例制备得到的低碳深冲钢满足成分和性能要求。采用美国进口康耐视在线表面检测仪,对实施例制备得到的低碳深冲钢卷的表面质量进行检测,其可分辨60余种钢卷表面质量缺陷,检验精度高,可100%识别钢卷起皮缺陷。检测结果表明,采用本发明提供的工艺制备得到的低碳深冲钢卷的起皮质量异议为0,钢卷质量提升效果明显,本发明提供的工艺方法能有效的控制低碳深冲钢的质量,而且生产工艺流程短,生产成本相对较低,节能减排。由以上实施例可知,本发明提供了一种低碳深冲钢的制备工艺,包括:依次进行转炉冶炼工序、氩站工序、rh精炼工序、板坯连铸工序和钢坯轧制工序;所述转炉冶炼工序控制终点碳含量为0.06~0.08%,终点氧含量200~400ppm,出钢温度为1660~1680℃。与现有技术相比,本发明对工艺流程进行优化,通过采用rh精炼工艺进行进一步的脱碳,使转炉工序可以高碳出钢,避免产生大量的夹杂物。本发明中转炉出钢碳含量相对较高,使钢水过氧化程度低,脱氧合金消耗减少,钢水收得率高,并减轻对转炉炉衬的侵蚀。本发明提供的制备工艺能够得到质量良好的低碳深冲钢。当前第1页12