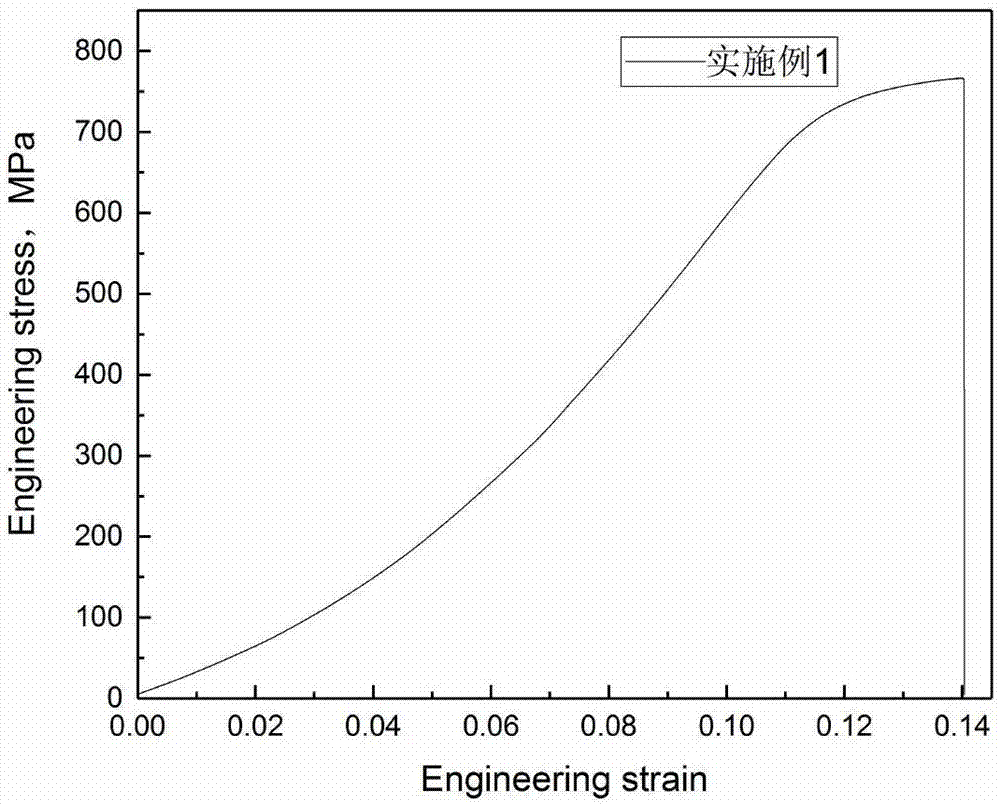
本发明涉及一种抗拉强度750mpa级fe-mn-al-c系轻质铸钢及其制备方法,属于金属材料类及冶金领域。
背景技术:
:世界钢铁制造商所开展ulsab-avc的项目完成,证明了钢铁仍然是今后汽车使用的主导材料。作为汽车节能减排、环保和降本降耗的主要途径之一,汽车轻量化已经成为未来汽车产业公认的发展方向。从世界范围内的能源危机爆发到现在,汽车轻量化材料在汽车中的比例已经翻倍。汽车轻量化新材料也成为人们关注的热点,预计未来市场规模高达数万亿元。钢铁材料在整个汽车用材料中所占的比例约为70%,是汽车最主要的材料,其中590mpa—1480mpa级先进高强度钢约占汽车用钢的49%。有学者指出,通过向钢中添加一定量的al、mn及c等轻量化元素,在合金成分优化、热处理及成型工艺控制的基础下,得到兼具低密度和高强韧的新型汽车用钢,将会在不牺牲汽车结构零件强度的前提下有效减轻汽车自身重量。有研究数据表明,汽车自重每减少10%,燃油消耗可降低6%至8%,可有效节约能源,对汽车降低排放,改善性能有着重要意义。随着汽车工业的迅猛发展,市场迫切需要大量高强度和低密度兼备的抗拉强度为750mpa级轻质钢来满足汽车轻量化的需要。在现有的技术中,cn106498307a公开了一种780mpa级冷加工性能良好的高强高韧轻质钢及其制备方法,该方法所制备的轻质钢所添加的c、mn、al等轻质元素较少,减重效果仅在5%左右,严重影响车身自重的轻量化效果。cn104928568a公开了一种铁素体低密度高强钢及其制造方法,该方法采用冶炼铸造、热轧、热轧后退火、酸洗、冷轧及连续退火一系列复杂工艺,其制造工艺复杂,成本昂贵,不利于轻质钢的普遍使用。cn104674109a公开了一种低密度fe-mn-al-c系冷轧汽车用钢板及制备方法,该方法需要经过锻造、热轧和冷轧等工艺来提高钢板的力学性能,不适用于形状复杂或具有复杂内腔只能通过铸造成型的汽车零部件。cn106521318a公开了一种高强度fe-mn-al-c系低密度铸钢及其制备方法,其mn、si含量较高,具有很高的抗拉强度,有很好的强度和密度的配合,但其塑性较差,易出现脆性断裂,受其塑性较差的影响,其使用范围受到影响,不适用于密度减小、强度较高和塑性较好同时要求的零件。因此,迫切需要一种制备简单、成本低廉且具有超高强度的轻质钢制备工艺。技术实现要素:本发明的目的就是针对上述已有技术存在的缺点,提供一种750mpa级的高强韧轻质铸钢及其制备方法。本发明的轻质钢通过较高的c含量(0.60~1.50%)与合理的si含量(0.50~1.50%)的成分设置,其抗拉强度≥750mpa,屈服强度≥700mpa,密度≤7.0g/cm3,断后伸长率≥15%,具有非常好的强度、密度和塑性的配合,非常适用于制造汽车复杂结构铸件并且可以有效减轻汽车自重。本发明采用真空感应电炉熔炼,整个过程发生在真空环境下,有利于金属内部气体杂质的祛除并且在电磁力的搅拌下可以使成分更加均匀。真空感应熔炼较传统冶炼相比更加节能环保,人工作业环境好,劳动强度小,操作更加简单方便,符合我国节能环保的发展战略。本发明的技术方案是:一种750mpa级超高强度fe-mn-al-c系轻质铸钢,其化学成分重量百分数为:c:0.60~1.50%,mn:10.00~14.00%,al:6.50~12.00%,si:0.50~1.50%,ni:0.15~0.55%,cr:0.15~0.45%,cu:0.01~0.06%,mo:0.10~0.60%,v:0.05~0.25%,ti:0.05~0.35%,nb:0.01~0.08%,ce:0.001~0.010%,p≤0.008%,s≤0.008%,其余为fe和不可避免的杂质;同时,mn与al的重量百分比满足于18%≤mn+al≤22%;nb、v和ti的重量百分比满足于0.25%≤nb+v+ti≤0.50%。所述的ce的质量百分比含量优选为0.005~0.010%。所述的c的质量百分比含量优选为0.6~0.8%。所述的750mpa级超高强度fe-mn-al-c系轻质铸钢的制备方法,包括如下步骤:1)配料:以高纯铁、电解锰、金属铬、工业硅、镍板、海绵钛、钼铁、钒铁、铌铁、铝粒、增碳剂、铜板、ce稀土为原料,按照目标成分的配比进行配料并称重;2)造型;3)熔炼:向真空感应熔炼炉内加入高纯铁,抽真空至5~10pa,然后升温至1480~1500℃冶炼,待高纯铁完全熔清后冲入氩气19000~20000pa,然后再加入电解锰、金属铬、工业硅、镍板、海绵钛、钼铁、钒铁、铌铁、铝粒、增碳剂和铜板,当物料全部熔清后再精炼10~15分钟,精炼温度为1500~1510℃;精炼结束后,在浇注前向合金溶液中加入称量好的ce稀土并搅拌;4)浇注:提高功率将温度升到1530~1550℃后出钢;将合金溶液浇注到砂型中,空冷放置至室温后获得轻质钢铸件;5)热处理:铸件的热处理在箱式热处理炉内进行,首先进行固溶处理,固溶温度为900~1100℃,保温0.5~3小时,水冷至室温;然后在4小时内进行时效处理,时效温度为350~600℃,保温30min~15小时,空冷至室温;最后得到超高强度fe-mn-al-c系低密度铸钢。所述的增碳剂具体为天然石墨、人造石墨、焦炭或无烟煤。上述一种750mpa级超高强度fe-mn-al-c系轻质铸钢,所用的原材料和设备均通过公知的途径获得,所用的操作工艺是本
技术领域:
的技术人员所掌握的。本发明的有益效果为:根据国际上对超轻汽车用钢的研究,将抗拉强度小于270mpa的钢板称为低强度钢板,抗拉强度在270-700mpa为高强度钢板,而抗拉强度在700mpa以上的为超高强度汽车钢板。fe-mn-al-c系轻质钢是在超低碳钢或c-mn钢的基础上添加al、si等轻质元素形成的,本发明通过对c、mn、al、si轻质元素及nb、v、ti等强碳化物生成元素的含量及后续的热处理工艺参数进行合理优化设计,保证了轻质铸钢在不经锻造、轧制的条件下就拥有良好的力学性能,可在需要减轻自身重量且形状复杂只能通过铸造方式生产的汽车零部件上使用。具体体现在:(1)本发明生产工艺简单,无需锻造、轧制即可得到高强韧的性能,熔炼所需中间合金来源广泛,降低了低密度超高强度钢的生产成本。因此,本发明所开发的超高强度fe-mn-al-c系低密度铸钢及其制备方法具有很好的推广应用前景。(2)本发明的超高强度fe-mn-al-c系低密度铸钢的抗拉强度>750mpa,屈服强度大于700mpa,断后延伸率>10%,密度<7.0g/cm3,具有良好的强韧性和低密度的配合,达到了超高强度汽车用低密度钢板的力学性能范围,具有非常好的力学性能。(3)本发明的超高强度fe-mn-al-c系低密度铸钢采用真空感应炉熔炼,在实际生产中的应用性很强,现有的钢铁熔炼及热处理设备都可以对其进行加工,无需额外的改进,对生产设备的要求较低且生产效率高、节约能源,有利于环境的保护。(4)本发明的超高强度fe-mn-al-c系低密度铸钢可应用在汽车、航空航天、建筑等重要领域,具有良好的应用前景,并且符合国家节能减排的发展战略。(5)本发明的超高强度fe-mn-al-c系低密度铸钢为奥氏体与铁素体双相组织,并且含有少量碳化物。碳化物的析出可钉扎晶界,阻碍位错的滑动,提高变形抗力,使其具有较高的强度。mo、v和al的加入细化了奥氏体晶粒,通过细化晶粒可使钢具有良好的塑性;ce元素的加入可提高钢的韧性,疲劳极限,降低冷脆转变温度。(6)本发明的超高强度fe-mn-al-c系低密度铸钢具有良好的抗腐蚀性能,使其能够更广泛使用。附图说明下面结合附图和实施例对本发明进一步说明。图1为本发明热处理工艺曲线示意图;图2为本发明实施例1时效处理后的超高强度fe-mn-al-c系低密度铸钢的典型显微组织200倍金相照片;图3为本发明实施例1典型拉伸曲线。具体实施方式下面用具体实施方式对本发明(的技术方案)做进一步说明,以下实施例均在本发明技术方案为前提下进行实施,给出了详细的实施方案和具体的操作过程,但本发明的保护范围不限于下述的实施例。选取三种合金成分c:0.8%、mn:12%、si:0.7%、ni:0.2%、cr:0.3%、cu:0.05%、mo:0.3%、v:0.1%、ti:0.2%、al:9%、ce:0.008%、nb:0.05%(wt%)(合金1);c:0.6%、mn:10%、si:0.5%、ni:0.15%、cr:0.3%、cu:0.05%、mo:0.3%、v:0.1%、ti:0.2%、al:9%、ce:0.008%、nb:0.05%(wt%)(合金2);c:0.65%、mn:11%、si:0.7%、ni:0.2%、cr:0.3%、cu:0.05%、mo:0.4%、v:0.1%、ti:0.2%、al:8%、ce:0.01%、nb:0.05%(wt%)(合金3)作为典型例子。按照本发明的技术方案,以高纯铁、电解锰、金属铬、工业硅、镍板、海绵钛、钼铁、钒铁、铌铁、铝粒、增碳剂、铜板、ce稀土中间合金为原料,各中间合金材质单如表一所示,经熔炼制成轻质钢铸锭,经过热处理,加工成所需的合金并对所得合金微观组织和力学性能进行检测分析。实施例1前期准备:清洗坩埚,检查水、电、气、油及设备是否正常。第一步,配料按目标成分c:0.8%、mn:12%、si:0.7%、ni:0.2%、cr:0.3%、cu:0.05%、mo:0.3%、v:0.1%、ti:0.2%、al:9%、ce:0.008%、nb:0.05%(wt%)(合金1)的质量百分比计算各物料的质量(高纯铁15.7kg、电解锰2.53kg、金属铬109g、工业硅205g、镍板40g、海绵钛80g、钼铁108.9g、钒铁42.7g、铌铁16.1g、铝粒2kg、增碳剂(人造石墨)160g、铜板11.4g、ce稀土3.2g)(说明,在实际生产中,由于熔炼中有烧损或测量仪器的误差,最终的成分很难做到都和目标成分完全一致,在一定范围内即可接受。其中间合金的加入量还要按照表1各元素熔炼收得率计算。此为本领域技术人员公知手段。)。高纯铁、硅铁等大块炉料采用100kg电子称称量,增碳剂、铌铁、钒铁、钛铁、稀土等量少的炉料采用200g电子称称量,各炉料称量前用砂轮打磨,去掉其表面氧化皮,每炉配料20kg。表1表2:配料材质单。表2第二步:造型本实施例造型采用的是水玻璃砂,砂型配比如表3所示。造型前,将砂子先干混再湿混,在混砂的过程中控制好水玻璃的加入量,在保证砂型强度的情况下,防止造成不必要的浪费。然后用于造型,待造好型后,在型上扎几个均匀的气孔,用吹二氧化碳的方式将其砂型硬化。待砂型完全硬化后,取出模具,最后涂刷耐火材料,等待浇注。造型材料配比(wt%)性能参数石英砂(新砂)93.540—70目水玻璃6.5模数m=2.1—2.6表3第三步:熔炼首先向真空感应熔炼炉中加入所需高纯铁15.7kg,然后检查真空炉的气密性,抽真空,之后送电进入冶炼阶段,在整个过程中保持真空度在5pa,待高纯铁完全熔清后冲入氩气20000pa以防止下一阶段合金料的挥发损失,然后加料(预先称量好的电解锰2.53kg、金属铬109g、工业硅205g、镍板40g、海绵钛80g、钼铁108.9g、钒铁42.7g、铌铁16.1g、铝粒2kg、增碳剂160g、铜板11.4g)进入合金化阶段。合金全部熔清后进入精炼期,熔炼时间为10分钟。精炼期结束后,在浇注前向合金液加入ce稀土3.2g并搅拌均匀。第四步:浇注提高功率将温度升到1530℃后出钢;将合金溶液浇注到砂型中,空冷获得铸件;第五步:热处理铸件的热处理在热处理炉内进行,先进行固溶处理,待炉温升到1000℃稳定15min后将铸件放入,保温1小时后取出,迅速投入水槽中,慢慢搅动,使铸件能够快速冷却,水温为30℃。;然后在4小时内进行时效处理,时效温度为500℃,待炉温升到500℃稳定15min后放入,保温9小时,空冷至室温;得到组成如表4中实施例1所示的超高强度fe-mn-al-c系低密度铸钢。图3为本实施例得到的750mpa级超高强度fe-mn-al-c系低密度铸钢的典型组织的照片。如图3所示,铸钢的基体组织为均匀等轴奥氏体,含有少量的铁素体并且晶界及晶内析出有点状分布的碳化物。固溶处理水淬会使碳化物以细小的颗粒从过饱和的奥氏体基体中弥散析出,弥散分布的碳化物有助于提高奥氏体的强度。细小均匀的奥氏体基体组织,在形变时有助于防止裂纹的生成和扩展,增强了钢的塑性和韧性。实施例2按目标成分c:0.6%、mn:10%、si:0.5%、ni:0.15%、cr:0.3%、cu:0.05%、mo:0.3%、v:0.1%、ti:0.2%、al:9%、ce:0.008%、nb:0.05%(wt%)(合金2)的质量百分比计算各物料的质量(高纯铁15.2kg、电解锰2.11kg、金属铬109g、工业硅146g、镍板30g、海绵钛80g、钼铁108.9g、钒铁42.7g、铌铁16.1g、铝粒2kg、增碳剂120g、铜板11.4g、ce稀土3.2g)。配料、造型、熔炼、浇注方法如实施例一所示,不同之处为:铸件在1000℃固溶保温50min,水冷至室温,然后在500℃时效保温5h,空冷至室温。得到组成如表4中实施例2成分低密度铸钢。实施例3按目标成分c:0.65%、mn:11%、si:0.7%、ni:0.2%、cr:0.3%、cu:0.05%、mo:0.4%、v:0.1%、ti:0.2%、al:8%、ce:0.01%、nb:0.05%(wt%)(合金3)的质量百分比计算各物料的质量(高纯铁15.1kg、电解锰2.32kg、金属铬109g、工业硅205g、镍板40g、海绵钛80g、钼铁143.4g、钒铁42.7g、铌铁16.1g、铝粒1.8kg、增碳剂130g、铜板11.4g、ce稀土3.2g)。配料、造型、熔炼、浇注方法如实施例一所示,不同之处为:铸件在900℃固溶保温50min,水冷至室温,然后在450℃时效保温8h,空冷至室温。得到组成如表4中实施例3成分低密度铸钢。表4为实施例1、实施例2和实施例3低密度钢最终熔炼所得的合金成分,其各元素含量用arl4460火花直读光谱仪测得。表4通过万能拉伸试验机参考gb/t228.1-2010国家标准做成直径为5mm的拉伸试棒,测定各实施例试样的力学性能;利用洛氏硬度计参考gb/t230.2-2012国家标准测定各实施例试样的硬度;利用精密天平测定各实施例试样的密度。其硬度、抗拉强度、屈服强度、密度如表5所示。表5从表5可以看出,本发明研发的fe-mn-al-c系低密度钢密度最低可降低到6.84g/cm3,相比一般铸钢密度降低了12.3%,且抗拉强度达到768mpa,屈服强度15.03mpa,断后伸长率达15.03%,具有较好的强度、塑性和密度的匹配。本发明未尽事宜为公知技术。当前第1页12