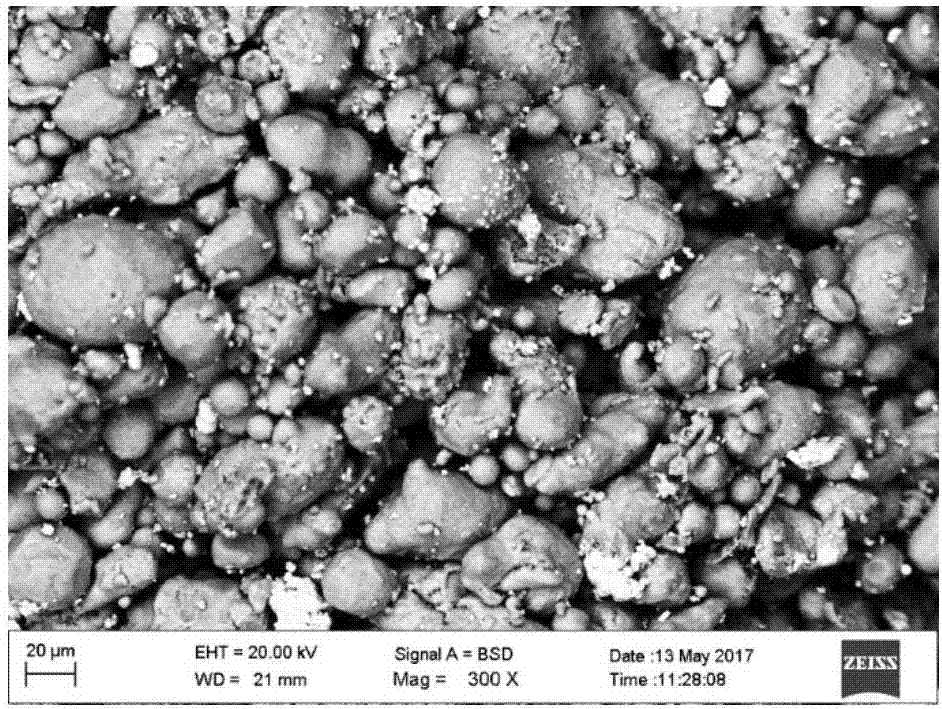
本发明提供一种利用粉末注射成形技术制备高性能铝合金的方法,属于粉末冶金领域。
背景技术:
:铝合金密度低、比强度高、塑性好、具有优良的导电性、导热性和抗蚀性,广泛应用于航空航天、电力电子、建筑等工业领域。近年来,航空航天、汽车、可穿戴电子设备等领域对高性能小型复杂形状的铝合金结构件的需求逐渐增加。然而,采用机械加工工艺制备小型复杂零部件材料利用率低、加工成本高,不适合批量生产。而铸造工艺的成形复杂形状的能力、精度均不能满足实际需求,且由于铸造组织不均匀会影响产品表面状态和表面处理工艺。采用快速冷凝-粉末冶金工艺可以制备高强度、高刚度的铝合金材料,其室温拉伸强度可以超过800mpa[guojq,kazamans.mechanicalpropertiesofrapidlysolidifiedal-ti-fe,al-cu-feandal-fe-cu-tibasedalloysextrudedfromtheiratomizedpowders.materialsscienceandengineeringa,1997,232(1-2):177-182],但这种工艺不能直接制备出近终形的产品,工艺成本高,目前只限应用于航空航天等高端领域。传统粉末冶金压制-烧结工艺可以大批量生产近终形零件,schaffer等人[maq,schaffergb.sinteringofaluminiumanditsalloys.sinteringofadvancedmaterials,2010,291-323;lumleyrn,sercombetb,schaffergb.surfaceoxideandtheroleofmagnesiumduringthesinteringofaluminum.metallurgicalandmaterialstransactionsa,1999,30(2):457-463;sercombetb,schaffergb.ontheroleofmagnesiumandnitrogenintheinfiltrationofaluminiumbyaluminiumforrapidprototypingapplications.actamaterialia,2004,52(10):3019-3025]基于液相烧结原理,在烧结过程中实现了铝粉表面氧化膜的破除及烧结致密化,其烧结密度可以达到98%,使粉末冶金铝合金制品在汽车、家电和电子设备中获得了广泛应用。但传统的粉末冶金法由于受模具的限制在制备复杂形状零件方面会有较大局限性,这限制了粉末冶金铝合金零部件更广泛的应用。martin和schaffer等人[martinjh,yahatabd,hundleyjm,mayerja,schaedlerta,pollocktm.3dprintingofhigh-strengthaluminiumalloys.nature,2017,549(7672):365-369.sercombetb,schaffergb.rapidmanufacturingofaluminumcomponents.science,2003,301(5637):1225-1227.]曾在nature和science上发表了他们采用3d打印技术制备复杂形状的铝合金零件的研究结果,该方法在制备单个或小批量复杂形状产品方面具有优势,但不适合大批量产品的生产。因此,传统的制备和加工方法在制备高性能复杂形状的铝合金零部件方面都存在一定的局限性,急需开发一种低成本大批量制备高性能复杂形状铝合金零部件的制备技术。粉末注射成形(powerinjectionmolding,简称pim)是将现代塑料注射成形技术引入粉末冶金领域而形成的一门新型近净形制造技术[25],其工艺流程为:首先将金属或陶瓷粉末与有机粘结剂均匀混合并制成粒状原料,在加热状态下用注射成形机将其注入模腔内固化成形,然后用化学或热分解的方法将成形坯中的粘结剂脱除,最后经烧结致密化得到最终产品。该技术在批量制备小型复杂金属零部件方面有独特的优势,因而被誉为“当今最热门的零部件成形技术”和“21世纪的金属零部件制造技术”,近年来在铁基合金、不锈钢、钨基高比重合金等材料体系中获得了广泛应用[26-30]。然而,将粉末注射成形技术应用于铝合金零件制备还面临三个方面的主要问题。第一,与传统的压制成形相比,注射成形过程中,金属粉末不发生塑性变形,粉末间的摩擦剪切也很少,因此,其表面氧化膜更加完整,更不利于烧结致密化;第二,由于注射成形坯体中有机粘结剂约占30-40vol.%,脱除粘结剂后,注射成形坯体内部的孔隙率要远大于压制坯体,颗粒间接触少,原子扩散更为困难。第三,金属铝粉活性高,容易吸潮团聚,不利于制备均匀的喂料,且还会与有机粘结剂中的氧基和水气反应,进一步增加粉末表面的氧化膜厚度,进一步增加了铝合金粉末烧结致密化的难度。粉末冶金材料的性能一般取决于其烧结的致密度,当粉末冶金铝合金的致密度达到98%以上时,其性能接近于铸态材料的性能。目前,仅有极少数文献和专利报道了铝合金的注射成形的研究。tan等人将纯铝粉与碳化硅或金属氟化物混合,与氧化铝膜形成共晶相破除氧化膜,脱脂后在真空中烧结,但其致密度低于93%,抗拉强约100mpa[tanlk,maj.advancesinpowdermetallurgyandparticualtematerials.2003,8:282–288.lasvegas,nv,mpif.]。katou等使用纯al粉在650℃的真空环境烧结2h,发现致密度和力学性能与铝粉粒径有关,粒径最小的3μm烧结后致密度可达到96%,抗拉强度和延伸率分别为120mpa和19%[katouk,mstsumotoa.appicationofmetalinjectionmouldingofalpowder[j].journalofthejapansocietyofpowderandpowdermetallurgy.2016,63(7):468-471.]。acar等人也使用d50为7.35μm的纯铝粉,没有添加任何合金元素,在接近熔点的温度下烧结,但其致密度很低,微观组织中尚存在较多孔洞[acarl,gulsoyho.sinteringparametersandmechanicalpropertiesofinjectionmouldedaluminiumpowder[j].powdermetallurgy.2011,54(3):427-431.]。liu等人在预合金粉aa6061(al+0.95mg+0.65si+0.27cu)的基础上添加了2%的sn以促进烧结,在n2烧结气氛下,获得了致密度98%的烧结坯,人工时效后抗拉强度为300mpa[liuzy,sercombetb,schaffergb.metalinjectionmouldingofaluminiumalloy6061withtin[j].powdermetallurgy.2008,51(1):78-83.],但该研究所采用的原料粉末为合金粉末,价格比较昂贵。综上所述,目前关于铝合金注射成形的研究主要存在以下问题:若采用纯铝粉为主要原料,致密度均低于96%,力学性能较差,无法满足结构材料的性能要求;而采用预合金粉为主要原料的铝合金,虽然其致密度能达到98%以上,但原料粉末造价高昂,成分较高。技术实现要素:本发明提供一种利用粉末注射成形技术制备高性能铝合金的方法。以纯铝粉为主要原料,通过控制合金元素含量、粘结剂体系优化、微量合金元素的添加、烧结制度的优化等手段,提高注射成形铝合金致密化烧结,实现高性能复杂形状铝合金零部件的低成本大批量制备。一种利用粉末注射成形技术制备高性能铝合金的方法,其特征在于:以al-cu-mg-si合金体系为基础,含有少量合金元素sn;原料粉末采用纯al粉、cu粉、sn粉、al-50mg和al-12si粉末;将特定组成的原料粉末与蜡基粘结剂置于辊式混炼机上进行混炼获得喂料,通过注射成形技术制备得到生坯,经过溶剂脱脂,在高纯氮气气氛下进行热脱脂-烧结一体化步骤,得到高致密度的注射成形铝合金制品。具体工艺步骤为:(1)所述的用于注射成形的铝合金为al-cu-mg-si体系,含有少量的合金元素sn。采用的原料粉末为:al(10-40μm)、cu(<5μm)、sn(<5μm)单质粉和al-50mg(<5μm)、al-12si(<5μm)二元合金粉;(2)所述的注射成形用铝合金中各合金元素的质量百分含量为:cu3-6%,mg1-3%,si0.2-2.0%,sn0.1-2.0%,al为余量。上述成分的优先范围为:cu3.5-5.0%,mg1.0-2.0%,si0.4-1.2%,sn0.1-1.2%;al为余量;(3)所述的注射成形用铝合金的粘结剂各组元的质量百分含量为:石蜡(20-30%),蜂蜡(20-30%),聚乙烯蜡(20-30%),低密度聚乙烯(10-30%),硬脂酸(3-10%);(4)所述的注射成形用铝合金喂料的装载量为55-65%,即喂料中铝合金粉末的占总质量的55-65%。混炼的参数为:混炼温度170℃,混炼时间为1.5-2h。(5)所述的注射成形用铝合金的注射参数为:注射温度为150-170℃,注射压力80-100mpa,模具温度40-60℃。(6)所述的注射成形用铝合金生坯的脱脂工艺分为溶剂脱脂和热脱脂两个步骤,其中溶剂脱脂的溶剂为三氯乙烯,温度30-60℃,脱脂时间为6-18h。(7)所述的注射成形用铝合金热脱脂与烧结过程采用一步法完成,具体工艺参数为:以2℃/min升温至180-220℃,保温20-30min,接着以1℃/min升温至280-320℃,保温60-180min;再以1℃/min升温至450-480℃,保温60-180min,以2-5℃/min升温至540-570℃,保温30-90min,以2-5℃/min升温至590-610℃,保温30-120min,然后随炉冷却。热脱脂过程与烧结过程均采用高纯氮气保护,氮气速率为1.0-3.0l/min。(8)所述的注射成形用铝合金的固溶处理参数为:以1-5℃/min速率升温至500-530℃,保温60-240min,水淬。(9)所述的注射成形用铝合金的时效处理参数为:以1-5℃/min速率升温至150-250℃,时效时间2-24h。采用本发明所述方法制备的铝合金材料微观组织均匀,致密度大于98%,抗拉强度大于300mpa,可实现高性能复杂形状铝合金零部件的低成本大批量制备。本发明和现有技术相比所具有的有益效果在于:1.注射成形方法具有生产效率高,材料利用率高,成分分布均匀,不需后续加工等特点,在批量制备小型复杂形状铝合金零部件方面具有独特优势。2.所述的一种利用粉末注射成形技术制备高性能铝合金的方法,采用纯铝粉为主要原料,其他合金元素通过超细cu粉、sn粉、al-50mg和al-12si的形式加入,所有原材料粉末。通过多种原料粉末引入合金元素,有利于根据不同的使用需求调整合金的具体成分。同时,这些原材料粉末均已工业化生产,成本比定制多元铝合金粉末会大幅下降。3.本发明所述的注射成形用al-cu-mg-si铝合金体系中的mg元素主要用于破除铝粉表面的氧化膜,使烧结过程中合金元素形成的液相容易在纯al颗粒间进行填充。铝粉表面氧化膜的含量与铝粉的比表面积直接相关,即取决于原料粉末中铝粉的粒度。本发明使用的al粉的粒径范围为10-40μm,mg元素的最佳含量为1.0-2.0wt.%。4.本发明所述的注射成形用al-cu-mg-si铝合金体系中cu和si元素是最主要的液相形成元素,用于液相辅助烧结过程中铝合金的致密化。si元素的另一个作用是降低al-cu液相与基体的润湿角,使液相更容易填充孔隙。5.本发明所述的注射成形用al-cu-mg-si铝合金体系中会加入微量合金元素sn,sn元素主要有两个方面的作用,首先是降低液相的表面张力,使合金液相更容易填充孔隙。其次是sn与al的空位结合能要高于cu和si元素,因此sn更容易首先与al基体中的空位结合,这就抑制了cu和si元素向al基体中扩散,使合金中的液相能长时间的维持并持续填充孔隙。但当sn含量升高时,会对铝合金性能产生不利影响,首先sn由于表面张力低,在坯体热脱脂的过程中容易随粘结剂的挥发溢出坯体的表面;其次,sn元素在al基体中的固溶度很小,因此多余的sn元素在烧结后均位于晶粒边界上,无法通过固溶处理消除,因此影响铝合金的性能。6.本发明所述的注射成形用铝合金的粘结剂各主要含有石蜡、蜂蜡、聚乙烯蜡、低密度聚乙烯和硬脂酸等。由于铝合金中al-mg、al-cu和al-si的共晶温度较低,分别为460℃、550℃和579℃,因此需要在铝合金液相出现前将粘结剂脱除干净,因此本发明选用石蜡、蜂蜡、聚乙烯蜡和低密度聚乙烯等几种具有较低挥发温度的粘结剂。此外,这几种粘结剂具有不同的挥发温度,在脱脂过程中可形成脱脂温度梯度,有利于铝合金的坯体在脱脂过程中保持形状。硬脂酸主要起到润滑剂的作用。7.本发明中铝合金的烧结致密化过程材料阶梯烧结的方式进行,即分别在450-470℃、550-570℃、590-610℃三个温度区间内保温一定时间,而传统铝合金的烧结一般采用直接升温至最高烧结温度保温的方式。上述三个温度区间分别对应al-mg、al-cu和al-si共晶液相的生成温度,在这几个温度区间进行保温,有利于合金中液相的充分生成,促进烧结体的致密化。附图说明附图1所采用的纯al粉的形貌;附图2注射成形铝合金生坯的微观形貌;附图3注射成形铝合金烧结后的微观组织形貌;附图4注射成形铝合金经过固溶和时效处理后的微观形貌;附图5注射成形铝合金零件宏观照片。具体实施方式实施例1:注射成形铝合金体系的成分优化(a)配料:将所设计的各元素按照质量百分比(见表1)配好后在混料机上干混2h制得预混合粉;粘结剂采用蜡基粘结剂,各组元按质量百分比石蜡:蜂蜡:聚乙烯蜡:低密度聚乙烯:硬脂酸=24:24:24:24:4称量,粉末和粘结剂的计量精度为0.1g。(b)喂料制备:将混合均匀得混合粉与配制好的粘结剂按62%的装载量称量,按步骤置于cf-1l型强力加压式密炼机中进行混炼,混炼温度为170℃,转速为30r/min,经1.5-2h混合物形成熔融态,充分混匀后,取出冷却。(c)注射成形:将喂料破碎后,倒入cj80-e型注射机料筒中,进行注射操作,得到所需形状的铝合金注射坯。注射温度为160℃,注射压力90mpa,模具温度50℃。(d)脱脂-烧结:溶剂脱脂采用三氯乙烯,溶脱温度30-60℃,溶脱时长6-18h;,热脱脂气氛采用普通氮气,热脱脂升温制度为以2℃/min升温至200℃,保温20-30min,接着以1℃/min升温至300℃,保温60-180min;再以1℃/min升温至480℃,保温60-180min,至此脱脂完毕。接着采用高纯氮气作为烧结气氛,以2-5℃/min升温至560℃,保温30-90min,02-5℃/min升温至600℃,保温30-120min。表1不同成分铝合金的烧结致密度编号alal-mgcual-sisn致密度1余量130.20.286.8%2余量13.80.80.694.3%3余量14.61.41.295.6%4余量15.42.01.894.7%5余量1.530.81.290.8%6余量1.53.80.21.891.5%7余量1.54.62.00.298.9%8余量1.55.41.40.696.4%9余量231.41.895.4%10余量23.82.01.298.5%11余量24.60.20.693.5%12余量25.40.80.298.1%13余量2.532.00.693.5%14余量2.53.81.40.298.4%15余量2.54.60.81.896.3%16余量2.55.40.21.291.2%经过对比上述步骤得到的多组样品发现,当合金元素含量较少时,即分布于晶界的液相量不足,由于不能有效填充铝颗粒之间的缝隙,最终合金致密度普遍不高;但当合金元素含量过多,将产生大量的液相,过多的液相呈网状结构分布在铝颗粒周围,而液相大都由硬脆相组成,严重割裂基体之间的结合,导致材料致密度严重下降。而当合金元素含量范围适中,且各元素都在其功能范围之内时,材料致密度都能在98%以上,如sn元素,当其他元素含量适中,sn在0.2-1.2wt.%范围内,由于可以优先与基体铝中的空位结合,使晶界的液相保持更久的时间以充分填充孔隙,但大于此范围时,晶界液相大幅度增加,对材料尺寸精度带来不可控影响;而对于si,含量较少时,在其发挥促进al-cu与基体润湿性的作用上大打折扣,其致密度也很难提高;此外,当cu含量较高时,由于已经产生大量的液相,若其与基体的润湿性没有得到很好的改善,也将带来致密度的降低。当合金元素含量在合理范围时,材料微观组织致密均匀(如图3所示),致密度大于98%,抗拉强度大于300mpa。实施例2:注射成形铝合金粘结剂体系的成分优化(a)配料:将al-mg-cu-si-sn各元素按照质量百分比91.7:1.5:4.6:2.0:0.2配好后在混料机上干混2h制得预混合粉;粘结剂采用蜡基粘结剂,各组元按质量百分比按表2称量,粉末和粘结剂的计量精度为0.1g。(b)喂料制备:将混合均匀得混合粉与配制好的粘结剂按62%的装载量称量,按步骤置于cf-1l型强力加压式密炼机中进行混炼,混炼温度为170℃,转速为30r/min,经1.5-2h混合物形成熔融态,充分混匀后,取出冷却。(c)注射成形:将喂料破碎后,倒入cj80-e型注射机料筒中,进行注射操作,对比不同配比的粘结剂对注射过程的影响,以及注射生坯的完整性、光洁度和组织均匀性。注射温度为160℃,注射压力90mpa,模具温度50℃。表2不同成分的粘结剂体系对脱脂与烧结性能的影响经实验对比得出,适于注射成形铝合金的粘结剂范围为:石蜡(20-30%),蜂蜡(20-30%),聚乙烯蜡(20-30%),低密度聚乙烯(10-30%),硬脂酸(3-10%)。当前第1页12