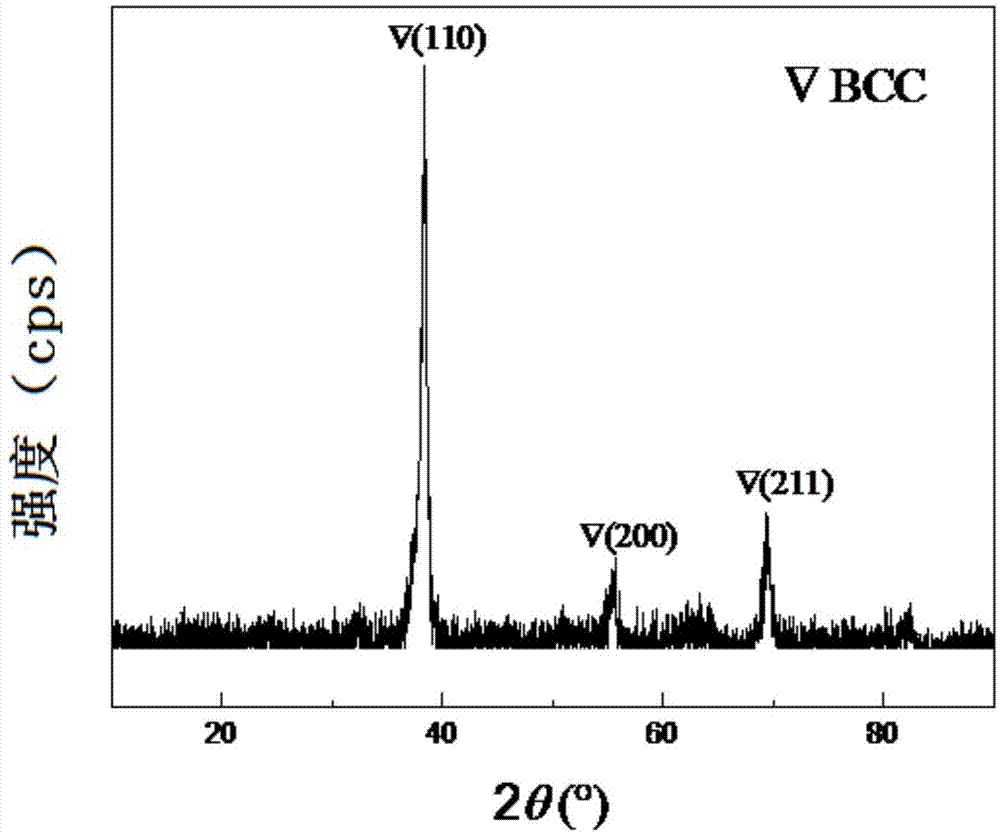
本发明涉及高熵合金领域,尤其涉及一种nbzrtita难熔高熵合金粉末的制备方法及nbzrtita难熔高熵合金粉末。
背景技术:
:高熵合金是近年发展起来的一种新型合金。与传统合金以一种或两种元素为主要组元不同,高熵合金是指由四种以上分子量相等或相近的组元形成的合金,其中每种元素的含量远大于5%且不高于30%,合金具有各主元随机混溶的单相固溶体结构,这种结构具有很高的混合熵,所以倾向于形成单相或多相简单结构的高熵固溶体,而不是生成金属间化合物等复杂结构。此种新型合金具有热力学上的高混合熵效应、结构上的晶格畸变效应、动力学上的扩散迟滞效应以及性能上的鸡尾酒效应。现有的研究结果表明,高熵合金具有一些优于传统合金的性能,例如:高强度、高硬度、耐回火软化、高耐磨性、良好的耐腐蚀性和特殊的磁性能等,是材料学科中继非晶合金之后又一个全新的前沿研究领域。难熔金属高熵合金是基于发展高温结构金属而开发的新型高熵合金体系。2010年美国空军研究实验室senkov在“intermetallics”杂志上公开发表了第一篇难熔高熵合金的文章“refractoryhigh-entropyalloys”。难熔高熵合金的组元元素为难熔金属元素,包括cr、hf、mo、nb、ta、ti、v、w、zr,以及非难熔金属元素al,主要体系有monbtaw、hfnbtazr、crmonbta和crnbvzr等。目前,关于难熔高熵合金力学性能的研究大多集中于难熔高熵合金的硬度和压缩性能。难熔高熵合金硬度普遍较大,可在宽温域内保持高强度,monbtaw和monbtavw两种含w的合金具有良好的高温力学性能,在2000k高温下仍可保持较高的强度。目前已公开报道的难熔高熵合金铸态下大多呈树枝晶组织和等轴晶组织,相结构为一个或两个bcc固溶相,含有cr、v元素的合金除bcc主相外还会出现laves相。难熔元素性质之间较大差异性极大丰富了难熔高熵合金的性能。难熔高熵合金的成功开发为高熵合金的研究提供了新思路。目前,难熔高熵合金的制备以真空电弧熔炼法为主。然而,高熔点nbzrtita高熵合金的制备过程中却存在一系列难点:由于合金的熔点较高,传统的熔铸法必然要克服加热温度高的难题,工艺难度较大;为了使成分均匀,需要经过多次重熔;同时,熔液凝固过程中不可避免地会产生枝晶偏析等成分不均匀现象,通过真空电弧熔炼法制备出的nbzrtita高熵合金虽展现出了极佳的力学性能及在含能结构材料领域巨大的应用潜力,但也存在着一系列无法克服的缺点:熔炼出的产品均匀样品的极限尺寸只有40mm左右并且有无法消除的缩孔。这些缺点都制约了nbzrtita难熔高熵合金性能的进一步提高及实际应用。而采用常规的单质粉末进行烧结也无法制备此类合金。近年来,国内外学者开始将机械合金化法用于高熵合金的制备。机械合金化是一种通过不断冷焊、断裂、再冷焊的过程使粉末在固态下实现合金化的高能机械球磨技术。因为机械合金化是一种固态加工工艺,所以可以显著降低材料的制备温度,克服熔点相差较大的原材料难以熔炼的问题,消除从液体到固体的转变过程中的枝晶偏析。机械合金化还具有成分可调范围大的特点,可以制备一些厌溶合金或过饱和固溶体。为了获得块体材料,机械合金化得到的金属粉末还必须经过热压、热等静压、放电等离子烧结等后续烧结工艺以获得致密的块体。相比于传统的熔铸法,粉末冶金法工艺简单,且制备出的合金晶粒更加细小、组织更加均匀,综合力学性能甚至超过传统熔铸法制备出的合金。例如:采用机械合金化和放电等离子烧结法制备出的al0.6conifeti0.4合金的压缩屈服强度和断裂强度分别达到2732mpa和3172mpa,塑性变形量达到了10.1%,表现出良好的综合力学性能(materialsscience&engineeringa,565(2013):439–444)。然而,由于nbzrtita的组成元素均为高熔点难熔金属,这些金属均具有硬度高、塑性差、扩散系数低等特点,因此前述方法并不能用于nbzrtita块体合金的制备。目前关于高熔点高熵合金的文献十分有限,高熔点高熵合金nbzrtita的制备方法也仅限于真空电弧熔炼法。若能采用粉末冶金法制备nbzrtita合金,则不但可显著降低合金的制备温度,降低能耗,简化其制备工艺,而且能消除枝晶偏析,使合金的晶粒细化、成分均匀,从而将使其力学性能进一步改善,具有非常重要的科学和工程意义。所以作为粉末冶金法制备高熵合金的第一步也是最关键一步,通过机械合金化制备nbzrtita难熔高熵合金意义重大。本发明对于发展高熵合金的制备技术,提高高熵合金的力学性能,促进高熵合金的研究和应用都将具有十分重要的意义。技术实现要素:本发明要解决的技术问题是克服现有技术的不足,提供nbzrtita难熔点高熵合金粉末的制备方法,该方法步骤简单、出粉率高,制备出的nbzrtita难熔高熵合金粉末组织均匀、晶粒细小,呈单相体心立方(bcc)结构。为解决上述技术问题,本发明采用以下技术方案:nbzrtita难熔高熵合金粉末的制备方法,包括以下步骤:将原料nb、zr、ti和ta单质粉末混合,然后添加物质无水乙醇和/或正庚烷,进行高能球磨,得到单相bcc结构的nbzrtita难熔高熵合金粉末。上述的技术方案中,经混合的各单质粉末在高能球磨过程中,逐渐实现合金化,最后形成单相bcc结构的合金粉末,此时,合金化过程完成。上述的nbzrtita难熔高熵合金粉末的制备方法中,优选地,按质量比百分比计,所述无水乙醇和/或正庚烷的添加量为所述nb、zr、ti、ta单质粉末质量总和的0.3%~30%。上述的nbzrtita难熔高熵合金粉末的制备方法中,优选地,所述高能球磨的球磨罐和磨球材质为不锈钢。上述的nbzrtita难熔高熵合金粉末的制备方法中,优选地,所述高能球磨的工艺条件为:球料比为8︰1~12︰1,球磨转速为250r/min~350r/min。上述的nbzrtita难熔高熵合金粉末的制备方法中,优选地,所述高能球磨的时间为40~85h。上述的nbzrtita难熔高熵合金粉末的制备方法中,优选地,当添加的物质为无水乙醇时,所述高能球磨的时间为50~85h;当添加的物质为正庚烷时,球磨时间为40~75h。上述的nbzrtita难熔高熵合金粉末的制备方法中,优选地,当添加的物质为无水乙醇时,所述高能球磨的时间为50~75h;当添加的物质为正庚烷时,球磨时间为40~55h。上述的nbzrtita难熔高熵合金粉末的制备方法中,优选地,按摩尔比计,所述nb、zr、ti、ta单质粉末的比例nb︰zr︰ti︰ta为1︰1︰1︰1,即优选为等摩尔比,更有利于高熵合金单相固溶体结构的形成,也可以为非等摩尔比。上述的nbzrtita难熔高熵合金粉末的制备方法中,优选地,所述混合、高能球磨在惰性气体保护下进行。作为一个总的发明构思,本发明还提供一种上述的制备方法制备得到的nbzrtita难熔高熵合金粉末,其结构为单相bcc结构,晶粒尺寸达到几十纳米,即为纳米级别。本发明通过在混合粉末中添加无水乙醇或正庚烷,再进行高能球磨制备出单相体心立方(bcc)结构的合金粉末,获得了组织均匀、晶粒细小的nbzrtita高熵合金粉末。与现有技术相比,本发明的优点在于:1、nbzrtita的组成元素均为高熔点难熔金属,这些金属均具有硬度高、塑性差、扩散系数低等特点,这些物理属性均不利于通过机械合金化的方式形成合金。机械合金化形成合金必须经历塑性变形、冷焊扩散、破碎细化这三个阶段,nb、zr、ti、ta元素的高硬度和低塑性均不利于原料粉产生塑性变形,而它们的低扩散系数则不利于冷焊扩散。因此,若要制备由难熔金属组成的难熔高熵合金通常需要延长球磨时间,但是球磨时间的增强意味着增加了粉料与不锈钢球和不锈钢罐之间的碰撞和接触时间,经研究发现,球磨时间过长会产生两个不利后果:1、增加了粉末中的缺陷数量,使得出现无序非晶相的几率大幅度增加;2、使得粉料与不锈钢球和不锈钢罐之间的冷焊加剧,极大地降低了最终高熵合金粉的出粉率。为解决上述问题,本发明通过大量的研究发现,在球磨过程中加入液态的无水乙醇和/或正庚烷,能减少粉料与不锈钢球和不锈钢之间的冷焊,极大地提高最终合金的出粉率,使得到的nbzrtita高熵合金粉末组织更加均匀,晶粒细小。2、本发明的nbzrtita高熵合金粉末的方法操作简单,容易实现,出粉率高。3、由于nb、zr、ti、ta均为高熔点金属,传统的熔炼方法需要加热到2904℃以上高温才能将其熔化,同时需多次重熔以消除成分偏析,而本发明采用机械合金化方法获得高熵合金粉末使其制备块体合金时不需要加热到熔点温度就可获得性能较好的块体材料,有效地降低了加工温度,简化了其制备工艺。4、本发明通过机械合金化获得了成分均匀的高熵合金粉末,后续再结合放电等离子烧结技术的放电效应、烧结温度低和烧结时间短等一系列优点,可以获得晶粒细小、无枝晶偏析的高熵合金块体材料,使制备得到的材料的强度相比于电炉熔炼得到的材料进一步提高。附图说明图1为本发明实施例1制备的nbzrtita的x射线衍射图谱。图2为本发明实施例2制备的nbzrtita的x射线衍射图谱。图3为本发明实施例3制备的nbzrtita的x射线衍射图谱。图4为本发明实施例4制备的nbzrtita的x射线衍射图谱。图5为对比例1制备的nbzrtita的x射线衍射图谱。图6为对比例2制备的nbzrtita的x射线衍射图谱。图7为对比例3制备的nbzrtita的x射线衍射图谱。图8为本发明实施例2制备的nbzrtita的saed图。图9为本发明实施例1~4和对比例1~3球磨过程中在球磨30h时取样分析的xrd射线衍射对比图谱。图10为本发明实施例1制备的nbzrtita的sem衍射图谱。图11为本发明实施例3制备的nbzrtita的sem衍射图谱。图12为对比例1制备的nbzrtita的sem衍射图谱。图13为对比例3制备的nbzrtita的sem衍射图谱。具体实施方式以下将结合说明书附图和具体实施例对本发明做进一步详细说明。实施例1一种nbzrtita高熵合金粉末的制备方法,采用机械合金化方法,包括如下工艺条件:采用nb、zr、ti、ta四种单质粉末的等原子比混合粉末50g作为原料,进行混合,在行星式高能球磨机的球磨罐中进行球磨。罐体材料及磨球的材质均为不锈钢,球磨罐内抽真空并充高纯氩气(99.99%)作为保护气氛,添加无水乙醇0.15g(0.3%)作为球磨介质。球磨过程中球料比为10︰1,转速为300r/min,球磨50h后将nbzrtita合金粉末取出,此时粉末已转变为单相bcc固溶体。混合粉末在高能球磨过程中,逐渐实现合金化,最后形成单相bcc结构的合金粉末,此时,合金化过程完成。本实施例中,原料混合、高能球磨以及对样品进行分析时的取样均在惰性气氛下进行。经球磨后获得等原子比的nbzrtita高熵合金粉末,其xrd结果如图1所示,显示为单相bcc固溶体。实施例2一种nbzrtita高熵合金粉末的制备方法,采用机械合金化方法,包括如下工艺条件:原料粉末的成分和含量、设备,球料比、转速均同实施例1,球磨介质为15g(30%)无水乙醇,球磨时间为75h。经球磨后获得等原子比的nbzrtita高熵合金粉末,其xrd结果如图2所示,显示为单相bcc固溶体。本实施例中,原料混合、高能球磨以及对样品进行分析时的取样均在惰性气氛下进行。实施例3一种nbzrtita高熵合金粉末的制备方法,采用机械合金化方法,包括如下工艺条件:原料粉末的成分和含量、设备、球料比、转速均同实施例1,球磨介质为0.15g(0.3%)正庚烷,球磨时间为40h。经球磨后获得等原子比的nbzrtita高熵合金粉末,其xrd结果如图3所示,显示为单相bcc固溶体。本实施例中,原料混合、高能球磨以及对样品进行分析时的取样均在惰性气氛下进行。实施例4一种nbzrtita高熵合金粉末的制备方法,采用机械合金化方法,包括如下工艺条件:原料粉末的成分和含量、设备、球料比、转速均同实施例1,球磨介质为15g(30%)正庚烷,球磨时间为55h。经球磨后获得等原子比的nbzrtita高熵合金粉末,其xrd结果如图4所示,显示为单相bcc固溶体。本实施例中,原料混合、高能球磨以及对样品进行分析时的取样均在惰性气氛下进行。对比例1:一种nbzrtita高熵合金粉末的制备方法,采用机械合金化方法,包括如下工艺条件:原料粉末的成分和含量、设备,球料比、转速均同实施例1,球磨介质为0.15g(0.3%)硬脂酸,球磨时间为30h。经球磨后获得等原子比的nbzrtita高熵合金粉末,其xrd结果如图5所示,显示为结晶性很弱(衍射峰相对强度弱、干扰噪音信号强)单相bcc固溶体。本对比例中,原料混合、高能球磨以及对样品进行分析时的取样均在惰性气氛下进行。对比例2:一种nbzrtita高熵合金粉末的制备方法,采用机械合金化方法,包括如下工艺条件:原料粉末的成分和含量、设备、球料比、转速均同实施例1,球磨介质为15g(30%)硬脂酸,球磨时间为30h。经球磨后获得等原子比的nbzrtita高熵合金粉末,其xrd结果如图6所示,显示为结晶性很弱的单相bcc固溶体。本对比例中,原料混合、高能球磨以及对样品进行分析时的取样均在惰性气氛下进行。对比例3:一种nbzrtita高熵合金粉末的制备方法,采用机械合金化方法,包括如下工艺条件:原料粉末的成分和含量、设备、球料比、转速均同实施例1,未加球磨介质,球磨时间为30h。经球磨后获得等原子比的nbzrtita高熵合金粉末,其xrd结果如图7所示,显示为单相bcc固溶体。本对比例中,原料混合、高能球磨以及对样品进行分析时的取样均在惰性气氛下进行。结果表征及分析:表1:样品球磨介质单相形成时间出粉率实施例10.3%无水乙醇50h60%实施例230%无水乙醇75h80%实施例30.3%正庚烷40h50%实施例430%正庚烷55h90%对比例10.3%硬脂酸30h<1%对比例230%硬脂酸30h30%对比例3无介质添加30h<1%表1为采用不同球磨介质时,制备nbzrtita高熵合金粉末的单相形成时间和出粉率。由于在相同的球磨条件下球磨时间的增加会降低出粉率,因此,从表1可得出,采用无水乙醇和正庚烷作为球磨介质,相对于不添加球磨介质或采用硬脂酸作为球磨介质时,大大提高了出粉率及xrd衍射峰中的相对强度。图8为实施例2中得到的合金粉末的选区电子衍射(saed)图,该图进一步证明了形成了bcc结构单相固溶体。在实施例1~4和对比例1~3的高能球磨过程中,在球磨30h时均取样进行分析球磨得到的产物晶型。图9即为采用不同球磨介质球磨30h后取样分析对应的xrd图谱,从图9中可看出:球磨30h后,不添加球磨介质和以硬脂酸为介质的nbzrtita粉末样品为bcc单相固溶体结构,而以无水乙醇和正庚烷的粉末样品为bcc+hcp双相结构。结果表明,硬脂酸的添加与否对合金粉末单相固溶体的出现时间和出粉率影响不大。当加入无水乙醇和正庚烷作为球磨介质时,合金粉末单相固溶体的出现时间延长,且出粉率大幅度增加。图10为添加质量分数为0.3%的无水乙醇在球磨50h得到样品(实施例1)的sem及元素分布图谱,图11为添加质量分数为0.3%的正庚烷在球磨40h得到的样品(实施例3)的sem及元素分布图谱,图12为添加质量分数为0.3%的硬脂酸在球磨30h得到的样品(对比例1)的sem及元素分布图谱,图13为未添加球磨介质在球磨30h得到样品(对比例3)的sem及元素分布图谱。本发明中,对于未添加介质或添加硬脂酸的样品来说,由于在得到单相合金粉末时,出粉率已经极低,再延长球磨时间将会导致无法收集到粉末,因此本发明选取得到单相合金粉末的样品进行对比。结合图10、11、12、13和xrd分析可以得出,未添加介质或以硬脂酸作为球磨介质时,合金粉在变成体心立方单相固溶体结构时的元素均匀性不佳;而以正庚烷和无水乙醇作为球磨介质时,虽然合金粉在变成体心立方单相固溶体结构所需的时间增加,但此时合金粉可实现元素均匀化。这是因为,本发明的合金原料在本发明特殊的球磨合金化的过程中时,一方面能实现元素均匀化,另一方面合金会由于不断的球磨而经历晶粒尺寸不断减小,且晶相结构从不同金属原料混合物到单相固溶体。本发明中,加入无水乙醇、正庚烷延长了形成单相固溶体的时间,球磨时间更长,从而使得到的单相固溶体的元素均匀化的程度也相应提高,且减小晶粒尺寸,形成了纳米级的高熵合金;同时,极大地减少了冷焊,显著提高了出粉率。虽然本发明已以较佳实施例揭示如上,然而并非用以限定本发明。任何熟悉本领域的技术人员,在不脱离本发明技术方案范围的情况下,都可利用上述揭示的技术内容对本发明技术方案做出许多可能的变动和修饰,或修改为等同变化的等效实施例。因此,凡是未脱离本发明技术方案的内容,依据本发明技术实质对以上实施例所做的任何简单修改、等同变化及修饰,均应落在本发明技术方案保护的范围内。当前第1页12