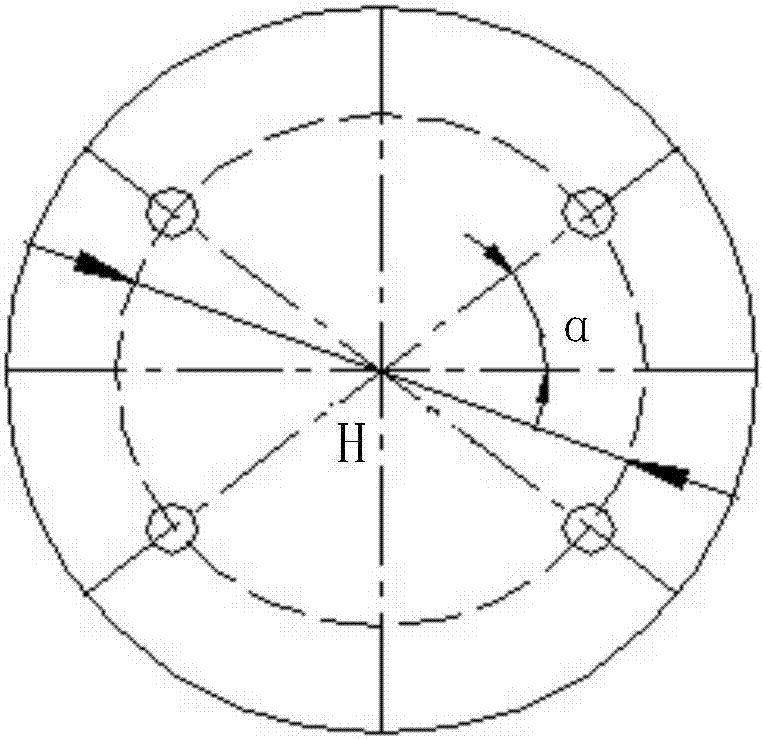
本发明属于钢冶金
技术领域:
,特别涉及一种转炉终渣气化脱磷处理后循环利用的方法。
背景技术:
:中国钢铁工业近20年来发展迅速,对国民经济快速增长发挥了重要作用,但在节省资源、能源和减少炉渣等固体废弃物排放等方面,目前面临着巨大的压力和挑战。以占中国产钢量90%以上氧气转炉炼钢为例,每年生产约6.2亿t粗钢,要产生6000万t以上炉渣,消耗3000万t以上石灰和700万t以上轻烧白云石,而用于生产炼钢石灰和轻烧白云石的石灰石与生白云石矿产均为重要的不可再生资源。目前应用或正在探索中转炉渣的综合利用或减少排放的方法有很多种,大致分为两类,一种是在炉渣从转炉排放为固体物以后再加以处理和利用,比较成熟的是回收金属铁,以后用于烧结矿添加剂、合成渣原料、磷肥或转炉渣水泥,即所谓“末端治理”,但是有效利用价值较低;另一种是炉渣在熔融状态,乃至在转炉内就加以循环利用,即所谓“源头治理”,这种方法是目前转炉渣的发展方向,符合无废或少废冶金的生态工业发展方向,比较成熟的有转炉溅渣护炉留渣操作等冶炼工艺。20世纪后期,深冲钢和高级别管线钢等钢种对磷含量要求苛刻,传统的单渣法炼钢脱磷率低,脱磷效果较差。90年代中期,日本各大钢厂进行了转炉铁水脱磷的试验研究,并在取得成功后迅速推广,解决了超低磷钢的生产难题。双联法是采用两座转炉联合作业,一座转炉脱磷,另一座转炉接受来自脱磷炉的低磷铁水脱碳,典型的双联法工艺流程为:高炉铁水→铁水预脱硫→转炉脱磷→转炉脱碳→二次精炼→连铸。日本转炉采用双联法脱磷炼钢工艺的主要有JFE福山制铁所的LD-NRP法、住友金属的SRP法、神户制钢的H炉法、新日铁的LD-ORP法,我国宝钢、鞍钢、首钢京唐公司等也都选用了双联法炼钢工艺。转炉双联法脱磷在大批量生产纯净钢时,转炉容量大,有充分的反应空间,反应动力学条件优越,铁水中磷可脱到0.010%以下,为少渣冶炼创造了条件;转炉双联法为生产超低磷钢、管线钢及优质宽厚板铸坯提供了有利的条件;双联法成本相对较低,转炉脱碳渣用于另一座转炉脱磷的双联法,生产1t铁水的钢铁料消耗比传统方法减少25kg,石灰消耗减少40%。但转炉双联法炼钢基建成本较高,需合理调度两座转炉设备,炉渣及钢水互相反倒,操作较复杂。新日铁室兰制铁所(两座270tLD-OB转炉)和大分制铁所(3座370t复吹转炉)受设备和产品的限制,采用了MURC技术,在同一转炉进行铁水脱磷预处理和脱碳吹炼,类似传统炼钢的双渣法。MURC工艺操作中将转炉冶炼分为两个阶段,在第1阶段主要进行脱硅、脱磷,结束后倒出部分炉渣,然后进行第2阶段吹炼,吹炼结束后出钢但将炉渣保持在炉内,下一炉在炉内留渣情况下装入废钢、铁水,然后进行第1和第2阶段吹炼,并以此循环往复。室兰制铁所和大分制铁所全部采用MURC工艺,前期脱磷渣一般倒出50%,脱碳渣直接留在炉内用于下一炉脱磷吹炼,MURC工艺冶炼周期约33~35min。2001年Ogawa等报道了新日铁开发的MURC转炉炼钢新工艺及其在8t转炉的试验情况。近年来,新日铁陆续报道了MUCR工艺相关情况,新日铁公司的大分、八幡、室兰、君津等钢厂采用了该工艺,产钢占新日铁总产钢量55%左右,转炉炼钢石灰消耗减少40%以上。20世纪50~70年代,中国一些转炉钢厂在铁水硅、磷质量分数高时,为了降低石灰消耗,减少吹炼过程喷溅,改善脱磷效果,曾采用出钢后留渣或“留渣+双渣”炼钢工艺。随着高炉生产水平的日益提高(铁水硅质量分数降低),高磷铁矿石用量减少(铁水磷质量分数降低),以及顾忌留渣造成铁水喷溅安全隐患,留渣炼钢工艺没有更大规模推广采用。近年来国内许多钢厂开始采用转炉留渣炼钢工艺,王新华等的发明专利201610012514.4“一种减少渣量的转炉炼钢方法”和201110340294.9“一种冶炼低磷钢的转炉冶炼工艺方法”,其关键技术是脱磷阶段通过采用低碱度(w(CaO)/w(SiO2):1.3~1.5)和低MgO质量分数(≤7.5%)渣系,形成流动性良好和适度泡沫化炉渣,解决了“留渣+双渣”炼钢工艺快速足量倒渣和渣中金属铁质量分数高这两大难题。针对转炉底吹搅拌弱的问题,在脱磷阶段采用低枪位和高强度供氧方法,利用顶吹氧气流加强金属熔池搅拌以促进脱磷,脱磷阶段结束时[P]平均降低至0.029%左右,脱碳阶段终点[P]降低至0.0096%左右,满足了绝大多数钢种对磷质量分数控制要求。经工业试验形成了SGRS工艺方法,首钢在其迁钢公司5座210t复吹转炉和首秦公司3座100t复吹转炉大规模采用此法,取得了炼钢石灰消耗减少47%以上,轻烧白云石消耗减少55%以上,渣量降低30%以上的效果。崔阳等的发明专利200910088141.2提出了“一种在溅渣护炉条件下顶底复吹转炉铁水脱磷的方法”,专利通过溅渣护炉操作有效利用前一炉次的炉渣和保护炉衬,同时提高脱磷效率。这些专利方法所基于的双渣法都需要在冶炼中期之前快速倒渣,提枪中断吹氧操作,与常规工艺相比,由于增加了炉渣固化和脱磷结束倒渣的时间,采用双渣+留渣工艺后转炉单炉生产周期比常规冶炼延长约4min,并且为了降低炉渣氧化性并固化炉渣,其溅渣护炉工艺中加入多种调质造渣料,如石灰、生白云石、轻烧白云石、镁碳球等。李建新等的发明专利200910077085.2提出了“一种使用脱磷剂的转炉冶炼工艺”,其技术方案指出利用前期低温和高氧化亚铁等良好的动力学条件,并使用含少量CaCl2的CaO基脱磷剂进行脱磷,后期重新造渣,脱碳渣做为下炉的脱磷渣使用。最近,赵东伟等的发明专利201610166145.8提出了“一种转炉高效脱磷的冶炼方法”,专利指出溅渣护炉后倒出残余炉渣,在转炉吹炼开始前,向炉内加入预熔渣,成分为CaO:70~85%,SiO2:15~30%,进行转炉吹炼操作。这些专利均优化了溅渣护炉后的炉渣,但存在的问题是未能充分对转炉渣进行改质并深入利用,磷富集问题限制了大量转炉渣在钢铁厂内部的循环利用。20世纪70年代末,日本的伊藤公久研究了Ca2SiO4-Ca3(PO4)2和CaO-SiO2-Fe2O3液相渣间磷的平衡分配比,结果表明转炉渣中的磷绝大部分富集在初晶相Ca2SiO4-Ca3(PO4)2中,以固溶体形态存在,很难去除。Morita等学者采用微波碳热还原对CaO-SiO2-FetO系合成渣、铁水脱磷预处理渣和含Cr的转炉不锈炉渣中Fe、P、Cr的回收进行了基础研究,验证了该方法脱磷的可行性并提出了进一步回收还原产物中P的方法。采用微波加热碳热还原转炉炉渣进行气化脱磷,是将炉渣中磷元素脱除的一条有效途径。关于经济有效地去除转炉炉渣中磷的方法,尤其是利用溅渣护炉过程中炉内气化脱除熔渣中磷的方法有很多报道,王书桓等的发明专利200610012514.4发明了一种“转炉溅渣护炉过程中气化脱除熔渣中磷的方法”,在溅渣护炉前,向熔池中加入适量脱磷剂,在溅渣过程中,高压氮气通过氧枪后产生巨大冲击力,将炉内熔渣击碎成颗粒飞溅起来挂于炉衬,此过程为固(焦炭)-气(氮气)-液(熔渣)之间的反应、以及熔渣内部的化学反应提供了良好的动力学条件,使熔渣中的磷得以通过化学反应进入气相脱除,气化脱磷剂分碳质脱磷剂和硅质脱磷剂两种,碳质更具有工业应用现实意义,经多年实验室基础实验和钢铁企业工业试验,气化脱磷率达到40%水平,留渣率80%以上,吨钢炉渣量平均为40~60kg/t,取得了良好的效果。王虎的发明专利201510561089.3发明了“一种用转炉煤气溅渣护炉作业的方法”,该工艺采用转炉煤气代替氮气进行转炉溅渣护炉作业,实现溅渣护炉作业时快速高效气化脱磷,降低炼钢成本。这些专利方法均能有效气化脱磷,但仍停留在转炉渣的处理上,未提出用于下炉冶炼的作用及影响,没有形成高效循环炼钢工艺。中国发明专利申请CN201710588339.1提出一种转炉气化脱磷渣循环脱磷炼钢的方法,该申请在一定程度上克服了上述
背景技术:
中提到的一些问题,但该申请关于气化脱磷的操作上给出的操作方法较为粗略,实践中存在脱磷剂损失过多或者操作不易控制等问题,仍有待进一步的改进。技术实现要素:为解决上述问题,本发明提供一种转炉炉渣留渣气化脱磷模式下循环利用冶炼方法,该方法对气化脱磷操作工艺进行了进一步改进,使得操作易控制,降低成本,且脱磷效果好。具体,为实现上述目的之一,本发明采用的技术方案如下:一种转炉炉渣留渣气化脱磷方法,所述方法包括如下步骤:转炉冶炼完毕并出钢后,倾倒出部分炉渣,转炉内留存一部分炉渣;根据剩余炉渣中FeO和P2O5的量计算确定还原剂用量;在顶吹氮气开始溅渣护炉前加入1/2的计算确定还原剂用量;溅渣护炉过程全程底吹氮气,转炉底部采用环缝式底吹供气元件,并控制氮气流量;剩余1/2计算确定还原剂用量在降枪吹氮开始后加入并在调渣阶段全部加完,并控制枪位,获得气化脱磷后的炉渣;所述气化脱磷后的炉渣保留在转炉中用于下一炉的冶炼。进一步,所述留存一部分炉渣的量为1/2-2/3全部渣量。进一步,其中的还原剂为焦炭粉。进一步,所述焦粉粒度要求在8mm~10mm之间,小于8mm焦粉粒度不大于5%。进一步,焦粉加入量由还原平衡反应获得,以全部还原渣中P205和FeO所需碳量的1.2倍的量为计算确定还原剂用量,具体计算公式为:其中:W(c):焦炭加入量,kg;W(渣):渣重量,kg;W(P2O5):P2O5百分含量,%;W(FeO):FeO百分含量,%;1.2:为碳当量倍数。进一步,转炉底部采用环缝式底吹供气元件为底吹供气元件由不锈钢无缝钢管组成;所述喷吹原件设置在炉底0.4~0.5D半径同心圆上,与耳轴连线成38°左右夹角。进一步,所述控制枪位为调渣枪位控制和溅渣枪位控制两阶段;调渣枪位控制高于基本吹炼枪位;溅渣枪位低于冶炼基本枪位。为实现上述目的之二,本发明采用的技术方案如下:一种转炉炉渣留渣气化脱磷模式下循环利用冶炼方法,所述方法包括如下步骤;在上一炉转炉炉渣留渣并按照上述方法气化脱磷方法操作完成后,在转炉中兑铁加废钢;进行冶炼,过程中加入新的造渣剂,所述新的造渣剂根据需求并考虑前一炉留渣量来确定;冶炼完毕后进行测温和取样,合格后进行出钢操作;出钢后倾倒出部分钢渣,按照上述方法进行气化脱磷操作从而实现循环利用冶炼。进一步,所述新的造渣剂包括石灰、白云石、矿石和铁皮球,且分批次加入,冶炼初期,头批入炉石灰量为1/2-2/3总石灰用量以及轻烧白云石、矿石和铁皮球,冶炼中期,加入第二批造渣料,石灰用量为1/3-1/2总石灰用量。本发明无需炉渣专门处理设备,借用溅渣护炉时良好动力学条件,向炉内加入还原剂还原炉渣,还原后的脱磷产物最终以磷蒸汽形式随炉气溢出炉内,工业生产较易实现。气化脱磷后炉渣循环利用于下一炉冶炼,可根本上实现钢渣在企业内部的循环,减少废物排放量,是实现节能减排的重要措施。本发明从动力学方面入手,改变还原剂溅渣前全部一次性加入方式。所用焦粉在顶吹氮气前加入约1/2总加入量,剩余部分在降枪吹氮开始后加入并在调渣阶段全部加完。通过此种加料方法增加焦粉与炉渣反应面积,强化气化脱磷效果。本发明所用焦粉粒度要求在8mm~10mm之间,小于8mm焦粉粒度不大于5%,较小粒度易于增加焦粉与炉渣反应面积,同时避免粒度过小被炉气带出炉内。热力学已证明在溅渣护炉气氛下采用焦粉还原P205可行,且大量循环炉气下优于FeO先还原。焦粉加入量由还原平衡反应获得,以全部还原渣中P205和FeO所需碳量为一倍碳当量。试验证明,实际焦炭加入量在约1.2倍碳当量时,可得到较高气化脱磷率。少量富余焦粉可作为下炉冶炼生热剂,不对下炉冶炼造成影响。本发明对溅渣护炉阶段枪位及下炉留渣操作后枪位进行优化控制。溅渣护炉过程中枪位控制分为调渣枪位控制和溅渣枪位控制两阶段。溅渣护炉前期,渣中(FeO)含量高,炉渣流动性好,前期加入焦粉,起到气化脱磷和调渣双重作用,合理调渣枪位既要提供炉渣与焦粉混合所需动能,又需避免炉渣飞溅造成的炉渣、焦粉混合不均,调渣枪位以高于基本吹炼枪位为宜,实际控制根据炉渣物性及渣量大小灵活控制。调渣阶段,炉渣流动性好,传质快,是气化脱磷的关键时期。溅渣枪位低于冶炼基本枪位,保证溅渣所需足够动能,但枪位也不能过低,避免动能消耗于炉渣内部及炉底冲刷,溅渣枪位通过观测炉口火焰及渣粒起跳情况灵活控制。采用上述操作方式优点及效益在于:在没有增加设备投资的前提下将冶金炉渣循环利用,是一种环保、高效的炉渣处理方式。气化脱磷炉渣循环使用,可降低石灰投入量,提高矿石、石灰石等冷却料用量,节约生产成本。同时所留炉渣渣系已经形成,有益于入炉石灰融化,对转炉脱磷有益。附图说明通过阅读下文优选实施方式的详细描述,各种其他的优点和益处对于本领域普通技术人员将变得清楚明了。附图仅用于示出优选实施方式的目的,而并不认为是对本发明的限制。而且在整个附图中,用相同的参考符号表示相同的部件。在附图中:图1是本发明转炉冶炼的工艺流程示意图;图2是本发明转炉炉底喷吹原件布置方式图;图3是具体实施方式中某企业65吨转炉留渣溅渣护炉枪位示意图;图4是具体实施方式某企业基于留渣模式下转炉冶炼枪位过程控制图。具体实施方式下面将参照附图更详细地描述本公开的示例性实施方式。虽然附图中显示了本公开的示例性实施方式,然而应当理解,可以以各种形式实现本公开而不应被这里阐述的实施方式所限制。相反,提供这些实施方式是为了能够更透彻地理解本公开,并且能够将本公开的范围完整的传达给本领域的技术人员。以某企业65吨转炉单渣留渣法操作为例,其冶炼操作工艺制度如下所示:1、该企业65吨转炉冶炼过程如图1所示。冶炼完毕拉碳时,通过控制摇炉角度恒定留渣量在4吨左右,避免留渣量过大影响下炉次冶炼,同时渣量稳定利于冶炼控制。出钢完毕后,摇正炉体,溅渣护炉前由高位料仓加入1/2总量焦粉,降枪吹氮进入溅渣护炉模式,开吹同时加入剩余焦粉,并在吹炼调渣阶段加入全部焦粉,该企业调渣时间控制在20-50s,调渣枪位根据渣量及渣中(FeO)含量不同灵活控制。溅渣护炉期间全程底吹氮气操作,如图2所示,转炉底部采用环缝式底吹供气元件为底吹供气元件由不锈钢无缝钢管组成;所述喷吹原件设置在炉底0.4~0.5D半径同心圆上,与耳轴连线成38°左右夹角。氮气流量控制在350Nm3/h。该企业冶炼终渣P2O5含量控制在2.5-3.2%之间,终渣FeO含量控制在15-25%之间,焦粉加入量以全部还原渣中FeO和P2O5所需焦粉量为基准碳当量,实际加入量以1.2倍碳当量为宜,焦粉加入量计算公式如式(1)所示,不同成分吨渣所需焦粉量如表1所示。其中:W(c):焦炭加入量,kg;W(渣):渣重量,kg;W(P2O5):P2O5百分含量,%;W(FeO):FeO百分含量,%;1.2:为碳当量倍数。表1不同炉渣成分下吨渣碳粉加入量2、该企业转炉溅渣护炉时间控制在1-3min,溅渣护炉期间枪位控制如图3所示。由图3可知,溅渣护炉枪位控制受渣中(FeO)含量影响较大,当渣中(FeO)含量约15%时,调渣枪位略高于吹炼基本枪位,同时观测炉口渣粒活跃度,待渣粒稀少,降枪至合适溅渣枪位;炉渣(FeO)含量约20%时,调渣枪位高于吹炼基本枪位400mm左右进行,待炉口火焰消失后降至基本枪位吹炼,同时观测炉口渣粒活跃度情况,合理调枪至溅渣枪位;炉渣(FeO)含量约25%时,调渣枪位在高于吹炼基本枪位800mm左右进行,此时时时观测炉口状况,控制顶吹氮气流量谨防溢渣,待炉口火焰消失后调枪至高于基本枪位400mm左右进行吹炼,炉口渣粒活跃度降低后合理调枪至溅渣枪位。3、溅渣护炉后炉渣全部留在炉内作为下炉初渣使用。留渣操作后,因前期渣渣系已经形成,利于前期脱磷,冶炼前期宜采用低枪位冶炼,且石灰加入时间延迟,石灰多批次加入,维持高磷容量渣系;冶炼中期防止返干;冶炼末期,控枪防回磷,冷却剂用量不宜过大,防止喷溅。留渣操作典型枪位控制模式如图4所示。实施例1-6某企业转炉在转炉炉渣气化脱磷模式下循环利用冶炼方法的具体工艺如下所述。冶炼钢种为低合金HRB400,单炉次铁水装入量铁水装入量62-66t,废钢装入量8-12t,石灰加入量2.2-2.8t,白云石加入量1.2-2.3t,石灰石用量0.5-1.5t,铁皮球用量0.3-1.1t,吹氧时间约15min,冶炼过程枪位1.2-2.7m,冶炼终点碳0.02-0.11%,平均0.05%,冶炼终点平均温度1665℃,终渣FeO含量15-25%,平均为19%,终渣P2O5含量2.5-2.9%,平均2.75%,终渣碱度平均2.5。留渣炉次焦粉量平均145kg/炉,留渣量平均4t,溅渣护炉枪位1.1-2.7m,炉渣脱磷率在36.12%~42.02%之间,平均值为39%。各实施例具体的工艺参数见表2。表2实施例1-6的工艺参数实施例上炉次石灰/kg终渣FeO/%终渣P2O5/%焦粉/kg1留渣220018.272.5791452留渣236020.612.7661403留渣226018.022.7381454留渣234015.452.6311505不留渣265020.522.86106不留渣268018.542.9110由表2可知,留渣炉次石灰加入量平均2290kg/炉,不留渣炉次石灰平均加入量2665kg/炉,留渣操作吨钢节约石灰量约5kg/t。大量实验数据证实,留渣操作可节约石灰300~500kg/炉,吨钢石灰消耗减少3.5-6kg,折合吨钢成本节省2~3元。循环利用后钢铁料消耗控制在1.05以下,较以往相比炉渣铁耗节约3.5-5.5kg/t钢,吨钢成本节约4~9元;焦粉消耗成本1-2元/t钢,综合考虑节约成本5-10元。同时,转炉炉渣冶金领域循环使用,是一种环保、直接、高效的炉渣处理方式。以上所述,仅为本发明较佳的具体实施方式,但本发明的保护范围并不局限于此,任何熟悉本
技术领域:
的技术人员在本发明揭露的技术范围内,可轻易想到的变化或替换,都应涵盖在本发明的保护范围之内。因此,本发明的保护范围应以所述权利要求的保护范围为准。当前第1页1 2 3