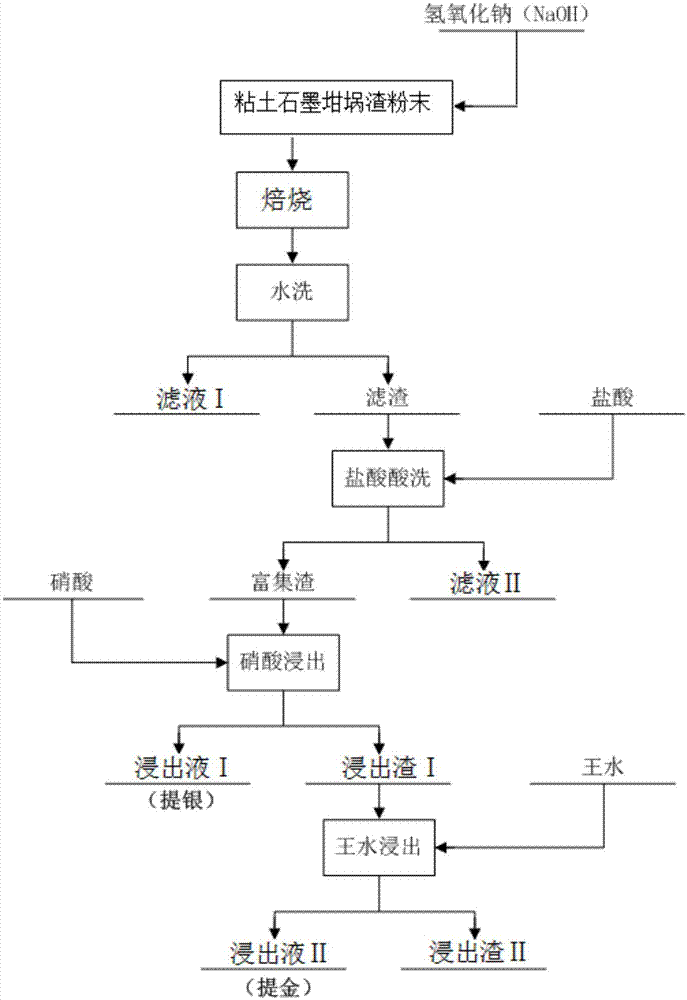
本发明属于有色金属回收
技术领域:
,具体涉及一种碱焙烧提取粘土石墨坩埚渣中金和银的方法。
背景技术:
火法冶炼金属时,经常使用粘土石墨坩埚对熔炼之后的金属进行铸形,熔炼、浇筑时会有少量的粗金属渗透到坩埚里。坩埚多次使用,在坩埚内壁会富集大量的金属。尤其是在冶炼金时,所用粘土石墨坩埚中富集有较多的金和银,金、银是高价值的贵金属,具有极高的经济回收价值。叶志清公布了一种采用全湿法提取火法冶炼坩埚渣中铟、锗的方法(专利申请号cn201010169155.x全湿法提取火法冶炼坩埚渣中铟、锗的方法),采用稀硫酸浸出铟,然后采用mno2做氧化剂用浓硫酸浸出锗,可以实现对大部分锗、铟的分别回收,且能保持较高的回收率。金属熔炼之后的熔体温度通常高于1000℃,而石墨在空气中的燃点为850~1000℃,纯石墨坩埚在浇铸过程中极易损坏。所以,金属火法冶炼过程中使用的坩埚均为粘土石墨坩埚。目前,对从粘土石墨坩埚渣中提取金属金和银的研究较少。因为耐火粘土的存在,直接采用火法对金坩埚渣进行高温煅烧时,坩埚渣会烧结成块,难以提取金和银;此外,耐火粘土主要为铝硅酸盐等难溶性物质,而骨料氮化硅也是化学稳定性极好,直接采用硝酸和王水进行浸出提取其中的金和银,回收率也是几乎为零。因此,现有技术从粘土石墨坩埚渣中回收金和银存在一定的技术难度。技术实现要素:本发明针对坩埚渣中耐火粘土严重影响金、银回收提取,造成金、银回收效率低的问题,而提供一种新型的湿/火法相结合的方法及工艺流程,对粘土石墨坩埚渣中的金、银进行回收。本发明提供了一种碱焙烧提取粘土石墨坩埚渣中金和银的方法,包括以下步骤:1)将粘土石墨坩埚渣粉末与氢氧化钠、助熔剂均匀混合,在500~700℃下焙烧,然后冷却、研磨成样品粉末。2)样品粉末经水洗,酸洗,干燥处理得到粉末状的富集渣;3)将富集渣置于硝酸溶液中,常温搅拌进行浸出反应,反应完全后的混合溶液经过稀释,过滤得到浸出渣ⅰ和浸出液ⅰ,浸出液ⅰ经过还原提取银;4)浸出渣ⅰ置于王水中,在50~80℃下搅拌进行浸出反应,反应完全后的混合溶液经过稀释,过滤得到浸出液ⅱ,浸出液ⅱ经过还原提取金。优选的,步骤1)中所述粘土石墨坩埚渣粉末的粒径为150-325目。优选的,步骤1)中所述粘土石墨坩埚渣粉末与氢氧化钠的质量比为2:1~1:2。优选的,步骤1)中所述助熔剂为偏硼酸锂。优选的,所述偏硼酸锂的用量为粘土石墨坩埚渣粉末、氢氧化钠和偏硼酸锂三者质量总和的0.5~3%。优选的,步骤2)中所述水洗采用纯水搅拌清洗,搅拌时间为30~120min。优选的,步骤2)中所述酸洗采用浓度为0.5~2mol/l的盐酸溶液搅拌清洗。优选的,步骤3)中所述硝酸溶液的浓度为63-130g/l。优选的,步骤3)中所述富集渣与硝酸溶液的质量体积比为1:1-5g/ml。优选的,步骤4)中所述浸出渣ⅰ与王水的质量体积比为1:1-5g/ml。本发明步骤1)中所述焙烧的时间为1-2h。本发明步骤2)中所述样品粉末先经过纯水搅拌清洗,搅拌的时间为30~120min,然后过滤分离得到滤液ⅰ和滤渣,滤渣再经过浓度为0.5-2mol/l的盐酸溶液搅拌清洗,搅拌的时间为30~120min,滤渣和盐酸溶液的质量体积比为1:1-5g/ml,然后过滤分离得到滤液ⅱ和富集渣。本发明步骤3)中所述反应完全后的混合溶液稀释3-5倍,然后过滤得到浸出渣ⅰ和浸出液ⅰ。本发明步骤4)中过滤能够得到浸出液ⅱ和浸出渣ⅱ,浸出渣ⅱ能够继续返回到步骤3)中代替富集渣,进一步提取金和银。本发明所述粘土石墨坩埚渣粉末是通过粘土石墨坩埚渣研磨、过筛得到的,金坩埚渣粉碎之后粒径为150~325目。本发明所述粘土石墨坩埚渣是通过对郴州市金贵银业股份有限公司报废的火法冶炼金的粘土石墨坩埚粉碎得到的,其中粘土石墨坩埚渣中的金属元素的质量百分比为:金(au):0.013%、银(ag)5.284%、铜(cu):0.710%。粘土石墨坩埚是指以石墨、碳化硅、硅石、粘土、沥青和焦油为原料烧制而成的一类坩埚。通常其中石墨的含量为35~55%,骨料的含量为(如:碳化硅)25-45%,粘土的含量为:15~25%,以及少量的沥青和焦油。本发明提供了一种碱焙烧提取粘土石墨坩埚渣中金和银的方法,最优选的步骤如下:1)采用粉碎机将废粘土石墨坩埚进行破碎、研磨、过筛,得到粒径为200目的粘土石墨坩埚渣粉末,分析检测得到粘土石墨坩埚渣粉末中各金属元素的含量如下:au:0.013%、ag:5.284%、cu:0.710%;按质量比1:1称取粘土石墨坩埚渣粉末与氢氧化钠,添加占粘土石墨坩埚渣粉末、氢氧化钠和偏硼酸锂三者质量总和的2%的偏硼酸锂之后混合均匀,放置于马弗炉中,在空气氛围中,600℃下焙烧2小时,然后,自然冷却至室温,研磨粉碎成样品粉末。2)样品粉末先经过纯水搅拌清洗,搅拌的时间为30min,然后过滤分离得到滤液ⅰ和滤渣,滤渣再经过浓度为1mol/l的盐酸溶液搅拌清洗,搅拌的时间为30min,滤渣和盐酸溶液的质量体积比为1:2g/ml,然后过滤分离得到滤液ⅱ和富集渣;3)富集滤渣置于浓度为63g/l的硝酸溶液中进行浸出反应,常温搅拌进行浸出反应4h,反应完全后的混合溶液稀释3倍,过滤得到浸出渣ⅰ和浸出液ⅰ,浸出液ⅰ经过还原提取银;其中富集渣与硝酸溶液的质量体积比为1:2g/ml;4)浸出渣ⅰ置于王水溶液中,在60℃下搅拌进行浸出反应5h,反应完全后的混合溶液经过稀释,过滤得到浸出液ⅱ和浸出渣ⅱ,浸出液ⅱ经过还原提取金;其中浸出渣ⅰ与王水的质量体积比为1:1.5g/ml。采用最优的步骤得到的金和银的提取率最高。目前,大家对火法冶炼金属的坩埚渣中的金属回收研究较少,专利申请号cn201010169155.x公开了一种全湿法提取火法冶炼坩埚渣中铟、锗的方法,采用稀硫酸浸出铟,然后采用mno2做氧化剂用浓硫酸浸出锗,可以实现对大部分锗、铟的分别回收,且能保持较高的回收率。目前从金属冶炼渣中回收金和银是直接采用硝酸和王水浸出,因此在现有技术的基础上,本领域技术人员能够想到采用湿法提取本申请粘土石墨坩埚渣中的金、银。但是本申请的发明人通过研究发现,直接以硝酸和王水浸出粘土石墨坩埚渣中的金、银,会使得金和银的提取率大大降低,杂质较多,得到的金属纯度不高,实用价值降低。另外,若直接对粘土石墨坩埚渣进行煅烧,粘土石墨坩埚渣会烧结成块,影响后期金、银的提取效果。因此本申请的发明人想到要除去粘土石墨坩埚渣中的粘土成分,而目前除去粘土的常规方法是用氢氟酸浸出、硅氟酸浸出等方法,但此方法环境污染较大,浸出效果不佳。本申请先让粘土中的难溶性物质(硅铝酸盐)与氢氧化钠在高温熔融条件下,转变为可溶性硅酸钠和偏铝酸钠,然后通过水洗、酸洗,有效、环保、节能地除去其中的粘土成分,提高金、银的提取效果。本申请采用火法和湿法相结合提取粘土石墨坩埚渣中的金和银,相较于只采用湿法,本申请金和银的提取率大大提高。并且本申请的通过碱焙烧法处理粘土石墨坩埚渣,先去除其中的粘土、沥青、焦油及其他杂质金属,最后分别用酸和王水浸出的方法将金和银分离出来,相较于不经过碱焙烧法处理而直接煅烧或者不经过碱焙烧法处理而直接酸浸煮,本申请在煅烧之前先进行碱焙烧处理,能够避免在高温煅烧的过程中粘土石墨坩埚渣粉末成块;除去了石墨坩埚渣中绝大部分的粘土、有机物,铜等组分,实现金和银与其他杂质的分离,提高了金、银的浸出回收率,并且本发明采取此种操作顺序,能够使金和银最大程度的与其他杂质分离,提高了金、银的浸出回收率。本发明的有益效果是:1、本申请采用火法和湿法相结合提取粘土石墨坩埚渣中的金和银,相较于只采用湿法,本申请金和银的提取率大大提高。2、本申请先用氢氧化钠与粘土石墨坩埚渣高温焙烧,再水洗、酸洗,能够有效除去其中的粘土成分,避免在后期的煅烧过程中成块,影响后期金、银的提取效果。3、本申请采用碱酸焙烧法去除粘土石墨坩埚中的粘土组分,相较于氢氟酸法和氟硅酸法更为环保。4、本申请的粘土石墨坩埚渣在经过碱焙烧处理之后,分别用酸和王水浸出的方法将金和银分离出来。相较于不经过碱焙烧处理,本申请的处理方法能够避免在煅烧的过程中粘土石墨坩埚渣成块,实现金和银与其他杂质的分离,提高了金、银的浸出回收率。5、采用本发明的操作顺序,能够使金和银最大程度的与其他杂质分离,提高了金、银的浸出回收率。6、本发明的原料来源充足,价格低廉,生产成本低。7、本发明的提取过程中金、银不分散,在富集渣中分两步浸出,第一步浸出银元素,第二步浸出金元素,即能回收金,又能回收银,且能保持较高的回收效率。附图说明图1为本发明的工艺流程图。具体实施方式为使本发明的目的、技术方案和优点更加清楚明白,以下结合具体实施例,对本发明进一步详细说明。实施例11)采用粉碎机将废粘土石墨坩埚进行破碎、研磨、过筛,得到粒径为200目的粘土石墨坩埚渣粉末,分析检测得到粘土石墨坩埚渣粉末中各金属元素的含量如下:au:0.013%、ag:5.284%、cu:0.710%;按质量比1:1称取粘土石墨坩埚渣粉末与氢氧化钠,添加占粘土石墨坩埚渣粉末、氢氧化钠和偏硼酸锂三者质量总和的2%的偏硼酸锂之后混合均匀,放置于马弗炉中,在空气氛围中,600℃下焙烧2小时,然后,自然冷却至室温,研磨粉碎成样品粉末;2)样品粉末先经过纯水搅拌清洗,搅拌的时间为30min,然后过滤分离得到滤液ⅰ和滤渣,滤渣再经过浓度为1mol/l的盐酸溶液搅拌清洗,搅拌的时间为30min,滤渣和盐酸溶液的质量体积比为1:2g/ml,然后过滤分离得到滤液ⅱ和富集渣;3)富集滤渣置于浓度为63g/l的硝酸溶液中进行浸出反应,常温搅拌进行浸出反应4h,反应完全后的混合溶液稀释3倍,过滤得到浸出渣ⅰ和浸出液ⅰ,浸出液ⅰ经过还原提取银;其中富集渣与硝酸溶液的质量体积比为1:2g/ml;4)浸出渣ⅰ置于王水溶液中,在60℃下搅拌进行浸出反应5h,反应完全后的混合溶液经过稀释,过滤得到浸出液ⅱ和浸出渣ⅱ,浸出液ⅱ经过还原提取金;其中浸出渣ⅰ与王水的质量体积比为1:1.5g/ml。实施例21)采用粉碎机将废粘土石墨坩埚进行破碎、研磨、过筛,得到粒径为150目的粘土石墨坩埚渣粉末,分析检测得到粘土石墨坩埚渣粉末中各金属元素的含量如下:au:0.013%、ag:5.284%、cu:0.710%;按质量比2:1称取粘土石墨坩埚渣粉末与氢氧化钠,添加占粘土石墨坩埚渣粉末、氢氧化钠和偏硼酸锂三者质量总和的0.5%的偏硼酸锂之后混合均匀,放置于马弗炉中,在空气氛围中,500℃下焙烧1小时,然后,自然冷却至室温,研磨粉碎成样品粉末;2)样品粉末先经过纯水搅拌清洗,搅拌的时间为60min,然后过滤分离得到滤液ⅰ和滤渣,滤渣再经过浓度为0.5mol/l的盐酸溶液搅拌清洗,搅拌的时间为60min,滤渣和盐酸溶液的质量体积比为1:5g/ml,然后过滤分离得到滤液ⅱ和富集渣;3)富集滤渣置于浓度为80g/l的硝酸溶液中进行浸出反应,常温搅拌进行浸出反应4h,反应完全后的混合溶液稀释3倍,过滤得到浸出渣ⅰ和浸出液ⅰ,浸出液ⅰ经过还原提取银;其中富集渣与硝酸溶液的质量体积比为1:1g/ml;4)浸出渣ⅰ置于王水溶液中,在80℃下搅拌进行浸出反应5h,反应完全后的混合溶液经过稀释,过滤得到浸出液ⅱ和浸出渣ⅱ,浸出液ⅱ经过还原提取金;其中浸出渣ⅰ与王水的质量体积比为1:5g/ml。实施例31)采用粉碎机将废粘土石墨坩埚进行破碎、研磨、过筛,得到粒径为325目的粘土石墨坩埚渣粉末,分析检测得到粘土石墨坩埚渣粉末中各金属元素的含量如下:au:0.013%、ag:5.284%、cu:0.710%;按质量比1:2称取粘土石墨坩埚渣粉末与氢氧化钠,添加占粘土石墨坩埚渣粉末、氢氧化钠和偏硼酸锂三者质量总和的3%的偏硼酸锂之后混合均匀,放置于马弗炉中,在空气氛围中,700℃下焙烧1.5小时,然后,自然冷却至室温,研磨粉碎成样品粉末;2)样品粉末先经过纯水搅拌清洗,搅拌的时间为120min,然后过滤分离得到滤液ⅰ和滤渣,滤渣再经过浓度为2mol/l的盐酸溶液搅拌清洗,搅拌的时间为120min,滤渣和盐酸溶液的质量体积比为1:1g/ml,然后过滤分离得到滤液ⅱ和富集渣;3)富集滤渣置于浓度为130g/l的硝酸溶液中进行浸出反应,常温搅拌进行浸出反应4h,反应完全后的混合溶液稀释5倍,过滤得到浸出渣ⅰ和浸出液ⅰ,浸出液ⅰ经过还原提取银;其中富集渣与硝酸溶液的质量体积比为1:5g/ml;4)浸出渣ⅰ置于王水溶液中,在50℃下搅拌进行浸出反应5h,反应完全后的混合溶液经过稀释,过滤得到浸出液ⅱ和浸出渣ⅱ,浸出液ⅱ经过还原提取金;其中浸出渣ⅰ与王水的质量体积比为1:1g/ml。对比例11)采用粉碎机将废粘土石墨坩埚进行破碎、研磨、过筛,得到粒径为200目的粘土石墨坩埚渣粉末,分析检测得到粘土石墨坩埚渣粉末中各金属元素的含量如下:au:0.013%、ag:5.284%、cu:0.710%;将粘土石墨坩埚渣粉末放置于马弗炉中,在空气氛围中,600℃下焙烧2小时,然后,自然冷却至室温,研磨粉碎得到富集渣;2)富集滤渣置于浓度为63g/l的硝酸溶液中进行浸出反应,常温搅拌进行浸出反应4h,反应完全后的混合溶液稀释3倍,过滤得到浸出渣ⅰ和浸出液ⅰ,浸出液ⅰ经过还原提取银;其中富集渣与硝酸溶液的质量体积比为1:2g/ml;3)浸出渣ⅰ置于王水溶液中,在60℃下搅拌进行浸出反应5h,反应完全后的混合溶液经过稀释,过滤得到浸出液ⅱ和浸出渣ⅱ,浸出液ⅱ经过还原提取金;其中浸出渣ⅰ与王水的质量体积比为1:1.5g/ml。对比例21)采用粉碎机将废粘土石墨坩埚进行破碎、研磨、过筛,得到粒径为200目的粘土石墨坩埚渣粉末,分析检测得到粘土石墨坩埚渣粉末中各金属元素的含量如下:au:0.013%、ag:5.284%、cu:0.710%;2)将粘土石墨坩埚渣粉末置于浓度为63g/l的硝酸溶液中进行浸出反应,常温搅拌进行浸出反应4h,反应完全后的混合溶液稀释3倍,过滤得到浸出渣ⅰ和浸出液ⅰ,浸出液ⅰ经过还原提取银;其中富集渣与硝酸溶液的质量体积比为1:2g/ml;3)浸出渣ⅰ置于王水溶液中,在60℃下搅拌进行浸出反应5h,反应完全后的混合溶液经过稀释,过滤得到浸出液ⅱ和浸出渣ⅱ,浸出液ⅱ经过还原提取金;其中浸出渣ⅰ与王水的质量体积比为1:1.5g/ml。分别测定实施例1和对比例1的粘土石墨坩埚渣粉末经过碱焙烧处理前后的质量变化以及煅烧后的状态,结果如表1。表1粘土石墨坩埚渣粉末煅烧前后的质量变化以及煅烧后的状态从表1中的数据可知,经过焙烧处理之后,实施例1和对比例1中的粘土石墨坩埚渣粉末重量均发生了一定量的降低,表明在焙烧过程中,去除了坩埚渣中的易燃烧组分,达到了焙烧除杂的目的。此外,实施例1中碱焙烧处理后的粘土石墨坩埚渣粉末经过600℃高温焙烧之后的重量减少量明显大于对比例1中粘土石墨坩埚渣粉末的重量减少量,可以推断出经过碱焙烧处理,有效地去除了坩埚渣原样中的粘土成分,提升了易氧化燃烧组分的比例,提高了焙烧除杂效率,并且经过高温煅烧不会烧结成块,提高了后期金、银的提取率。测定实施例1中粘土石墨坩埚渣粉末、浸出渣ⅰ、浸出液ⅰ、浸出渣ⅱ和浸出液ⅱ这5种物质中金(au)、银(ag)和铜(cu)的含量,并由此计算实施例1中粘土石墨坩埚渣粉末中au、ag的提取率,结果如表2。表2各物质中au、ag和cu的含量以及au、ag的提取率从表2中的数据可知,本发明中的粘土石墨坩埚渣粉末经过碱焙烧和硝酸处理后,其中的铜元素被大量除去,很好的实现铜元素与金和银的分离,提高了最终金和银的提取效率,本发明实施例1中粘土石墨坩埚渣粉末中金和银的提取率分别为95.61%和97.12%,提取率高,能够对粘土石墨坩埚渣中的金、银分别进行有效的回收。测定实施例1-3和对比例1-2的粘土石墨坩埚渣粉末中金和银的提取率,结果如表3。表3粘土石墨坩埚渣粉末中金和银的提取率实施例金的提取率(%)银的提取率(%)实施例195.61%97.12%实施例294.26%96.87%实施例395.54%97.00%对比例17.66%4.34%对比例26.49%2.38%从表3中的数据可知,与对比例相比,采用本发明的方法从粘土石墨坩埚渣粉末中提取金和银的提取率大大提高,并且最优选的是实施例1。说明本申请采用火法和湿法相结合提取粘土石墨坩埚渣中的金和银,相较于只采用湿法,本申请金和银的提取率大大提高。并且本申请的粘土石墨坩埚渣采用碱焙烧,水洗和酸洗,最后分别用酸和王水浸出的方法将金和银分离出来,相较于直接煅烧,本申请能够避免在煅烧的过程中粘土石墨坩埚渣粉末成块,除去了石墨坩埚渣中绝大部分的铜,实现金和银与其他杂质的分离,提高了金、银的浸出回收率,并且本发明采取此种操作顺序,能够使金和银最大程度的与其他杂质分离,提高了金、银的浸出回收率。当前第1页12