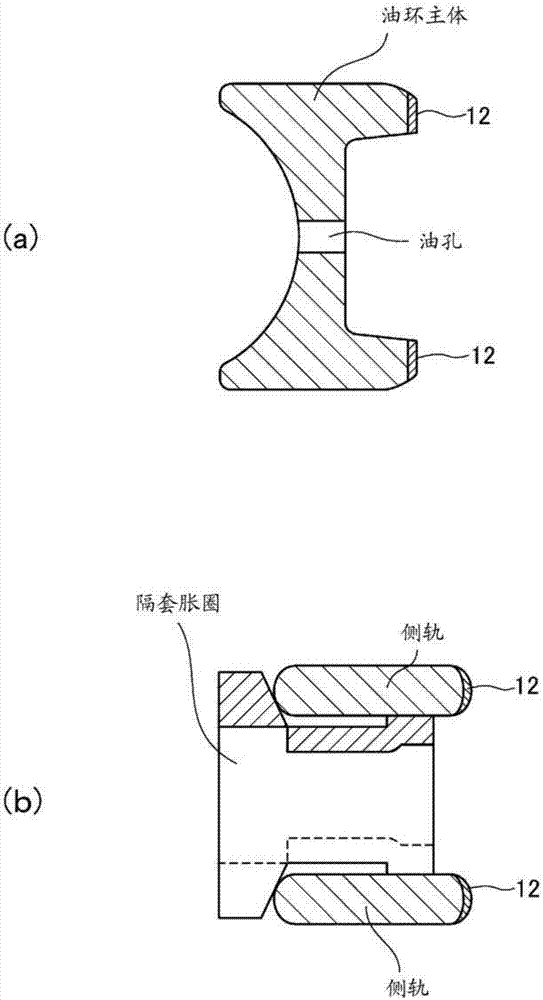
本申请是中国申请号为201480003731.x、发明名称为“硬质碳被膜”且申请日为2014年02月27日的专利申请的分案申请。本发明涉及硬质碳被膜,特别涉及在硬质碳被膜层内的密合性高,初始融合性及耐磨性良好的硬质碳被膜。
背景技术:
:一直以来,已知形成在活塞环等滑动零件的滑动面上且具有低摩擦和耐磨性的各种硬质碳被膜。在下述专利文献1中,记载了一种硬质碳被膜,在滑动面上被覆有碳类被膜的活塞环中,所述被膜是叠层两层以上硬度不同的两种类的层而得到的叠层被膜,所述两种类的层的硬度差为500~1700hv,硬度高的层的厚度与硬度低的层的厚度相同或更厚,被膜整体的厚度形成为5.0μm以上。另外,在下述专利文献2中记载了一种dlc涂层,涉及一种内燃机的滑动部件特别是活塞环,其具有ta-c型的dlc涂层,残余应力在所述涂层的整个厚度上发生变化,包含至少一个残余应力梯度。现有技术文献专利文献专利文献1:日本特开2012-202522号公报专利文献2:日本特表2012-527581号公报技术实现要素:发明所要解决的问题但是,专利文献1记载的硬质碳被膜由于是将硬度不同的硬质碳被膜多层叠层而成,因此虽然可以较厚地形成膜厚,但是硬度高的层的厚度为5~90nm时,最表面不一定总是保持高硬度的膜,因此存在耐磨性差这种问题。另外,有可能产生层间剥离,存在为了形成多层叠层结构而使制造工序变得繁杂,难以容易地制造这种问题。另外,专利文献2记载的硬质碳被膜虽然可以较厚地形成层厚度,但是残余应力在被膜的整个厚度上发生变化,需要形成至少一个残余应力梯度,因此存在制造工序繁杂,难以容易地制造这种问题。因此,本发明是鉴于上述问题而开发的,其目的在于,提供一种硬质碳被膜,其在硬质碳被膜层内的密合性高,初始融合性及耐磨性良好,并且可以通过简单的制造方法就能够形成希望的膜厚。解决问题的技术方案本发明的硬质碳被膜形成于活塞环基材的至少外周滑动面上,且实质上不含氢,其中,通过将电子能量损失谱法(eels)与透射型电子显微镜(tem)组合而成的tem-eels光谱法测定的所述硬质碳被膜的sp2成分比为40%~80%,所含的大颗粒在硬质碳被膜表面的面积比为0.1%~10.0%。另外,本发明的硬质碳被膜优选通过改变电弧电流强度的工序来形成,所述改变电弧电流强度的工序包括:在电弧电流为60a~100a、脉冲偏压为-2000v~-800v的条件下进行处理的第1成膜工序、以及在电弧电流为100a~150a、脉冲偏压为-2000v~-800v的条件下进行处理的第2成膜工序。另外,优选的是,本发明的硬质碳被膜在最表面具有表层纳米叠层部,用透射型电子显微镜(tem)观察所述表层纳米叠层部时,被膜截面为条纹状。另外,优选的是,本发明的硬质碳被膜的所述表层纳米叠层部还包括最表面成膜工序:在所述第2成膜工序后,以规定的间隔反复多次地进行脉冲偏压为-2000v~-800v的高电压处理和脉冲偏压为-200v~-100v的低电压处理。另外,优选的是,本发明的硬质碳被膜在所述硬质碳被膜下具有由ti、cr或si制成的基底层。另外,优选的是,本发明的硬质碳被膜在所述基底层和所述活塞环基材之间形成有由pvd被膜、镀cr被膜或氮化层的任一个制成的基材层。另外,优选的是,本发明的硬质碳被膜形成了如下的表面粗糙度:基于din4776标准的初始磨损高度rpk为0.2μm以下。另外,优选的是,本发明的硬质碳被膜的膜厚形成为5μm以上。另外,优选的是本发明的硬质碳被膜的膜厚形成为0.5μm以上且低于5μm。发明效果本发明的硬质碳被膜通过将电子能量损失谱法(eels)与透射型电子显微镜(tem)组合而成的tem-eels光谱法测定的sp2成分比为40%~80%,且所含的大颗粒在硬质碳被膜表面的面积比为0.1%~10.0%,因此能够形成耐磨性优异的硬质碳被膜。另外,大颗粒在硬质碳被膜表面的面积比为0.1%~10.0%,因此其表面凹凸变小。其结果是,不需要进行作为最终加工的例如研磨或抛光加工等表面平滑化处理,就能够以低成本提供具有上述特性的活塞环。本发明的硬质碳被膜通过包括在电弧电流为60a~100a、脉冲偏压为-2000v~-800v的条件下进行处理的第1成膜工序、以及在电弧电流为100a~150a、脉冲偏压为-2000v~-800v的条件下进行处理的第2成膜工序的离子镀膜法形成,因此能够在同一道次内进行处理,可以容易地形成硬质碳被膜层内的密合性高、耐磨性良好的硬质碳被膜。在第1成膜工序中,抑制了大颗粒的核生成,并且还抑制了核生长。其结果是,在第2成膜工序中抑制了大颗粒的增加,可形成表面凹凸小而平坦的膜,能够提高初始融合性及耐磨性。另外,本发明的硬质碳被膜在最表面具备表层纳米叠层部,用透射型电子显微镜(tem)观察该表层纳米叠层部时被膜截面为条纹状,因此能够提高韧性及耐磨性。另外,因为本发明的硬质碳被膜还具备最表面成膜工序,即,在所述第2成膜工序后以规定间隔反复多次脉冲地进行偏压为-2000v~-800v的高电压处理和脉冲偏压为-200v~-100v的低电压处理,因此可以提高硬质碳被膜表面的韧性及耐磨性,防止裂纹及缺口。另外,本发明的硬质碳被膜在所述硬质碳被膜之下具有含有ti、cr或si的基底层,因此能够提高硬质碳被膜的密合性。另外,本发明的硬质碳被膜在所述基底层和所述活塞环基材之间形成有由pvd被膜、镀cr被膜或氮化层的任一个构成的基材层,因此能够提高硬质碳被膜的密合性。另外,本发明的硬质碳被膜的表面粗糙度如下:基于din4776标准的初始磨损高度rpk为0.2μm以下,因此能够提高初始融合性。另外,本发明的硬质碳被膜因在硬质碳被膜内的密合性高,因此即使将其膜厚形成为5μm以上,也能够良好地保持耐磨性。另外,本发明的硬质碳被膜在硬质碳被膜内的密合性高,因此即使其膜厚形成为0.5μm以上且低于5μm,也能够良好地保持耐磨性。附图说明图1是形成有本发明的实施方式的硬质碳被膜的活塞环的剖视图;图2(a)表示在2片式油环上形成有本实施方式的硬质碳被膜的情况的图,(b)表示在3片式油环上形成有本实施方式的硬质碳被膜的情况的图;图3是表示本发明的实施方式的硬质碳被膜的制造工序的流程图;图4是表示在离子镀膜法中的电弧电流及脉冲偏压的变化的图;图5是用于说明摩擦磨损试验的概要的图;图6是用于说明磨损试验的概要的图;图7是表示磨损试验的试验结果的图表;图8是显示透射型电子显微镜确认结果的被膜截面tem像且在弱焦条件下拍摄的图,(a)是实施例1的观察结果,(b)是实施例2的观察结果;图9表示共焦点显微镜对被膜表面状态的确认结果的图,(a)是实施例1的观察结果,(b)是比较例2的观察结果;图10是将本实施方式的硬质碳被膜用于形成有基材层的活塞环基材时的活塞环的剖视图。标记说明10:活塞环;11:活塞环基材;12:硬质碳被膜;13:基底层;14:基材层。具体实施方式下面,使用附图对用于实施本发明的最佳实施方式进行说明。另外,以下的实施方式不限定各权利要求的发明,另外,实施方式中说明的特征的全部组合对于发明的解决方案而言并非是必须的。图1是形成有本发明的实施方式的硬质碳被膜的活塞环的剖视图,图2(a)是表示在2片式油环上形成有本实施方式的硬质碳被膜的情况的图,(b)是表示在3片式油环上形成有本实施方式的硬质碳被膜的情况的图,图3是表示本发明的实施方式的硬质碳被膜的制造工序的流程图,图4是表示在离子镀膜法中电弧电流及脉冲偏压的变化的图,图5是用于说明摩擦磨损试验的概要的图,图6是用于说明磨损试验的概要的图,图7是表示磨损试验的试验结果的图表,图8是用表示透射型电子显微镜的确认结果的被膜截面tem像且在弱焦条件下拍摄的图,(a)是实施例1的观察结果,(b)是实施例2的观察结果,图9是表示用共焦点显微镜对被膜表面状态的确认结果的图,(a)是实施例1的观察结果,(b)是比较例2的观察结果,图10是将本实施方式的硬质碳被膜应用于形成有基材层的活塞环基材时的活塞环的剖视图。如图1所示,在形成有本实施方式的硬质碳被膜的活塞环10中,在活塞环基材11的至少外周滑动面上形成有硬质碳被膜12。另外,在硬质碳被膜12之下形成有基底层13。另外,也可以不必设置基底层13,其形成是任意的。形成有本实施方式的硬质碳被膜12的活塞环10,是安装于形成在活塞上的活塞环槽内,通过活塞的往复运动一边在汽缸套的内周面滑动一边进行往复运动的滑动部件。另外,活塞环10可以用作顶环、第二环、油环中的任何活塞环。另外,在将本实施方式的硬质碳被膜12应用于油环的情况下,可以应用于如图2(a)所示由油环主体和螺旋胀圈构成的2片式油环,或如图2(b)所示由两个侧轨和隔套胀圈(スペーサエキスパンダ,spacerexpander)构成的3片式油环中的任一种油环。活塞环基材11的材质没有特别限定,只要是由一直以来使用的材质构成即可,优选使用对于由任何材料构成的活塞环基材11都可以适用的例如不锈钢材料、铸造材料、铸钢材料、钢材等。具体而言,优选使用马氏体不锈钢、铬锰钢(sup9材料)、铬钒钢(sup10材料)以及硅铬钢(swosc-v材料)等。另外,活塞环基材11可以是在母材上直接形成硬质碳被膜12,也可以对pvd处理(cr-n系、cr-b-n系、ti-n系)、镀cr处理或氮化处理过的活塞环基材11形成硬质碳被膜12。另外,本实施方式的活塞环10优选制成安装于由铝合金形成的活塞的活塞环使用,优选制成针对由铸铁、硼铸铁、铸钢、铝合金等构成的汽缸套的活塞环使用。另外,作为活塞环基材11,也可以根据需要进行前处理。作为前处理,优选进行表面抛光,调整表面粗糙度。表面粗糙度的调整例如优选通过用金刚石研磨料对活塞环基材11的表面进行研磨加工而进行表面抛光的方法等进行。通过这样的表面粗糙度的调整,可以将活塞环基材11的表面粗糙度调整至以jisb0601(2001)中的算术平均粗糙度ra计为0.02μm以上0.07μm以下的范围内。本实施方式的硬质碳被膜12是由非晶态的碳构成的被膜,含有0.1~5.0原子%的氢(h),余部除碳(c)以外由不可避免的杂质构成。另外,本实施方式的硬质碳被膜12的膜厚可以形成希望的厚度,例如,可以形成为5μm以上。在此,对于以上述比率含有h的理由进行说明。因为若h比0.1原子%少,则被膜硬度过高,密合性就会变差,若h比5.0原子%多,则会妨碍硬质碳被膜的特征即低摩擦性及耐磨性。另外,本实施方式的硬质碳被膜仅含有0.1~5.0原子%左右的h,因此从硬质碳被膜整体来看,实质上是不含氢的所谓无氢硬质碳被膜。需要说明的是,在ar气氛中形成硬质碳被膜时,通过在氩气中封入微量h,从而使h含于硬质碳被膜中。一般而言,硬质碳被膜是以石墨为代表的碳键sp2键、以金刚石为代表的碳键sp3键混合存在的被膜。另外,所谓sp2成分比,表示石墨成分(sp2)相对于硬质碳的石墨成分(sp2)及金刚石成分(sp3)的成分比(sp2/(sp2+sp3))。优选的是,通过将电子能量损失谱法(eels)与透射型电子显微镜(tem)组合而成的tem-eels对本实施方式的硬质碳被膜12进行测定时,sp2成分比为40%以上80%以下的范围内。sp2成分比低于40%时,易产生硬质碳被膜内部的剥离,不优选。若sp2成分比超过80%,则成为石墨,因此难以形成硬质碳被膜,不优选。更优选为sp2成分比为40%以上60%以下的范围内。这样的sp2成分比的测定可以通过eels分析装置(gatan制造,model863giftridem)进行。tem-eels法进行测定的测定步骤如下。(1)通过eels分析装置测定eels光谱。对于测定的eels光谱,用以一次函数对峰前拟合,用三次函数对峰后进行拟合,将峰值强度标准化。(2)然后,将金刚石的数据和石墨的数据进行对比,使峰值的开始位置一致,进行能量校正。(3)对于校正完成的数据,求出280ev~310ev的范围内的面积。(4)在280ev~295ev的范围,分离为两个峰(一个为sp2的峰,另一个是ch或非结晶的峰),求出285ev附近的峰面积。(5)获取上述(3)的280ev~310ev的范围内的面积、上述(4)的285ev附近的峰面积。对于该面积比,将石墨设为100,将金刚石设为0,根据相对值求出sp2成分比。将这样求出的值作为sp2成分比。另外,将后述的实施例1及2作为试样时按照上述测定步骤得到的数据示于下述表。本测定方法中,取3个分析点计算出平均值。(表1)另外,本实施方式的硬质碳被膜12的表面粗糙度即初始磨损高度rpk为0.2μm以下,其结果是,可以提高初始融合性。若rpk超过0.2μm,表面的凹凸则变大,不能实现优异的初始融合性。另外,更优选初始磨损高度rpk为0.15μm以下。大颗粒在本实施方式的硬质碳被膜12表面中的面积比为0.1%~10.0%,其结果是。能够提高初始融合性和耐磨性。若超过10.0%,则表面的凹凸增大,不能实现优异的耐磨性。另外,若低于0.1%,虽然能够实现优异的耐磨性,但成膜本身较难,在制造管理和成本方面存在一些难点。另外,大颗粒在硬质碳被膜12表面中的面积比更优选为0.1%~5.0%。该大颗粒在硬质碳被膜表面中的面积比可以使用激光技术株式会社制造的共焦点显微镜(optelicsh1200)进行图像解析而获得。具体地说,拍摄活塞环外周(物镜100倍、黑白共焦图像),并实施自动二值化来进行。阈值决定法通过判别分析法进行,进行调整并将研磨缺陷等排除之后,从被二值化的图像提取面积率。测定硬质碳被膜的5处任意部位,取其平均值。另外,本实施方式的硬质碳被膜12的硬度(从被膜表面测定)以维氏硬度hv计为1500~2500的范围,通过纳米压痕法测定时为20gpa以上、30gpa以下的范围。另外,维氏硬度可以使用微小维氏硬度试验机(株式会社akashi制)等进行测定,利用纳米压痕法进行的测定例如可以使用株式会社elionix.制造的纳米压痕仪进行测定。另外,在本实施方式的硬质碳被膜12的最表面形成有表层纳米叠层部,该表层纳米叠层部被叠层至希望的厚度,形成0.1μm以上、2μm以下的程度的总厚度。若厚度低于0.1μm,则不能充分发挥韧性及耐磨性提高的作用,若超过2μm,成膜需要时间,成本提高,因此不优选。表层纳米叠层部的各层厚度为0.01μm以上、0.02μm以下程度,叠层多层该范围内的厚度的层而构成。优选表层纳米叠层的最表面的硬度为hv1800~2800的范围。基底层13由选自cr、ti或si的至少一种金属形成。本实施方式的硬质碳被膜12在硬质碳被膜12下形成有基底层13,因此能够提高硬质碳被膜12和活塞环基材11之间的密合性。理想的是,基底层13通过溅射法或离子镀膜法形成。另外,将硬质碳被膜12的膜厚形成为5μm以上时,优选基底层13形成为0.1~2.0μm的厚度。另外,在硬质碳被膜12的膜厚低于5μm的情况下,基底层13适合形成为0.05~1.0μm的厚度。接着,参照图2及图3对本实施方式的硬质碳被膜12的制造方法进行说明。第1,为了将活塞环基材11的表面粗糙度即jisb0601(2001)中的算术平均粗糙度ra调整为0.02~0.07μm而通过金刚石磨料对活塞环基材11的表面进行研磨,对表面进行抛光。之后,经由安装夹具安放在腔室内,使腔室内形成真空后,通过加热器进行预热,并实施离子清洗,导入惰性气体即氩气,通过溅射法或离子镀膜法预先想活塞环基材11上形成基底层13(s101)。之后,将封闭靶的百叶窗打开,从靶中放出碳等离子,通过电弧离子镀膜法在基底层13上叠层形成硬质碳被膜12(s102~s104)。需要说明的是,就电弧离子镀膜法而言,如果使用过滤阴极电弧方式(filteredcathodicvacuumarc:fcva),可以抑制大颗粒。另外,作为使用fcva的过滤方法,可以采用使管状的电磁过滤器在靶和腔室之间发生弯曲的结构(弯曲结构)。另外,就弯曲的次数而言,可以形成一个弯曲部位,也可以形成二个弯曲部位以上。通过采用这种弯曲机构,在弯曲机构中,大颗粒会堆积于电磁过滤器的内壁而被除去,可以仅将离子化的靶导入腔室内。如图3所示,该电弧离子镀膜法包括在电弧电流为60a~100a、脉冲偏压为-2000v~-800v的条件下进行处理的第1成膜工序s102、和在电弧电流为100a~150a、脉冲偏压为-2000v~-800v的条件下进行处理的第2成膜工序s103。另外,在此之后,还包括以规定间隔多次反复实施电弧电流维持在100a~150a不变,而脉冲偏压为-2000v~-800v的高电压处理和脉冲偏压为-200v~-100v的低电压处理的最表面成膜工序s104。第1成膜工序s102是为了抑制急剧的电弧电流增加而产生的密合不良和大颗粒的增加而实施的工序,通过该第1成膜工序s102,产生碳等离子,对活塞环10施加脉冲偏压,以0.1~0.5μm的厚度形成硬质碳被膜12。第2成膜工序s103是以希望的厚度形成硬质碳被膜12的工序,实施达到希望的厚度的处理。另外,由第2成膜工序s103形成的膜厚为0.5~12.0μm左右,更优选形成1.0~8.0μm。由该第2成膜工序s103形成的硬质碳被膜12可以形成以维氏硬度hv计为1700左右的硬度。最表面成膜工序s104是为了提高硬质碳被膜12的最表面的硬度而实施的工序,以1~10秒的间隔切换脉冲偏压为-2000v~-800v的高电压处理和脉冲偏压为-200v~-100v的低电压处理进行成膜。优选该最表面成膜工序s104的处理后的硬质碳被膜12的最表面形成以维氏硬度hv计为2000左右的硬度。将该第1成膜工序s102、第2成膜工序s103及最表面成膜工序s104的电弧电流、脉冲偏压设置在上述的范围的理由如下。在第1成膜工序s102中,形成硬质碳被膜12时,在成膜初期的电弧电流比60a小的情况下,因电弧电流过小,难以对电弧电源进行控制,电弧电流超过100a的情况下,有可能导致电弧电流的急剧增加而产生密合不良(剥离)或大颗粒增加。在第2成膜工序s103中,通过第1成膜工序s102使电弧放电稳定后,电弧电流比100a小的情况下,成膜速度变慢,使硬质碳被膜12形成至规定的膜厚就会花费时间,电弧电流比150a大的情况下,产生过剩的碳等离子,大颗粒的产生增多。另外,对于脉冲偏压,以单层施加于活塞环基材11上的脉冲偏压比-800v大时,无法在维持耐磨性不变的情况下形成厚膜,脉冲偏压比-2000v小的情况下,成膜速度变慢,要将硬质碳被膜12成膜至规定的膜厚需花费时间。另外,在最表面成膜工序s104中,施加于活塞环基材11的脉冲偏压比-100v大时,会形成膜应力低、耐磨性低的膜,脉冲偏压比-200v小的情况下,无法在维持耐磨性不变的情况下形成厚膜。另外,从上述的第1成膜工序s102向第2成膜工序s103转移时电弧电流上升的方法,可以使其阶梯状逐步变化,也可以使其倾斜状线性变化。实施例接着,参照实施例和比较例,对本发明进一步详细地进行说明。(摩擦磨损试验)首先,在φ80mm的活塞环基材(在jis标准的swosc-v材料的外周滑动面上实施25μmcr-n系的pvd被膜)的表面,通过离子镀膜法形成0.3μm的ti层作为基底层。在该活塞环基材11上通过以下的方法成膜硬质碳被膜并进行摩擦磨损试验,观察有无磨损。另外,活塞环基材使用由c:0.55质量%、si:1.35质量%、mn:0.65质量%、cr:0.70质量%、cu:0.03质量%、p:0.02质量%、s:0.02质量%、残量:fe及不可避免的杂质构成的基材。(实施例1)在第1成膜工序(电弧电流90a、脉冲偏压-1800v)中,用18分钟形成0.2μm的膜厚,在第2成膜工序(电弧电流120a、脉冲偏压-1800v)中,用456分钟形成5.2μm的膜厚,作为整体形成膜厚5.4μm的硬质碳被膜。(实施例2)在第1成膜工序(电弧电流90a、脉冲偏压-1800v)中,用18分钟形成0.2μm的膜厚,在第2成膜工序(电弧电流120a、脉冲偏压-1800v)中,用456分钟形成5.2μm的膜厚,在最表面成膜工序(电弧电流120a、将脉冲偏压设为-1800v和-150v,以3秒间隔反复720次)中,形成0.8μm的膜厚,作为整体形成膜厚6.2μm的硬质碳被膜。(实施例3)在第1成膜工序(电弧电流100a、脉冲偏压-1200v)中,用41分钟形成0.5μm的膜厚,在第2成膜工序(电弧电流150a、脉冲偏压-1200v)中,用772分钟形成11.0μm的膜厚,作为整体形成膜厚11.5μm的硬质碳被膜。(实施例4)在第1成膜工序(电弧电流100a、脉冲偏压-1200v)中,用41分钟形成0.5μm的膜厚,在第2成膜工序(电弧电流150a、脉冲偏压-1200v)中,用772分钟形成11.0μm的膜厚,在最表面成膜工序(电弧电流150a、将脉冲偏压设为-1200v和-100v,以3秒间隔反复720次)中,形成1.0μm的膜厚,作为整体形成膜厚12.5μm的硬质碳被膜。(实施例5)在第1成膜工序(电弧电流60a、脉冲偏压-2000v)中,用14分钟形成0.1μm的膜厚,在第2成膜工序(电弧电流100a、脉冲偏压-2000v)中,用105分钟形成1.0μm的膜厚,在最表面成膜工序(电弧电流140a、将脉冲偏压设为-2000v和-200v,以3秒间隔反复720次)中,形成1.0μm的膜厚,作为整体形成膜厚2.1μm的硬质碳被膜。(实施例6)在第1成膜工序(电弧电流100a、脉冲偏压-2000v)中,用41分钟形成0.5μm的膜厚,在第2成膜工序(电弧电流150a、脉冲偏压-2000v)中,用281分钟形成4.0μm的膜厚,作为整体形成膜厚4.5μm的硬质碳被膜。(实施例7)在第1成膜工序(电弧电流60a、脉冲偏压-1200v)中,用14分钟形成0.1μm的膜厚,在第2成膜工序(电弧电流150a、脉冲偏压-1200v)中,用70分钟形成1.0μm的膜厚,作为整体形成膜厚1.1μm的硬质碳被膜。(比较例1)通过溅射法(电力3000w、脉冲偏压-150v)用75分钟形成膜厚0.045μm的低硬度dlc,通过电弧离子镀膜法(电弧电流120a、脉冲偏压-150v)用39分钟形成膜厚0.45μm的高硬度dlc,以2层合计膜厚0.495μm的形式叠层11次,形成膜厚5.45μm的硬质碳被膜。(比较例2)通过电弧离子镀膜法(电弧电流90a、脉冲偏压-200v)用90分钟形成膜厚1.0μm的硬质碳被膜。(比较例3)在第1成膜工序(电弧电流120a、脉冲偏压-1200v)中,用34分钟形成0.5μm的膜厚,在第2成膜工序(电弧电流150a、脉冲偏压-1200v)中,用358分钟形成5.1μm的膜厚,作为整体形成膜厚5.6μm的硬质碳被膜。(比较例4)在第1成膜工序(电弧电流100a、脉冲偏压-200v)中,用16分钟形成0.2μm的膜厚,在第2成膜工序(电弧电流150a、脉冲偏压-200v)中,用386分钟形成5.5μm的膜厚,作为整体形成膜厚5.7μm的硬质碳被膜。(比较例5)在第1成膜工序(电弧电流100a、脉冲偏压-3000v)中,用16分钟形成0.2μm的膜厚,在第2成膜工序(电弧电流150a、脉冲偏压-3000v)中,用365分钟形成5.2μm的膜厚,作为整体形成膜厚5.4μm的硬质碳被膜。(比较例6)在第1成膜工序(电弧电流60a、脉冲偏压-3000v)中,用14分钟形成0.1μm的膜厚,在第2成膜工序(电弧电流100a、脉冲偏压-3000v)中,用526分钟形成5.0μm的膜厚,作为整体形成膜厚5.1μm的硬质碳被膜。(比较例7)在第1成膜工序(电弧电流60a、脉冲偏压-300v)中,用14分钟形成0.1μm的膜厚,在第2成膜工序(电弧电流100a、脉冲偏压-300v)中,用547分钟形成5.2μm的膜厚,作为整体形成膜厚5.3μm的硬质碳被膜。另外,在如下试验条件下进行。硬质碳被膜的氢含量设为0.3原子%,从活塞环切出20mm长度,用作滑动侧试验片(销型试验片)40。配合侧试验片41使用由jisg4805中规定为高碳铬轴承钢材的suj2钢制成且尺寸为φ24×7.9mm、硬度hrc62以上的配合侧试验片41(盘型试验片),如图5所示实施下述条件下的srv试验。试验装置:srv试验装置负载:100n、200n、300n频率:50hz试验温度:80℃滑动宽度:3mm润滑油:5w-30,125ml/hr试验时间:10分钟试验结果如表1所示,在比较例1中在负载为200n以上时观察到磨损,在比较例2中负载为300n上时观察到磨损,与此相反,在实施例1~7中,即使负载为300n,也没有确认到磨损,确认具有良好的耐磨性。另外,在表1中,“○”表示未确认到磨损。[表2]负载(n)比较例1比较例2实施例1实施例2实施例3实施例4实施例5实施例6实施例7100○○○○○○○○○200磨损○○○○○○○○300磨损磨损○○○○○○○[磨损试验]接着,使用上述实施例1~7及比较例1~7,实施磨损试验。磨损试验使用如图6所示的阿姆斯拉式磨损试验机50。使用的试样51将实施例1、2及比较例1、2作为7mm×8mm×5mm的固定片,配合材料52(旋转片)使用环形(外径40mm、内径16mm、厚度10mm)的旋转片,使试样51和配合材料52接触,施加负载p,通过以下的试验条件进行,测定固定片的磨损比率。试验装置:阿姆斯拉式磨损试验机润滑油:0w-20油温:80℃转速:1.0m/s负载:784n试验时间:7小时配合材料:硼铸铁试验结果如图7所示,与比较例1相比,可以确认实施例1及2磨损比率大幅度低至30%~40%,可以确认耐磨性非常良好。另外,也可以确认,与比较例1~7相比,实施例3~7的磨损比率低。[透射型电子显微镜观察试验]接着,使用上述的实施例1、2及比较例2,通过透射型电子显微镜(transmissionelectronmicroscope:tem)进行观察试验。首先,观察实施例1及2的被膜截面tem像。被膜截面tem像的观察通过在弱焦条件下的浓淡比较来进行。其结果如图8(a)所示,可以确认实施例1的截面状态构成对比度差较小的均质被膜。这样,实施例1由均质的被膜构成,因此可以确认被膜的耐磨性优异。另外,如图8(b)所示,对于形成于实施例2的最表面的表层纳米叠层部,观察到对比度的状态为条纹状。一般认为,亮的对比度的部分是电子线透射多的低密度的部分,暗的对比度的部分是电子线透射少的高密度的部分。可以确认,这种对比度显现为条纹状,是由于以规定间隔反复多次实施脉冲偏压为-150v的高电压处理和脉冲偏压为-1800v的低电压处理而形成了表层纳米叠层部,通过该表层纳米叠层部提高了韧性及耐磨性。接着,观察实施例1及比较例2的表面状态。如图9(a)所示,可以确认,实施例1与图9(b)所示的比较例2的表面状态相比较,大颗粒的量大幅度降低。另外,图9(a)、(b)中暗的部分是可观察大颗粒的部位。对于该观察结果,通过计算暗的部分相对于整体的面积率,计算大颗粒的面积率。另外,关于计算方法,使用上述共焦点显微镜进行图像解析来计算。另外,sp2成分比通过上述的tem-eels的测定来计算。另外,基于din4776标准对实施例1~7及比较例1~7的表面粗糙度即初始磨损高度rpk进行测定。以下的表2是将这些大颗粒面积率、sp2成分比及初始磨损高度rpk的确认结果汇总在一起制成的表。[表3]这样,可以确认实施例1~7中,大颗粒面积率处于0.1%~10.0%的范围内,sp2成分比处于40%~80%的范围内。另外,可以确认,比较例1~3中,大颗粒面积率为13.2%以上,显示出超过10.0%的大的值,比较例2及4~7中,sp2成分比超过40%~80%的范围。另外,可以确认,实施例1~7的固定片磨损比与比较例1~7的固定片磨损比相比,显示低的值,大颗粒面积率处于0.1%~10.0%及sp2成分比处于40%~80%的范围内的硬质碳被膜具备高的耐磨性。另外,关于初始磨损高度rpk,可以确认,实施例1~7为0.2μm以下,通过与上述大颗粒面积率及sp2成分比的结构所实现的耐磨性发生协同作用,而具有更高的耐磨性。这样,根据透射型电子显微镜的确认结果可以确认,实施例1~7以及比较例1~7的结构的差异。另外,对本实施方式的硬质碳被膜12形成为膜厚为5μm以上的厚度的情况进行了说明,但膜厚不限于此,例如也可以形成为0.5以上且低于5μm。在这样形成为薄被膜的情况下,如图10所示,如果在基底层13和活塞环基材11之间形成由pvd被膜、镀cr被膜或氮化层的任一个构成的基材层14,则可以进一步提高硬质碳被膜12的密合性。以上,对说明的本实施方式的硬质碳被膜12仅在活塞环10的外周滑动面形成硬质碳被膜等的情况进行了说明,但也可以在活塞环基材的上面、下面以及内周面连续地形成硬质碳被膜12等。加以这样的变更或改良的方式也包含于本发明的技术范围,这一点从权利要求书的记载可以明确得知。当前第1页12