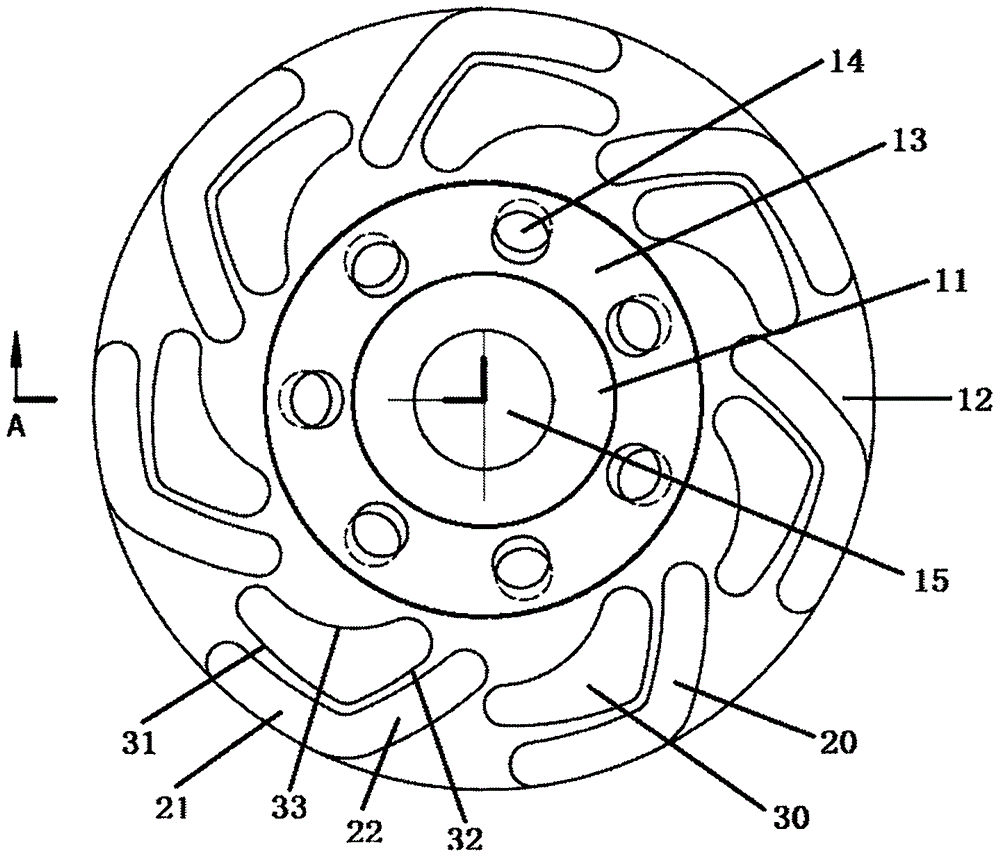
本发明涉及金刚石磨削工具的
技术领域:
,更具体地说,本发明涉及一种瓷砖加工用磨轮。
背景技术:
:金刚石磨轮是指以金刚石颗粒作为磨料的金刚石刀头焊接或者冷压在钢基体上而成的轮状或碗状的金刚石磨削工具。其中的金刚石刀头是通过人造金刚石和其它的金属粉末通过冷压和热压烧结而成,然后焊接在碗状或轮状的钢基体上。金刚石磨轮通常被装在打磨机、角磨机或数控机床上来打磨如混凝土、花岗岩、大理石、瓷砖等。在现有技术中,用于混凝土、大理石等石材的磨轮通常在轮状或碗状的基体的平面上设置环形的金刚石工作面。采用环形的磨轮形式,磨具在使用过程中,当磨粒磨钝时,由于磨粒自身部分碎裂或结合剂断裂,磨粒从磨具上局部或完全脱落,而磨具工作面上的磨料不断出现新的切削刃口,或不断露出新的锋利磨粒,使磨具在一定时间内能保持切削性能。为了改进排屑,在环形工作面的基础上,现有技术中还出现了具有沟槽的非连续环形工作面的磨轮。本发明的申请人开发了一种具有多个l形金刚石磨块的磨轮,其进一步提高了对大理石、花岗岩等的磨削性能,但其对研磨性很弱的石材以及瓷砖等,导致磨削效率降低,通过尝试对胎体进行“弱化”,但这会导致胎体对金刚石颗粒的包镶能力下降,容易导致金刚石颗粒大面积脱落并且出刃高度较低。技术实现要素:为了解决现有技术中的上述技术问题,本发明的目的在于提供一种瓷砖加工用磨轮。本发明的瓷砖加工用磨轮,包括碗形钢基体,所述碗形钢基体包括位于上沿的环形加工面;其特征在于:所述环形加工面上设置有多个l形金刚石磨块,所述l形金刚石磨块由金刚石颗粒和钎料结合剂通过混料、冷压和烧结形成;并且所述钎料钎料结合剂中含有空心微珠。其中,所述钎料结合剂由25~35wt%的电解铜粉、3~6wt%的雾化锡粉、10~15wt%的cst合金粉、2.5~5.0wt%的空心微珠和余量的电解铁粉组成。其中,所述电解铜粉、雾化锡粉和电解铁粉的平均粒径为13~75μm。其中,所述空心微珠的密度为1.2~2.8g/cm3,粒径为150~300μm。其中,所述烧结在保护气氛下于880~910℃进行。其中,所述金刚石颗粒的粒径为180~500μm。其中,所述l形金刚石磨块的耐磨性为0.3×10-5~0.8×10-5。其中,所述l形金刚石磨块由沿着环形加工面外圆周延伸设置的第一磨块段和自所述环形加工面外圆周向环形加工面内圆周延伸设置的第二磨块段组成,所述第一磨块段和第二磨块段具有基本相同的宽度。其中,所述环形加工面上设置有多个心形通孔,心形通孔与l形金刚石磨块一一对应,并且心形通孔位于所述环形加工面的内圆周一侧与所述l形金刚石磨块之间。其中,所述心形通孔由靠近所述l形金刚石磨块的第一磨块段的第一外侧边、靠近所述l形金刚石磨块的第二磨块段的第二外侧边和连接所述第一外侧边和第二外侧边的第三外侧边形成。与现有技术相比,本发明的瓷砖加工用磨轮与现有的环形磨轮相比具有以下有益效果:本发明的瓷砖加工用磨轮同时具有径向和轴向的把持力,顺应性好,应用于瓷砖的磨削具有与瓷砖相匹配的耐磨损性,金刚石颗粒出刃高度高,磨削效率高。附图说明图1为本发明的瓷砖加工用磨轮的俯视图。图2为图1沿着a方向的剖切图。图3为l形金刚石磨块的两段间的夹角示意图。图4为本发明的瓷砖加工用磨轮的立体图。具体实施方式以下将结合具体实施例对本发明的瓷砖加工用磨轮做进一步的阐述,以帮助本领域的技术人员对本发明的发明构思、技术方案有更完整、准确和深入的理解。如图1~2所示,本发明的瓷砖加工用磨轮,包括碗形钢基体10,碗形钢基体10由圆形底面11、环形加工面12和位于圆形底面11和环形加工面12之间的圆台形侧面13组成,圆形底面11上设置有中心轴孔15,所述中心轴孔15用于装配角磨机的动力输出轴。圆台形侧面13自圆形底面11至环形加工面12具有逐渐变大的横截面,并且圆台形侧面13上设置有多个散热孔14,所述多个散热孔14沿着所述中心轴孔15的轴线方向对称分布。所述钢基体10通常为低碳钢或低合金钢等通过铸造以及机械加工而成。在本发明中,环形加工面12上可通过冷压和烧结工艺形成有多个l形金刚石磨块20,所述l形金刚石模块20的个数一般为6~8个,在以下实施例和比较例中均为7个。所述l型金刚石磨块20首先是通过金刚石颗粒与钎料结合剂配料形成成型料,然后将钢基体放置在工装模具中并投放成型料,通过冷压得到毛坯,最后在石墨模具中并于保护气氛中进行烧结。在本发明中,l形金刚石磨块20由沿着环形加工面外圆周延伸设置的第一磨块段21和自所述环形加工面外圆周向环形加工面内圆周延伸设置的第二磨块段22组成,并且所述第一磨块段21和第二磨块段22为一体成型结构,所述第一磨块段21和第二磨块段22具有基本相同的宽度。如图3所示,将所述第一磨块段和第二磨块段邻近部分的切线方向的夹角定义为二者的夹角,并且二者之间的夹角设计为120°~150°。将夹角设计为上述范围能够保证磨削时,磨轮的顺应性同时还能使得其中的金刚石磨块能够获得持久的自锐性能。所述环形加工面12上还设置有多个心形通孔30,心形通孔30与l形金刚石磨块一一对应,并且心形通孔30位于环形加工面12的内圆周一侧与l形金刚石磨块20之间。心形通孔30由靠近l形金刚石磨块20的第一磨块段21的第一外侧边31、靠近l形金刚石磨块20的第二磨块段22的第二外侧边32和连接第一外侧边31和第二外侧边32的第三外侧边33形成。l形金刚石磨块20与心形通孔30均匀设置在环形加工面12上。在本发明中,通过设置与l形金刚石磨块一一对应且邻近于所述l形金刚石磨块的心形通孔能够保证在高速磨削的工况下的排屑和散热问题,非常适合于干磨削工艺。图4为本发明的磨轮的立体图。在本发明中,l形金刚石磨块由金刚石颗粒和钎料结合剂通过混料、冷压和烧结形成;所述钎料结合剂由25~35wt%的电解铜粉、3~6wt%的雾化锡粉、10~15wt%的cst合金粉、2.5~5.0wt%的空心微珠和余量的电解铁粉组成。所述电解铜粉、雾化锡粉和电解铁粉的平均粒径为13~75μm。其中,所述空心微珠的密度为1.2~2.8g/cm3,粒径为150~300μm(在以下实施例中空心微珠的密度为2.3g/cm3,粒度为60目)。所述烧结在保护气氛下于880~910℃进行。所述金刚石颗粒的粒径为180~500μm。采用上述钎料结合剂烧结制备得到的磨块具有适中的耐磨性,其耐磨性为0.3×10-5~0.8×10-5。所述耐磨性通过以下公式计算得到:在上述公式中:m为磨耗系数;w为试样实验前后的质量差,g;d为试样直径,mm,s为试样的摩擦行程,mm;ρ为试样的密度,g/cm3。磨损性通过本发明的钎料结合剂烧结制成直径为6mm,高度为8mm的圆柱试样在磨损试验机上测定。实施例11)配料:以重量百分比表示,钎料结合剂由35%的电解铜粉、3%的雾化锡粉、10%的cst合金粉、2.5wt%的空心微珠和余量的电解铁粉组成。金刚石颗粒的浓度为0.8ct/cm3,金刚石粒度为40/45目,混制成成型料,采用三维混料机,混料120分钟。2)冷压:调整好工装模具,先投放清洁好的65mn钢基体,投放成型料并将粉料刮均匀,然后到冷压成型钢模中加压成型得到冷压的“l”型磨轮的毛坯。3)烧结:将冷压的“l”型磨轮的毛坯,组装在石墨模具中,在真空气氛中进行烧结,烧结温度在880℃。4)后加工:烧结后的磨轮基体表面喷砂、测动平衡、喷漆、开刃。5)后加工好的磨轮,进行打标、印字,按要求包装入库。得到的磨轮中的磨块的耐磨性为0.7×10-5。实施例21)配料:以重量百分比表示,钎料结合剂由25%的电解铜粉、6%的雾化锡粉、15%的cst合金粉、5.0wt%的空心微珠和余量的电解铁粉组成。金刚石颗粒的浓度为0.8ct/cm3,金刚石粒度为40/45目,混制成成型料,采用三维混料机,混料120分钟。2)冷压:调整好工装模具,先投放清洁好的65mn钢基体,投放成型料并将粉料刮均匀,然后到冷压成型钢模中加压成型得到冷压的“l”型磨轮的毛坯。3)烧结:将冷压的“l”型磨轮的毛坯,组装在石墨模具中,在真空气氛中进行烧结,烧结温度在880℃。4)后加工:烧结后的磨轮基体表面喷砂、测动平衡、喷漆、开刃。5)后加工好的磨轮,进行打标、印字,按要求包装入库。得到的磨轮中的磨块的耐磨性为0.4×10-5。实施例31)配料:以重量百分比表示,钎料结合剂由30%的电解铜粉、5%的雾化锡粉、12wt%的cst合金粉、3.0wt%的空心微珠和余量的电解铁粉组成。金刚石颗粒的浓度为0.8ct/cm3,金刚石粒度为40/45目,混制成成型料,采用三维混料机,混料120分钟。2)冷压:调整好工装模具,先投放清洁好的65mn钢基体,投放成型料并将粉料刮均匀,然后到冷压成型钢模中加压成型得到冷压的“l”型磨轮的毛坯。3)烧结:将冷压的“l”型磨轮的毛坯,组装在石墨模具中,在真空气氛中进行烧结,烧结温度在880℃。4)后加工:烧结后的磨轮基体表面喷砂、测动平衡、喷漆、开刃。5)后加工好的磨轮,进行打标、印字,按要求包装入库。得到的磨轮中的磨块的耐磨性为0.5×10-5。对比例11)配料:以重量百分比表示,钎料结合剂由30%的电解铜粉、5%的雾化锡粉、12wt%的cst合金粉、3.0wt%的石墨粉和余量的电解铁粉组成。金刚石颗粒的浓度为0.8ct/cm3,金刚石粒度为40/45目,混制成成型料,采用三维混料机,混料120分钟。2)冷压:调整好工装模具,先投放清洁好的65mn钢基体,投放成型料并将粉料刮均匀,然后到冷压成型钢模中加压成型得到冷压的“l”型磨轮的毛坯。3)烧结:将冷压的“l”型磨轮的毛坯,组装在石墨模具中,在真空气氛中进行烧结,烧结温度在880℃。4)后加工:烧结后的磨轮基体表面喷砂、测动平衡、喷漆、开刃。5)后加工好的磨轮,进行打标、印字,按要求包装入库。得到的磨轮中的磨块的耐磨性为0.5×10-5。对比例21)配料:以重量百分比表示,钎料结合剂由30%的电解铜粉、5%的雾化锡粉、12wt%的cst合金粉、3.0wt%的硼粉和余量的电解铁粉组成。金刚石颗粒的浓度为0.8ct/cm3,金刚石粒度为40/45目,混制成成型料,采用三维混料机,混料120分钟。2)冷压:调整好工装模具,先投放清洁好的65mn钢基体,投放成型料并将粉料刮均匀,然后到冷压成型钢模中加压成型得到冷压的“l”型磨轮的毛坯。3)烧结:将冷压的“l”型磨轮的毛坯,组装在石墨模具中,在真空气氛中进行烧结,烧结温度在880℃。4)后加工:烧结后的磨轮基体表面喷砂、测动平衡、喷漆、开刃。5)后加工好的磨轮,进行打标、印字,按要求包装入库。得到的磨轮中的磨块的耐磨性为0.5×10-5。对比例31)配料:以重量百分比表示,钎料结合剂由30%的电解铜粉、5%的雾化锡粉、12wt%的cst合金粉、3.0wt%的白炭黑和余量的电解铁粉组成。金刚石颗粒的浓度为0.8ct/cm3,金刚石粒度为40/45目,混制成成型料,采用三维混料机,混料120分钟。2)冷压:调整好工装模具,先投放清洁好的65mn钢基体,投放成型料并将粉料刮均匀,然后到冷压成型钢模中加压成型得到冷压的“l”型磨轮的毛坯。3)烧结:将冷压的“l”型磨轮的毛坯,组装在石墨模具中,在真空气氛中进行烧结,烧结温度在880℃。4)后加工:烧结后的磨轮基体表面喷砂、测动平衡、喷漆、开刃。5)后加工好的磨轮,进行打标、印字,按要求包装入库。得到的磨轮中的磨块的耐磨性为0.4×10-5。将实施例3以及对比例1~3制备的磨轮安装在角磨机上对瓷砖以干磨削方式进行磨削试验(切入式,转速3000r/min,切深0.1mm),磨削200分钟后测量瓷砖单位面积的磨削量δv(mm3/mm),以实施例3的磨削量作为基准“1”,则对比例1~3的相对磨削量分别如表1所示。表1对比例1对比例2对比例3相对磨削量0.780.750.69通过对磨轮磨削的表面进行观察可以发现,实施例3磨块的表面出刃的金刚石颗粒出刃高度较高,可达100~150μm,而且大部分有局部破碎的现象,表现出良好的自锐性能。而对比例1~2,出现了较多的脱落现象,对比例3中发现磨平的金刚石颗粒较多,而且出刃高度一般为70~120μm,表现出了较差的自锐性。对于本领域的普通技术人员而言,具体实施例只是对本发明进行了示例性描述,显然本发明具体实现并不受上述方式的限制,只要采用了本发明的方法构思和技术方案进行的各种非实质性的改进,或未经改进将本发明的构思和技术方案直接应用于其它场合的,均在本发明的保护范围之内。当前第1页12