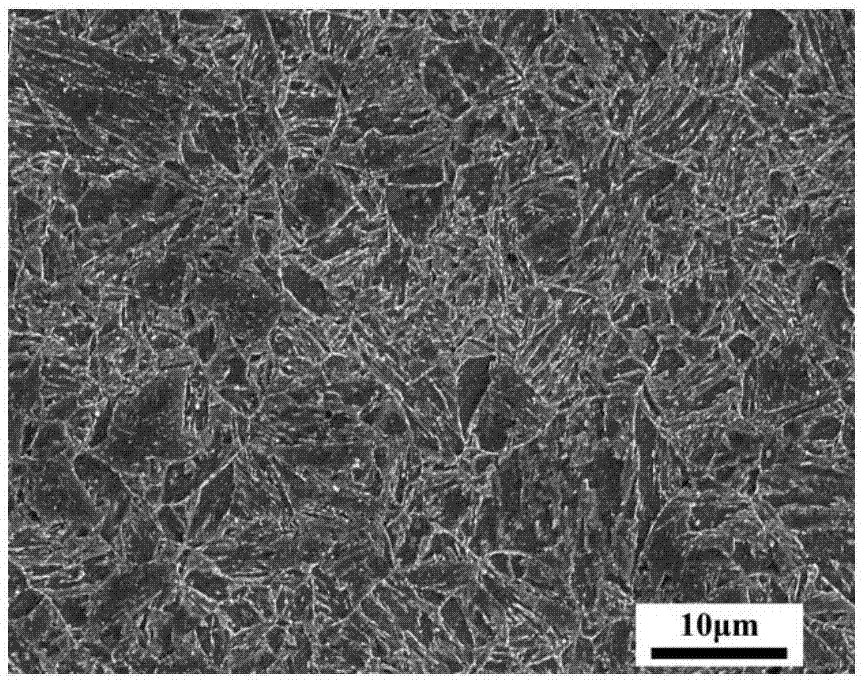
本发明属于合金钢及钢管制造领域,具体涉及一种汽车稳定杆用超高强度钢及稳定杆制造方法。
背景技术:
:汽车稳定杆是为了防止汽车转弯时侧向倾覆的扭力杆,通常固定在汽车底盘左右悬架的下臂。随着资源、能源、环境压力的日益增加,在保证整车性能的前提下实现轻量化已成为当前汽车行业的发展潮流。汽车稳定杆采用高强度和高塑性的空心部件以减少钢材用量,是实现汽车轻量化的有效途径之一。近年来为了节约能源、简化工序,汽车及机械类性能要求较高的零部件相继开发出非调质钢、空冷贝氏体钢等新材料,但在弹簧类产品中应用较少。如公开号为cn102899589a《一种高强度非调质贝氏体钢及制备方法》是在曲轴锻造后快速空冷获得部分贝氏体组织代替调质钢制曲轴的方法。虽然钢中加了mo、v、cr等多种贵重元素,但因最终得到的组织强韧性不足(抗拉强度rm≥1085mpa,屈服强度rp0.2≥795mpa),不能满足稳定杆类弹性件的力学性能要求。多数高强韧空冷贝氏体钢的力学性能也达不到弹簧产品的要求,有的则含有多种较高含量的贵重元素或稀有元素(如mo、ni、v等),使材料成本很高而难以实际应用。公开号cn1078269a的专利《高强韧性高淬透性空冷贝氏体钢》强调高淬透性,要求大尺寸的零件在空气中自然冷却,即在900℃~300℃之间的冷速≥1℃/min即可,但是为了保证淬透性而不得不提高mn、si等元素的含量,还要加入mo、v等贵重元素,材料成本较高。另外,零件空冷所需的时间很长,使要求短周期大批量生产的汽车横向稳定杆难以得到实际应用。公开号cn105088081a《稳定杆用贝氏体和马氏体弹簧钢及稳定杆的制造工艺》,加热至900℃~1050℃后采用控制冷却获得以贝氏体加部分低碳马氏体及少量残余奥氏体,然后低温回火使材料力学性能达到rm≥1350mpa,屈服强度rp0.2≥1050mpa,断后延伸率a≥10%,断面收缩率z≥35%。然而其强度仍然较低,难以满足汽车轻量化的需求。技术实现要素:本发明的目的是针对上述技术问题,通过成分设计和形变热处理工艺,形成晶粒细小均匀且由贝氏体/板条马氏体/残余奥氏体/片状马氏体复相组织组成的高强韧汽车稳定杆。为达到本发明的目的,本发明汽车稳定杆用超高强度钢包含以下重量百分比的化学成分:c0.20%~0.50%,mn0.50%~3.0%,cr0.01%~0.45%,al0.015%~0.07%,si0.20%~1.35%,b0.001%~0.006%,v+ti0.01~1.20%,余为fe和不可避免的杂质。优选的,本发明汽车稳定杆用超高强度钢的化学成分按重量百分比计为:c0.35%~0.40%,mn2.1%~2.5%,cr0.18%~0.27,al0.04%~0.06%,si1.20~1.35%,b0.004~0.006%,v0.04~0.05,ti0.03~0.04。本发明汽车用超高强度钢稳定杆的制造工艺,包括以下步骤:(1)使所述超高强度钢的化学成分构成的原料依次进行转炉或电炉冶炼、lf炉精炼和vd炉真空脱气;(2)精炼所得钢水连铸连轧成圆钢坯,并清除表面褶皱和缺陷;(3)对圆钢坯进行斜轧穿孔和定减径;(4)退火处理并酸洗;(5)进行3~5道次冷拔和1道次空拔,每一次冷拔之后进行退火处理;(6)进行热处理。进一步的,步骤(3)中,斜轧穿孔温度为1100℃~1250℃,压下量10~25%。进一步的,步骤(4)中,退火处理具体步骤为:先将钢管在760℃~850℃保温1h~5h,后于650℃~780℃保温1h~5h;酸洗采用浓度为4%~25%的盐酸或硫酸。进一步的,步骤(5)中,进行3道次冷拔,其中,冷拔的变形量和轧制速度分别为14%~17%、2m/min;20%~21%、2.5m/min;24%~25%、3m/min,空拔的变形量和轧制速度为22%~23%、3m/min。每一次冷拔后退火处理的温度为700℃~780℃,保温时间1h~5h。进一步的,步骤(6)中,热处理具体步骤为:首先将钢管加热至ac1以上20℃~100℃,保温5min~30min,随后空气加速冷却或水冷至250℃~450℃,保温30mim~150min,最后空气加速冷却或水冷。本发明的化学组成成分和关键工艺的设计依据如下:c是钢中最常用也最有效的强化元素,通过间隙固溶强化和碳化物析出强化发挥作用。本发明中设计碳含量在0.20%~0.50%之间,通过奥氏体化后快速冷却至ms点和mf点之间一定温度,获得合适含量的板条马氏体和贝氏体及少量残余奥氏体。在此温度保温,促使碳元素由过饱和的马氏体和贝氏体内向残余奥氏体扩散,提高奥氏体稳定性。最后快速冷却至室温,使残余奥氏体部分转变为高碳的片状马氏体从而提高强度,部分保留下来并在随后的冷加工或服役变形过程中发生形变诱发相变而提高塑韧性。c含量太低无法形成足够数量的马氏体和贝氏体,强度不足,太高则降低塑性及焊接性能。本发明钢中mn元素的添加可提高基体的强度和淬透性,并通过降低ac3温度细化冷却后的晶粒,此外,mn作为奥氏体形成元素,也提高了奥氏体含量和稳定性,以此提高塑韧性。但过高的mn含量使钢坯偏析严重、热应力及组织应力大、焊接性下降等,据此设计的mn含量在0.50%~3.0%之间。少量的cr和b元素保证了钢的淬透性,使钢在空冷条件下也能形成足够数量的板条马氏体和贝氏体。然而过多的cr使钢硬脆,因此将cr含量控制在0.01%~0.45%之间。si可通过间隙固溶的形式获得强化,从而同时提高抗拉强度和屈服强度。si能显著阻碍碳化物的形成,一方面实现了碳化物的细小尺度,另一方面保证足够的c元素扩散至奥氏体内。si含量过高使钢管冷拔时的裂纹倾向提高,恶化焊接性能,并易导致冷脆,据此设计的si含量在si0.20%~1.35%之间。v和ti元素能形成细小碳化物获得强化,并阻碍晶粒粗化,使钢保持细小晶粒尺度。采用本发明汽车稳定杆用超高强度钢和稳定杆制造方法生产的稳定杆,通过低碳板条马氏体、贝氏体和高碳片状马氏体获得强化,通过残余奥氏体的形变诱发相变作用提高塑韧性。与现有技术相比,实现了强韧性的极佳匹配,综合力学性能远优于现有钢种,充分满足稳定杆类弹性件的力学性能要求,可减少稳定杆钢材用量,实现汽车轻量化。附图说明图1是根据本发明实施例1制造的汽车稳定杆用超高强度钢基体组织的sem扫描电镜图。图2是根据本发明实施例1制造的汽车稳定杆用超高强度钢的工程应力-应变曲线图。具体实施方式下面根据具体实施例对本发明的技术方案做进一步说明。本发明的保护范围不限于以下实施例,列举这些实施例仅出于示例性目的而不以任何方式限制本发明。实施例1依次进行电炉冶炼、lf炉精炼、vd炉真空脱气和连铸连轧制得汽车稳定杆用超高强度钢圆坯,化学组成成分为c0.39%,mn2.21%,cr0.25%,al0.06%,si1.33%,b0.005%,v0.04,ti0.04%。于1200℃斜轧穿孔,压下量20%,穿孔后直接定减径。此后进行退火处理并酸洗:先将钢管在800℃保温1.5h后于720℃保温1h;酸洗采用浓度为10%%的盐酸或硫酸。对钢管进行3道次冷拔,道次变形量和轧制速度分别为14%、20%、24%;2mm/min、2.5mm/min、3mm/min,并且每次冷轧后进行退火处理。将钢管加热至930℃,保温12min,随后水冷至350℃,保温150min,后水冷至室温。最终按现有常规稳定杆总成制作方法制作稳定杆总成。本实施例生产的稳定杆基体组织为板条马氏体、片状马氏体和残余奥氏体,平均晶粒尺寸不足10μm(见图1)。奥氏体化后水冷至320℃,使奥氏体部分相变为板条马氏体,部分保留为残余奥氏体,随后的等温保温使板条马氏体中过饱和的碳元素向残余奥氏体内扩散,最后水冷使部分残余奥氏体转变为片状马氏体,部分保留至室温,最终残余奥氏体含量约9.2%。高碳片状马氏体的产生使得材料的强度相比于单一板条马氏体进一步提高,逆变奥氏体富c、mn等元素,热力学稳定性好,在冷却过程中不发生马氏体相变,但在形变过程中发生马氏体相变,耗散能量,避免微孔的产生和颈缩的提前发生,从而改善塑韧性,同时降低屈强比。本实施例超高强度钢的应力应变曲线如图2所示,其力学性能为:抗拉强度1756mpa,屈服强度1447mpa,延伸率13.2%。实施例2其他步骤同实施例1,钢管化学组成成分为c0.48%,mn1.34%,cr0.40%,al0.037%,si0.76%,b0.005%,v0.07,ti0.02%。冷拔之后将钢管加热至920℃,保温15min,随后水冷至250℃,保温60min,最后水冷至室温。其残余奥氏体含量约4.5%,抗拉强度1774mpa,屈服强度1468mpa,延伸率10.4%。实施例3其他步骤同实施例1,钢管化学组成成分为c0.21%,mn0.50%,cr0.28%,al0.042%,si1.35%,b0.004%,v0.08。冷拔之后将钢管加热至950℃,保温5min,随后水冷至380℃,保温120min,最后水冷至室温。其残余奥氏体含量约9.1%,抗拉强度1658mpa,屈服强度1453mpa,延伸率14.2%。实施例4其他步骤同实施例1,钢管化学组成成分为c0.35%,mn2.96%,cr0.37%,al0.045%,si1.20%,b0.004%,v0.02,ti0.03。冷拔之后将钢管加热至920℃,保温20min,随后水冷至320℃,保温30min,最后水冷至室温。其残余奥氏体含量约7.5%,抗拉强度1742mpa,屈服强度1453mpa,延伸率12.4%。实施例5其他步骤同实施例1,钢管化学组成成分为c0.28%,mn1.45%,cr0.02%,al0.07%,si0.89%,b0.005%,v0.07,ti0.01。冷拔之后将钢管加热至900℃,保温20min,随后水冷至280℃,保温45min,最后水冷至室温。其残余奥氏体含量约6.8%,抗拉强度1635mpa,屈服强度1428mpa,延伸率13.3%。对比例1其他步骤同实施例1,钢管化学组成成分为c0.15%,mn0.75%,cr0.04%,al0.052%,si1.21%,b0.006%,v0.06,ti0.03。冷拔之后将钢管加热至920℃,保温10min,随后水冷至300℃,保温40min,最后水冷至室温。其碳含量较少,形成的板条马氏体强度不足,同时没有足够的碳稳定奥氏体,残余奥氏体含量少,且难以形成片状马氏体,抗拉强度1451mpa,屈服强度1245mpa,延伸率10.2%。对比例2其他步骤同实施例1,钢管化学组成成分为c0.43%,mn0.82%,cr0.03%,al0.031%,si1.26%,b0.004%,v0.08。冷拔之后将钢管加热至1000℃,保温10min,随后水冷至320℃,保温45min,最后水冷至室温。由于奥氏体化温度过高,其晶粒发生粗化,且奥氏体化后的淬火组织中开始产生片状马氏体,其尺寸与残余奥氏体中产生的片状马氏体相变明显粗化,因而损坏塑性,抗拉强度1724mpa,屈服强度1467mpa,延伸率6.7%。对比例3其他步骤同实施例1,钢管化学组成成分为c0.30%,mn2.11%,cr0.36%,al0.04%,si1.02%,b0.004%,v0.06%。冷拔之后将钢管加热至920℃,保温12min,随后水冷至200℃,保温50min,最后水冷至室温。其基体组织为板条马氏体和少量残余奥氏体,奥氏体含量约1.3%,抗拉强度1526mpa,屈服强度1468mpa,延伸率8.9%。对比例4其他步骤同实施例1,钢管化学组成成分为c0.24%,mn1.73%,cr0.35%,al0.06%,si0.75%,b0.002%,v0.04,ti0.04。冷拔之后将钢管加热至920℃,保温15min,随后水冷至450℃,保温30min,最后水冷至室温。其基体组织为单一贝氏体,抗拉强度968mpa,屈服强度744mpa,延伸率16.8%。本发明汽车稳定杆用超高强度钢及稳定杆制造方法提供的稳定杆,通过在板条马氏体/贝氏体基体上进一步引入高强度的片状马氏体和高韧性的残余奥氏体来提高力学性能,其屈服强度rp0.2≥1400mpa,抗拉强度rm≥1600mpa,断后延伸率a≥10%,强韧性综合力学性能远优于现有钢种,充分满足稳定杆类弹性件的力学性能要求,可减少稳定杆钢材用量,实现汽车轻量化。将实施例1-5,以及对比例1-4所得钢的力学性能总结对比如表1,可发现本发明方案所得稳定杆钢综合力学性能优秀。表1实施例与对比例所得稳定杆用钢力学性能对比实施例抗拉强度(mpa)屈服强度(mpa)延伸率(%)实施例11756144713.2实施例21774146810.4实施例31658145314.2实施例41742145312.4实施例51635142813.3对比例11451124510.2对比例2172414676.7对比例3152614688.9对比例496874416.8当前第1页12