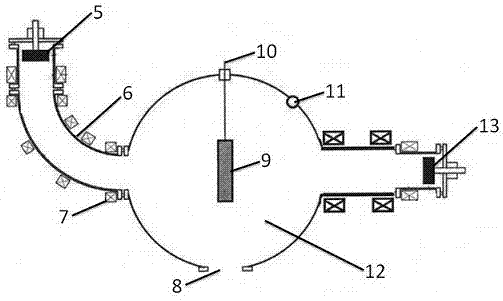
本发明涉及薄膜制备领域,具体涉及一种质量厚度为500-1000μg/cm2自支撑镓薄膜及其制备方法。
背景技术:
自支撑薄膜,相对于有衬底薄膜而言,是指在使用过程中无衬底支撑的薄膜。常用的自支撑薄膜制备技术是在固体抛光表面(如抛光硅片或玻璃片)涂覆或生长可溶性脱膜剂后,沉积薄膜,再将脱膜剂溶解。自支撑薄膜除要求能自支撑外,还要求具有无缺陷、均匀平坦、纯净、大面积、低应力等特性。中国专利cn106868460a,采用聚焦重离子溅射法制备了质量厚度为400~2000μg/cm2自支撑ir靶,解决了现有技术制备工艺出现靶膜卷曲、平整性极差的技术问题。然而,由于在溅射的过程中容易导致ir沉积层与铜基之间存在较大的残余应力,在溶解分立时释放应力会致使ir沉积层出现裂纹,影响自支撑靶的使用。另外,该发明制备步骤复杂,在沉积ir沉积层时,采用了两步,需要将ir沉积层取出聚焦重离子溅射沉积系统后再次放入沉积。技术实现要素:本发明的目的是根据现有技术所存在的缺陷,提供了一种质量厚度为500-1000μg/cm2、具有低应力、均匀且致密的自支撑镓薄膜的制备方法。为了解决现有技术所存在的问题,本发明提供的技术方案如下:一种质量厚度为500-1000μg/cm2自支撑镓薄膜的制备方法,包括以下步骤:(1)在衬底表面沉积氯化钾脱模剂;(2)采用90度磁过滤阴极真空弧(fcva)系统在衬底表面沉积氧化镁缓冲薄膜;(3)将样品旋转180°,采用直管磁过滤阴极真空弧(fcva)系统再次沉积镓薄膜;(4)将得到的衬底放入盛有乙醇溶液的容器中进行脱模处理;(5)用打捞板将镓薄膜捞起,得到质量厚度为500-1000μg/cm2自支撑镓薄膜。优选地,步骤(1)中所述衬底为玻璃或者单晶硅衬底。优选地,步骤(1)中采用电子束热蒸发法沉积氯化钾脱模剂,所述氯化钾脱模剂厚度180-280nm,优选为240-260nm。优选地,步骤(2)中采用氧化镁靶材作为90度fcva阴极,起弧电流为55-80a,弯管磁场1.0-3.0a,束流50-80ma,负偏压为-100~-200v,沉积时间为10-30min,占空比为40-80%。优选地,步骤(2)中所述氧化镁缓冲薄膜厚度为120-180nm,优选地,为140-160nm。优选地,步骤(3)中采用镓靶材作为直管fcva阴极,起弧电流为70-100a,弯管磁场2.0-5.0a,束流50-120ma,负偏压为-150~-350v,沉积时间为60-120min,占空比为50-90%。优选地,步骤(3)中所述镓薄膜厚度为10-40μm,优选地,为20-30μm。优选地,步骤(4)中所述乙醇溶液含水质量为5%-8%。本发明的目的之二,在于提供一种所述制备方法制备得到的质量厚度为500-1000μg/cm2自支撑镓薄膜。本发明与现有技术相比,其有益效果为:(1)通过采用90度磁过滤阴极真空弧(fcva)系统以及直管磁过滤阴极真空弧(fcva)系统共同制备缓冲薄膜、镓薄膜,制备过程中无需中途去除衬底,方法简单且易于工业应用。(2)本发明通过在镓薄膜与衬底之间制备氧化镁作为缓冲层,在脱模处理的过程中可以避免残余应力的释放导致自支撑镓薄膜的破裂。(3)直管磁过滤阴极真空弧(fcva)系统原子离化率非常高,大约在90%以上。由于原子离化率高,可使等离子体密度增加,成膜时大颗粒减少,有利于提高薄膜致密性、结合力等。(4)本发明经过创造性的设计,采用所述制备方法制备出质量厚度为500-1000μg/cm2、具有低应力、均匀且致密的自支撑镓薄膜。附图说明图1为本发明所采用的沉积装置示意图。图2为实施例1、2脱模处理之前得到的自支撑镓薄膜示意图。图3为实施例1、2脱模处理之后得到的自支撑镓薄膜示意图。图4为实施例1得到的自支撑镓薄膜的sem图。图5为实施例2得到的自支撑镓薄膜的sem图。附图标记说明1衬底2氯化钾脱模剂3氧化镁缓冲薄膜4镓薄膜590度fcva阴极6等离子体导管7弯管磁场8抽真空接口9工件台10负偏压端子11进气口12反应腔13直管fcva阴极。具体实施方式下面结合具体实施例对本发明进行进一步描述,但本发明的保护范围并不仅限于此。实施例1一种质量厚度为600μg/cm2自支撑镓薄膜的制备方法,包括以下步骤:选择2cm×2cm×0.5cm的玻璃作为衬底1,采用电子束热蒸发法沉积氯化钾脱模剂2,所述氯化钾脱模剂2厚度240nm;将玻璃衬底1放置于工件台9上,采用氧化镁靶材作为90度fcva阴极5、镓靶材作为直管fcva阴极13,通过抽真空接口8对沉积装置抽真空,使得反应腔12内真空度为1.2×10-4pa;随后从进气口11通入氩气,使得反应腔12内真空度为1.5pa;开启90度磁过滤阴极真空弧(fcva)系统并设置沉积参数为:起弧电流为60a,弯管磁场2.0a,束流50ma,负偏压为-150v,沉积时间为15min,占空比为40%,在氯化钾脱模剂2表面沉积厚度为180nm的氧化镁缓冲薄膜3。关闭90度磁过滤阴极真空弧(fcva)系统,将玻璃衬底1旋转180°,开启直管磁过滤阴极真空弧(fcva)系统并设置沉积参数为:起弧电流为80a,弯管磁场3.0a,束流100ma,负偏压为-250v,沉积时间为100min,占空比为90%,在氧化镁缓冲薄膜3上沉积厚度为50μm的镓薄膜4。将得到的玻璃衬底1放入盛有含水质量为5%的乙醇溶液的容器中进行脱模处理5min。用打捞板将镓薄膜捞起,得到质量厚度为600μg/cm2自支撑镓薄膜。对比例1一种自支撑镓薄膜的制备方法,包括以下步骤:选择2cm×2cm×0.5cm的玻璃作为衬底1,采用电子束热蒸发法沉积氯化钾脱模剂2,所述氯化钾脱模剂2厚度240nm;将玻璃衬底1放置于工件台9上,采用镓靶材作为直管fcva阴极13,通过抽真空接口8对沉积装置抽真空,使得反应腔12内真空度为1.2×10-4pa;随后从进气口11通入氩气,使得反应腔12内真空度为1.5pa;开启直管磁过滤阴极真空弧(fcva)系统并设置沉积参数为:起弧电流为80a,弯管磁场3.0a,束流100ma,负偏压为-250v,沉积时间为100min,占空比为90%,在氧化镁缓冲薄膜3上沉积厚度为50μm的镓薄膜4。将得到的玻璃衬底1放入盛有含水质量为5%的乙醇溶液的容器中进行脱模处理5min。用打捞板将镓薄膜捞起,得到自支撑镓薄膜。实施例2一种质量厚度为1000μg/cm2自支撑镓薄膜的制备方法,包括以下步骤:选择2cm×2cm×0.5cm的单晶硅作为衬底1,采用电子束热蒸发法沉积氯化钾脱模剂2,所述氯化钾脱模剂2厚度260nm;将单晶硅衬底1放置于工件台9上,采用氧化镁靶材作为90度fcva阴极5、镓靶材作为直管fcva阴极13,通过抽真空接口8对沉积装置抽真空,使得反应腔12内真空度为1.3×10-4pa;随后从进气口11通入氩气,使得反应腔12内真空度为1.2pa;开启90度磁过滤阴极真空弧(fcva)系统并设置沉积参数为:起弧电流为55a,弯管磁场1.0a,束流70ma,负偏压为-120v,沉积时间为30min,占空比为80%,在氯化钾脱模剂2表面沉积厚度为150nm的氧化镁缓冲薄膜3。关闭90度磁过滤阴极真空弧(fcva)系统,将玻璃衬底1旋转180°,开启直管磁过滤阴极真空弧(fcva)系统并设置沉积参数为:起弧电流为90a,弯管磁场4.0a,束流80ma,负偏压为-220v,沉积时间为9min,占空比为70%,在氧化镁缓冲薄膜3上沉积厚度为35μm的镓薄膜4。将得到的玻璃衬底1放入盛有含水质量为8%的乙醇溶液的容器中进行脱模处理6min。用打捞板将镓薄膜捞起,得到质量厚度为1000μg/cm2自支撑镓薄膜。对比例2一种自支撑镓薄膜的制备方法,包括以下步骤:选择2cm×2cm×0.5cm的单晶硅作为衬底1,采用电子束热蒸发法沉积氯化钾脱模剂2,所述氯化钾脱模剂2厚度260nm;将单晶硅衬底1放置于工件台9上,采用镓靶材作为直管fcva阴极13,通过抽真空接口8对沉积装置抽真空,使得反应腔12内真空度为1.3×10-4pa;随后从进气口11通入氩气,使得反应腔12内真空度为1.2pa;开启直管磁过滤阴极真空弧(fcva)系统并设置沉积参数为:起弧电流为90a,弯管磁场4.0a,束流80ma,负偏压为-220v,沉积时间为9min,占空比为70%,在氧化镁缓冲薄膜3上沉积厚度为35μm的镓薄膜4。将得到的玻璃衬底1放入盛有含水质量为8%的乙醇溶液的容器中进行脱模处理6min。用打捞板将镓薄膜捞起,得到自支撑镓薄膜。采用x射线应力测定方法测定自支撑镓薄膜的残余应力,结果记于表1。表1实施例1对比例1实施例2对比例2残余应力(mpa)210459196470从实施例1-2制备自支撑镓薄膜的扫描电镜图可以看出,镓薄膜具有致密结构;从实施例1-2与对比例1-2制备自支撑镓薄膜的残余应力结构可以得出,采用本发明提供的制备方法可以显著降低自支撑镓薄膜的残余应力。以上所述仅为本发明的实施例,并非因此限制本发明的专利范围,凡是利用本发明说明书内容所作的等效结构或等效流程变换,或直接或间接运用在其他相关的
技术领域:
,均同理包括在本发明的专利保护范围内。当前第1页12